-
Subscribe to Blog:
SEARCH THE BLOG
CATEGORIES
- Aerospace
- Asset Maintenance
- Automotive
- Blog
- Building Products
- Case Studies
- Chemical Processing
- Consulting
- Food & Beverage
- Forestry Products
- Hospitals & Healthcare
- Knowledge Transfer
- Lean Manufacturing
- Life Sciences
- Logistics
- Manufacturing
- Material Utilization
- Metals
- Mining
- News
- Office Politics
- Oil & Gas
- Plastics
- Private Equity
- Process Improvement
- Project Management
- Spend Management
- Supply Chain
- Uncategorized
- Utilities
- Whitepapers
BLOG ARCHIVES
- July 2025 (1)
- June 2025 (4)
- May 2025 (1)
- April 2025 (1)
- March 2025 (1)
- February 2025 (4)
- January 2025 (4)
- December 2024 (4)
- November 2024 (2)
- October 2024 (6)
- September 2024 (5)
- August 2024 (5)
- July 2024 (6)
- June 2024 (3)
- May 2024 (3)
- April 2024 (4)
- March 2024 (3)
- February 2024 (4)
- January 2024 (5)
- December 2023 (2)
- November 2023 (1)
- October 2023 (6)
- September 2023 (3)
- August 2023 (4)
- July 2023 (2)
- June 2023 (3)
- May 2023 (7)
- April 2023 (3)
- March 2023 (3)
- February 2023 (5)
- January 2023 (6)
- December 2022 (2)
- November 2022 (5)
- October 2022 (5)
- September 2022 (5)
- August 2022 (6)
- July 2022 (3)
- June 2022 (4)
- May 2022 (5)
- April 2022 (3)
- March 2022 (5)
- February 2022 (4)
- January 2022 (7)
- December 2021 (3)
- November 2021 (5)
- October 2021 (3)
- September 2021 (2)
- August 2021 (6)
- July 2021 (2)
- June 2021 (10)
- May 2021 (4)
- April 2021 (5)
- March 2021 (5)
- February 2021 (3)
- January 2021 (4)
- December 2020 (3)
- November 2020 (3)
- October 2020 (3)
- September 2020 (3)
- August 2020 (4)
- July 2020 (3)
- June 2020 (5)
- May 2020 (3)
- April 2020 (3)
- March 2020 (4)
- February 2020 (4)
- January 2020 (4)
- December 2019 (3)
- November 2019 (2)
- October 2019 (4)
- September 2019 (2)
- August 2019 (4)
- July 2019 (3)
- June 2019 (4)
- May 2019 (2)
- April 2019 (4)
- March 2019 (4)
- February 2019 (5)
- January 2019 (5)
- December 2018 (2)
- November 2018 (2)
- October 2018 (5)
- September 2018 (4)
- August 2018 (3)
- July 2018 (2)
- June 2018 (4)
- May 2018 (3)
- April 2018 (3)
- March 2018 (2)
- February 2018 (2)
- January 2018 (1)
- December 2017 (1)
- November 2017 (2)
- October 2017 (2)
- September 2017 (1)
- August 2017 (2)
- July 2017 (2)
- June 2017 (1)
- April 2017 (3)
- March 2017 (3)
- February 2017 (2)
- January 2017 (2)
- December 2016 (2)
- November 2016 (4)
- October 2016 (4)
- September 2016 (3)
- August 2016 (6)
- July 2016 (4)
- June 2016 (4)
- May 2016 (1)
- April 2016 (3)
- March 2016 (4)
- February 2016 (2)
- January 2016 (4)
- December 2015 (3)
- November 2015 (3)
- October 2015 (1)
- September 2015 (1)
- August 2015 (4)
- July 2015 (6)
- June 2015 (4)
- May 2015 (7)
- April 2015 (6)
- March 2015 (6)
- February 2015 (4)
- January 2015 (3)
CONNECT WITH US
Tag Archives: Six Sigma
The automotive manufacturing industry has been traveling a strange and bumpy road over the past couple of years. The pandemic created a traffic jam in the supply chain. At the same time, demand for new cars dried up. Who was driving? Everyone was at home during the lockdown. And on the heels of that, interest in electric vehicles began to surge. According to research by the International Energy Association, the demand for EVs is expected to rise 35% by the end of 2023 after a record-breaking 2022.
What did it all mean for auto manufacturers? Demand for traditional vehicles lowered as demand for electric vehicles grew, forcing auto manufacturers to do a delicate dance of balancing the type of production they’ve always done with the new processes and systems needed to produce EVs. The moving target of demand coupled with shaky supply brought about inventory uncertainty — how much was enough, but not too much? And then, there was (and continues to be) the labor shortage, with seasoned workers retiring and younger ones not exactly flooding through the doors.
