-
Subscribe to Blog:
SEARCH THE BLOG
CATEGORIES
- Aerospace
- Asset Maintenance
- Automotive
- Blog
- Building Products
- Case Studies
- Chemical Processing
- Consulting
- Food & Beverage
- Forestry Products
- Hospitals & Healthcare
- Knowledge Transfer
- Lean Manufacturing
- Life Sciences
- Logistics
- Manufacturing
- Material Utilization
- Metals
- Mining
- News
- Office Politics
- Oil & Gas
- Plastics
- Private Equity
- Process Improvement
- Project Management
- Spend Management
- Supply Chain
- Uncategorized
- Utilities
- Whitepapers
BLOG ARCHIVES
- June 2025 (4)
- May 2025 (1)
- April 2025 (1)
- March 2025 (1)
- February 2025 (4)
- January 2025 (4)
- December 2024 (4)
- November 2024 (2)
- October 2024 (6)
- September 2024 (5)
- August 2024 (5)
- July 2024 (6)
- June 2024 (3)
- May 2024 (3)
- April 2024 (4)
- March 2024 (3)
- February 2024 (4)
- January 2024 (5)
- December 2023 (2)
- November 2023 (1)
- October 2023 (6)
- September 2023 (3)
- August 2023 (4)
- July 2023 (2)
- June 2023 (3)
- May 2023 (7)
- April 2023 (3)
- March 2023 (3)
- February 2023 (5)
- January 2023 (6)
- December 2022 (2)
- November 2022 (5)
- October 2022 (5)
- September 2022 (5)
- August 2022 (6)
- July 2022 (3)
- June 2022 (4)
- May 2022 (5)
- April 2022 (3)
- March 2022 (5)
- February 2022 (4)
- January 2022 (7)
- December 2021 (3)
- November 2021 (5)
- October 2021 (3)
- September 2021 (2)
- August 2021 (6)
- July 2021 (2)
- June 2021 (10)
- May 2021 (4)
- April 2021 (5)
- March 2021 (5)
- February 2021 (3)
- January 2021 (4)
- December 2020 (3)
- November 2020 (3)
- October 2020 (3)
- September 2020 (3)
- August 2020 (4)
- July 2020 (3)
- June 2020 (5)
- May 2020 (3)
- April 2020 (3)
- March 2020 (4)
- February 2020 (4)
- January 2020 (4)
- December 2019 (3)
- November 2019 (2)
- October 2019 (4)
- September 2019 (2)
- August 2019 (4)
- July 2019 (3)
- June 2019 (4)
- May 2019 (2)
- April 2019 (4)
- March 2019 (4)
- February 2019 (5)
- January 2019 (5)
- December 2018 (2)
- November 2018 (2)
- October 2018 (5)
- September 2018 (4)
- August 2018 (3)
- July 2018 (2)
- June 2018 (4)
- May 2018 (3)
- April 2018 (3)
- March 2018 (2)
- February 2018 (2)
- January 2018 (1)
- December 2017 (1)
- November 2017 (2)
- October 2017 (2)
- September 2017 (1)
- August 2017 (2)
- July 2017 (2)
- June 2017 (1)
- April 2017 (3)
- March 2017 (3)
- February 2017 (2)
- January 2017 (2)
- December 2016 (2)
- November 2016 (4)
- October 2016 (4)
- September 2016 (3)
- August 2016 (6)
- July 2016 (4)
- June 2016 (4)
- May 2016 (1)
- April 2016 (3)
- March 2016 (4)
- February 2016 (2)
- January 2016 (4)
- December 2015 (3)
- November 2015 (3)
- October 2015 (1)
- September 2015 (1)
- August 2015 (4)
- July 2015 (6)
- June 2015 (4)
- May 2015 (7)
- April 2015 (6)
- March 2015 (6)
- February 2015 (4)
- January 2015 (3)
CONNECT WITH US
Tag Archives: building products
Like most industries today, the building products industry is faced with a host of challenges. These uncertain economic times aren’t helping matters any. Here are some of the top challenges we’ve identified, and tactics to combat them.
Challenge #1: Post-COVID demand
As the tumultuous start to the decade began to ease back into normalcy, the industry saw an increase in consumer spending and a boom for the construction and building products industries. What was behind it? Potential customers had time to sit and think. A year or more of being involuntarily secluded in their homes put their current infrastructure to the test. Who thought that kitchen countertop was a good idea? Wouldn’t it be nice to open the wall up and put in a breakfast bar? And… while we’re at it, let’s install that screened-in porch to go with it. The projects consumers had been thinking about for months were finally able to be realized and construction started up again with a vengeance.
