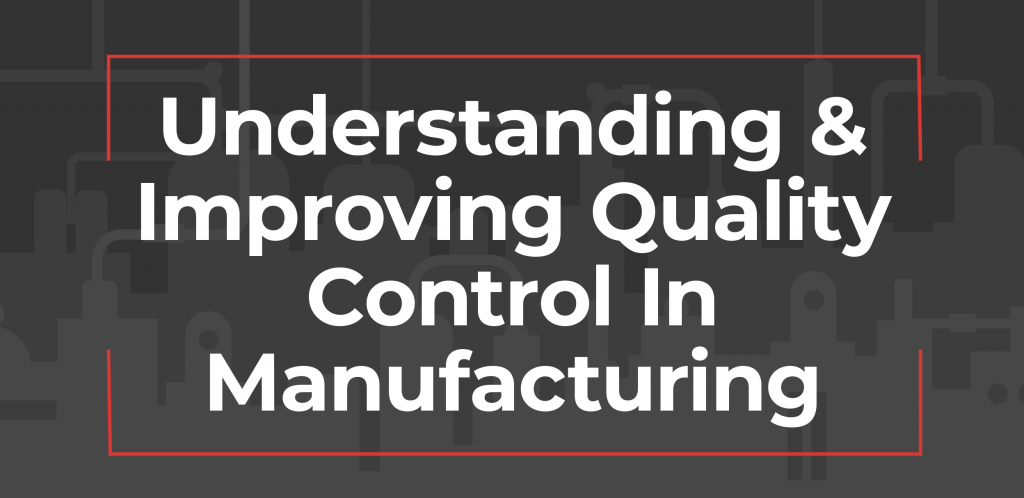
Understanding & Improving Quality Control in Manufacturing
For Manufacturers, Quality Control Should Be Sales MVP
For companies that manufacture products of any kind, there is a direct link between quality control and number of units sold. Engineers and technical staff sweating the QC details in the bowels of the factory may not see the link, nor may the salespeople who deliver high-tech presentations to million-dollar prospects in corporate suites. Nevertheless, the link exists, and it is solid: Well-made and consistent products boost revenues, while product defects drive existing customers and prospects into the eager arms of competitors.
The accompanying resource presents a highly focused overview of Quality Control that will be helpful for manufacturers, converting and fabrication, as well as personnel in manufacturing organizations who may not realize how important QC is to the success of their companies — and perhaps to their careers.
The term “quality control” is often used loosely and means different things to different people. The below infographic defines quality control and distinguishes it from quality assurance, another important discipline in manufacturing. The essence of quality control is its focus on preventing defective products from reaching the customer — this is the overarching goal of QC and the purpose behind every QC test, inspection, report and review. Once you understand this simple (but sometimes elusive) definition of QC, its connection to sales becomes crystal clear.
The Risks and Benefits of QC
The cost of product defects is high on a host of fronts. If customers receive defective products, a lot of bad things can happen. If the manufacturer is lucky, the defects will be identified on the receiving dock, in which case the costs may be “limited” to a rejection, return and replacement.
These situations are costly enough but still pale in comparison to the cost of having a bad product not be identified quickly and, instead, used by the customer. If the product causes severe monetary losses, injury or death, the cost of litigation (to say nothing of the human toll) could be enough to put even a large manufacturing organization out of business.
On the flip side, high quality standards help build a company’s reputation for quality; attract prospects; generate referrals; earn reorders; enable the company to set higher prices; and push competitors into other markets and products niches. This is why QC should be every employee’s favorite department. To learn more about quality control and how to improve it in your organization, please continue reading.
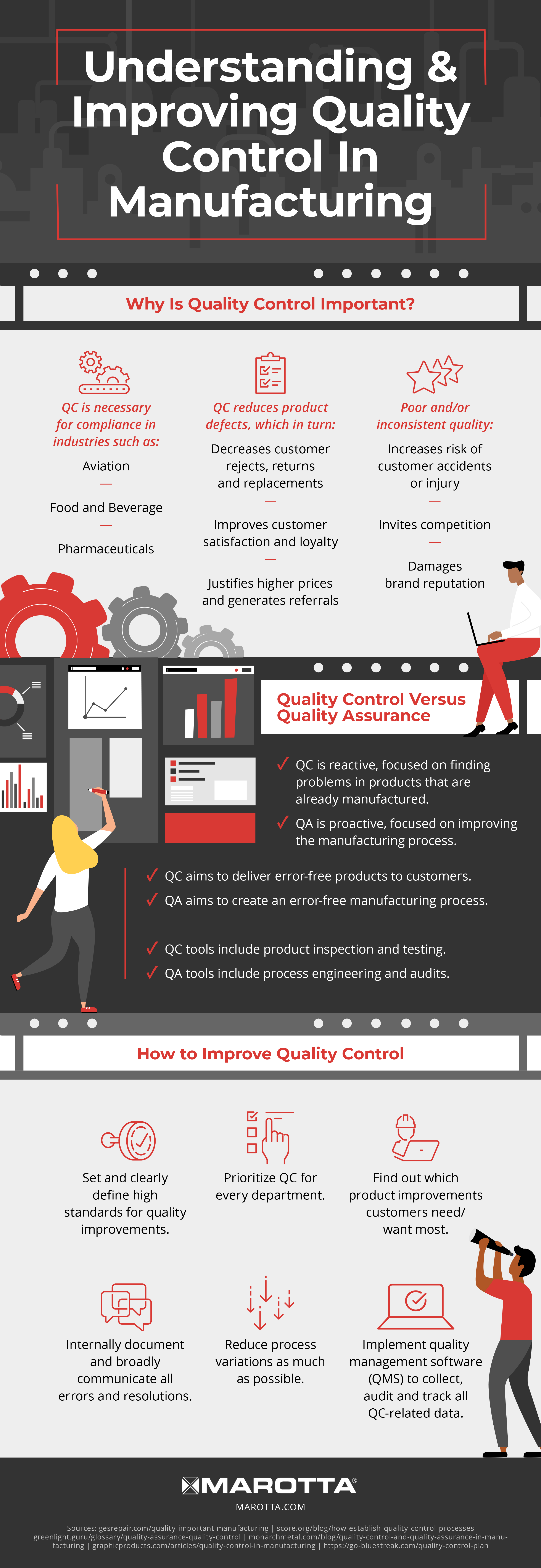
Quality Control in manufacturing from Marotta Controls.
Quality control is near and dear to the hearts of every USC Consulting Group consultant. We pride ourselves on the quality of our work and our 98.3% client satisfaction rating proves that fact. Contact us today and we can help improve the quality in your operations.