-
Subscribe to Blog:
SEARCH THE BLOG
CATEGORIES
- Aerospace
- Asset Maintenance
- Automotive
- Blog
- Building Products
- Case Studies
- Chemical Processing
- Consulting
- Food & Beverage
- Forestry Products
- Hospitals & Healthcare
- Knowledge Transfer
- Lean Manufacturing
- Life Sciences
- Logistics
- Manufacturing
- Material Utilization
- Metals
- Mining
- News
- Office Politics
- Oil & Gas
- Plastics
- Private Equity
- Process Improvement
- Project Management
- Spend Management
- Supply Chain
- Uncategorized
- Utilities
- Whitepapers
BLOG ARCHIVES
- July 2025 (1)
- June 2025 (4)
- May 2025 (1)
- April 2025 (1)
- March 2025 (1)
- February 2025 (4)
- January 2025 (4)
- December 2024 (4)
- November 2024 (2)
- October 2024 (6)
- September 2024 (5)
- August 2024 (5)
- July 2024 (6)
- June 2024 (3)
- May 2024 (3)
- April 2024 (4)
- March 2024 (3)
- February 2024 (4)
- January 2024 (5)
- December 2023 (2)
- November 2023 (1)
- October 2023 (6)
- September 2023 (3)
- August 2023 (4)
- July 2023 (2)
- June 2023 (3)
- May 2023 (7)
- April 2023 (3)
- March 2023 (3)
- February 2023 (5)
- January 2023 (6)
- December 2022 (2)
- November 2022 (5)
- October 2022 (5)
- September 2022 (5)
- August 2022 (6)
- July 2022 (3)
- June 2022 (4)
- May 2022 (5)
- April 2022 (3)
- March 2022 (5)
- February 2022 (4)
- January 2022 (7)
- December 2021 (3)
- November 2021 (5)
- October 2021 (3)
- September 2021 (2)
- August 2021 (6)
- July 2021 (2)
- June 2021 (10)
- May 2021 (4)
- April 2021 (5)
- March 2021 (5)
- February 2021 (3)
- January 2021 (4)
- December 2020 (3)
- November 2020 (3)
- October 2020 (3)
- September 2020 (3)
- August 2020 (4)
- July 2020 (3)
- June 2020 (5)
- May 2020 (3)
- April 2020 (3)
- March 2020 (4)
- February 2020 (4)
- January 2020 (4)
- December 2019 (3)
- November 2019 (2)
- October 2019 (4)
- September 2019 (2)
- August 2019 (4)
- July 2019 (3)
- June 2019 (4)
- May 2019 (2)
- April 2019 (4)
- March 2019 (4)
- February 2019 (5)
- January 2019 (5)
- December 2018 (2)
- November 2018 (2)
- October 2018 (5)
- September 2018 (4)
- August 2018 (3)
- July 2018 (2)
- June 2018 (4)
- May 2018 (3)
- April 2018 (3)
- March 2018 (2)
- February 2018 (2)
- January 2018 (1)
- December 2017 (1)
- November 2017 (2)
- October 2017 (2)
- September 2017 (1)
- August 2017 (2)
- July 2017 (2)
- June 2017 (1)
- April 2017 (3)
- March 2017 (3)
- February 2017 (2)
- January 2017 (2)
- December 2016 (2)
- November 2016 (4)
- October 2016 (4)
- September 2016 (3)
- August 2016 (6)
- July 2016 (4)
- June 2016 (4)
- May 2016 (1)
- April 2016 (3)
- March 2016 (4)
- February 2016 (2)
- January 2016 (4)
- December 2015 (3)
- November 2015 (3)
- October 2015 (1)
- September 2015 (1)
- August 2015 (4)
- July 2015 (6)
- June 2015 (4)
- May 2015 (7)
- April 2015 (6)
- March 2015 (6)
- February 2015 (4)
- January 2015 (3)
CONNECT WITH US
Tag Archives: Turnarounds
Are you performing preventive maintenance on a regular basis? If you’re not, you may want to consider adding it to your schedule. Why? In a word, it’s about efficiency. In a few words (as its name suggests), it prevents problems before they start. Preventive maintenance is becoming the manufacturing industry standard. Roughly 80% of asset and facilities stakeholders are embracing the process as a way to cut costs, increase efficiency, and keep assets running like clockwork.