Great! But building products manufacturers have been struggling to meet this ever-growing demand.
Strategy: Don’t turn down work — extend your lead time
Many of our clients have more work than they can handle right now. While it may seem unrealistic to take on every project in sight, it’s important to shore up your bottom line that took such a hit during the pandemic. Extending your lead time by a few weeks will allow you to accept more jobs and keep business flowing.
Challenge #2: Supply chain bottlenecks
A post-COVID boom is great for business — until you can’t get the materials you need at a price that makes sense. Supply chain disruptions have been commonplace for a few years now and that disruption is touching nearly every industry imaginable.
The pandemic showed just how vulnerable the current state of the supply chain is across the globe. From shipping and transportation delays to factory disruptions and material shortages, it has never been more important to keep a close eye on where and how you are sourcing your materials.
Strategy: Implement SIOP to keep a careful watch on your inventory
Being mindful and proactive about your inventory is the best way to make sure you have the materials you need, when you need them. We are helping many of our clients implement Sales, Inventory and Operations Planning (SIOP) to do just that.
SIOP is a process that facilitates having the right inventory conversations at the right time by integrating customer-focused demand plans with production, sourcing and inventory. Using this method, companies can get a clearer look at their operations and create better-informed strategy decisions.
Read more about SIOP in our eBook, Sales, Inventory & Operations Planning: It’s about Time.
Challenge #3: Rising Costs
We get it. This problem is everyone’s problem these days. Despite the already razor-thin profit margins in the building and construction industry, material prices continue to rise across the board. Your business isn’t operating for free, and finding ways to complete projects under budget and stay profitable is proving to be a harder challenge with each passing quarter.
Strategy: Include an escalation clause in your contracts
There are a few strategies you can employ to combat rising costs, but each has its pros and cons. Should you finance material purchases? Raise your prices? Will these strategies help your bottom line, or will it cause customers to look elsewhere?
Ultimately, the wisest strategy seems to be including an escalation clause in your contracts, stating that if prices increase by a certain percentage or more during the duration of the project, you have the right to adjust your costs accordingly. This provides the most flexibility for your business without risking losing customers to cheaper alternatives.
At USC Consulting Group, we’re here to help you through these uncertain economic times. And the good times, too! If you’d like to learn more about these common industry disruptors and our solutions, download our free eBook, “Constructing the Building Products Industry: An Outlook of Challenges and Solutions.”
It’s a double-edged sword for the building products industry today.
The production and demand slump during the pandemic has turned into a boom. Residential and commercial building is on a high.
Yet, challenges still exist for the building products industry as it navigates these uncertain economic times.
While each company has its unique issues, our team of subject matter experts have compiled the most common challenges we’re seeing for the building products industry today, and share productive solutions we’re recommending to our clients to tackle them.
Download our free eBook “Constructing the Building Products Industry: An Outlook of Challenges and Solutions” as we advise on tactics to deal with the boom and optimize your operations.
In this eBook you will learn how to overcome the following:
- Rising costs
- Supply chain bottlenecks
- Understaffing & skills gap
- Post-COVID boom
These strategies will help you get started on combating industry challenges and carry you through these uncertain economic times. If you need more in-depth help or would like to discuss specific issues you are experiencing, give us a call today. We listen first and then advise on how we can make your operations more efficient.
Challenges like growing demand for sustainable practices, rising raw material costs, and a volatile construction market have forced the building materials industry to adapt quickly over the past few years. Right now, new technology and design strategies are transforming how buildings are made.
These technologies offer significant benefits — like reduced cost, minimal waste, and improved sustainability — that building materials manufacturers need to be aware of.
1. Smart Building Materials
Smart building materials are adaptive and change their properties based on changes in environmental conditions.
Smart glass, for example, can change transparency as needed to maximize the energy efficiency of a building.
In the summer months, when building owners need to keep a home or office cooler, an automated system can turn the glass translucent or opaque. This allows the glass to absorb solar radiation and prevent sunlight from heating the building. In winter months, the windows will “open,” turning transparent and letting in as much light and heat as possible.
These changes are often coordinated by a smart building system that may also be adjusting an intelligent HVAC system, or smart light fixtures that alter light output based on time of day and room occupancy.
