-
Subscribe to Blog:
SEARCH THE BLOG
CATEGORIES
- Aerospace
- Asset Maintenance
- Automotive
- Blog
- Building Products
- Case Studies
- Chemical Processing
- Consulting
- Food & Beverage
- Forestry Products
- Hospitals & Healthcare
- Knowledge Transfer
- Lean Manufacturing
- Life Sciences
- Logistics
- Manufacturing
- Material Utilization
- Metals
- Mining
- News
- Office Politics
- Oil & Gas
- Plastics
- Private Equity
- Process Improvement
- Project Management
- Spend Management
- Supply Chain
- Uncategorized
- Utilities
- Whitepapers
BLOG ARCHIVES
- May 2025 (1)
- April 2025 (1)
- March 2025 (1)
- February 2025 (4)
- January 2025 (4)
- December 2024 (4)
- November 2024 (2)
- October 2024 (6)
- September 2024 (5)
- August 2024 (5)
- July 2024 (6)
- June 2024 (3)
- May 2024 (3)
- April 2024 (4)
- March 2024 (3)
- February 2024 (4)
- January 2024 (5)
- December 2023 (2)
- November 2023 (1)
- October 2023 (6)
- September 2023 (3)
- August 2023 (4)
- July 2023 (2)
- June 2023 (3)
- May 2023 (7)
- April 2023 (3)
- March 2023 (3)
- February 2023 (5)
- January 2023 (6)
- December 2022 (2)
- November 2022 (5)
- October 2022 (5)
- September 2022 (5)
- August 2022 (6)
- July 2022 (3)
- June 2022 (4)
- May 2022 (5)
- April 2022 (3)
- March 2022 (5)
- February 2022 (4)
- January 2022 (7)
- December 2021 (3)
- November 2021 (5)
- October 2021 (3)
- September 2021 (2)
- August 2021 (6)
- July 2021 (2)
- June 2021 (10)
- May 2021 (4)
- April 2021 (5)
- March 2021 (5)
- February 2021 (3)
- January 2021 (4)
- December 2020 (3)
- November 2020 (3)
- October 2020 (3)
- September 2020 (3)
- August 2020 (4)
- July 2020 (3)
- June 2020 (5)
- May 2020 (3)
- April 2020 (3)
- March 2020 (4)
- February 2020 (4)
- January 2020 (4)
- December 2019 (3)
- November 2019 (2)
- October 2019 (4)
- September 2019 (2)
- August 2019 (4)
- July 2019 (3)
- June 2019 (4)
- May 2019 (2)
- April 2019 (4)
- March 2019 (4)
- February 2019 (5)
- January 2019 (5)
- December 2018 (2)
- November 2018 (2)
- October 2018 (5)
- September 2018 (4)
- August 2018 (3)
- July 2018 (2)
- June 2018 (4)
- May 2018 (3)
- April 2018 (3)
- March 2018 (2)
- February 2018 (2)
- January 2018 (1)
- December 2017 (1)
- November 2017 (2)
- October 2017 (2)
- September 2017 (1)
- August 2017 (2)
- July 2017 (2)
- June 2017 (1)
- April 2017 (3)
- March 2017 (3)
- February 2017 (2)
- January 2017 (2)
- December 2016 (2)
- November 2016 (4)
- October 2016 (4)
- September 2016 (3)
- August 2016 (6)
- July 2016 (4)
- June 2016 (4)
- May 2016 (1)
- April 2016 (3)
- March 2016 (4)
- February 2016 (2)
- January 2016 (4)
- December 2015 (3)
- November 2015 (3)
- October 2015 (1)
- September 2015 (1)
- August 2015 (4)
- July 2015 (6)
- June 2015 (4)
- May 2015 (7)
- April 2015 (6)
- March 2015 (6)
- February 2015 (4)
- January 2015 (3)
CONNECT WITH US
Tag Archives: Logistics
Long-haul trucking has become more expensive and less logistically viable, making intermodal transportation an increasingly attractive alternative. Its market growth will directly affect industrial production and commerce, impacting manufacturers and business owners. Which trends should they prepare for in 2025?
Why Intermodal Transportation Is Becoming More Common
Intermodal transportation involves moving freight by multiple modes of transportation — rail, air, road and ship. Lately, its growth has been exponential. Experts project its upward trajectory will continue. According to a Research and Markets report, the intermodal freight transportation market will reach an estimated $103.78 billion in 2028, up from $58.85 billion in 2024, achieving a compound annual growth rate of 15.2%.
The cost of long-haul trucking is among the foremost driving factors. Geopolitical issues and inescapable inflation have driven fuel prices up. The ongoing labor shortage is also compounding this problem. According to the International Road Transport Union, more than 50% of trucking companies had difficulty filling driver positions due to the shortage in 2023.
Since far fewer younger people are entering the trucking industry, the supply of skilled drivers is diminishing. Many of those who remain are demanding higher wages. Employers can either comply or lose their staff to competitors, further driving up operational expenses.
Other factors besides the high cost of long-haul trucking are driving intermodal transportation growth. For one, the e-commerce market is booming. Urbanization and an increased demand for expedited delivery support heightened manufacturing output, which drives the need for intermodal transportation. Ultimately, while these factors are core growth drivers, other burgeoning trends have moved into position to cause dramatic, abrupt changes in 2025.
Trends Pushing Intermodal Transportation Growth in 2025
Three significant trends should support positive growth for the intermodal transportation market in 2025.
Emissions Regulations Are Tightening
Various countries worldwide are getting serious about greenhouse gases. For instance, the European Union set a carbon dioxide standard for heavy-duty vehicles, targeting a 15% reduction by 2025 and a 45% reduction by 2030. These emerging environmental regulations will likely drive firms away from long-haul trucking and toward other modes of transportation.
Interest Rates May Soon Ease
The Federal Reserve may soon reduce interest rates. Experts project it could carry out two rate reductions in 2025. This forecast is not as optimistic as the previous one, which projected up to four cuts. This change may be the culprit of an abundance of caution — officials are waiting to see the impacts of President Trump’s policy changes. His handling of trade and immigration could influence their decision-making process.
The freight market will see growth if interest rates ease. In addition to rebounding from the yearslong recession, industry professionals would experience heightened borrowing capabilities. These factors could increase their resiliency to disruption and give them a unique opportunity to explore intermodal transportation.
Logistics Technologies Are Advancing
Advanced logistics and management technologies can increase supply chain visibility, making managing multiple modes of transport more accessible. With real-time tracking, edge computing, telematics and global positioning systems, intermodal transportation is not as risky as it otherwise would be. Since these solutions are becoming more powerful and affordable every year, even small business owners can leverage them.