By performing regular preventive maintenance (or its cousin, data-based predictive maintenance) you are heading off problems, snafus and breakdowns at the pass. It’s about identifying and handling any potential issues that may be lurking down the road. The point is to find potential problems before they become real problems that could lead to delays and costly headaches.
The irony of preventive maintenance is that it can sometimes seem like it causes more problems than it solves. It requires regular downtime, which in itself is a problem. There’s also the tricky matter of timing. Finding the optimal time to perform the maintenance can be a delicate balance between shutting down for maintenance too soon and waiting too long.
But, the challenges are worth the rewards. Ensuring you have the proverbial well-oiled machine will make your operation more efficient and productive now and in the future.
Let’s take a look at preventive maintenance benefits and challenges and how it can help boost your operations.
Preventive maintenance benefits
The idea behind doing regular maintenance on the lifeblood of your manufacturing operations — your machinery — is to keep it humming along at optimal efficiency and prevent any problems that might occur. Benefits to making it a regular part of your business process include:
You control the downtime schedule. It’s true that performing maintenance requires downtime. You’ll experience a work stoppage because of it. However, the good news is, when that downtime happens is up to you. You can schedule it for slow periods and avoid your high-volume times. Build maintenance into your schedule as a regular part of your routine.
Fewer surprises. A snafu happens, something breaks, and you have to stop production to figure out what it is and fix it. That can happen at any time, and trust us, it will happen when you least want it to. Performing preventive, not reactive, maintenance will lessen those unwelcomed surprises that erode your productivity and profitability. A general rule is that planned work will cost two-thirds less than unplanned work in time and other resources.
Increased efficiency. At USC Consulting Group, we’re all about efficiency, and one of the surest ways to find “hidden efficiencies” that you didn’t even know were possible is to perform regular preventive maintenance on your machines.
Increased longevity of your machinery and assets. This is key. Just like your car needs regular oil changes and tune-ups to keep it running at its best, so do your assets.
Preventive maintenance challenges
There are some challenges with doing regular preventive maintenance. However, in our view, these don’t outweigh the benefits.
Finding the optimal time to do it is tricky. A regular schedule is the key to finding the best time to shut down for maintenance. And the downtime is typically where we see the most pushback from executives and managers who aren’t thrilled with this process.
It will cause shutdowns. There’s no way around it. To perform maintenance on your equipment, the line must stop.
If it ain’t broke, don’t fix it. This is an old adage for a reason. You may be shutting down for your scheduled maintenance when no problems actually exist. The shutdown does come at a productivity cost, so… is it worth it? Some manufacturers solve this issue by performing predictive maintenance instead. It’s a more complex process that is data driven, and analyzes how your assets are performing in real time. All’s well? No shutdown. But if you find problems, that’s when you act. It reduces downtime, and you’re not replacing any parts while they’re still good to go. The downside of this approach is complexity and connectivity. If you don’t have state-of-the-art machinery, you won’t get the data analytics that this process requires. That’s why the majority of manufacturers today are using the preventive approach.
At USC Consulting, we’ve been helping manufacturing businesses increase their efficiency, production, throughput and profits for more than half a century. Get in touch today if you’d like to learn more about how preventive maintenance benefits can boost your bottom line.
As a typical rule of thumb in maintenance, planned work will consume roughly one third of the resources (labor cost, materials cost, and costs associated with equipment down-time) as unplanned work will consume. Therefore, the first objective of any maintenance program can be simplified as maximizing the percentage of time and resources spent on planned maintenance, and reducing the amount of unplanned maintenance or repair work resulting from unexpected breakdowns.
Understanding the Types of Work
Planned work can be broken down into two main categories: preventative maintenance and planned repairs. Preventative maintenance includes all the work done not in response to a failure, but to prevent future failures from occurring. This work is typically outlined by the manufacturer in terms of frequency and work that must be performed (oil change, lube, and filter). If the fleet size remains constant, so will the level of preventative maintenance. Planned repairs are work that must be done as a result of wear and tear in which the equipment has not yet failed and can still run reliably until the maintenance department is set up with the required materials, labor, and shop space to adequately address these repairs. For exemplary purposes in this article, we will consider maintenance needed for an underground mine as a model. Due to the travel time in underground mining and the requirement in most cases to have repairs done in the shop after a wash, these two types of planned work are best done together to minimize the mechanic’s trips to and from the equipment.
Given that the level of preventative maintenance will remain considerably flat, as both the materials required and time required can be predicted and cyclical, the only way to effectively increase planned work as a proportion of total work is to increase the level of planned repairs. The first task is to shift the balance of planned maintenance and unplanned maintenance. That is, to convert as much of the resources spent on unplanned work as possible into resources spent on planned work.
Converting Unplanned Work into Planned Maintenance
The first step is to create a backlog, a master list of all known repairs that must be made to each piece of equipment. It consists of repairs necessary to components that are in a partial state of failure, but have not yet failed. The size of a backlog and how well it is managed will provide some valuable insight as to the over-all health of your assets. A complete detailed backlog will also provide other benefits to management when taking a closer look at each type of equipment and analyzing which components require more attention than others. If repairs to equipment must be done before the equipment actually fails, the ability to identify or predict failures before they actually occur will be crucial. Coordination can then be made for the replacement of these components before failure occurs. This can be a very difficult and daunting task when considering a large fleet with complex equipment.
The first element to be considered when creating and managing a backlog is where the backlog work will be sourced from. Where will the maintenance planners get the information to create backlog list? Each time the equipment is inspected, an opportunity is provided to gather backlog. In an underground mining environment, some of these touch points include the preventative maintenance services, planned repairs, and operator circle checks.
An additional inspection can be strategically added to generate a greater and more detailed amount of backlog. Figure 1 below depicts the impact on parts procurement time of an inspection conducted by a mechanic in a predetermined time frame before the equipment is scheduled to come into the shop for a preventative maintenance service.
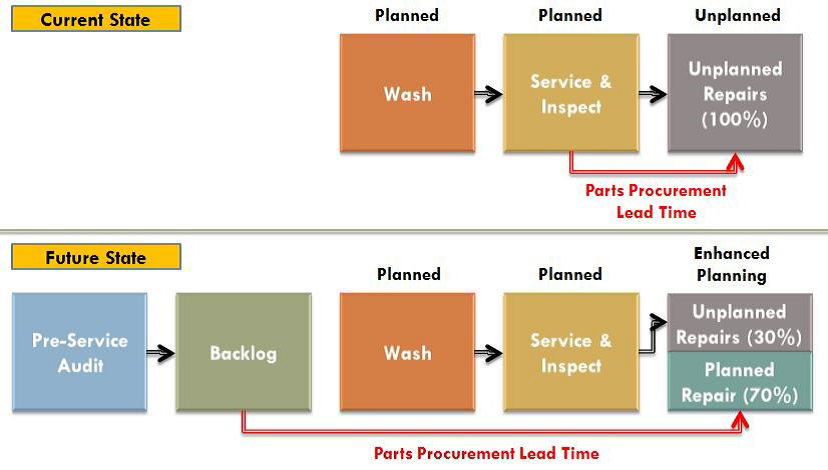
Figure 1—Current State vs. Future State with Backlog
Once the backlog list has been developed, the repairs can then be strategically scheduled alongside the preventative maintenance services while the equipment is already in the shop with shop space and labor assigned to it. Additionally, once these repairs have been scheduled, parts and materials can be ordered, packaged, and delivered to the shop where the repairs will be completed.
The supply benefits of planning repairs before failure are amplified in underground mining as the remote locations can be difficult for suppliers to deliver to. Even once on site, the materials must go through a complex supply delivery system to make their way underground. Planning these repairs ahead of time allows the equipment to run for the duration of this prolonged lead time. If the equipment is run until failure, it will remain down for the entire duration of this lead time until the needed parts can be delivered.
In generating and completing the backlog list against each piece of equipment, failures and breakdowns that would normally occur can now be discovered before failure and repaired on average much quicker than if the equipment would have broken down. The backlog system is working towards converting unplanned maintenance work into planned maintenance work, and therefore consuming one third of the resources on each repair converted as would normally be expended.
Planned maintenance leads to significant cost savings with improved productivity. For 50 plus years USC Consulting Group has helped organizations develop planned maintenance programs to increase their uptime. Contact us today to start converting your maintenance practices and keep your operations running as much as possible.
Learn more about project management best practices.
Every organization with major assets has different initiatives or projects it wants to pursue such as shutdowns, turnarounds, outages or other large scale capital projects. However, managing all the details that go into those efforts — from team coordination to stakeholder communication — requires a dedicated strategy. Furthermore, avoiding schedule overrun and staying within or under budget is critical. That’s where project management comes in, which helps leaders better monitor, control and execute projects by emphasizing:
- An established scope of work and delivery schedule.
- Different methodologies for different projects.
- Progress tracking and win sharing.
Want to learn more? Download our eBook “Getting Down to Business: The Essentials of Project Management.”
Planning an upcoming project? Contact us today to speak with our subject matter experts about your initiative.
The project management office (PMO) is a common organizational feature among modern businesses. Eighty-five percent of enterprises have PMOs, according to researchers for the project management software provider PM Solutions. Of those companies that do not have PMOs, 30 percent plan to establish them over the next year.
Organized and well-resourced PMOs can drastically improve operations, allowing companies to execute improvement strategies that are on time and under budget. However, few PMOs perform at this level. A mere 25 percent of PMOs facilitate improvements to productivity, and only one-third consistently deliver under budget. Why? Because many PMOs suffer from functional and structural issues that hinder their performance.
For a deeper look at a Project Management Office and its structure, check out ProjectManager.com as they provide an extensive guide to PMOs.
Now, let’s look at a few common PMO issues and how to address them:
Lack of operational identity
Businesses often form Project Management Offices for one of two reasons:
- Executive leaders have requested the formation of a permanent PM team.
- An operational issue warrants an internal team of problem-solvers.
In either scenario, the resulting PMO can encounter roadblocks as they try to find a clear identity, the Project Management Institute reported. PMOs created at the behest of business leaders often struggle to pinpoint their purpose. At the same time, PMOs established to address one-off problems tend to be slightly more productive, as they at least come into existence with a clear objective in mind. But once they tackle the objective they were created to achieve, finding new purpose can be difficult.
PMOs can avoid this issue by crafting an organizational identity upon formation. For instance, some PMOs use responsive processes and specialize in solving reported problems. Others take a more proactive approach by staffing multiple project managers and technical executors who can actively pinpoint and iron out problem areas. PMOs that work to cultivate actionable identities are more likely to find sustainable success than those that function with seemingly little direction. But organizations should refrain from building PMOs with overly rigid missions. Agility is essential in today’s operational climate, and a PMO that can adapt is far more likely to face new challenges confidently and correctly.
Ineffective performance metrics
In order to achieve success, PMOs must know what excellent performance on the shop floor actually looks like. Metrics are, of course, responsible for painting a full picture.
Unfortunately, few seem to work off such measurements. Analysts for PM Solutions found that more than 40 percent of PMOs struggle to demonstrate their value, which speaks the weakness of their reporting structures. The absence of ironclad performance data can lead to resourcing issues and distrust among executive and operations leaders. This makes it more difficult for PMOs to execute, even without the context data provides.
The root of this problem lies in the actual mechanics of tracking performance. Many PMOs rely on manual reporting practices powered by unwieldy spreadsheets. This variable alone makes it difficult for these offices to collect and analyze actionable data, leaving many to give up on such efforts entirely. Enterprises can overcome this issue by outfitting their PMOs with back-end solutions capable of gathering real-time performance insights that map to specific internal initiatives.
Fear of failure
PMOs pursue long-term performance excellence. As a result, project managers are always searching for projects and cultivating processes meant to maximize the likelihood of success and, ultimately, revenue. But this desire to demonstrate value can actually cause dysfunction within PMOs. PM departments that constantly look for wins may avoid innovative methodologies that could lay the groundwork for operational transformation in favor of more traditional, battle-tested solutions.
Today, according to PMI, 15 percent of the programs managed through PMOs result in failure. This figure indicates that many PMOs put timeliness and budget above overarching business performance by submitting unambitious project plans. Sure, they’re likely to be executed on time and under budget but will have little impact on the operation when all is said and done. PMOs must be empowered to break free from convention and pursue innovative methods for improving their businesses.
In the end, enterprises that overcome these challenges can expect to create powerful PMOs that lead internal initiatives, realize goals, and catalyze real change.
Here at USC Consulting Group, we’ve been working with our partners across various industries for five decades, lending them operational insights that bolster shop-floor functionality and facilitate financial success. Does your PMO lack direction, struggle with its key performance indicators, or feel trapped in a vicious cycle of boilerplate solutions to complex and unique problems? Connect with us today to learn more about our work and how we can help your PMO reach its full potential.
USC Consulting Group, a global operations management consulting firm, achieves 50 years of empowering performance. But, what exactly does that mean? View our latest infographic to find out…
(click to enlarge)
To learn more about our entire service offerings visit our website www.usccg.com and be sure to follow us on LinkedIn and Twitter.
Like what you see? Subscribe to our blog to receive the latest insights from our subject matter experts.
The Trump administration recently published its 2019 budget proposal, which includes deep spending cuts totaling hundreds of billions of dollars. The budget request also calls for the elimination of several federal oversight bodies, including the U.S. Chemical Safety Board, according to Bloomberg. Created in 1990 as part of the Clean Air Act, the independent watchdog leverages $11 million in annual funding to investigate industrial incidents stemming from the mismanagement of caustic chemicals. While the elimination of the CSB seems, on the surface, an ideal development for industrial organizations, some industry leaders and workplace safety experts have expressed skepticism.
Modern manufacturers are deeply invested in protecting their employees, and support the work of bodies such as the CSB as they establish new workplace safety paradigms centered on innovative strategies and technology. Current CSB Chairperson Vanessa Allen Sutherland has received praise from industry leaders for streamlining the agency’s investigation workflows and collaborating more effectively with businesses. Despite these positive developments, however, the agency has been put on the chopping block as part of a wider push for government deregulation.
How would the abolition of the CSB impact firms developing new safety and reliability programs?
Addressing chemicals in the workplace
Chemical compounds are among the most serious safety hazards found within industrial work environments, according to the National Safety Council. Manufacturers and other businesses leverage hundreds of different substances in everyday workflows and produce significant amounts of equally dangerous chemical residue. Workers who encounter these materials can suffer serious or sometimes fatal injuries. In fact, approximately 268 American employees died in 2016 because of such exposure events, according to research from the Occupational Safety and Health Administration. Firms in the industrial space are well aware of the dangers that their workers face, which drives them to develop safety and reliability programs that prevent injuries.
Oversight bodies like OSHA and the CSB are heavily involved in these efforts, working with industry stakeholders to create enforceable policies that keep employees safe, even as they encounter risk while performing everyday duties. In 2016, the CSB conducted seven major investigations, including an inquiry into the 2013 explosion at the West Fertilizer Company plant in West, Texas, that killed 15 workers and injured more than 260 others. Through these investigations, the CSB developed best practice recommendations so industrial businesses do not repeat the errors of their less fortunate peers. OSHA adds another dimension by approaching the subject of chemical management from the position of the worker and formulating safety standards that keep employees safe. While businesses in the industrial space have traditionally butted heads with OSHA, they have had a productive relationship with the CSB, which many leaders credit for revolutionizing chemical handling practices here and abroad. Its investigations have resulted in the creation of new guidelines that not only keep workers safe but also reduce costs associated with employee injury.
Considering operations after CSB
If Congress embraces the Trump administration’s budget and authorizes the elimination of the CSB, then industrial organizations would have to seek out new external partners and refocus their efforts in order to ensure vigilance in an environment with little federal oversight. The critical insight the agency once provided would be gone, increasing the likelihood of catastrophic events caused by small operational lapses. The West fertilizer plant resulted in more than $230 million in damages to the local community. Without the CSB, another similar situation may develop.
USC Consulting Group can help chemical manufacturers with operating efficiency by developing effective safety and reliability programs for addressing chemical usage in the workplace. Furthermore, our consultants can establish asset performance management programs to ensure facilities are properly maintained with scheduled maintenance and well-planned outages, resulting in their employees staying safe from avoidable mishaps.
Is your organization considering how it might operate in a world without the U.S. Chemical Safety Board? Connect with USC Consulting Group today to learn more on how to improve safety in the workplace.
Truly innovative asset management covers all aspects of monitoring, analyzing, and maintaining capital equipment. Does your business have all its bases covered?
Now recovering from economic instability over the last decade, companies in asset-intensive industries have begun to invest in new and recommissioned equipment. In turn, these decisions ignite a fervent interest in improving uptime quality through optimized workflows, reliability-centered maintenance, and proactive decision-making.
Download our latest e-book “Asset Management: The Rise of Reliability” to discover asset management best practices from our team of experienced operational experts. Here are the seven points examined and discussed therein.
1. Work management
A work order is more than just a slip of paper. Its life cycle extends further than most businesses realize and should include information valuable to future successes in asset management.
2. Downtime tracking
If you fail to understand the nuance of downtime tracking, you will fail to sustainably decrease it.
3. Preventive and predictive maintenance
Reward awaits those facilities that understand what these two cutting-edge maintenance methodologies entail and how to execute on them properly to achieve new heights.
4. Asset criticality review
Are you allocating your resources to the machinery that matters most to your business? Align your goals with your actual asset management processes with a comprehensive ACR.
5. Equipment history capture and analysis
Those who ignore history are doomed to repeat it. Do you know what sorts of data you should capture about your assets today in order to make informed decisions tomorrow?
6. Root cause failure analysis
Assets fail for any number of reasons, but they boil down to three basic types of failure. Learn these as well as tips for digging below the surface when failures strike.
7. Operator equipment care
Line operators can work wonders for an innovative asset management program – if only their leaders know how best to utilize them.
Process mapping allows businesses to chart out steps in a given system to understand them more fully. Virtually every process in any industry can and should be mapped, in order to conceptualize exactly where bottlenecks may exist, wasteful actions occur and, where emergency detours might be necessary to preserve production or service uptime.
As any cartographer will tell you, there are right and wrong ways to construct maps. While process mapping might not have been what map-makers like the ancient explorers had in mind, similar rules apply. We’ve collected a few best practices for creating valuable process maps that deliver results and hone operations.
“Process mapping works best with concrete tasks.”
1. Tangible processes map best
Almost any process materializes well onto a process map. It is, however, worth noting the small category of those that don’t: highly abstract processes. Process mapping works best with concrete tasks that include appreciable and quantifiable objectives.
If process map-makers find it keeps failing to address all the concerns that led them to begin the project in the first place, that may be a sign the prospective map ought to be broken down into smaller chunks, a set of process maps within a greater process map. The road to the top of the mountain is beaten by many footsteps, so don’t attempt to leap there in a single bound.
2. Know where you’ve been and where you’re going
Since it is a tool commonly attributed to an agenda of continuous improvement, process mapping exists within a time continuum. Perhaps an organization has used process mapping since its inception, or maybe it’s part of a new operational excellence initiative. In either case, the use of this resource represents a single moment in an organization’s unending commitment to changing for the better. As such, process mapping should exploit the context of time any way it can.
“Treating process maps like historical documents can provide valuable insight.”
Process mapping can provide valuable insight as to how a company’s performance has improved or declined – a great metric for change management – as well as what sorts of process maps might be worthwhile in the future. Concise documentation is always needed to flesh out the story around the map: the reasons for updating, iterations of experimentation with process changes or shifts, or whether the team reached its goals at that time in history.
These notes will be informed by legacy and, in turn, inform future mappers. After all, process changes may pave the way for whole new avenues of possibility. Most of all, meticulousness ensures no step in the process goes unheeded and operations have the highest potential to succeed.
3. Strive for simplicity
All that said, these notes should be supplementary to process mapping and not exist on the map itself. Process maps should clearly and succinctly outline a system in the order it should be performed, with careful attention paid to visual simplicity. Save the extra documentation for planning meetings, but leave it off the map itself to prevent confusion or worse: non-use.
4. Try cross-functional mapping – but only when you’re ready
While all process maps are subject to time, only some are subject to a single department. In many instances, process mapping is most beneficial when it goes beyond a single silo. However, cross-functional process mapping adds a new dimension of complexity, as different departments may be subject to requirements, regulations, customs and, other kinds of checks and balances.
Gain some experience with a few simpler processes before tackling organization-wide process mapping challenges. Cross-functional maps can bring about significant improvements, but only if they’re established and implemented with speed and accuracy honed through experience.
“Every step from beginning to end should result in some tangible value.”
5. Distinguish value at every turn
Process mapping is very much a value-based activity. Every step from beginning to end should result in some tangible value for the organization and/or its customers, even if the benefit is simply a more optimized system. But to accomplish this, the map-maker must examine what value means for their organizations – and their organizations alone – as it pertains to each component of their process maps as well as the “big picture” objective.
Say a manufacturer wants to create a process map for an equipment changeover that includes a recently established standardized method operators have been asked to perform. Although the overarching reason for standardization might be to improve lead times, each step within the process map should demonstrate a quantifiable time management improvement over past operations:
Has the location of the equipment components necessary for changeover moved so they’re physically closer to the operator? Does the asset need to be equipped with different resources like raw materials or packaging? If so, how with a process mapping change factor into reloading?
However, the value in a single step doesn’t necessarily have to align with the process map’s general objective. So long as it’s of benefit to either the business or the client, the process map succeeds.
Comprehensive preventive maintenance and asset management ensure both the functionality, and efficiency of high-value equipment at a given business throughout its lifecycle. Yet, without an equally comprehensive auditing and optimization strategy for the ancillary processes around enterprise assets, businesses may accidentally overextend their operating budgets in unnecessary, preventable ways.
How can manufacturers, process industries, energy providers and other asset-intensive sectors optimize their preventive maintenance programs without hurting their productivity?
Reduce preventive maintenance schedule variance
When it comes to preventive maintenance, no matter how beneficial it may be to enhancing the performance of enterprise assets, it is possible to have too much of a good thing.
Is your maintenance schedule overbooked, underbooked, or just right?
Uneven scheduled downtime, for instance, could hike up operational costs in one of three ways:
- When preventive maintenance occurs too frequently, maintenance labor costs outweigh the threat posed by machine deficiency or outright failure. Balancing these costs is crucial to getting everything a business needs from its PM, but not overpaying for superfluous maintenance.
- Spacing scheduled preventive maintenance too far apart has its obvious consequences, like unintentionally allowing a small deficiency to exacerbate unnoticed.
- Choppy preventive maintenance schedules that vary hinder managers from planning strategically over the long term, both in an operational sense and financially.
Moreover, as The Maintenance Phoenix pointed out, scheduling variance could be the result of uncalibrated enterprise asset management software like computerized maintenance management systems (CMMS). Variance could also occur when maintenance professionals assigned repairs don’t carry out work orders within a tight timeframe. To cut down on preventive maintenance variance, businesses should assess their operational data, determine whether their maintenance programs suffer from any of these issues and take the needed corrective steps.
Minimize spare parts inventory management and costs
Traditionally, spare parts management follows along the same vein as asset management. In fact, there is considerable overlap between the two. Both preserve asset availability and mitigate the impact of downtime when it strikes.
That said, businesses must constantly work toward honing their spare parts inventory as much as possible without compromising the insurance these components provide asset uptime. Accomplishing this involves a two-pronged approach to spares: analysis and adjustment.
When a particular component within an asset breaks, an inventory of spare parts on hand accelerates the repair process. However, spare part inventory growth inexorably leads to cost increases, sometimes to the tune of as much as 20 percent or more of company expenditures, according to Life Cycle Engineering. Instead of adding a new batch of spares to the pile whenever assets appear to require them, it might be more cost-beneficial to perform root cause analysis on the “bad actor.”
For example, if a manufacturer spends $2,000 per month stocking fan belts for an asset integral to production, perhaps spending a little more on a one-time RCA cost may uncover why the asset churns through fan belts in the first place. A successful RCA, followed by corrective maintenance, could effectively eliminate the recurring cost entirely.
After tackling spare parts inventory, businesses should then be sure to adjust procurement plans accordingly so they represent the new optimized operations precisely and cut costs.
Process industries, perhaps more so than any other, need a strong risk management approach since they experience and interact with risk on a daily basis. Due to the continual nature of a process-focused enterprise, these companies ostensibly subject themselves to the highest level of risk because they’re continually operating without stop.
As such, the most production-minded companies who pride themselves on efficient, timely output require a stellar and comprehensive risk management strategy. But risk is multifaceted, and in many ways, proper risk management deployment can positively impact and maximize lean processes.
“Everyone working at a processing plant assesses and manages risk.”
How does risk management apply to lean processes?
Lean processes boil down to the elimination of waste. While some experts may argue honing operations has more to it than, the mission of an average company seeking to increase value potential is to “trim the fat” and reduce areas of excess. According to Lean Manufacturing Tools, some of these areas include overproduction, overprocessing and extraneous movement.
However, promoting a true lean mindset shouldn’t hinge myopically on the problem, but the factor or process that yields the problem. This is where risk management comes in. In one way or another, everyone working at a processing plant assesses and manages risk. For example, when an employee applies his occupational knowledge by safely operating heavy machinery, he’s leveraging the risk of injury with his expertise. That said, risk management doesn’t exclusively pertain to preventing injuries in the workplace. That same employee prevents value loss by processing material properly.
Managers and supervisors seeking to flesh out their risk management simultaneously enhance their lean capabilities. BASF explained risk matrices as a very simple math problem: Risk equals probability times severity. This means equal weight is given to small issues that occur frequently and huge ones that only happen once in awhile. Lean process oversight follows similar guidelines: Waste production can be glaring or ingrained in the system, but either way, it’s unwanted at a business seeking efficiency.
Proper risk management avoids processes that could take down the whole operation.
Why risk management and lean operations complement each other without redundancy
In fact, many common areas typically attributed to managing risk are practically blood-related to lean opeations. For instance, since the advent of the digital age, data curation has wedged itself into every industry. Regardless as to what companies do, these days, they all do it with data. In process industries, apart from customer data, information gleaned from machinery and integral technologies can provide managers with valuable insight toward both eliminating inefficiencies and removing risk from the equation.
For example, if a piece of smart equipment reports to a company’s operational risk management system that it’s running too hot, this procedure blends liability control with lean best practices. Not only do these alerts reduce the chances of worker injury, but they also give supervisors an advanced opportunity to address the issue on their own terms, rather than having to deal with a crippled production line completely out of the blue. A Mälardalen University study found downtime can consume almost a quarter of a manufacturer’s total cost ratio. Thankfully, intelligent data deployment and management can resolve those risks and many more.
The biggest mistake a person looking to optimize their production can make is cutting corners. Lean processes aren’t made by throwing the baby out with the bathwater, but by utilizing the resources available with the most innovative and effective methods. operational risk management keeps workers safe, but it’s just as important as a deterrent for expensive downtime, compromise products and surprise repairs.