Improving processes is paramount for the automotive manufacturing industry now. Here are a few ways you can do that:
Lean Six Sigma. If there ever was a need for auto manufacturing process improvements like the ones Lean Six Sigma can produce, it’s now. LSS is the blending of two efficiency methodologies, Lean and Six Sigma. It’s a bit ironic, because the Lean methodology, which focuses on efficiency and eliminating waste, was developed back in the day by Henry Ford… or at Toyota, depending on who you ask. It got its start on the auto manufacturing line, with the intent of eliminating the “seven deadly wastes”: overproduction, waiting, transporting, processing, inventory, excess motion and defects. At USC Consulting Group, we’ve added an eighth waste. People. Specifically, not using them to their fullest, not seeing untapped potential in great workers, and not training and developing people to rise through the ranks. Lean is about eliminating waste to produce more product quickly and efficiently.
Six Sigma, the other side of the Lean coin, is about quality control. Minimizing flaws and defects. But it’s deeper than that, rooted in data. The goal is to improve cycle time while eliminating or reducing defects.
SIOP. It’s difficult to achieve careful, accurate planning for the future when the road ahead contains so many bumps. That’s why we take the usual sales and operations planning (S&OP) process to a different level by adding inventory to the mix. The goal is to look ahead, anticipating the inventory you need while also coordinating with sales, marketing, and finance to involve the entire organization in this process. A key to SIOP is using inventory as a strategic tool to help offset variation in either demand or production issues.
Predictive Maintenance. Yes, it sounds extremely basic, but we find that heading off trouble before it starts can eliminate the risk of bogging down your entire production line to fix what’s broken.
Skills Training. Investing in training is playing the long game, but in light of your best people on the line retiring and fewer people to take their place, it’s paramount. Training has advantages in addition to the obvious — your people being more skilled on the job. It also demonstrates in a very tangible way that you are committed to the growth and success of your employees. You gain loyal workers and create a pipeline for advancement. It’s a win-win.
Technology Investments. USC Consulting Group is not about coming in and asking manufacturers to invest in the latest and greatest technology in order to become more efficient. No, efficiency takes harder work than just installing a new machine. However, in some cases, it’s necessary to level up. Legacy technologies don’t have the same features and capabilities as newer models. And in the auto manufacturing industry, you’re dealing with producing an entirely new product with electric vehicles. It may be time to look at your technology and decide if it can take you into the future or keep you in the past.
Doing business in the automotive manufacturing industry is like driving a manual transmission. You are constantly shifting gears to keep pace with traffic – in this case, the consistent change of consumer demand. Operations consulting helps companies improve their processes and be prepared for what’s coming down the road. We help manufacturers become more efficient and profitable in this or any economy.
Is working with operations consultants an untraveled road for you? Please get in touch. We’d love to talk with you about it.
Leo Tolstoy once said: “Everyone thinks of changing the world, but no one thinks of changing himself.”
How true that is. Sure, he was talking about the Russian Revolution, but the words of the author of War and Peace, considered by some to be the greatest novel ever written, are just as applicable in today’s manufacturing workplaces as they were back then. It’s especially true when manufacturers are going through the process of implementing Lean Six Sigma.
When you’re talking about a culture change as big as Lean Six Sigma (LSS), it can feel a bit like your company is going through a revolution. And as Tolstoy so astutely pointed out, changing the “world” — your workplace culture, processes and procedures — is all well and good, but changing oneself and one’s role in it? Is that really necessary? As hard as it is for many managers and top leadership to hear, the answer to that question is “yes.”
It’s hard to hear and even harder to accept because, inherent in the concept of change is the notion that you were doing something wrong. People who have been on the job awhile, from the workers on the front lines to the people in the corner office, are resistant and, dare we say, defensive about that notion. But it’s not about companies doing something wrong. It’s about finding opportunities for greater efficiency, throughput and, frankly, profit.
At USC Consulting Group, we help companies implement LSS. Our Lean Six Sigma Master Black Belt, Dr. Frank Esposto, leads many of these implementations. But as Frank tells companies, LSS isn’t just about a new set of tools and operating procedures. It’s about culture change, too. And managers and top brass embracing that change is crucial to LSS success.
Lean Six Sigma 101
Here’s a quick rundown of Lean Six Sigma.
The whole concept of Lean started with either Henry Ford or Toyota, depending on who you ask. The idea was identifying and eliminating waste in manufacturing operations. Toyota called them the “seven deadly wastes” and that term stuck. At USC, we added an eighth. They include:
- Overproduction. It leaves you with unused product.