Trends Slowing Intermodal Transportation Growth in 2025
While industry leaders hope for a meaningful upturn in 2025, these concerning trends may hold back the intermodal transportation market.
Cargo Theft Is on the Rise
The more stops and handoffs there are, the easier it is for bad actors and malicious insiders to infiltrate supply networks unnoticed. Cargo theft already increased by nearly 50% from 2023 to 2024. Would a multimodal strategy introduce carriers to a heightened risk of stolen freight? This question does not inspire confidence.
Geopolitical Instability May Worsen
Geopolitical instability often follows elections. Roughly 50% of the global population lived in countries that held a national election in 2024 — the largest election year in history. Naturally, inevitable policy and party changes lead to trade tensions and restrictions, potentially disrupting supply chains. In other words, the entire world will likely feel the effects in 2025.
The Government Might Introduce New Tariffs
A shift toward higher tariffs often results in a reduction in import and export volume. Trade restrictions are another common by-product. These obstacles could complicate the Federal Reserve’s efforts to ease interest rates, potentially slowing the growth of the multimodal transportation market.
The Far-Reaching Impacts of Intermodal Transportation
One year may not seem like a long time, but it is. By the end of 2025, interest rates, labor market logistics technologies and the geopolitical landscape could look completely different. Whether supply chains experience a recession or congestion, multimodal shipping will likely remain a rising market. However, companies and manufacturers should remain observant — the trends that influence growth may indirectly impact their profits and business opportunities.
*This article is written by Jack Shaw. Jack is a seasoned automotive industry writer with over six years of experience. As the senior writer for Modded, he combines his passion for vehicles, manufacturing and technology with his expertise to deliver engaging content that resonates with enthusiasts worldwide.
The nature of supply chains has evolved over the years, with new technologies and many players in the middle making logistics highly complicated and expensive. A report by PwC indicates that logistics and supply chain costs account for approximately 10% of the organization’s total expenses. This is the most costly issue businesses struggle to minimize in their supply chain operations.
Managed transportation systems (MTS) address this problem, providing an organized way of consolidating logistics and eliminating waste. According to Gartner, the transportation management systems (TMS) market is expected to grow by 60%. This boom exemplifies the role of MTS in adapting to the prevailing dynamics of supply chain management.
This article will define MTS within the supply chain, reveal its operational and financial advantages, and explain how companies can embed them within their current structures and processes without disruption.
Benefits of Using Managed Transportation Systems
Managed transportation systems (MTS) go beyond optimizing shipping routing and data analysis management. They help manage logistics, allowing companies to concentrate on their primary business operations. Outsourcing the transportation management systems promotes professional development within the organization. It also enhances efficiency by eliminating wastefulness and saves costs in the long run.
The following are key benefits of using MTS in your supply chain processes:
Risk Management
Risk management has become more crucial now than ever because disruptions are bound to impact a company’s performance in its logistics industry. A managed transportation system can reduce risk by controlling carrier relationships and fine-tuning supply chain networks while using data-driven predictive tools to prevent delays or inefficiencies.
Cost Savings
Managed transportation systems assist organizations in selecting appropriate carriers and routes. This helps marketers cut transportation costs. In fact, companies that use data-driven insights can make well-organized decisions geared toward saving and managing costs effectively in the long run.
Simplified Day-to-Day Operations
If your company outsources logistics management, it can concentrate on its core business activities, such as developing new products and servicing customers. MTS providers manage logistics complexities, from booking shipments to addressing issues that may arise, so internal resources can be focused on core operations, increasing operational efficiency.
Enhanced Data and Insights
MTS analytics helps businesses monitor where logistics failed in real time. These insights allow businesses to make timely decisions, reduce delivery time, and optimize supply chain operations. Research indicates that data analytics helps cut costs and improve service levels.
Achieving Cost Efficiency with Managed Transportation Solutions
To stay competitive in the logistics market, your business must focus on reducing the cost of operations. But how do we achieve this? It’s pretty simple: Integrate managed transportation systems into your business.
Here are some vital hands-on ways to guarantee cost-effectiveness with MTS.
Carrier Optimization
Cost efficiency starts with choosing the appropriate carrier. MTS providers are not always out to settle on the cheapest rates but instead aim to optimize carrier selection by balancing cost and service performance. This guarantees timely deliveries and reduces transport costs.
Route and Mode Optimization
MTS helps companies find an optimum route and transport mode, resulting in huge cost savings. Increased route planning and mode selection for faster transit times help save on fuel consumption.
Data-Driven Decision Making
Data analytics are essential tools in minimizing a company’s costs. MTS vendors gather information from multiple systems and provide organizations with intelligence regarding logistics activities. Predictive and prescriptive analytics help forecast demand, anticipate disruptions, and make informed decisions that drive long-term cost savings.
Harnessing Data-Driven Insights for Superior Supply Chain Management
As supply chains grow more complex, data and analytics have become more than an optional add-on; they have become enablers of efficiency and resiliency. With the situation becoming even more complicated due to global disruptions, regulatory demands, and changing market conditions, data-driven approaches can bring a paradigm shift in supply chain management.
Here’s how businesses can capitalize on data-driven capabilities to improve the efficiency of their supply chain.
Supply Chain Data Management
Effective data management is the backbone of survival in the modern supply chain. There is an increasing reliance on advanced analytic tools for managing large volumes of data, which warrants quick insights and quicker actions.
According to KPMG’s Future of Supply Chain report, 39% of global supply chain professionals say they will invest in digital technologies to strengthen their data analysis capabilities. The readily available data enables an organization to anticipate interruptions, enhance visibility, and support efficient actions that maximize costs and service.
AI-Enabled Supply Chain Planning
Traditionally, demand planning is frequently carried out across departments using antiquated methods. This always leads to slow and less accurate forecasts. Fortunately, using AI-powered supply chain planning, the gaps between internal and external data can now be eliminated by leveraging unique machine learning models that link disparate types of information into a much more accurate forecast.
Generative AI in Supply Chain
Generative AI (GenAI) can transform supply chain management by making automation and decision-making easy. Examples of Gen AI use cases are translating complex data, summarizing legal documents, and analyzing customer feedback in real time.
Gen AI helps supply chain leaders more easily spot early warning signs, such as disruptions in supplier countries. It also supports faster response due to its capacity for handling huge amounts of information.
Best Practices for Leveraging Managed Transportation Systems in Your Business
A managed transportation system is a significant step and must be planned accordingly. Some best practices can help guide the process and ensure business gain from these systems.
1. Evaluate the Specific Needs of Your Business
Each company has different logistics requirements, and there may not always be a one-size-fits-all answer. When choosing a managed transportation provider or system, map your specific needs and see if they align with what they have—this is key. Shipment volume, frequency, and where you operate your business are some things to reflect on.
2. Monitor Key Performance Indicators (KPIs)
Measuring success for managed transportation system metrics begins with setting KPIs as they provide the capability to formulate results and track ongoing progress. Some metrics to monitor in your LSP are on-time delivery rates, transportation cost per shipment, and how fuel-efficient they run. Frequent monitoring of these KPIs will help determine the probable areas where the system could be improved to deliver desired outcomes.
3. Focus on Continuous Improvement
The logistics industry is ever-changing, and what works today may not work tomorrow. Businesses should be proactive agents, constantly assessing their managed transportation system and making informed course corrections based on data intelligence and performance metrics.
While this explanation can be more in-depth, businesses that embrace these best practices will have a smoother deployment of their managed transportation system and the operational as well as cost-saving results they expect.
Conclusion
There are many benefits of using managed transportation systems for businesses trying to improve supply chain efficiency and cost savings. MTS gives companies the tools needed to modernize logistics by delivering real-time visibility, route optimization, and data-driven decision support so that carriers can gain a competitive advantage in an increasingly complex supply chain. By deploying these systems, businesses can reduce costs and improve compliance and overall customer satisfaction.
*This article is written by Sheer Logistics. Sheer Logistics provides technology-driven supply chain solutions that empower businesses with visibility, efficiency, and agility across their logistics operations. With a focus on transparency and strategic partnership, Sheer Logistics helps clients optimize their supply chains and drive sustainable growth.
When cargo theft occurs, the entire supply chain suffers. Manufacturers must be aware of these recent trends occurring and act accordingly to protect their assets. With smart planning, businesses can adequately thwart thieves and safeguard their employees. Here are considerations for manufacturers to move in the right direction.
1. Understanding the Most Significant Risks
First, companies should understand the specific threats to which they are most vulnerable. The most immediate danger could be trucks in unsecured areas where thieves can quickly access them. In other instances, manufacturers may see organized crime targeting highly valued goods. Regardless, business owners need to acknowledge their weaknesses.
Researchers have investigated risk influential factors (RIFs) to determine the most damaging aspects. A 2022 study published in Reliability Engineering and System Safety developed a data-driven Bayesian network model to predict and diagnose cargo theft. The experts said product category, year, region, location type and modus operandi are the most significant RIFs. Therefore, manufacturers should be aware of these guidelines.
2. Leveraging Advanced Algorithms
Improving cargo security has become more challenging due to increased attack surfaces and opportunities for outside threats. In response, manufacturers must leverage advanced technologies like artificial intelligence (AI) and machine learning (ML) to protect their assets. Algorithms are excellent tools for business owners because they reduce the theft risk when transporting goods on the road.
A 2024 study published in Computers and Industrial Engineering used a physical internet-based analytic model to combat rising cargo theft. The researchers used real-world scenarios in their experiments to understand the benefits and drawbacks. Their model determined the risk of different product types based on their specific routes, allowing them to better understand the threshold where shipments become vulnerable to criminal organizations.
3. Using the Internet of Things (IoT)
IoT devices are critical for management operating systems (MOS) because they enhance software and hardware capabilities. With these gadgets, manufacturers can improve productivity and financial performance. IoT research is also critical for securing cargo through each step of transit. For instance, GPS technology provides real-time knowledge of each shipment.
Manufacturers should take advantage of IoT because it can be present with the device and around the facility. Smart cameras are an excellent example because business owners can remotely monitor the feeds and promptly take action. Advanced technology also lets manufacturers take extra steps to protect their cargo. Smart locks with biometric recognition are a vital safeguard against thieves.
4. Improving Cybersecurity Practices
Cargo theft increased by 46% in the first quarter of 2024 compared to the same time in 2023. CargoNet reported 925 incidents in the quarter, emphasizing the need for heightened security tactics. While physical barriers are necessary, manufacturers should also improve their cybersecurity practices. Internet crime is equally damaging to companies and could be more challenging to predict.
Ransomware attacks are among the most pivotal for manufacturers, considering their frequency. A 2022 IBM report found that 23% of these incidents affected manufacturing, making it the most targeted industry. Preventing ransomware attacks entails basic to advanced cybersecurity tactics, such as multifactor authentication, anti-malware software and software updates.
5. Selective Supplier Partnerships
Some manufacturers outsource specific tasks to reduce overhead and strengthen their bottom line. In addition to these partners, companies must watch other links in the supply chain. Businesses should monitor supplier relationships to ensure security — otherwise, they risk lost revenue and downtime while fixing errors.
Supplier relationships start with background checks and regular audits. Manufacturers must ensure these partners do their best to detect and address vulnerabilities. Business owners should find companies with pertinent industry certifications like C-TPAT if applicable. Monitoring should continue throughout the relationship with consistent communication and key performance indicators (KPIs).
6. Properly Training Employees
While suppliers can be security liabilities, it’s equally essential for manufacturers to monitor their employees. Workers may willingly or unknowingly contribute to cargo theft through their actions, so businesses should protect them from themselves. First, company leadership should train employees on best security practices, such as reporting procedures and proper loading.
Then, the company should focus on internal theft from its workers. Experts say over 75% of employees have stolen from their employer at least once. Therefore, robust internal measures should be in place to prevent theft. Mitigating employee stealing includes restricting access control and using biometric scanners. Business owners could also encourage workers to be vigilant of suspicious activity.
7. Controlling Supply Chain Aspects
Ultimately, it’s up to manufacturers and business owners to control as many supply chain aspects as possible. Internal audits are a valuable tool because they reveal gaps in shipments and where theft has potentially occurred. Once a company understands its insufficiency, leadership teams can act accordingly. Businesses should audit their inventory, security and other critical business features.
Supply chain professionals should also regain control in areas they may consider less secure, such as transit. Highways and oceans provide plenty of unknowns, so businesses must protect their cargo before, during and after the route. Besides GPS devices, forward-thinking companies wield electronic seals, telematics devices, light sensors and other tech.
Tackling Theft and Protecting Assets
The rise in cargo theft should alarm manufacturing professionals and business owners. Outside threats have become more sophisticated through physical and cybersecurity risks. While crimes have increased, manufacturers should proactively combat thieves. Leadership teams should scrutinize suppliers, employees and other aspects of the supply chain to ensure safety.
*This article is written by Jack Shaw. Jack is a seasoned automotive industry writer with over six years of experience. As the senior writer for Modded, he combines his passion for vehicles, manufacturing and technology with his expertise to deliver engaging content that resonates with enthusiasts worldwide.
