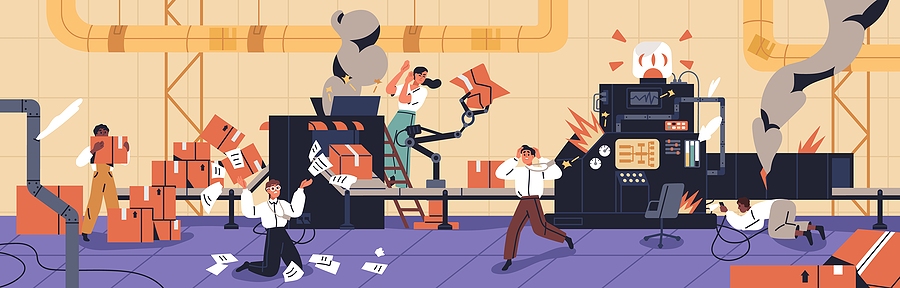
The ‘Permacrisis’ Era: How to Manage Your Operations to Overcome Instability
Last year, the London-based Collins Dictionary named “permacrisis” as the word of the year. It means an extended period of instability caused by an onslaught of seemingly never-ending crises — wildfires, pandemics, hurricanes, floods, inflation, air quality alerts, the highest heat ever recorded in some regions of the world, economic instability, wars… the list goes on. Sound familiar? You name it, we’ve all lived through it. And it shows no signs of slowing down.
In the immortal words of Gilda Radner on Saturday Night Live: It’s always something.
The way we see it here at USC Consulting Group, it IS always something. That’s called life. While the world may be going through an unusually rocky stretch, there is no perfect time to be running your business. Whether it’s external crises like the ones we’ve described, or internal upheavals like layoffs, mergers, unforeseen difficulties or the myriad hiccups that can occur, things are going to happen. When they do, companies can thrive, not just survive, with a mix of focusing on process improvements and operational excellence, optimizing your supply chain, and implementing standard operating procedures, along with a dash of the old-fashioned notion that “this too shall pass.”
Here are a few tactics for making sure you’re on solid footing, even during the rockiest of times.
Process improvements
The goal is operational excellence, right? But is that ever truly achievable? Yes, but it can also be a moving target. It means continuous improvements to processes, becoming as efficient as possible. We find that it’s about eliminating bottlenecks, waste and other snags that can impede productivity. Getting the right people in the right jobs and empowering them to get that job done. Developing standards and key process indicators that will tell you when you’re on target and when you aren’t, and using data to “manage by the numbers.”
Optimizing the supply chain: Don’t DRIP!
What’s DRIP? It’s a popular acronym when talking about supply chain. It stands for data rich, information poor. The fragility of the supply chain, no matter the industry you’re in, has become crystal clear in recent years. Optimizing your supply chain needs to be top of mind to make sure you don’t get caught short, and as DRIP suggests, it starts with making sure you’re using data to its fullest. Outdated inventory systems can impede that. Supply, Inventory and Operations Planning (SIOP) is a method we here at USC utilizes that emphasizes inventory as a strategic tool to allow businesses to get a better look at their operations and formulate superior strategy decisions.
SIOP gives you the ability to capture, analyze, integrate and interpret high-quality data, which is the key to staying ahead of the market. The aim is to achieve process automation and glean predictive analytics, which give you a strategic advantage… so you don’t DRIP.
Learn more about SIOP in this free eBook
Standard operating procedures (SOPs)
Much is being written in the news lately concerning “institutional knowledge,” and how the loss of it can be devastating to companies. What is it? It’s what’s NOT in your training manual. It’s what the person you think is “irreplaceable” knows. The ins and outs of doing the job that your best people learn through years of experience. When they retire, or leave the company for whatever reason, that knowledge walks out the door with them. That’s why it’s so important to develop standard operating procedures for every job in your company, and write those procedures down on stone tablets if necessary.
Comprehensive training
When you have those SOPs down, that’s just the first step. Training your people in exactly how to do the job, so everyone across all of your facilities is doing it in the same way, is vital.
Sound like a tall order? It can be. That’s where we come in. At USC Consulting Group, we have 55+ years of experience helping companies optimize their efficiency, ramp up their production, solidify those SOPs and operate to the max. If you’re wondering if now is the right time to hire an operations consultant, download our aptly named eBook, “When is the Right Time to Bring in Operations Consultants?” It’s free, and it will give you more information about how we can help your business.