Other smart materials include self-healing materials, self-adjusting concrete, and transparent metals. These materials may help to create more sustainable buildings that cost less to repair, maintain, and operate.
2. Additive Manufacturing
Additive manufacturing technologies — like 3D printing — help businesses create construction materials in a way that minimizes waste. Large, specialized 3D printers can be used in factories or on-site to print structures like concrete panels for new housing units.
This process can enable businesses to significantly accelerate the construction process. While 3D printing can’t fully automate construction yet — workers are still needed to insert rebar into printed concrete structures — new materials may soon change this.
Certain thermoset composites, for example, harden into stonelike structures as they cure, and offer strength that’s similar to rebar-reinforced concrete. These materials could help to further streamline construction.
3. Laser Measures
Precision in building materials is essential. A new structure, if it’s off-spec even by a few centimeters, can mean significant waste and setbacks as workers correct the structure.
Laser measures are alternatives to measuring tape and other “analog” tools. They use lasers to provide construction workers with accurate measurements on the construction site.
These tools offer a few key advantages over conventional measuring tools. Laser measures typically provide more accurate readings than conventional materials and can also be adjusted more easily. This can reduce the amount of time it takes to capture measurements in a large area, helping businesses to scale up construction operations.
Combined with other, more advanced measurement-taking methods — like construction-site VR and AR — these measures can help make construction much more efficient.
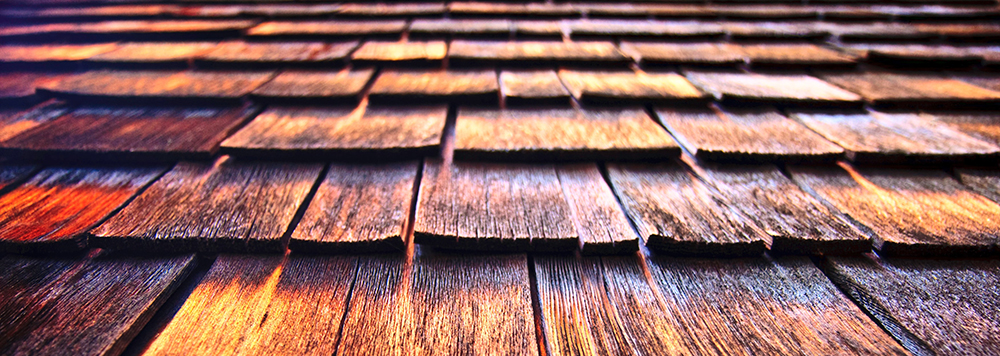
Composite roofing shingles are an example of building materials manufacturers technologies.
4. Sustainable Materials
The rising demand for sustainable materials has had a major impact on the building materials market. Materials like bamboo, composite roofing shingles, and reclaimed wood have emerged in the past few years as three options for businesses wanting to provide sustainable materials options to customers.
These materials typically have a much lower carbon footprint than comparable materials, like concrete, asphalt, or brick. Composite shingles, for example, are made from a combination of materials, often slate, laminate, and wood. They provide shingles with an appearance similar to ceramic or asphalt shingles, but that are lightweight and have a low carbon cost.
In some cases, they may also help a construction company drive down costs and reduce waste. Reclaimed wood, for example, enables construction companies to find a new life for wood that would have otherwise gone to a landfill.
The unique appearance of reclaimed wood has also made the material popular with some consumers — meaning that offering the material could enable building materials businesses to thrive in certain niche markets.
How New Technology Is Changing the Building Materials Market
These innovations are helping building materials manufacturers adapt to a changing construction market. Additive manufacturing techniques and measurement tools like laser measures are transforming how construction companies approach their work.
At the same time, the growing popularity of sustainable materials, like smart glass and composite shingles, is making it easier for providers to offer sustainable material options to their customers.
*This article is written by Devin Partida. Devin is a tech writer with an interest in the IIoT and manufacturing. She is also the Editor-in-Chief of ReHack.com.
COVID-19 has been a take-no-prisoners virus. In mere months, thousands of businesses have folded in a variety of industries or are on the verge of closing. Some sectors have proven to be more resilient than others though. For instance, while a number of economists anticipated real estate would likely be hard-hit, the combination of solid economic fundamentals as well as record-low interest rates have kept the industry humming. Indeed, the Pending Home Sales Index reached nearly 9% in August and the existing-home sales topped a seasonally adjusted annual rate of 6 million during the same period, according to the latest estimates from the National Association of Realtors. Engaged buyers and highly limited inventory have kept builders hard at work nationwide.