It’s no secret to most that since the COVID-19 pandemic began, there have been unprecedented economic and logistical disruptions experienced on a global scale. Supply chains were particularly hard hit by the pandemic as production and shipping were halted around many parts of the world.
In the United States, ports saw decreased demand and were forced to switch from working around the clock to minimal hours. While this led to a significant decrease in shipping times, it also resulted in ships waiting at sea for weeks before they could dock. For organizations that rely on these ports, this slowdown in productivity led to a great deal of anxiety about deliveries and customer service.
However, in the last several months, there has been a dramatic turnaround in the ports of the United States. Backlogs are starting to clear, and ships can dock in much shorter time frames than before. Does this mean that everything is back to normal? Not exactly.
The State of Global Shipping
At the height of the pandemic, there was a shortage of containers due to the decrease in demand for shipping services and ports operating at limited hours. This caused ships to wait longer than usual to dock, leading to a bottleneck in supply chains disrupted by COVID-19. As a result, many depots had difficulty meeting customer demands, and there was a corresponding drop in consumer confidence.
Now, there is a surplus of containers due to increased demand for shipping services, and ports are back up and running at full capacity. This has created a new challenge for container depots, as space is filling up quickly, and there is nowhere for the containers to go.
Perhaps one of the most positive changes since the pandemic began is the freight rates. During the first two years of the pandemic, cargo freight rates recorded the most significant spike, but shipping cost has returned to pre-pandemic levels. This is a welcome sign for those in the industry, making it easier for companies to get their goods out without destroying their margins.
Unlike last year, retailers now have more than enough inventory. As a result, warehouses are operating close to full capacity, and space is increasingly limited. This has led to a slight uptick in storage rates and an increase in the cost of warehousing, but these are expected to level off once the market stabilizes.
While the inventory situation may have improved for retailers and distributors, ordering has significantly slowed for manufacturing factories. Until current inventory levels return to normal, it’s expected that production facilities will have a difficult time ahead as work dries up and demand for resources is limited. This may mean closures or layoffs in the manufacturing sector, which could have a ripple effect on the entire supply chain.
Container repositioning and movement have also been disrupted, creating a new problem for supply chains. Container ships are now struggling to move empty containers from ports of loading to ports of discharge. This could result in congestion and delays, which is something that supply chains have been trying to avoid since the pandemic began. Now, blank or canceled sailings are on the rise ahead of the year’s most significant spending period.
What These Conditions Indicate for Shipping
Overall, it appears that while the situation has improved since the beginning of the pandemic, there is still a lot of work to be done before things return to normal. There are still backlogs, container shortages, and an increase in storage costs, which could lead to further production slowdown.
The mindsets of consumers are also drastically shifting. As inflation has increased this past year exponentially, customers may become more price sensitive and look for cheaper alternatives. This could mean that businesses will need to re-evaluate their pricing strategies to continue to remain competitive in the market while being forced to sacrifice their margins.
Another thing to consider is the total cost of shipping, which includes fuel costs, port fees, and labor. The increase in global demand for resources has raised these costs across the board. As a result, companies may be forced to adjust their budgets or look for alternative suppliers and routes to keep their operations running efficiently. While this may not be enough to cover the full cost of shipping, it could make a difference in the long run.
Shippers also need to prepare for new challenges with canceled sailings, and some ports skipped altogether. This could leave importers and exporters scrambling to find alternative routes or adjust their supply chains accordingly. Unlike last year, many ports are functioning at full capacity, but there is still a need for increased efficiency and cost-saving measures to ensure the smooth transportation of goods.
Looking Forward
It’s clear that the shipping industry is going through a challenging period, but there are still positives to take away. Freight rates have returned to pre-pandemic levels, and warehouses are operating close to full capacity. The biggest challenge right now appears to be coping with the new norm of consumer demand and figuring out how to balance cost with competitive pricing.
Regardless of the challenges, shippers should remain optimistic and continue to look for ways to adjust their operations accordingly. By leveraging existing technology, adapting strategies, and staying ahead of market trends, shippers can ensure that their supply chains remain profitable and efficient in the long run.
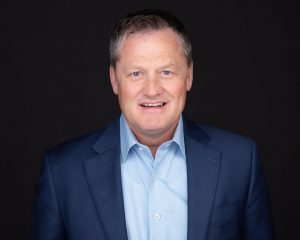
David L. Buss
*This article is written by David L. Buss. David is CEO of DB Schenker USA, a 150 year old leading global freight forwarder and 3PL provider. David Buss is responsible for all P&L aspects in the United States, which is made up of over 7,000 employees located throughout 39 forwarding locations and 55 logistics centers.
Supply chain analytics refers to the collection of data and information that provide insights into logistics performance, from inventory management to fulfilling and shipping orders.
How Data Analytics is Changing the Supply Chain Landscape
The ever-increasing reliance on big data is altering the landscape of supply chains as we know them. Historically, the majority of supply chain management was dependent on intuition and experience. However, with the introduction of powerful data analytics technologies, supply chains are now guided by data-driven decision making.
The ever-increasing availability of data is driving this transition. Previously, data was dispersed across numerous silos inside a business, making it difficult to provide a comprehensive perspective of the supply chain. Organizations, on the other hand, may collect and store data from all areas of the supply chain in one central location owing to data warehouses and data lakes. This enables supply chain managers to see the entire picture and make data-driven decisions to increase efficiencies and performance.
The rising availability of strong data analytics tools is another factor pushing the change to data-driven decision making. To examine data in the past, supply chain managers had to rely on manual procedures or limited software tools. However, a wide range of powerful data analytics technologies is now available to assist managers in making sense of massive data sets and uncovering hidden patterns and trends. The transition to data-driven decision making is reshaping the supply chain landscape and has far reaching implications for how businesses function.
Organizations may improve the efficiency and performance of their supply chains by leveraging the power of data, providing them with a competitive advantage in the marketplace.
The Advantages of Data Analytics in Supply Chain Management
Data analytics can aid in the smooth and effective operation of supply chains. Supply chains can uncover patterns and trends in past shipments by examining data from previous shipments. This can help them minimize disruptions and stock-outs while also improving inventory management. Furthermore, data analytics can assist supply chains in optimizing their routes and schedules, as well as tracking their success over time.
Here are some of the primary advantages of employing data analytics in supply chain management:
- Reduced Inventory Costs
- Optimized Production Plans
- More Efficient Cargo Shipments
- Reduced Risks
- Cross-Functional Cooperation
Check out the following infographic by 2Flow which takes a deep dive into ‘Analytics In The Supply Chain’.
