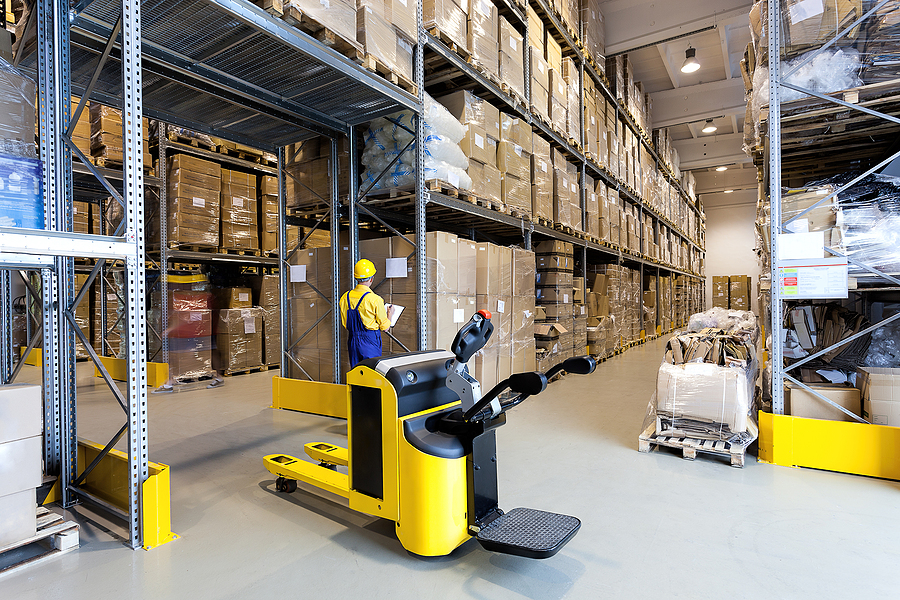
The Efforts You Need to Take to Improve Industrial Hygiene and Safety
The manufacturing industry keeps society ticking, but it consists of people. As technology advances, using it to improve worker safety reigns paramount, protecting the individuals who move the machines that create the products society uses daily. Keeping abreast of the latest developments to improve industrial health and safety helps owners and managers improve working conditions and processes.
Such improvements span every aspect of the industrial process, from producing the products to warehousing them and delivering them to customers. Responsible parties can draw inspiration from the innovations below to improve industrial hygiene and safety for a healthier and happier workforce.
Warehousing Procedures
Warehouses combine multiple workers and machines in a single small space, increasing the risk of accidents. Injuries can result from equipment misuse, failure to follow safety procedures or overuse stemming from repetitive motions. For example, approximately half of all workers at certain warehouses experience an injury within their first three years. Facilities have begun to implement the following innovations to decrease accident risk.
1. Warehouse Management Systems
These advanced computer programs boost efficiency by optimizing travel routes and times to streamline picking and putting away procedures. They can prevent “traffic jams” in aisles and decrease fall risk by keeping moving equipment like forklifts out of areas where workers are using ladders or scaffolding.
2. Robotics
Robots reduce repetitive motion injuries by taking some of the heavy lifting off human hands. Additionally, they can reduce fall risk by retrieving items on high shelves. Such technology also empowers warehouse managers to make better use of vertical space instead of increasing their facility’s footprint.
3. Appropriate Safety Gear
Relying on workers to supply PPE can result in the most vulnerable going without or investing in inferior protection to meet company requirements. Providing gloves, facial protection, hearing protection, steel-toed boots and reflective vests protects workers against sudden traumatic injuries while reducing some of the wear and tear of daily work on their physical selves.
Lockout/Tagout
Lockout/tagout procedures protect against electrocution and other traumatic events, such as crushing injuries when a piece of equipment goes down and multiple workers must coordinate their efforts to correct the problem. OSHA guidelines cover proper measures for controlling energy from electrical, mechanical, hydraulic, pneumatic, chemical and thermal sources. Compliance with these standards saves an estimated 120 lives yearly.
Here, too, technological improvements enhance worker safety. For example, video surveillance ensures workers apply the appropriate lockout devices to equipment before service work begins. Sensors can alert workers to energy remaining trapped in the system or sound the alarm if a stray body part enters the restricted area. Improved equipment testing ensures refurbished equipment meets lockout regulation standards before operators put it to use.
Heavy Equipment
Improvements in heavy equipment also increase safety in industrial environments. Electric forklifts produce fewer emissions than previous models, sparing workers’ lungs, and their narrower bodies and smaller turning radius prevent accidental collisions in crowded warehouses. They’re also quieter, reducing noise pollution. Approximately 18% of industrial workers have a hearing impairment, which lowers their life quality and may increase dementia risk.
Forklifts aren’t the only heavy equipment going electric. Many facilities have begun to outfit their organization with full electric fleets, and even bulldozers are joining this technical revolution. Electric vehicles typically have less complicated engines, leading to fewer malfunctions and opportunities for injuries to occur as crews scramble to find workarounds.
Fall Prevention
Falls from heights are the number one cause of workplace death in the UK and lag behind only transportation and workplace violence in the United States. The term “fall from height” is somewhat misleading, as many of the fatalities involved falls from lower levels, not towering skyscraper beams.
Improved safety technology and procedures work in tandem to prevent falls. For example, requiring harnesses for work involving ladders and scaffolding can reduce the risk of injury if the standing structure falls or an accidental bump sends it tumbling. Providing additional training is another safeguard, as advances in computer technology allow workers to remediate as needed instead of waiting for a single group training to refresh their knowledge.
Worker State of Mind
Improvements in technology won’t go as far as they can in increasing industrial hygiene and safety without the buy-in of the workers running operations. One of the simplest yet most effective methods of bringing up safety scores is to simply slow down. While this mindset goes against the obsession with productivity and metrics typical of many facilities, it’s a rebalancing of modern reality with human ability.
Consider an experiment on seminary students asked to give a speech on “The Good Samaritan” parable. Researchers told one group their participants were already waiting, creating a hurry. The second group was told they had just enough time, and the third was told they had more than enough. Even given the topic of the speech, only 10% of the hurried participants stopped to render aid to someone in need as they crossed campus, while 63% of the unhurried students paused.
Technology has increased overall productivity but has also added responsibilities for workers without a corresponding drop in working hours or adequate time to absorb new information and procedures. Exhaustion and burnout can lead to mistakes that cause injuries and cost lives.
Recent legislation to shorten the average workweek, if passed, could reduce the burnout many feel, improving workplace safety. In the meantime, site leaders can emphasize quality over quantity and stress safety over metrics in determining raises and bonuses to decrease the temptation to cut corners to make numbers.
Improving Industrial Hygiene and Safety
Workplace injuries cost countless lives and disrupt operations. Improving industrial hygiene and safety demonstrates a commitment to a strong, healthy and thriving workforce.
Site owners and supervisors should periodically review the latest updates to improve their operations. Keeping workers safe decreases liability, enhances workflow and results in a happier, more productive environment.
* This article is written by Jack Shaw. Jack is a seasoned automotive industry writer with over six years of experience. As the senior writer for Modded, he combines his passion for vehicles, manufacturing and technology with his expertise to deliver engaging content that resonates with enthusiasts worldwide.