Despite the residential housing sector’s strength, 2020 will likely be remembered as a down year for developers.
When 2020 officially concludes, the construction industry in the U.S. is anticipated to be 6.5% smaller than it was when the year began. That’s according to a recent report from ResearchandMarkets.com. If conditions continue at their present pace, the sector is poised to contract an additional 2% come 2021.
Coronavirus disruption in construction
The coronavirus is largely responsible. With over 7 million Americans infected by the strain and a variety of social distancing measures installed by states as well as employers, numerous projects that were slated to take place have been delayed, rescheduled, or started but with far fewer workers than initially anticipated. In some instances, this has been due to laborers who were sick; in others, developers were limited to having only so many people on job sites at once.
“In September, wood used for framing reached $950 per thousand board feet.”
Complicating matters further is the price of home-building materials, especially lumber. Forestry and logging companies have encountered their own struggles with the exploration and extraction of trees due to COVID. This, in turn, has led to higher purchase prices for developers. For example, in September, wood used for framing reached $950 per thousand board feet, according to the National Association of Builders. Tracing back to April, lumber prices in the U.S. are up 120%, on average. As a result of this, the cost of buying for would-be homeowners has risen roughly $16,000, NAHB estimates, stretching the finances of many budget-minded families too thinly.
What can building product manufacturers do to bounce back in 2021? Here are a few suggestions:
Embrace the new business as usual
Perhaps the biggest frustration of the COVID-19 crisis is the uncertainty of it all, as no one seems to know when advanced safety measures to slow the spread will end. While most parts of the country now allow laborers to be on the job — whereas before they were off-limits — roughly three-quarters of building product manufacturers believe COVID-19 restrictions will continue for another year, according to polling done by Construction Dive. More specifically, 88% expect social distancing and personal protective gear will be the norm for the long term.
As a result of this, businesses should try to acclimate themselves to the reality of having fewer hands. Whether it’s done by leveraging automation technology to tackle repeatable processes, or streamlining production through smarter asset utilization, building product manufacturers will need to ramp up their process efficiencies so workers can execute more effectively.
Prepare and source even further in advance
In addition to lumber being more expensive to purchase, it’s also harder to come by. As Newsweek reported earlier this summer, COVID-19 restrictions forced numerous lumber mills across the U.S. to cut back on their production, both for softwood lumber and treated lumber.
When the time comes to obtain material for a scheduled project, manufacturers may want to stock up. This is something that Jeffrey Luter of Fulcrum Associates has done and plans on continuing. Speaking to New Hampshire Business Review, Luter noted his company has extended its purchasing window rather considerably.
“Items that we would source three to four weeks before they are needed on the job site are being ordered 10-12 weeks in advance,” Luter explained.
Adopting a more forward-looking strategy can enable building product manufacturers to better prepare for fluctuations in the supply chain, which are forecast to continue in 2021.
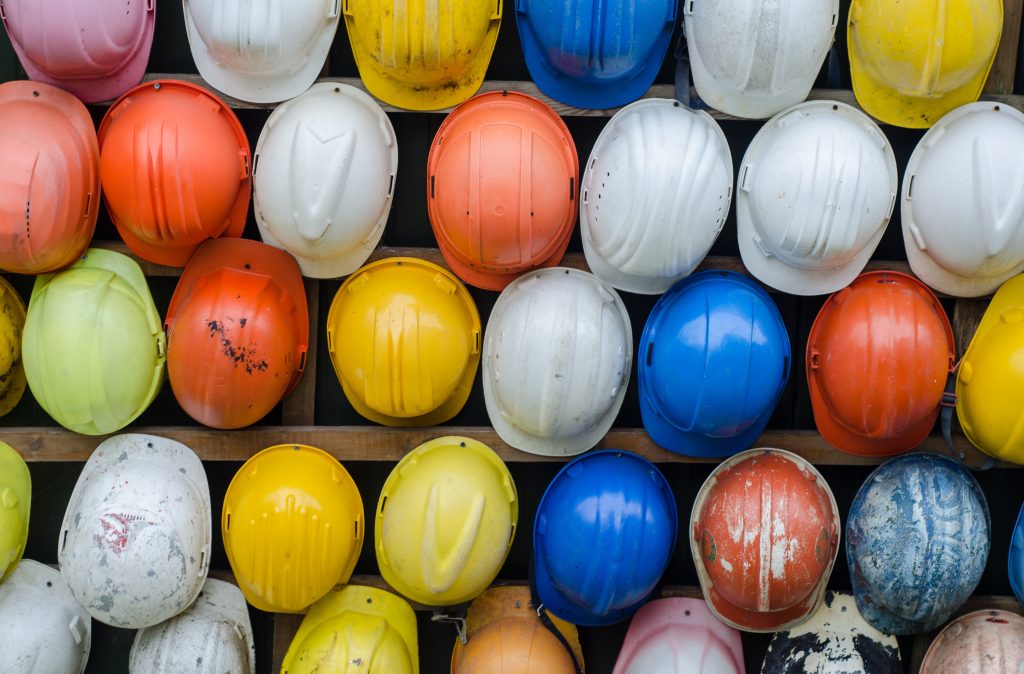
Building product manufacturers look to keep employees safe and well.
