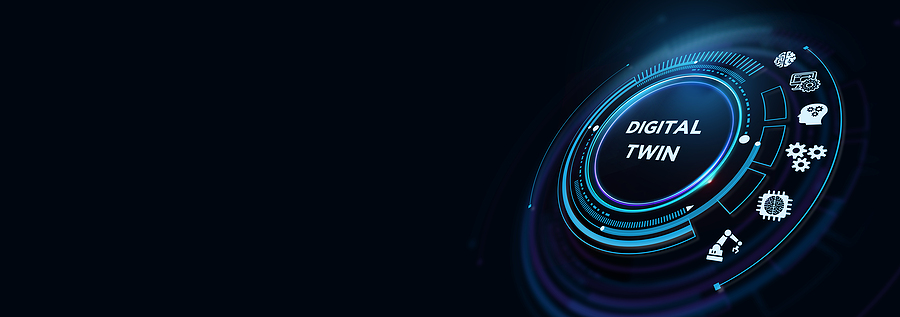
Digital Twins Technology and Their Impact on Manufacturing and Supply Chain Efficiency
It’s no secret that manufacturing and supply chain organizations are constantly in pursuit of a greater degree of efficiency. This is the key to remaining competitive in both increasingly contentious markets.
It’s also no secret that attaining a higher degree of efficiency is harder than it looks. Supply chain organizations have faced disruption from multiple angles, with decentralized distribution, competitors with a higher level of digitalization, and the deglobalization of trade causing them to fall behind. Similarly, manufacturers are attempting to ride out the silver tsunami and the resulting gap in team member experience while doing so.
Automation is already impacting both industries for the better, providing accurate analytics, monitoring and limiting resource expenditure, and removing manual tasks from employee dockets. But newer technological innovations promise to be a massive boon for both industries, optimizing operations, further streamlining decision-making, and enhancing productivity. Digital twins technology offers insights that revolutionize traditional manufacturing and supply chain management – and we’re about to break down exactly how.
What is Digital Twins Technology?
A common misconception that surrounds the topic of digital twins technology is that it’s just another form of 3D modeling – a sensor, a software platform, or a particularly creative application of artificial intelligence (AI). Digital twins are, in fact, none of these things.
Digital twins are an amalgamation of technologies that work in tandem to record, model, and simulate projects in real time. The technologies involved in this process will range according to organizations’ capabilities and needs but often include sensors, augmented reality tools, modeling software, and AI. Far from a simple model, digital twins technology tests, records, and reports key data points to leadership, unlocking agile decision-making on an unprecedented level.
Let’s quickly break down some of the use cases for digital twins in supply chain and manufacturing organizations:
- Predicting future bottlenecks with algorithmic insights: Instead of reacting to bottlenecks as they crop up, digital twins can model manufacturing and supply chain processes proactively. This empowers leaders to make decisions to avoid or break bottlenecks before they occur, instead of manually going back over data after an incident occurs to discover what went wrong.
- Assessing alternate plans of action: Unforeseen variables can always impact your ability to deliver – unless, that is, you have an algorithm on your side that can predict likely pain points and chart alternative plans of action. Digital twins can be used to test the viability of plan Bs and Cs, allowing you to react quickly when disaster strikes.
- Organization-wide transparency: When you create a digital twin, it stores its information in a widely accessible single source of truth, allowing stakeholders across the organization to see and understand what’s going on at every level.
Manufacturers in particular will see a massive value-add from digital twins technology, as it can be used to:
- Develop and virtually test stronger concrete;
- Improve yield sizes and limit defects in steel production;
- Accurately estimate costs and inventory;
- Design and create environmentally resistant structures.
While it’s not the most buzzed about technological innovation on the market, digital twins are certainly one of the more useful types of technology for manufacturers and supply chain organizations.
Digital Twins, Your Network, and Expanding Your Infrastructure
Digital twinning also has implications for your network, especially if you’ve already made the switch from copper to fiber. Employing digital twins technology necessitates a high capacity for data transference, as a large quantity of data will be consistently transferred to your single source of truth. While switching from copper to fiber can somewhat fill that need, depending on your network’s capacity and the quality of the components within, you may find that your current network doesn’t adequately support your data-transmitting needs.
Taking the step to convert to a dark fiber network is one possible solution, as dark fiber networks grant a robust, scalable network infrastructure that is entirely customizable according to need. Organizations that need to expand their bandwidth while also maintaining network security and consistent uptime may consider switching to dark fiber, as it is a high-capacity, consumer-controlled network that can effectively replace inferior infrastructure overnight.
Another option is actually using digital twins technology to replicate and reinforce your network. Creating a network digital twin allows you to connect tasks with network performance, granting you control over all facets of your network’s lifecycle. Similarly to how digital twinning allows you to identify bottlenecks and potential impediments to swift service throughout your operations, network digital twinning replicates those benefits for your network.
Either option will allow you to boost your network’s performance while also granting you a greater degree of visibility into and control over said network. This is key when using a technology like digital twins, which can consume quite a bit of bandwidth, as it allows you to reap the benefits of this technology without any unintended consequences.
Digital twins technology can empower manufacturers and supply chain organizations to drive efficiency, regaining a competitive edge in markets overrun with disruptions. With the right solution and the infrastructure to support it, you’ll find efficiency, customer satisfaction, and profits spike.
*This article is written by Ainsley Lawrence. View more of Ainsley’s articles here.