Supply chain analytics are guiding managers into the future with data-driven decision making. If you need assistance properly analyzing your data and setting up your supply chain management for success, contact USC Consulting Group today.
Yes, it’s that time again. The holiday season is around the corner and it is time for manufacturers to start preparing now.
Most holiday sales will come from online shopping, adding stress to supply chains and the warehousing industry. With proper management, it’s possible to plan to sustain efficient operations despite volume increases and demand.
Managers can analyze the warehouse itself and equip employees and equipment with the necessary tools to make it through the season. What techniques work and what should warehouse managers prioritize among their already lengthy to-do lists?
Preparing Warehouses for Increased Inventory
It’s time to walk the warehouse and analyze the state of everything. Is it already almost bursting with regular inventory, or is there clutter in the walkways? How much space could the warehouse reappropriate for enhanced storage solutions? What maintenance should be conducted to help bear the load of surplus inventory, spatially and financially?
Work with your logistics team on this walkthrough, which should happen long before the holidays hit, to allocate enough time to make renovations or install new structures. Rethinking the floor plan can reveal space optimizations and efficiency modifications, such as more efficient routes for workers and automated machines to pack expediently.
Countless systems and programs can help automate and streamline previously complicated inquiries and tasks, including:
- Implementing scheduling software to help employees trade shifts or sign up for overtime.
- Setting up cameras and other monitoring systems to check everything from maintenance to productivity.
- Choosing the optimal warehouse management system to keep tabs on inventory.
- Collaborating with relevant members of the supply chain with cloud-based blockchain tech, keeping communications open in case of delays or changes.
Your tech stack – the tech that synergizes to make your company run seamlessly – should receive adequate maintenance to ensure technology isn’t the reason for outages or stops in production. Suppose your warehouse does not have any or just a few of these technologies. In that case, this may be a time to invest, because they are long-term solutions that will continually provide benefits outside of the holiday season.
This is the prime time to reflect on the strategies that worked in the previous holiday seasons and what could be improved. Interview the workers to gather perspectives from those who were in the fray last time inventory demand was at its peak.
Readying Workers for Increased Demand
The topmost priority is ensuring the warehouse has enough staff to handle the holidays. It’s helpful to analyze analytics and demand forecasts from the past to make accurate assessments of staffing needs. This will ensure incoming and tenured staff feels supported by the company if they know management gives proper attention to employee well-being and workload distribution.
This doesn’t only include floor staff – extra hands in payroll and human resources to help with scheduling will probably be necessary. They must be equipped with the right resources to adjust for fluctuating employee numbers throughout the holiday season.
Do not resort to increasing hours to adjust for long days, as this will cause turnover and burnout, potentially leaving the success of your holiday season – and after – in jeopardy. It’s vital to prioritize retention during this time, as seasoned staff members can assist with helping seasonal entrants acclimate more quickly to the working environment.
Providing training beforehand will instill accurate expectations for work hours – which could extend past the holiday season due to potential returns – and holiday wages.
On top of having adequate staff is training existing and upcoming staff to mentally and physically prepare them for volume. This combines with informing staff of any changes made to the warehouse, including program updates and organizational shifts that will help efficiency. For mental preparation, ensure employees have access to resources to manage stress to help keep productivity level.
Equipping Shipping Fleets for Holiday Weather and Traffic
Safety is paramount when it comes to holiday shipping. Fleets must be ready to take on the climate shifts in the region while making deliveries on time.
There are plenty of ways to ensure the warehouse’s fleet can withstand holiday conditions. Vehicle maintenance will not only save money by keeping vehicles healthier, longer, but also save on potential injuries in the workplace by keeping employees safer. With hundreds of thousands of fleet vehicles preparing to travel for peak season, it’s also about keeping everyone else on the road safe.
Checking brake pads, tires, and windshield wipers are inexpensive and basic improvements on top of more complex modifications like stronger batteries.
Provide employees with training to know what precautions to take on the road. They must receive as much training as warehouse staff to communicate about and acclimate to unexpected holiday situations. Are they aware of alternate travel routes or how to react in a severe storm?
Warehouses must prep the fleet with insurance and real-time locating system (RTLS) technologies. Especially since the holidays provide the most intensive time crunch of the year, knowing how well your current shipping system is meeting expectations can help you make adjustments along the way to improve efficiency.
It also provides the warehouse and customers with peace of mind, knowing their packages will safely make it to their houses.
Warehouses Prepare for the Holiday Season
Though the holidays can feel overwhelming for anyone in consumer industries, it’s possible to deal with the work gracefully. These timeless strategies allow warehouse managers to find improvements and discover the tactics that genuinely make a difference.
Making necessary adjustments to your warehouses, training employees, and creating safe shipping environments will also reinforce strategies to use in subsequent seasons.
* This article is written by Devin Partida. Devin is a tech writer with an interest in the IIoT and manufacturing. She is also the Editor-in-Chief of ReHack.com.
When is the last time you can remember logistics dominating the headlines? Rarely has this industry gotten this much press. That’s because the public is feeling what we who work with logistics have known for awhile — bottlenecks and supply chain disruptions have led to an unprecedented level of delay transporting goods from point A to point B.
Foreign suppliers have been stymied because of travel restrictions as a result of complex and confusing vaccination and testing processes. But even when the cargo arrives, ports on both coasts of the U.S. are filled to the brim with container ships, backed up like a logjam because there are no trucks available to transport those containers to where they need to go.
As anyone involved with the industry knows, logistics is the unsung hero of the American economy. The public rarely thinks about how the product they’re putting into their grocery cart made its way to the store, but they sure notice when it’s not on the shelf.
The problem has gotten so bad that it has captured the attention of the media and even the White House.
All eyes are on logistics right now
This past month, logistics and supply chain disruptions have been the lead story on the evening news night after night, with reporters stationed at ports shooting footage of the enormous backlog of containers. News articles are advising consumers on how to plan for empty shelves in their local grocery store or worse yet, the toy stores around the holidays. Remember the toilet paper shortage of 2020? It’s on the horizon again. Parents are urged to shop now for holiday gifts for their kids.
The problem has become so dire that the White House launched the Supply Chain Disruptions Task Force in June, which focused on bottlenecks that are bedeviling everyone in the logistics industry. As part of that, President Biden named a “Port Envoy” specifically charged with driving coordination between private companies who run the transportation industry and the logistics supply chain.
At the UN General Assembly earlier this fall, heads of state worldwide got a letter from the International Chamber of Shipping (ICS) warning of a global transport system collapse if governments don’t restore freedom of movement to transport workers.
The government doesn’t have to tell the logistics industry about the problems it has been facing since 2020. And typical bureaucratic red tape might suggest they’re not going to snap their fingers and fix what’s wrong immediately. So what can logistics companies do to make sure the goods they deliver will keep rolling?