Keep crew safe and well
With many building product manufacturers operating with skeleton crews, the ongoing productivity of each individual becomes that much more important. However, with construction routinely being among the top industries for on-the-job industries, developers must prioritize the protection of all involved. This includes keeping laborers protected from infection. Tom Sullivan of Sullivan Construction told NHBR this has been an ongoing process throughout the pandemic.
“We take the temperature every day of everybody who comes on-site,” Sullivan said. “We apply social distancing to our projects. We have a mask requirement for all people on our job sites — including people from our group and myself. We want to make sure nobody gets sick. Our objective is to keep everybody healthy and use the latest and greatest protocols out there to protect everyone.”
Prioritize supply chain management
In addition to fully operational work crews, builders also require the materials to build. But as previously noted, key materials and equipment to development are either in short supply, virtually impossible to find or expensive to purchase. As a result, building products manufacturers should aim to optimize their supply chains as proactively as they can. This includes diversifying where they get their materials from so firms have more options and places to go when suppliers are out of stock. Strategic sourcing can help in this regard.
Building product manufacturers may also want to perform their own research to see where it’s possible to use one material in place of another. Former NAHB Chairman Randy Noel said certain alternative materials — such as steel — may serve as a sufficient option as a substitute for lumber. As the Steel Market Development Institute points out, steel may prove more cost-effective than wood framing because it won’t warp, split, crack or rot like wood does.
From strategic sourcing to efficiency improvements or cycle time reduction, USC Consulting Group has the solutions that can help your business find it’s footing in the building products landscape — in more ways than one. Contact us today to learn how we can help you be more efficient in your operations.
From the ground up, USC Consulting Group helps building material manufacturers solve their sourcing problems, fine-tune their operations and improve their bottom lines.
It all begins with a blueprint for success, developed and perfected by our experts and your in-house teams.
By starting with an optimization strategy, we set a strong foundation on which you can build a better-performing business.
We examine opportunities along the supply chain, from sourcing to scheduling, that can put you on sturdier footing.
We also use our knowledge of the industry to open processes in order to achieve greater throughput, yield, and OEE.
Our operational management specialists pay attention to every detail, no matter how small, and our clients take comfort knowing that we will implement the right strategies for continued improvement.
Every manufacturer is a special part of the whole to the Building Materials industry and we have worked with each to help reduce costs and improve productivity.
List of Building Materials Industry Manufacturers:
- Cement
- Flooring
- Fixtures
- HVAC
- Windows and doors
- Furniture
- Plumbing and pipes
- Electrical
- Drywall
- Bricks and siding
- Roofing and shingles
Want to put 50-plus years of consulting experience to work for you? Contact USC Consulting Group today.
In the blog Every Part Has a Purpose: Building Materials Manufacturing, we learned about a few of the challenges that the American housing market and its producers will be facing here in 2019. The number of wildfires occurring annually is increasing at alarming rates and the building materials manufacturers are feeling the repercussions from these natural disasters. The softwood and hardwood resources being burned down are causing the lumber suppliers to struggle to meet the demands of the home construction market. Furthermore, the housing market being on fire lately (pun intended) has led to intense bidding wars among buyers while developers work hard to increase inventories. To top it all off, material costs have increased significantly due to the global trade showdown linked to the recently introduced tariffs.
Backbone of the American housing market
Building materials manufacturers are poised to overcome the various obstacles thrown their way and accelerate operations in this demanding economy. Thus, continuing to power the U.S. housing market. But, just how pivotal are these building materials producers to the consumers who are scouring Zillow and Realtor.com in search of their dream home?