- Waiting. Waiting on the shop floor between steps on the line, or waiting on supply or even equipment.
- Transporting. Excessive movement of inventory, causing the possibility of damage, or even excessive movement within the manufacturing process itself.
- Processing. Do you have extra, unnecessary steps in the manufacturing process?
- Inventory. Too much stock on hand.
- Excess motion. Extra walking, lifting, reaching.
- Defects. Defects in product happen to the best of us.
- People. This is the eighth waste. It is about taking a close look at the untapped potential of your people.
The goal is to create greater efficiency on the line.
Six Sigma is a set of techniques aimed at reducing (in a perfect world, eliminating) the probability that an error or defect will occur in the process.
Together, as Lean Six Sigma, the two methodologies pack a punch of efficiency and perfection. LSS enables companies to produce better product faster, increasing throughput and quality.
Learn more about LSS in our eBook – Lean Six Sigma: Do You Really Know These Methodologies?
Why culture change is so important to LSS success
There’s a perception out there that Lean Six Sigma is simply a series of process improvements designed to eliminate waste and increase quality. It is that, for sure. But it also requires the aforementioned culture change. A change in attitudes and behaviors. Everyone, from frontline employees to the corner office, needs to be on board or this change won’t stick. You’ll slide back into your old ways.
It’s vital for the workers performing new processes to embrace those changes. But it’s just as vital for managers and supervisors and the top brass to change, too. Remember, you can’t change the world without changing yourself first.
What managers can do to embrace change
In order for the LSS changes to be sustainable, managers and executives need to demonstrate to employees that they’re on board. And that doesn’t mean sending out a memo of encouragement. It means changing daily work habits, just like employees are expected to do. A few ways to do that:
Walk the floor. This is arguably the most important piece of this puzzle for management. Get out of the office and onto the shop floor. Get into the trenches with your frontline employees. Show them you’re all in.
Ask senior employees for advice and input. You know who we’re talking about. The men and women who have been on your frontlines forever. Shift supervisors. Trusted workers. The people actually doing the job day after day. When you’re in the process of implementing LSS, their input is vital. Not only to the success of the project, but to their buy-in as well.
Roll up your sleeves. If it’s crunch time and you’re shorthanded, take off that suit coat, roll up your sleeves and help out any way you can.
Over the years, we’ve seen how companies that embrace change will succeed in becoming more efficient and profitable. Those that don’t may simply slide back into their old ways.
For leadership teams leading the charge for culture change, we lean on advice from Mahatma Ghandi, “Be the change that you wish to see in the world.”
If you’re in manufacturing, you’ve certainly heard of two process methodologies, Lean and Six Sigma. Lean, which has been around forever and has recently migrated from the manufacturing floor into other industries (they’re even talking about Lean HR methods) and Six Sigma, a newer technique. Two sides of the same coin, Lean looks at making processes more efficient and reducing lead times, while Six Sigma focuses on cutting down on defects. Both are useful goals when aiming to optimize your processes, throughput and ultimately, your bottom line.
Lean vs Six Sigma, which is better? Which should you be investing in if you’re coming up against inefficiencies in your production, and can they be used together?
Let’s take a closer look at both methodologies to see who comes out on top in this operational improvement matchup.
Lean
The whole concept of Lean started with identifying and eliminating waste in manufacturing operations. Pioneered back in the day by Toyota… or by Henry Ford even earlier, depending on who you ask, Lean manufacturing is about cutting costs, eliminating waste in both processes and products, and generally becoming as “lean and mean” as possible to reach optimal efficiency. The heart of the process is identifying and eliminating what Toyota called the “seven deadly wastes.” (We happen to think it’s eight.)
- Overproduction. Making too much leaves you with unused product.
- Waiting. This includes waiting on the shop floor between steps on the line, or waiting on supply or even equipment.
- Transporting. This covers excessive movement of inventory, causing the possibility of damage, or even excessive movement within the manufacturing process itself.
- Processing. Do you have extra, unnecessary steps in the manufacturing process? Are you doing in two or three steps what you can do in one?
- Inventory. Too much stock on hand. During the pandemic, many companies combatted supply chain delays by stocking up on inventory. We think that’s a mistake.
- Excess motion. This means getting from Point A to Point B on the floor, extra walking, lifting, reaching. Can things be configured more efficiently?
- Defects. Defects in product happen to the best of us.
- People. This is the eighth waste, which Toyota didn’t identify. Are you using your people to their fullest potential? Or is there untapped potential for a great manager or supervisor you haven’t noticed?
Examining all of these areas of “wastes” in your operation will help you become more efficient and ultimately more profitable. In other words, lean and mean.
