-
Subscribe to Blog:
SEARCH THE BLOG
CATEGORIES
- Aerospace
- Asset Maintenance
- Automotive
- Blog
- Building Products
- Case Studies
- Chemical Processing
- Consulting
- Food & Beverage
- Forestry Products
- Hospitals & Healthcare
- Knowledge Transfer
- Lean Manufacturing
- Life Sciences
- Logistics
- Manufacturing
- Material Utilization
- Metals
- Mining
- News
- Office Politics
- Oil & Gas
- Plastics
- Private Equity
- Process Improvement
- Project Management
- Spend Management
- Supply Chain
- Uncategorized
- Utilities
- Whitepapers
BLOG ARCHIVES
- April 2025 (1)
- March 2025 (1)
- February 2025 (4)
- January 2025 (4)
- December 2024 (4)
- November 2024 (2)
- October 2024 (6)
- September 2024 (5)
- August 2024 (5)
- July 2024 (6)
- June 2024 (3)
- May 2024 (3)
- April 2024 (4)
- March 2024 (3)
- February 2024 (4)
- January 2024 (5)
- December 2023 (2)
- November 2023 (1)
- October 2023 (6)
- September 2023 (3)
- August 2023 (4)
- July 2023 (2)
- June 2023 (3)
- May 2023 (7)
- April 2023 (3)
- March 2023 (3)
- February 2023 (5)
- January 2023 (6)
- December 2022 (2)
- November 2022 (5)
- October 2022 (5)
- September 2022 (5)
- August 2022 (6)
- July 2022 (3)
- June 2022 (4)
- May 2022 (5)
- April 2022 (3)
- March 2022 (5)
- February 2022 (4)
- January 2022 (7)
- December 2021 (3)
- November 2021 (5)
- October 2021 (3)
- September 2021 (2)
- August 2021 (6)
- July 2021 (2)
- June 2021 (10)
- May 2021 (4)
- April 2021 (5)
- March 2021 (5)
- February 2021 (3)
- January 2021 (4)
- December 2020 (3)
- November 2020 (3)
- October 2020 (3)
- September 2020 (3)
- August 2020 (4)
- July 2020 (3)
- June 2020 (5)
- May 2020 (3)
- April 2020 (3)
- March 2020 (4)
- February 2020 (4)
- January 2020 (4)
- December 2019 (3)
- November 2019 (2)
- October 2019 (4)
- September 2019 (2)
- August 2019 (4)
- July 2019 (3)
- June 2019 (4)
- May 2019 (2)
- April 2019 (4)
- March 2019 (4)
- February 2019 (5)
- January 2019 (5)
- December 2018 (2)
- November 2018 (2)
- October 2018 (5)
- September 2018 (4)
- August 2018 (3)
- July 2018 (2)
- June 2018 (4)
- May 2018 (3)
- April 2018 (3)
- March 2018 (2)
- February 2018 (2)
- January 2018 (1)
- December 2017 (1)
- November 2017 (2)
- October 2017 (2)
- September 2017 (1)
- August 2017 (2)
- July 2017 (2)
- June 2017 (1)
- April 2017 (3)
- March 2017 (3)
- February 2017 (2)
- January 2017 (2)
- December 2016 (2)
- November 2016 (4)
- October 2016 (4)
- September 2016 (3)
- August 2016 (6)
- July 2016 (4)
- June 2016 (4)
- May 2016 (1)
- April 2016 (3)
- March 2016 (4)
- February 2016 (2)
- January 2016 (4)
- December 2015 (3)
- November 2015 (3)
- October 2015 (1)
- September 2015 (1)
- August 2015 (4)
- July 2015 (6)
- June 2015 (4)
- May 2015 (7)
- April 2015 (6)
- March 2015 (6)
- February 2015 (4)
- January 2015 (3)
CONNECT WITH US
Tag Archives: U.S. Ports
It’s no secret to most that since the COVID-19 pandemic began, there have been unprecedented economic and logistical disruptions experienced on a global scale. Supply chains were particularly hard hit by the pandemic as production and shipping were halted around many parts of the world.
In the United States, ports saw decreased demand and were forced to switch from working around the clock to minimal hours. While this led to a significant decrease in shipping times, it also resulted in ships waiting at sea for weeks before they could dock. For organizations that rely on these ports, this slowdown in productivity led to a great deal of anxiety about deliveries and customer service.