At USC Consulting Group, we’ve been helping companies navigate all types of crisis situations for more than fifty years. In this two-part blog, we’ll highlight some of the strategies we’re recommending to our clients.
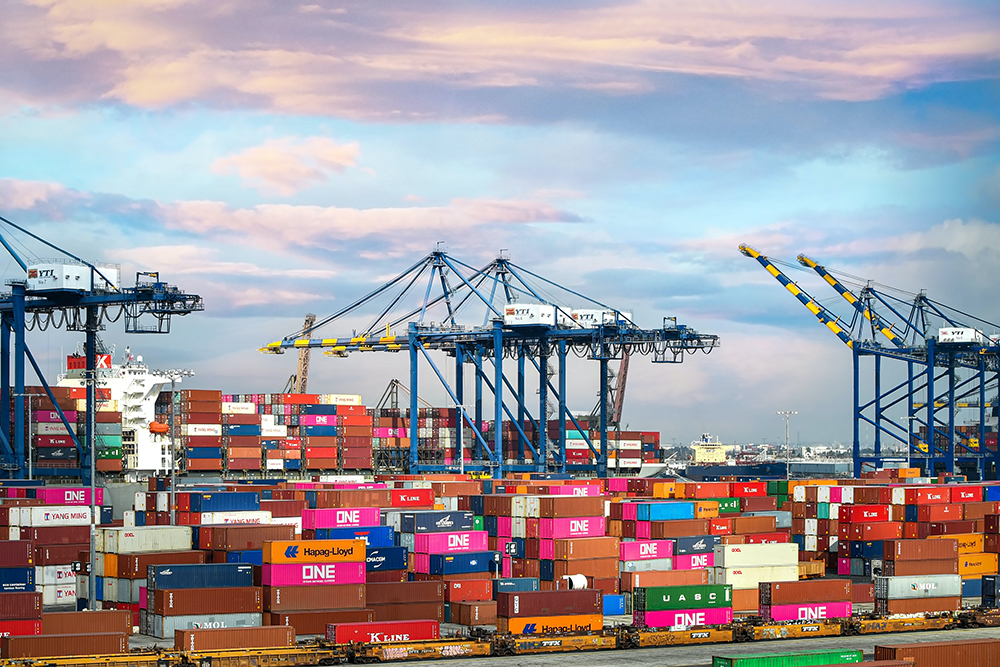
Shipping containers pile up at the Port of Los Angeles
Rethink foreign supply chains
Having Asia as a supply partner has long been seen as a way to cut costs. But that business model had been fraying at the edges even before the pandemic unraveled it. According to the 2022 26th Annual Third-Party Logistics Study, 83% of shippers saw supply chain disruption this year, and 68% of logistics pros believe supply chains have become too global. Looking for domestic suppliers is vital. And it’s not necessarily about the pandemic. Yes, the issue of pandemic-based restrictions and hold-ups exists now, but when this pandemic is in our collective rear-view mirror, it’s still vital to have more domestic suppliers. That’s because trade policies, diplomatic relations, tax laws, and governmental regulations can change, putting your supply chain in jeopardy.
Make operations more efficient by taking a 360-degree look
We specialize in making operations more streamlined by looking for hidden opportunities for efficiency that exist in your current processes and procedures. Will this solve the problem of your containers sitting at a port instead of being on the road? No. But making sure your internal operations are running at optimal efficiency will help balance your bottom line in the event more slowdowns occur.
Use SIOP to perfect supply levels
You’re probably familiar with sales and operations planning (S&OP), a process that involves sales forecast reports, planning for demand and supply, and other factors. It’s useful, but we think it’s incomplete. Inventory is left out of the mix. If you’ve been using S&OP, we encourage you to use sales, inventory, and operations planning, that factors in your all-important inventory. For more information on SIOP and how it can increase your operations efficiency, download our free eBook, Sales, Inventory, and Operations Planning: It’s About Time.
Ramp up your hiring
The trucking industry in particular is stretched extremely thin when it comes to drivers. All industries are experiencing a hiring crunch right now, and logistics needs to step up its hiring game to entice more people to sign on to the great jobs in transportation. That means competitive pay, solid benefits, and generous PTO.
In Part 2 of this topic, we look deeper into the Third-Party Logistics Study and go into more recommendations for moving logistics forward.
Go to Part 2 of Moving Logistics Forward series →
When you think of shipping and transportation, perhaps the last thing you consider is the threat that cybercrime can pose to the industry. However, as technology advances and systems become increasingly connected to online networks, cybersecurity is a necessity of modern shipping logistics.
Meanwhile, all kinds of digital attacks are increasing against a wide variety of industries. In this dangerous landscape, shipping companies must build strategies and implement processes that increase the safety of their digital systems.
From the rising threats to the evolving role of cybersecurity in shipping logistics, here’s what you should know.
The Rising Threat
When the COVID-19 pandemic struck, shutting down economies and causing widespread financial uncertainty, hackers took it as an opportunity to increase their malicious efforts. As many as 90% of surveyed IT leaders said they experienced an increase in cyber attacks due to the pandemic. Meanwhile, 93% said they had to delay key security projects in order to manage remote-work transitions.
This demonstrates the vulnerability of online global systems. Threats like the Kwampirs malware are running rampant and IT leaders are caught off-guard while attempting to deal with other pressing concerns.
But what does this have to do with the shipping logistics industry?
All kinds of new and highly connected technologies are propagating in the fleet management market. These innovations consist of sensors and monitors in the form of Internet of Things (IoT) devices, AI route-improvement software, and Advanced Driver Assistance Systems (ADAS) that improve driver safety through assisting with difficult and repetitive tasks. These in-vehicle monitoring systems bring location tracking and enhanced driver analytics to fleet management, creating altogether safer roads.
But what happens if these systems get hacked?
June of 2017 was a preview of exactly that. When 80 logistics and transportation ports were struck by ransomware, shipping company A.P. Moller-Maersk lost $300 million. Meanwhile, many deliveries were held and drivers forced to idle. The attack disrupted a complex supply chain and the effects rippled through various markets.
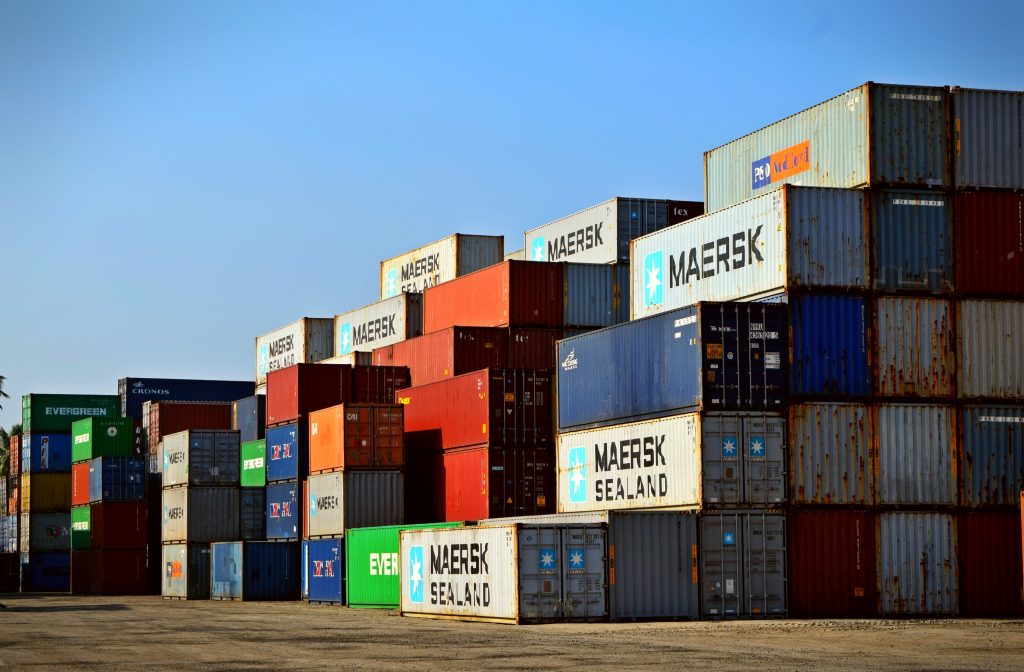
A.P. Moller-Maersk lost $300 million in 2017 due to a cyber attack.
As we come to increasingly rely on connected tech and even fully autonomous vehicles, the threat of cyberattack can be dangerous both financially and physically. Fortunately, there are a few simple steps you can take to better ensure supply chain cybersecurity.
Initiatives to Enhance Cybersecurity
Cybersecurity is needed in virtually every industry in today’s highly digital world. Securing your systems, however, can be difficult without the right professional assistance and reliable data services.
But finding the right help can be a challenge in its own right. Information systems professionals are in high demand, especially in the manufacturing and supply sector, where experts with the right skill set can earn their piece of a $2.17 trillion market.
Additionally, all kinds of IT personnel can build a better approach to secure shipping logistics through strategies like the following:
1. Assess compliance standards across the board.
A variety of data security standards are present across industries, such as HIPAA in healthcare or PCI-DSS in retail. Ensure all third-party suppliers and vendors meet relevant standards to facilitate safer information transfer.
2. Secure your software.
Software can be a vulnerability in supply chains. Protect yours with firewalls, VPNs, Transport Layer Security (TLS), and more to better ensure the safety of your networks and equipment.
3. Limit and monitor access.
Every user should maintain their own strong passwords and clearances. Data systems like blockchain can be helpful in securing information behind individualized user authorization keys, complete with immutable timestamps recording access to the system.
4. Educate your employees.
Avoiding a data breach can come down to simply educating your employees on avoiding links from unknown senders. Ensure all shipping logistics workers understand the importance of strong private passwords and maintain an awareness of common phishing practices.
5. Continuously run vulnerability assessments.
Risk assessments should be run at consistent intervals to help keep systems updated and functioning with the protections they need. Your assessments should include all IoT devices and networked equipment that could present an access point for an attacker.
When it comes to securing the digital systems throughout your shipping logistics processes, each of these strategies can mean the difference between a data breach or a prevented hack. Ensure your current systems are protected by a thorough baseline of SSL and VPN usage. Then, keep your employees educated in digital hygiene.
Evolving Roles in Cybersecurity and Logistics
With a comprehensive and consistent analysis of your data systems, you can mitigate the potential of a costly cyber attack. As our use of tech increases, cybersecurity will continue to play a greater role in shipping logistics.
Much like how a barcode system is now essential to inventory management, digital tools and AI technology are essential to managing supply chains with a modern edge. Systems like delivery and route management software can be the perfect way to increase your shipping efficiency, but the payoff won’t be nearly as great if your systems are compromised by malware.
Roles within shipping logistics are changing in consideration of the virtual shift. Understand the shifting nature of the industry and implement cybersecurity best practices like these to better protect your supply chains.
This article is written by guest author Beau Peters. View more of Beau’s articles here.
The trend towards automation is progressing all the time. With the advent of COVID-19 creating employment concerns amid a changing workforce, the role of automation in manufacturing has taken on new meaning.
Now, robotics looks to automate processes for the increased safety and productivity of the modern factory. There are many ways that automation trends are reshaping the industry. Here, we will look at a list of these trends and the ways they are altering global trade.
From faster processes to 3D printing innovations, automation in manufacturing looks much different than it has in past decades. Here’s what you should know.
1. Making Processes Faster and More Efficient
One report found that automation at a macroeconomic scale could increase global manufacturing GDP between 0.8% and 1.4% per year. While those numbers might seem small, the overall impact in economic growth is substantial.
Paired with increased productivity, automation offers the following benefits:
- Labor cost savings
- Improved safety
- Enhanced quality
- Overall efficiency
Currently, substantial losses in production time and energy occur in fighting human error and clunky procedures. With automated systems, efficiency can be integrated amidst better processes for fighting energy drains like friction. This translates to potentially millions of dollars in increased revenues for manufacturers that adopt automation technology.
2. Collecting Data Through Digital Twinning
Improving manufacturing processes is possible through the trend of digital twinning changing the manufacturing landscape. Digital twinning involves virtually modeling the manufacturing process alongside the real-world system. Doing so allows companies to gather valuable data and models for simulation and experimentation.
With 50% of large manufacturers set to utilize this tech by 2021, digital twinning represents the future of manufacturing. And for good reason. Up to 30% of improvements in product quality and product cycle time are possible thanks to digital twinning, allowing companies to pair data with experimentation for revenue-boosting results.
3. Increasing Safety Through Robotics
The emergence of COVID-19 changed the way businesses manage a workspace. This is true as well for factory floors where workers have to adopt sanitation and social distancing measures. Robotics allows for the safe implementation of these policies without increased human risk.
A series of roles are now increasingly being filled by robots to allow for greater safety procedures. These include:
- Assembly Line — Working side-by-side with humans are automated systems known as co-bots. On the assembly line, these co-bots are enhancing productivity while making social distancing increasingly possible.