Six Sigma
Six Sigma, at its most basic level, is about quality control. Minimizing flaws and defects. But it’s much deeper than that. Six Sigma is data driven, statistical and aims to improve cycle time while eliminating or reducing defects in manufacturing. It’s about using stats, data analysis and also project management techniques to improve the whole process.
The Six Sigma process is defined by an acronym: DMAIC. Define, Measure, Analyze, Improve and Control. First, you define the problem that you want to improve. Then, the team measures the process and analyzes it by using data analytics to get to the root of the problem. From there, it’s about creating improvements and fixes, and setting up controls to make sure it doesn’t happen again.
Six Sigma requires rigorous training to get the process right, so rigorous that practitioners need a certification in the process. The certifications are ranked with a belt system similar to martial arts, with white belts being familiar with the basic process, up to black belts who become masters of the process and are certified to take on complex problems and projects, and to train others in it.
Lean Six Sigma: Better together?
Should it really be Lean vs Six Sigma? Or rather Lean AND Six Sigma? Can these two powerful methods be used together? Yes indeed. In fact, they’ve joined to become one methodology in some circles: Lean Six Sigma, or LSS, which aims to cut defects and shorten lead times.
But, here’s the tricky part.
Ironically, Lean and Six Sigma can clash if not deployed correctly. Defects can be reduced by slowing processes down — reducing speed. On the other hand, you can increase the defect rate by speeding up processes.
Getting it right, striking that perfect balance is imperative. That’s why it requires training and certification in the techniques. At USCCG, Dr. Frank Esposto is our Lean Six Sigma Master Black Belt and Senior Director of Quality. He is also a certified LSS instructor.
Dr. Esposto states, “When we employ the Lean Six Sigma methodology to help our clients’ operations, we don’t simply come in and do it for them. We train clients in these techniques so they can employ them long after we leave.”
The training course Frank teaches is rigorous and hands-on. When participants complete the course, they are certified. Being certified in Lean Six Sigma is a highly sought-after skill.
To summarize, it is not Lean vs Six Sigma, but rather Lean Six Sigma – two complimentary methodologies that when balanced properly reduce operating costs, increase throughput, and achieve overall improvement to your bottom line.
Are you interested in learning more about how these powerful methodologies can work to optimize your processes? Give us a call today. In the meantime, read much more about LSS in our eBook: “Lean Six Sigma: Do You Really Know These Methodologies?”
How well do you know Lean? The concept is nothing new. Pioneered back in the day by Toyota… or by Henry Ford even earlier, depending on who you ask, Lean manufacturing is the art of maximizing customer value while minimizing waste. It’s about cutting costs, eliminating waste in both processes and products, and generally becoming as “lean and mean” as possible to reach optimal efficiency.
Another, newer term is often bandied about when talking about Lean: Six Sigma, a methodology designed to tackle defects in manufacturing and product/service development. Two sides of the same coin, while Lean looks at making processes more efficient and reducing process lead times, Six Sigma focuses on cutting down on defects. In fact, they’ve joined to become one methodology in some circles. Lean Six Sigma, or LSS, which aims to cut defects and shorten lead times. What is it? Are they stronger together? Could they clash? Who should use it? And who shouldn’t?
For answers to these questions, read USC Consulting Group’s eBook Lean Six Sigma: Do You Really Know These Methodologies? We’ll look deeper into Lean Six Sigma through the lens of Dr. Frank Esposto, USCCG’s Lean Six Sigma Master Black Belt and Senior Director of Quality, and a certified LSS instructor. You think you know Lean Six Sigma? Download the eBook below to find out.
Dr. Esposto discusses Toyota’s classic Lean manufacturing model that identifies “seven wastes” and he recommends you expand your mind to add one more. Furthermore, he will advise you on the best strategies for LSS training, the key challenges you will face, and the factors that lead to successful LSS implementation in your operations.
Applying the Lean Six Sigma methodologies effectively in your processes is not a one-size-fits-all and may require help. Dr. Esposto elaborates on the tools, techniques, and methods to use and the benefits you will gain from it.
So, how well do you know Lean Six Sigma methodologies? A whole lot more once your read this eBook.
Imagine a scenario in which there is unprecedented demand for the products you manufacture, but disruptions in the supply chain are making it difficult, if not impossible, to meet that demand and even if you do, logistics bottlenecks are preventing them from getting where they need to go. Many manufacturers have been running up against this problem since the pandemic began.
Now imagine that people’s very lives literally depend on those products being manufactured and delivered to their destinations.
If you’re in the medical device manufacturing industry, you’re likely thinking: “Welcome to my world.” Not only has it been as hard hit as any other manufacturer by supply chain disruptions and logistic backups, the implications of the resulting shortages of the devices they manufacture may cost people their lives.
The FDA is calling the shortages of medical devices at this critical time a “public health emergency.” It published a device shortage list including the categories of personal protective equipment for medical workers, testing supplies and equipment, and ventilation-related products. The list also outlines the specific products, the estimated duration of the shortage, and the reasons for the shortages, along with what the government is doing about it.
That list is illuminating — and even frustrating — for many reasons, but it’s not all bad news. Among the most common reasons for shortages, including increased demand and supply chain issues, which manufacturers have little control over, there is also one culprit that manufacturers can control: “Requirements for complying with good manufacturing practices.”
As medical device manufacturers know, the FDA has strict compliance requirements that affect every part of the process from designing to manufacturing to testing to shipping, even labeling. In those processes, there can be room for improvement. That’s something manufacturers can do — process improvements to get their products to market faster, while still complying with the FDA.
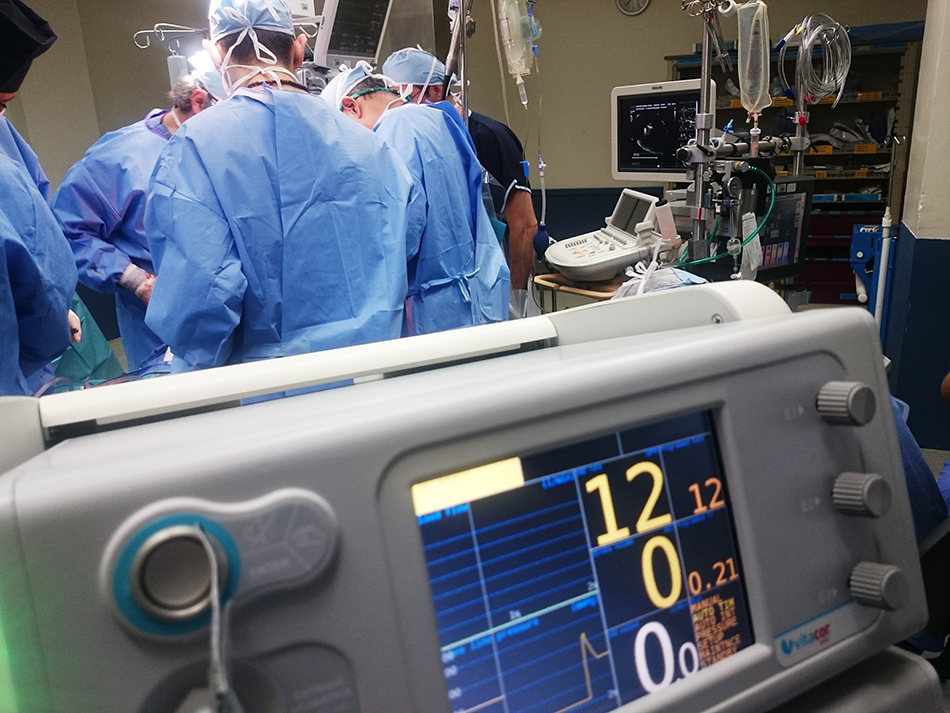
The FDA is calling the shortages of medical devices at this critical time a “public health emergency.”
What medical device manufacturers can do now
At USC Consulting Group, we’ve been helping manufacturers up their operational efficiency for more than 50 years. We analyze what you’re doing, how you’re doing it, and how we can create greater efficiency using your existing resources. A few tactics we’re implementing with our medical manufacturing clients to help mitigate these shortfalls and get their products to people who need them quicker include:
Investigate Lean / Six Sigma
Lean manufacturing is nothing new. The art of maximizing customer value while minimizing waste was pioneered by Henry Ford … or Toyota, depending on who you ask, decades ago. Six Sigma is a newer methodology designed to tackle defects in manufacturing. While Lean looks at making processes more efficient and reducing process lead times, Six Sigma focuses on cutting down on defects that can delay production. In fact, they’ve joined to become one methodology in some circles. Lean techniques help you get product off the line faster, heightening your throughput. Six Sigma strives to target the reason for any defects in the products. These two techniques can conflict — one sure way to cut down on defects is to slow down the process, which runs counter to Lean’s goals. Achieving the perfect balance between the two, and getting the job done faster with fewer defects, is indeed an art form, and worth exploring.
Use SIOP to make your planning and forecasting bulletproof
We recommend using SIOP (Sales, Inventory and Operations Planning) to elevate your planning process to achieve that perfect balance between your supply and demand. You’ve heard of S&OP, a popular business management process that involves sales forecast reports, planning for demand and supply, and other factors. The goal is to help companies get a better, more clear look at their operations and create better-informed strategy decisions, allowing them to deliver what clients need in the most profitable way.
