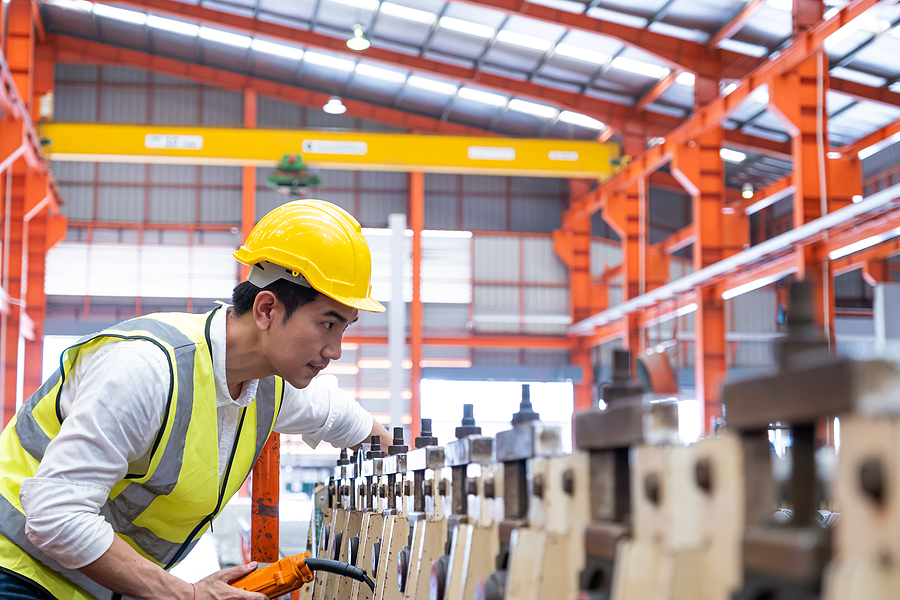
How to Utilize Statistical Process Control to Reduce Manufacturing Variability
Statistical process control (SPC) is a commonly used machine learning software in manufacturing that measures the consistency of a product’s performance based on its design specifications. Minimizing variability is a crucial part of avoiding defects and maintaining resilient manufacturing operations.
This guide outlines the different ways that businesses can effectively utilize SPC and reap all of the benefits this technology has to offer.
How Statistical Process Control Works
SPC is a tried and true technology that businesses have been using for more than 100 years to improve their manufacturing operations. It conducts ongoing statistical analyses, taking into account factors such as the materials, design, employees who handled the product and the machinery used to create the product.
SPC’s constant vigilance enables businesses to make swift and accurate resolutions to quality control problems. However, it’s not fully autonomous like other manufacturing software that can identify statistical correlations without human help. Instead, it relies on large amounts of training datasets that another source must manually input to achieve the desired results.
This form of machine learning is known as supervised learning. Businesses can input human-labeled datasets by themselves, or they can recruit another algorithm to automatically input statistics in a process called “machine annotation.” In either case, SPC needs to absorb as much raw data as possible to maximize its efficiency.
SPC displays its findings in easy-to-read control charts, and it’s the business’s responsibility to set the parameters for each chart by providing the software with enough information. This process includes six basic steps:
- Define the manufacturing process you want to monitor and control by establishing the input variables, output variables, equipment, materials and any other external factors that might affect the process.
- Collect the data that the software extrapolated from the variables you provided, then organize it into a digestible format — usually a chart or spreadsheet.
- Select and construct the control charts based on the type of data you’re using, such as weight, length, temperature and any defects that might have occurred.
- Look for patterns in the control charts that indicate special cause variations in performance due to underlying defects. You can calculate process variability through a capability index, such as C, Cpk, Pp and PPk.
- Investigate the root causes of the variations and make the necessary equipment, material or operational adjustments to correct them.
- Continue to collect and organize data to identify more variations, updating the control specifications as needed.
This process sounds awfully similar to Statistical Quality Control (SQC), but there are some key differences. Statistical Process Control measures independent variables, while SQC strictly focuses on dependent process outputs. SQC also carries out acceptance tests by screening individual product samples, while SPC relies on large datasets and doesn’t have an acceptance testing feature.
Types of SPC Tools
Many types of analysis tools have developed during SPC’s century-long evolution. These tools are split into two main categories — basic tools of quality (7-QC tools) and supplemental tools (7-SUPP tools). Here’s a quick rundown of how businesses can use the 7-QC tools:
- Stratification: separating data into subcategories by unique characteristics to clarify the origins of an existing problem.
- Histogram: A bar graph that displays the frequency of variability and the most common offenders.
- Check sheet: A document with tabular or metric format that tracks the number of special cause variations.
- Cause-and-effect diagram: A chart that shows all of the factors that lead to special cause variations and draws potential correlations between them.
- Scatter diagram: A dotted diagram that displays the overlap between dependent variables on the y-axis and independent variables on the x-axis.
- Control chart: A line-based graph that shows processes’ stability levels and pinpoints the likely variation within produced items.
- Pareto chart: This chart applies the 80/20 principle — 20% of variables cause 80% of problems — to display the most common causes of manufacturing failures.
Stratification also often appears in the 7-SUPP tools category because of its versatility and importance to statistical analysis. Breaking up large datasets into smaller digestible chunks makes SPC software more accurate at identifying problems and reducing variability. Here are the other six 7-SUPP tools:
- Flowchart: A straightforward diagram that outlines the step-by-step process of a manufacturing sequence.
- Defect mapping: A chart that shows the different types of known product flaws within a business’s manufacturing operations.
- Events logs: A variable summary showing the chain of events that resulted from an undesired occurrence.
- Progress centers: Centralized locations dedicated to tracking improvements and supporting informed decision making.
- Randomization: The deployment of random manual and automated input variables to eliminate human bias.
- Sample size determination: Choosing the number of subjects to include in a representative group when tracking manufacturing trends.
Today’s SPC software modules include all of these tools, allowing businesses to access dashboards that display the various charts and diagrams in one place. These insights can lead to identification of quantifiable improvement opportunities that maximize operational efficiency.
Benefits of Using SPC
SPC is one of the most effective machine learning resources for achieving consistent performance in manufacturing operations. Eliminating process errors allows businesses to simultaneously address the three biggest challenges in material handling — workplace hazards, equipment damage and carbon emissions — in many ways:
- Reduces manufacturing costs
- Monitors employee productivity
- Improves resource utilization
- Optimizes manual inspections
- Reduces rework and warranty claims
When these benefits combine, the final result is a more satisfied client base and a more profitable business. While SPC software can’t do all of the inspection work on its own, the tools and insights it provides are invaluable in a manufacturing environment.
Use Statistical Process Control to Its Full Potential
Business leaders who are willing to put in the necessary effort to provide SPC software with large datasets can use this technology to its full potential. They will gain access to numerous eye-opening statistics about operational inefficiencies and have all the knowledge they need to make accurate adjustments.
*This article is written by Jack Shaw. Jack is a seasoned automotive industry writer with over six years of experience. As the senior writer for Modded, he combines his passion for vehicles, manufacturing and technology with his expertise to deliver engaging content that resonates with enthusiasts worldwide.