- Sanitation — With COVID-19 concerns, more janitorial robots are being integrated to help sanitize workspaces. These robots go beyond the average Roomba, ensuring the cleanliness of shared spaces for employee safety.
- Heavy Lifting — The constant movement and shuffling of parts and packaging in the manufacturing industry create risks for human workers. Robots can reduce that risk while efficiently moving and hauling heavy objects across a factory.
With sanitation and dangerous work now being filled by robots, factory workers can enjoy a greater level of safety. This not only increases productivity for manufacturers but reduces liability risks and costs as well.
4. Focusing on Logistics for Better Processes
Artificial intelligence. The term might invoke fear in movie-going circles, but the integration of AI in manufacturing to enhance the logistics of every process is reshaping the industry.
AI relies on the accumulation of manufacturing data to provide streamlined logistics workflow. This means sensors, digital twinning, analytics, and more to truly understand and predict factory success. With each new data set, an AI can better learn a system, inform technicians of when maintenance is needed, and build better models for an effective process.
With all the implications for manufacturing improvement, AI is one trend of industrial robotics sure to last long into the future.
5. Changing the Manufacturing Process Through 3D Printing
Automation of manufacturing is changing through the increasing use of additive processes, such as 3D printing. This automation trend has a huge impact on manufacturing of all types of products, with a wide range of materials including sustainable and plant-based options possible.
3D printing uses a digital blueprint to then produce a product from the bottom up, bit-by-bit. By building in this way, the efficiency and durability of parts can be maximized even when using alternative materials. This process means better products at potentially cheaper production costs as the technology improves. The ability for sustainable materials to be substituted in production also has beneficial implications for the environment.
The Changing Landscape of Manufacturing
As the world integrates new automation technology, manufacturers look to reap the benefits. From more efficient practices to better building techniques, manufacturing in the modern world has made substantial headway towards safety and sustainability. These technological trends enhance the safety and productivity of any manufacturing workforce, but the question has to be asked—how will automation affect displaced workers?
Currently, humans and robotics are working side-by-side to deliver better solutions. However, only time will tell how workers adapt to increased automation in the new landscape of manufacturing technologies.
This article is written by guest author Beau Peters. View more of Beau’s articles here.
The last couple of decades have seen some significant changes affecting the logistics industry, and the supply chain as a whole. New regulations to working practices have forced fleets to more carefully monitor drivers, and make adjustments to ensure efficiency is maintained. The driver shortage also remains a problem, with some agencies predicting that the deficit could rise to 160,000 within the next decade.
Rising alongside these challenges, though, are technological advances. Some of them have the potential to help solve the prevalent issues of our industry, others could transform the shipping business as we know it. Technology continues to develop at a rapid rate, and advances such as artificial intelligence (AI) and autonomous vehicles are already starting to make an impact in the logistics industry.
We’re going to take a look at areas in which AI and autonomy both have the potential to alter the way the logistics industry does business, and how those we’ve already begun to embrace are developing. How might these affect the roles of workers in the sector, and what do we need to prepare for?
Fleet Management
Freight transportation is one of the most important industries to the health of the US economy. It not only provides a vital lifeline of essential products across the country, but it also gives us a valuable insight into consumer behavior and market fluctuations. When freight providers use tech tools to make their operations more efficient, there’s an opportunity to keep this indispensable economic resource serving the nation effectively.
For many companies, these operations take the form of ground freight — the use of fleets of trucks to quickly and cheaply deliver goods. In this sector, fleet management is an essential tool, which has also become one of the early adopters of AI software. With multiple mobile assets and constantly evolving variables such as road conditions and weather patterns, AI software does the grunt work of receiving and analyzing data. This software also factors in information from maps and vehicle service history, allowing for predictive maintenance. As a result, managers receive real-time predictions that allow them to make efficient advanced plans, and adjust them swiftly when conditions change.
One of the positives of utilizing AI in fleet management is its ability to keep learning. Collecting data from devices such as onboard vehicle diagnostics, GPS, and camera footage, the software is being fed evolving information that allows it to improve the predictions it makes. AI is reliant upon the quality of data and engaging with other tools that allow fleets to build better industry networks, and sharing important operational information can be key in giving AI platforms the information they need to bolster the entire logistics industry.
Safety Driven by Technology
Safety continues to be a key concern across the fleet industry. In recent years we’ve seen regulations come into effect that restrict the hours that drivers can be on the road, and technology — in the form of electronic logging devices that track drivers movements — is a mandatory feature in remaining DOT compliant. However, fleets have begun to look beyond these basic requirements to discover new ways for AI and autonomous tech to keep everyone safe.
Fully autonomous trucking is neither practical nor safe just yet and is unlikely to make an appearance for several years to come. However, some limited autonomy has found its way into trucks to improve safety. Adaptive cruise control is a prominent example of level 2 automation. It uses a combination of radar and a camera to detect the distance of objects in front of the truck, regulating the speed of the vehicle to reduce the potential for emergency braking.
These small, incremental improvements serve to gradually build confidence in the industry and the public. Legislators have started to approve certain aspects of autonomy, and as a result, we’ve started to see a ramping up of testing. Volvo and FedEx have recently trialed automated platooning in Europe, using vehicle to vehicle (V2V) communications systems and advanced driver assistance (ADA) to allow multiple trucks to maintain close distances behind one another on highways safely.
Staff Supported, Not Replaced
One of the key concerns surrounding automated systems such as self-driving vehicles and AI is their effect on employment. However, it’s been clear from the way in which this technology has been used and trialed in the logistics industry so far that the preference is to support workers rather than replace them.
Recently, UPS and Waymo teamed up to pilot autonomous package pickup in the Phoenix Metro area. This kind of short distance usage, to fill in the gaps for efficiency, could be an indicator of how autonomous trucking is likely to advance. Last-mile delivery is one of the areas in which there is a deficit of drivers, and there are expectations that this could be the key focus for autonomy, rather than long-distance driving.
It’s important to note that trials for full autonomy have required the presence of a human expert on board or in a supervisory role. This could also be an indicator of a change of career path for those in the trucking industry. Rather than removing jobs from the freight sector, automation could see a range of new skilled positions being introduced. Drivers could see their roles expanding to become on the road automation technicians, too. Though fleets may also need to start planning for the raise in salary level such high skilled workers will be able to command.
Progressing Forward
While we are not yet in a fully autonomous, AI-controlled world, elements of this technology have started to appear across the logistics industry. The slow and steady approach that the sector is taking allows us to assess where the challenges might lay, and make sensible adjustments accordingly. Workers and leaders alike need to watch how these advances are progressing, and plan to make changes in their investments and skill sets accordingly.
This article is written by guest author Beau Peters. View more of Beau’s articles here.