It’s a useful process, but we’ve found a lot of our clients do not include inventory as a strategic tool in their S&OP process. Therefore, they leave the “I” out of SIOP. Adding inventory into the mix is just one additional step, but we find it can be the key to the whole process. When you’re focusing on inventory, it requires more careful planning and elevates the entire planning process up a notch. When your inventory is optimized, which is not an easy mark to hit in these days of supply chain disruption, things tend to fall into place. With SIOP, you can make your inventory work harder for you.
Download our free eBook, “Sales, Inventory and Operations Planning: It’s About Time,” to dive deeper into SIOP.
Involve your frontline employees
We call it the Employee Involvement Prototype (EIP). It’s about engaging with your employees at the machine level and getting good data from the floor. It includes anyone who has to do with the line, and entails taking a look at those operations and processes with input from the men and women who are actually doing the job on an hour-by-hour basis.
Focus on throughput, productivity and yield
Take a good look at what’s happening on the line. What is the “drumbeat”? Are all your functions in sync? Can you improve production by cutting redundant steps?
For more information on these two points, download our whitepaper, “Strategies for Meeting Increasing Customer Demand.” It goes into much more detail about how you can create that proverbial well-oiled machine.
When it comes to caring for people and providing the products they need, time is of the utmost importance. Medical device manufacturers understand they must overcome the worst supply chain disruptions to deliver to the people whose lives depend on them.
Need help? Give us a call. We can save your operations so you can save lives.
One of the most effective methods of analyzing operational breakdowns is to conduct a Root Cause Analysis (RCA). Some of the data needed in order to drive the analysis includes all of the unplanned failure work orders, which component required repair for each work order, and how long each work order took to complete. This analysis can be conducted on each individual piece of equipment, an entire fleet of the same type of equipment, an entire fleet of the same piece of equipment purchased in the same year, or the entire fleet as a whole. Each Computerized Maintenance Management Software (CMMS) will calculate these values in its own way. The more specific to each individual piece of equipment, the better; however, total fleet size and time constraints may not allow for each piece of equipment to be analyzed on an individual basis.
Frequency vs Severity
The objective of the RCA is to select a failure that is having a substantial impact on the equipment in question. This can either be based on frequency or severity. Frequency being the amount of times the failure occurs within a given period. Severity being the cumulative time it takes to make the repairs within a given time period. Ideally, one or more types of failures may have a high frequency and a high severity. Collecting this data alone may uncover some surprising results. For example, some quick and easy repairs that do not take long can add up very quickly if the frequency is high enough. This can come as a shock when the total time spent on this one repair is tabulated.
Take, for example, the case of the Dead Battery (Figure 2). This repair on average may only take between half an hour and an hour for a mechanic to complete, including mostly drive time and a quick battery boost. It is such a quick, straight forward solution that it may not have captured much of management’s attention. Nevertheless, when you consider how many times a dead battery has occurred in the last three months and total the hours involved in correcting this issue, it may show up as the number two consumer of the maintenance department’s human resources (mechanics labor hours). Management must be critical at this point of statements such “that’s just the work environment.” Questions need to be asked about what can be done to improve the failures that drain the greatest amount of the department’s resources.
An important element to consider is that there are always multiple root causes for any given failure. The intent of conducting the RCA is to uncover all of the individual root causes that may lead to the failure of the component in question. The true root causes are rarely uncovered at the first layer of asking “Why?” for the first time. Each answer provided must then be analyzed all over again, and this process must continue until all avenues have been explored and the group has arrived at a tangible end. It will often take five “whys” to uncover the true root cause of an issue. Once the session has uncovered all of the possible root causes of the failure in question, a solution must then be presented to address each one individually.
These solutions come in the form of action items which are reviewed at the end of the meeting by the management team, responsibility is assigned, expected completion dates are provided, and the method in which the solution will be accomplished is discussed.
After conducting a Root Cause Analysis, the management team will have a list of action items. All of which will have varying impacts on the equipment’s reliability. It is important that the management team takes the time to assess each item on two main criteria: how easy the item will be to complete and to what extent its effect is predicted to have on the equipment. Combining these two scales will provide a strong basis for prioritizing action items and deciding what to tackle first. The management team should begin with the high impact, easy to implement action items and leave the low impact, hard to implement action items for last.
RCA Action Item Generation
When considering what corrective actions can be taken in order to solve the root causes of the failure in question, keep in mind the areas or touch points where changes can be made to affect the equipment. Again, these can be simplified as:
► The Operator (how the equipment is used) – Change the process in which the equipment is used. Sometimes an operator is using equipment incorrectly or in a harmful way without knowing it. Added training will often improve these issues. It is common for operators to be required to inspect all equipment before use. This usually occurs in the form of a pre-use checklist. This checklist can be modified to draw the operator’s attention to certain areas of the equipment in which wear can be seen. Noting this wear, and informing maintenance, can prevent the component from failing during use.
