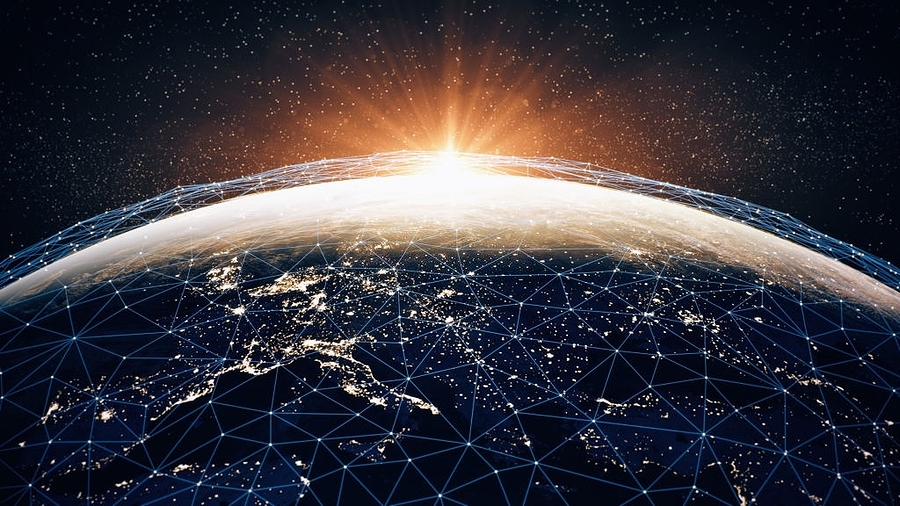
Why Supply Chain Improvement is Vital Now to Your Operations
If you’re like most manufacturers, your supply chain has been disrupted by COVID-19, especially if much of that supply came from China or Southeast Asia. Supply disruptions and downright stoppage hit back in February 2020, and demand dried up when the economy shut down shortly thereafter. Many manufacturers felt that one-two punch deeply. The U.S.-China trade war and other trade restrictions didn’t help matters, either.
Harvard Business Review predicts that, when the dust settles, this situation is going to shake out in the following ways:
- It will be a competitive advantage for manufacturers to increase their domestic production and domestic jobs.
- Manufacturers may face pressure to reduce or eliminate suppliers that are perceived as “risky,” like China.
- Manufacturers may want to consider cutting down the inventory in their global supply chains.
That sounds about right to us. We would add “look for hidden opportunities for efficiency” to that list.
But no matter how your supply chain looks when we emerge from this pandemic (and we will emerge from it) one thing will be certain. Consumers will still want a fair, if not low, price for whatever it is you’re manufacturing. Just because their supply chain is different than it was before February 2020, it doesn’t mean prices can soar. That’s going to be the biggest challenge. Moving forward, it will be vital to focus on supply chain improvement to ensure the success of your operations.
The Institute for Supply Management agrees, saying purchasing managers at some of the largest manufacturing companies expressed ongoing unease about future shocks to their supply chain while they scramble to remedy current shortages.
If your company is in a similarly tenuous situation, we have some recommendations for you to help shore up your supply chain risks and mend a broken supply chain.
1. Enhance communication with both customers and suppliers
Touching base with partners more frequently to avoid any confusion or misunderstandings is one of the best things you can do now in this uncertain supply chain environment. This is true for your customers as well as your suppliers. Customers who have low switching costs will find alternatives to your product if competitors are able to more promptly satisfy demand. Customer service level expectations have been lowered for many hard-to-get items during the pandemic, but if your product isn’t prompt, communication should be. Courteous responsiveness goes a long way to ease customer impatience.
2. Focus on strategic sourcing
It’s about enhancing transparency by leveraging intelligent data to more effectively forecast shortages. Strategic sourcing focuses on the development of long-term supply relationships for operationally critical products and services. Start by assessing the reliability of your current suppliers. Understand your relative importance to them as a customer, as well as the risks they are experiencing with their suppliers. Assess alternative vendors and your readiness to pivot quickly to a new supplier. If there are multiple vendors for a key material, inquire regarding their capability to handle increased supply requirements. This will help you affect supply chain improvement.
3. Stop, look and listen
No supply chain is perfect. Take time to walk the floor to see what could use some fine-tuning. Simply using your senses — looking and listening — can quite literally be eye-opening. Your employees and your machines can tell you a great deal about your current state of operations.
4. Increase your inventory
Lean manufacturing and Just-in-Time (JIT) inventory principles have enabled manufacturers to significantly reduce operating expenses and increase profitability. However, JIT inventory inherently comes with increased risk of supply outages. During times of uncertainty, perform cost-benefit analysis by assessing the holding cost of increased inventory levels versus the likelihood and cost of production disruptions.
[While you should increase your inventory to mitigate risks, here are 5 Reasons Why You Need to Stick with Lean Manufacturing Principles]
5. Look for ways to automate
Identify opportunities to automate certain work processes, diminishing cycle time and enhancing throughput. It’s about ferreting out those hidden opportunities for greater efficiency in your processes. That’s our wheelhouse, enhancing a company’s operational efficiency working with their current assets.
6. Keep an eye on maintenance
This isn’t the time to let machinery run on autopilot. Keep a regularly occurring maintenance schedule to head possible equipment breakdowns off at the pass. You can significantly reduce the effects of machinery snafus on production output if you’re on top of maintaining those assets.
At USC Consulting group, we’ve spent more than 50 years focusing on supply chain improvement and optimization. We can help you reduce your risks and vulnerabilities, which will lead to a more resilient and solid supply chain. Get in touch today.
[For more information about supply chain management, read our blog, 4 Ways Manufacturers Can Perfect Their Supply Chain]