However, in the last several months, there has been a dramatic turnaround in the ports of the United States. Backlogs are starting to clear, and ships can dock in much shorter time frames than before. Does this mean that everything is back to normal? Not exactly.
The State of Global Shipping
At the height of the pandemic, there was a shortage of containers due to the decrease in demand for shipping services and ports operating at limited hours. This caused ships to wait longer than usual to dock, leading to a bottleneck in supply chains disrupted by COVID-19. As a result, many depots had difficulty meeting customer demands, and there was a corresponding drop in consumer confidence.
Now, there is a surplus of containers due to increased demand for shipping services, and ports are back up and running at full capacity. This has created a new challenge for container depots, as space is filling up quickly, and there is nowhere for the containers to go.
Perhaps one of the most positive changes since the pandemic began is the freight rates. During the first two years of the pandemic, cargo freight rates recorded the most significant spike, but shipping cost has returned to pre-pandemic levels. This is a welcome sign for those in the industry, making it easier for companies to get their goods out without destroying their margins.
Unlike last year, retailers now have more than enough inventory. As a result, warehouses are operating close to full capacity, and space is increasingly limited. This has led to a slight uptick in storage rates and an increase in the cost of warehousing, but these are expected to level off once the market stabilizes.
While the inventory situation may have improved for retailers and distributors, ordering has significantly slowed for manufacturing factories. Until current inventory levels return to normal, it’s expected that production facilities will have a difficult time ahead as work dries up and demand for resources is limited. This may mean closures or layoffs in the manufacturing sector, which could have a ripple effect on the entire supply chain.
Container repositioning and movement have also been disrupted, creating a new problem for supply chains. Container ships are now struggling to move empty containers from ports of loading to ports of discharge. This could result in congestion and delays, which is something that supply chains have been trying to avoid since the pandemic began. Now, blank or canceled sailings are on the rise ahead of the year’s most significant spending period.
What These Conditions Indicate for Shipping
Overall, it appears that while the situation has improved since the beginning of the pandemic, there is still a lot of work to be done before things return to normal. There are still backlogs, container shortages, and an increase in storage costs, which could lead to further production slowdown.
The mindsets of consumers are also drastically shifting. As inflation has increased this past year exponentially, customers may become more price sensitive and look for cheaper alternatives. This could mean that businesses will need to re-evaluate their pricing strategies to continue to remain competitive in the market while being forced to sacrifice their margins.
Another thing to consider is the total cost of shipping, which includes fuel costs, port fees, and labor. The increase in global demand for resources has raised these costs across the board. As a result, companies may be forced to adjust their budgets or look for alternative suppliers and routes to keep their operations running efficiently. While this may not be enough to cover the full cost of shipping, it could make a difference in the long run.
Shippers also need to prepare for new challenges with canceled sailings, and some ports skipped altogether. This could leave importers and exporters scrambling to find alternative routes or adjust their supply chains accordingly. Unlike last year, many ports are functioning at full capacity, but there is still a need for increased efficiency and cost-saving measures to ensure the smooth transportation of goods.
Looking Forward
It’s clear that the shipping industry is going through a challenging period, but there are still positives to take away. Freight rates have returned to pre-pandemic levels, and warehouses are operating close to full capacity. The biggest challenge right now appears to be coping with the new norm of consumer demand and figuring out how to balance cost with competitive pricing.
Regardless of the challenges, shippers should remain optimistic and continue to look for ways to adjust their operations accordingly. By leveraging existing technology, adapting strategies, and staying ahead of market trends, shippers can ensure that their supply chains remain profitable and efficient in the long run.
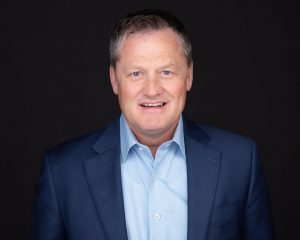
David L. Buss
*This article is written by David L. Buss. David is CEO of DB Schenker USA, a 150 year old leading global freight forwarder and 3PL provider. David Buss is responsible for all P&L aspects in the United States, which is made up of over 7,000 employees located throughout 39 forwarding locations and 55 logistics centers.