► The Mechanic (how the equipment is repaired) – Sometimes the method in which repairs are made inside or outside of the shop will affect the way the equipment operates. If the equipment’s use is required at the time of breakdown, a mechanic may provide a “patch” to ensure it runs immediately. These “patches” however, will not always last until the next service date for the piece of equipment.
► The Service (how the cyclical services are conducted) – Consider the actual activities performed on the equipment during its regular preventative maintenance service. Can these activities be changed or include more that would prevent the root cause in question? Perhaps a specific component that is failing often needs to be cleaned during the service or inspected specifically for signs of wear.
► The Design (how the equipment is designed or modified) – In underground mining, equipment modifications are often required by law in North America before the equipment can even be commissioned. These modifications can vary depending on the type of underground mine. It is important to understand what impact these modifications have on the operation of the equipment. In the Dead Battery case example, maybe the equipment in question was outfitted with additional lights to make it safer to drive underground where it is pitch black. The addition of these extra lights places a larger strain on the battery and alternator. Have the battery and alternator been upgraded to keep up with this added strain as well?
These are the areas that the department has complete control over. An organization cannot control the weather, but they can understand what effects the weather has and correct them at their root. Winter brings cold temperatures; cold temperatures make it difficult for equipment to start.
The temperature cannot be changed, but where the equipment is parked can be. Can they be stored in a heated area? Could block heaters be installed at low cost? These are the kinds of questions that must be discussed in the Root Cause Analysis session with all stakeholders in the room.
Finding the root causes of operational hardships can minimize downtime and significantly boost productivity. With over 50 years of operations management experience, USC Consulting Group can troubleshoot any issues and establish preventative maintenance processes to enhance your asset management. Reach out today to learn more on how to set up an effective Root Cause Analysis.
Innovation is driven by technological advancements, but far too often, manufacturers across all industries are overly concerned with how to bring the cutting edge to their products as opposed to their processes. The Big Data movement, canonized the world over as the saving grace for the burgeoning deluge of computerized information, allows businesses to do astronomically more in regards to customer relations and demand forecasting than once thought possible – that is, these companies can create a friction-less environment in which they can consume data at nigh-negligible costs, and apply their findings with minimal oversight and spend, resulting in momentous value-add potential.
But without the proper IT architecture in place, this can only be a pipe dream for businesses unwilling to bump up internal technological resources directly connected to production, be it the process or the product. Applications designed to monitor and control lean manufacturing initiatives can enhance the industries that bring them aboard, so long as these applications in question put the horse back before the cart, so to speak. What process improvements can be made to data-intensive operations using objective-minded management?
In manufacturing, measurement is everywhere, including data and process improvement.
Performance measurement
Believe it or not, metrics utilization isn’t just for the world of business – these days, the average individual uses a number of different “signals” to interact with the world around them, like how smartphone apps let hurried commuters know exactly what time public transportation pulls out of the station. In a sense, even low-tech devices like a car’s fuel gauges serve roughly the same purpose: conglomerating disparate information under a single, user-friendly visualization. In recent years, gas tank telemetry has evolved beyond simply stating fractions, but estimating how many miles a driver has left before refueling becomes a necessity. This is a much more actionable unit of measurement for this particular metric, as it assumes drivers won’t want to fill up unnecessarily as a means of saving money and time if it can be avoided without hindering functionality.
In a manufacturing plant, similar rules apply, but as industries grow more and more complex, production metrics continue to include more dimensions and incorporate larger volumes of data. However, the end results must be just as easy to understand and act on, perhaps even more so. Additionally, all manufacturers charting key performance indicators (KPIs) do so as these metrics relate to their own operations. Lean or Six Sigma only works so far as companies can identify their own shortcomings and apply these systems like antiseptic to a wound. According to a study by the faculty of manufacturing engineering at the Technical University of Malaysia, more often than not, KPIs “reflect the company’s mission, vision, objectives, and goal which are key imperatives to the company’s success,” especially when it comes to employee management. Any worthwhile application managing KPIs and alerting decision-makers as to vital data must therefore be as reliable as it is flexible to specific needs.
“Data from the end of a given process should inform operations at the very beginning.”
