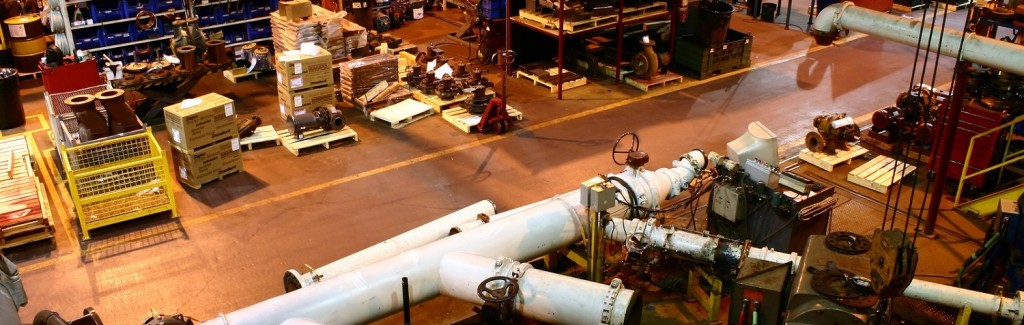
3 Signs Your Successful Manufacturing Scale-Up Could Backfire
Successful manufacturing scale-up can feel like reaching the top of a very tall hill with your product in tow. You’ve struggled to get past the uphill climb and make a place for yourself in your respective market. Once over the crest, it’s all smooth sailing from there, right?
Unfortunately, not quite – not only do all business environments act cyclically, oscillating between peaks and troughs, but the battle to the top can be just as dangerous as the ride “downhill.” Successful manufacturing scale-up at break-neck pace without any control is no success at all. Take back the helm of your manufacturing plant by keeping an eye out for these signs your operations have been knocked into a higher gear as you fast approach a brick wall.
Unprecedented sales
Sales increases can be both a blessing and a curse for unprepared manufacturers undergoing growth. Manufacturing works under a rudimentary supply-and-demand paradigm, so it’s safe to assume if a plant has never experienced a certain level of demand, it cannot consistently supply customers once it hits that mark unless they change their processes to accommodate.
Manufacturers with a close eye on rising sales metrics will have to make a decision before increased demand catches up with their supply capacity. Wrong answers could compromise the quality of their products or customer relations. Either their equipment, processes or a combination of the two cannot produce because they’ve simply never had to before. Acquiring new assets and operators may require a great deal of capital. Processes may be in desperate need of optimization to discover what they’re truly able to accomplish.
Even if manufacturers can temporarily supplement the difference in sales with excess finished products from their inventories accrued over less fortuitous months of labor, it isn’t the same as scaling operations commensurate with increased sales expectations. So, if sales continually test the limits of production capacity even during a scaling up, perhaps it’s time to accelerate proposed changes or realign expectations before it’s too late.
“Large WIP inventories are especially telling and troublesome for manufacturers.”
Inventory increases
Alternatively, an abundance of materials, work-in-progress/process (WIP) or finished inventories present a number of issues for manufacturers, all of which could easily lead to scaling imbalances as their cause. Large WIP inventories are especially telling and troublesome for manufacturers – as the U.S. Census Bureau explains, these unfinished goods drain enterprise cash flow, expend increasing operational costs for their management and count as a goose egg in terms of sales. That last bit is incredibly important – a large WIP inventory may skew operational data and lull decision-makers into a false sense of security vis-a-vis output.
Uncovering the production bottlenecks causing inventory overages only resolves half of the problem. Slowing down throughput, after all, compromises accelerated lead times. Plant managers must be mindful of operational capacity at all stages of production and scale them equally to generate positive results.
Labor uncertainty
Lean practices seek to optimize value-added production steps while reducing or eliminating non-value-added activities, the latter comprising a greater slice of the average manufacturer’s production pie. Ridding production of any and all waste should be secondary, however, to reprogramming the processes causing said waste.
To start, manufacturing plants should focus on smaller, more attainable improvements involving workforce management. For instance, asset utilization and standardization helps remove dissonance from the symphony of lean manufacturing by taking advantage of process steps proven to be the most efficient. As companies willingly accept higher demand, they must simultaneously ensure asset operators and managers adhere to defined protocol for things like materials handling and changeover that preserve quality and long-term productivity.