Here at USC, we love to analyze data and processes as much as Joey Tribbiani loves to eat sandwiches. So, we took a deeper dive into just how important these building materials manufacturers truly are to the industry. We put our results into a cool infographic for easy digestion. You will see that every part, or every manufacturer, has a significant purpose in powering the whole.
“More than a million houses are built monthly in the U.S.” That stat in itself is incredible. What’s even more mind-blowing is when you start considering “how” this is all made possible and realize how crucial building materials manufacturers really are to the industry.
Providing more power
It is essential that these behind-the-scenes producers improve their processes to keep pace with the housing market demands. However, with such a strain to keep up, building materials manufacturers may not have time to analyze and optimize their operations and could use some extra horsepower. USC Consulting Group is here to help. By working with your shop-floor personnel and leadership teams, we not only help to achieve greater throughput and yield, but can also enhance your supply chain management to improve in areas such as strategic sourcing, maintenance practices, and logistics.
Contact us today to discuss how together we can help you sustain as well as thrive in the current opportunistic landscape.
Lighting fixture producers the world over have much to look forward to. Predictions from Transparency Market Research indicate a near 7 percent compound annual growth rate through 2021, when global revenues will reach an estimated $215.29 billion.
However, the same cannot be said for bulb manufacturers, who came out of the Great Recession hurting and continue to see sharp declines. Although IBISWorld economists estimate a slight leveling through 2021 when compared to 2011-2016 figures, where bulb makers saw an 8.7 annualized contraction, it doesn’t take a business analyst to understand the direction of this industry is declining. And the truth is, this dip could eventually impact the fixture market in many ways.
What drivers have turned the dimmer switch down on the lighting industry? Could lean manufacturing practices help businesses operating in this sector find their way in the coming economic darkness?
1. Energy efficiency: ‘Sustainable’ for whom?
Be it for financial or ecological reasons, everyone from homeowners to business owners have begun switching to solid-state lighting like LEDs and OLEDs. According to the U.S. Department of Energy, SSL technology today could potentially reduce lighting electricity consumption by 75 percent, a big deal for those with burdensome energy bills, but not ideal for the lighting industry.
Apart from their electrical efficiency, SSL bulbs also last longer than conventional filament bulbs by a long shot. LEDs, for instance, outlast incandescents 25 times over, so says the DOE. Lighting has, in essence, innovated itself out of a lucrative consumer cycle. People may pay considerably more for a single light bulb than they did a decade ago, but not 25 times more. Lean practices like quality assurance inspections and process standardization will be a boon to these industries as they attempt to reclaim their former glory with a more reliable, simpler-made product.
2. Obsolescence new engine for lighting consumers
As creators of SSL products continue to integrate smarter, interoperable technology into their goods, a dead bulb will no longer drive consumers to buy – technological advancement will. That goes for fixtures, too.
Steve Arriola, director of operations at Hubbell Lighting in Greenville, S.C., showed Architectural Lighting Magazine luminaire manufacturing and assembly have taken on the appearance of any other electronics plant. This major shift impacts everything from equipment on the lines to the training required to work on the floor, not to mention the accelerated integration rate of embedded components required to meet customer demands.
Therefore, leaning out operations today while the industry rests on the cusp of a revolution will allow lighting manufacturers to hire and retain top talent, train workers on new technology, and capitalize on innovation rather than succumb to it. Furthermore, lighting manufacturers pushing to vertically integrate will need to rein in waste and optimize processes as much as possible to achieve the kinds of production cost savings and lead time cuts necessary to claim pole position in their market.
3. Trending now: Over-sized lighting fixtures
Large, modern chandeliers and pendant fixtures have come into favor with both residential and commercial lighting investors. So, as luminaire producers combine the traditional elegance of colossal installations with connected, data-driven mechanisms for a new age of consumers, they are met with attractive value propositions.
Yet as with all products that can be sold at a higher price point, manufacturers will need to back up their cost increases with value adds for the buyer – greater quality assurance, maintenance packages, responsibly sourced materials, etc. – any of which could tip a business into the red if lean manufacturing practices aren’t already in place and functioning smoothly.
Who knows what tomorrow might bring for the lighting industry. Uncertainty is the only certainty. Adopting a culture of lean manufacturing, however, ensures these businesses will stay responsive to changing customer expectations and technological integration.