Process Improvements
Collecting and reporting on terabytes of data is one thing, but what can the right data management platform do to streamline tangible on-site workflow? Operational process improvements and efficiency can be gained through data management applications driven by lean manufacturing principles like kanban, or a system of inventory control where production information acts as a catalyst. The popular “pull, don’t push” paradigm used throughout manufacturing finds a home here as well. Data from the end of a given process should inform operations at the very beginning to promote efficient resource spend and temper production based on throughput potential. If a popular nightclub reaches capacity but the bouncer continues to allow guests entry, it creates an unsustainable and unsafe situation for everyone involved. However, if that same bouncer grants access based on how many guests leave, the venue can serve the most patrons without causing a commotion.
That said, as the Massachusetts Institute of Technology outlines, small discrepancies in different kanban-focused data management tools could actually stifle objective-based process improvements and detract from lean manufacturing practices. Certain lean manufacturing data management assets compartmentalize different actions in a given process and assign products within production as “carriers of information.” Returning to the nightclub analogy, if the bouncer has to occasionally go into the club and manually count occupants, this can create inefficiency and can convince people waiting in line for admission to seek out another place to spend their Friday night. But if that bouncer uses a counting device at the door, he or she can immediately respond to a happy party leaving as the impetus for allowing more people in. Similarly, manufacturers shouldn’t be “counting heads” so much as they should ensure their process improvements made to process management applications assign throughput data its proper role as a production instigator. In doing so, manufacturers avoid bottle-necked workflow and any resulting downtime, upgrading their efficiency through more intelligent datalogical deployments.
Process maps can help you improve operations and add value to your organization.
In lean manufacturing, process maps are powerful tools that can help you understand what your current processes look like now, and what they should be. On continuous improvement projects they are essential. If you have embarked on the journey of making your facility more efficient, but are facing difficulty figuring out exactly where you need to make changes, you should consult with proven operations consultants who can use process maps to help identify your problem areas and eliminate them.
Process maps provide a realistic view of a production process
According to Six Sigma Material, that process maps involve the creation of detailed flow diagrams of processes, using color coded symbols. These maps provide a high-level view of what operations look like and how processes work with one another. The intention behind using process maps is to help you see your processes as they really are. This can be a very valuable learning experience for you, especially if you are ready to start making improvements.
“Consultants can help you identify automation opportunities, duplication, redundancy, delays, and idle time.”
Using process maps, operations consultants can help you identify automation opportunities, duplication, redundancy, poor decision-making, delays, and idle time. Addressing any one of these areas can raise efficiency at your plant, but addressing them all is a game changer. In lean manufacturing, this is known as waste elimination. Process maps are documents that should be updated and analyzed on a regular basis. The more detail they have, the easier it will be for you to have the best process and capture opportunities.
Enhance your value stream with process maps
According to Lean Manufacturing Tools, process maps can add value and reduce costs in an organization. They are one of the most important tools in a consultant’s kit. It is important to point out, however, that process maps are only helpful if you take action. It is essential to have a clearly defined goal to work toward. In this way, the analysis of your process map will be based on amending existing processes to get you to where you need to be.
A comprehensive process map captures your value stream – the processes that your product goes through, from raw material to customer delivery. In your value stream, a product goes through a series of steps that either add value or waste time. Done right, a process map will find those weak areas and allow you to improve them. All non-value adding steps and delays should be fixed and reflected in the next iteration of the process map. As previously mentioned, this involves taking action, which will necessitate educating and training plant staff – another area where manufacturing consultants shine.
Lean Manufacturing Tools also pointed out that depending on the purpose of the mapping, there are various tools that can be employed. Before mapping, you should know exactly what it is you are trying to achieve. Are you trying to fix an individual work cell or the whole supply chain. Value stream mapping, for example, will help you see your whole process, but it won’t provide enough detail to analyze a specific process.
Use process maps to improve your operations and add value to your organization.
A comprehensive view of a facility’s processes
Six Sigma Material explained that a successful process mapping exercise combines all types of diagrams and should show you your processes from a macro bird’s-eye view as well as on a granular level, but accomplishing this will require effort from your whole team. Additionally, improving your operations will involve educating everyone on what the processes are like and how they should be improved. Some improvements are self-evident, others need a little bit of extrapolation.
If you attempt to create process maps on your own and they don’t end up perfect, don’t worry. There are many software programs that can help you handle the complexity involved. These solutions can help you identify rework loops, communication issues, delays, and other issues. Additionally, you can create a brown paper process map, which combines many different mapping tools on a roll of paper that is often hung on a wall. You may be shocked to discover the number of steps involved in creating one of these, as well as the people and forms involved in a basic process. You may also find yourself wanting to dig deeper. However, if this seems difficult, you should probably consult with a manufacturing consulting firm with a proven track record in lean manufacturing techniques. Lean principles are all about improving your value stream by removing obstacles, delays, and other inefficiencies. In this area, getting outside help is a good idea so that you can successfully achieve your desired results.