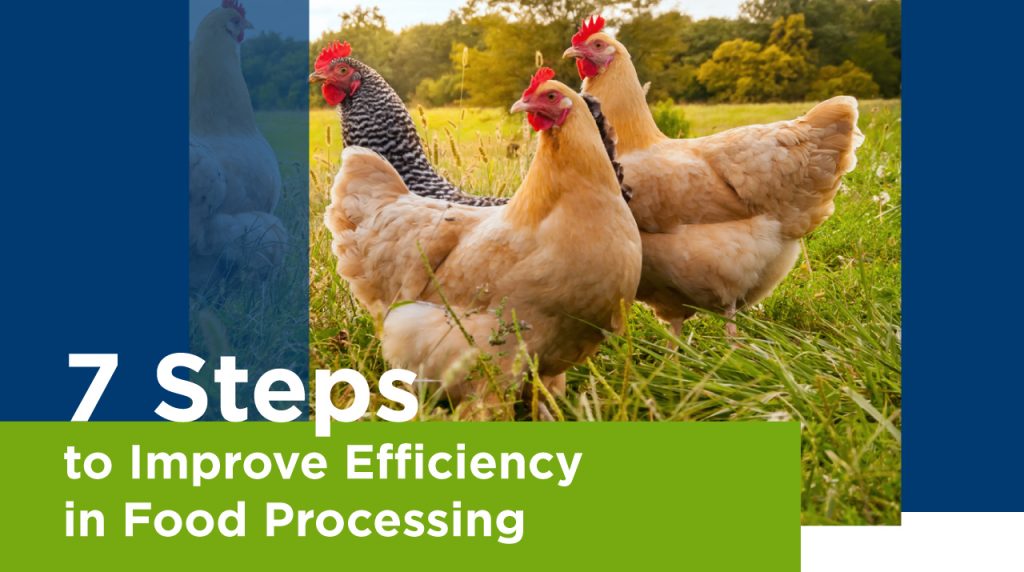
7 Steps to Improve Efficiency in Food Processing Immediately
In the food processing industry, optimal efficiency is the key to keeping those razor-thin margins in the black. Now, with ongoing challenges like supply chain delays and changing markets, it’s even more important.
Efficient processes lead to reduced operating costs, improved yield and throughput, and more control over your management systems.
The following graphic provides seven ways to improve your efficiency in food processing:
1. Identify loss points
Where are the opportunities for greater efficiency? Look at the equipment, like the grinder, blenders, transfer belts, oven, steamer, even the transportation and logistics. Where can you save time and money? A thorough loss point analysis can uncover key areas where more efficiency can be achieved.
2. Recipe/formula control
The goal here is to ensure accurate measurement of ingredients. To improve processes, use volumetric measuring, metering tools and “right size” recipes to match ingredient containers. It’s about containing costs and promoting formula consistency.
3. Calibrate measuring devices
You won’t get accurate measurements if the measuring devices are not functioning properly. All devices that provide “factual” information must be accurate! It means verifying the calibration of scales, load cells, meters and equipment speeds, temperatures, tolerances and capabilities.
4. Process control
Remember, any knob, dial, meter, switch or button can vary the process. It’s essential to understand what they control and what they reveal. Generate a thorough process run history to define the relationship (or correlation) of each control point to the end product.
5. Measure actual yield vs. plan
Challenge the current paradigms. How does yield loss vary when raw temps vary? How much do you lose if you extend cooking times? Are you batching properly? Focus on maintaining tolerances and capabilities, and monitor the causes of variation. It makes the invisible visible!
6. Audit fill weights
This is about understanding overfills. In the industry, they call it “the giveaway,” which happens when more product is added to a package to compensate for weight loss in processing. Shaving a bit off of each overfill can add up to huge savings.
7. Recovery and resolution
Review, report, resolve! Do a thorough root cause analysis, implement short-term fixes immediately, and seek to eliminate waste completely in the long run. Continuous improvement is the goal! Find opportunities for greater efficiency and help implement them.
It’s about developing a plan to measure performance, and ultimately getting to a “zero-loss based” yield. The more quickly and efficiently you get the job done, the sooner your product can be in the hands of the consumer. Questions? Contact us today.
For more information about how Food & Beverage consultants can significantly reduce your operating costs and improve productivity, read this eBook: