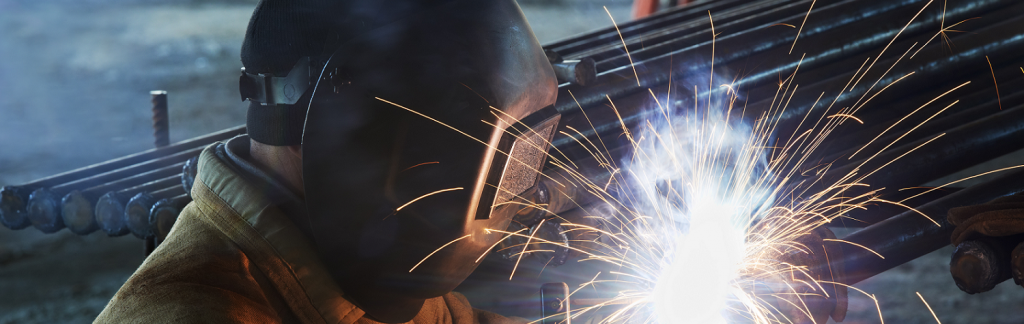
Make Time for Plant and Asset Maintenance
Having a proper asset maintenance plan in place is essential for every manufacturing plant. However, sometimes a major impediment to getting maintenance done is that production is ongoing 90% of the time. It is always better to be proactive about asset maintenance instead of having it be a reactionary activity, but in all situations, finding the time to assess and improve asset condition is the most important consideration. This post aims to help you identify ways to work on equipment without incurring extra unnecessary downtime.
Operators and maintenance staff must work together
Plant Engineering suggested that one of the most important times to do asset maintenance work is during changeovers. If your plant needs to switch from one product to another, or change the dimensions of production, the specific time it takes to do a changeover may be different, but with proper scheduling and flexibility, you will be able to create a window of opportunity to get in there and do the work. One way to free up staff and allow for the needed flexibility is to create a partnership between the operators and maintenance groups, yet have each group focus solely on their job and avoid overlap. Sometimes, maintenance staff find themselves performing operations tasks, which can affect overall productivity. Making sure operations work goes to the operators will free up maintenance staff do their job when those windows of opportunity open up.
“Preventative maintenance is never meant to hinder operations.”
Maintenance staff and operators must also work together, because if they don’t, downtime windows become sporadic and asset maintenance is delayed, which in turn affects production negatively. If the two groups work in partnership, operators will utilize equipment based on established procedures, complete their work efficiently, and honor their production scheduled downtimes without delay. While it may seem obvious, maintenance and operators must get their work done correctly. A plant will only be able to ensure timely operations when every aspect of the job is accounted for, such as resources and supplies being available at the asset location when it is time to do the work.
Preventative maintenance is meant to add-value, not detract
According to Plant Engineering, preventative asset maintenance, which involves maintaining equipment before failure occurs, is never meant to hinder operations. It falls under the responsibility of the maintenance department to ensure that equipment is not shut down unnecessarily for preventative maintenance work. Approximately 40% of preventative tasks do not uncover asset failures, so planning them at the wrong time is really a no value-added activity. That is not to say that preventative work could not save an operations from unexpected delays and shutdowns, but smart planning goes a long way.
Asset maintenance should be prioritized into the production schedule
A proven method for limiting downtime related to asset maintenance work is to conduct inspections that do not require assets to be powered down, otherwise known as predictive maintenance. Vibration and infrared analysis, as well as flow, pressure, temperature, and statistical analysis from the quality department can provide maintenance staff with a good idea about the condition of assets without having to stop everything. ReliablePlant explained that predictive maintenance must be done while the equipment is in normal operation, and that it helps find defects that would normally not be found through previously tried inspections methods. Manufacturers use new technologies to accurately examine the condition of assets and determine the presence of defects. Vibration analysis is the most common example of these condition-monitoring predictive technologies.
Preventive and preventative asset maintenance are all about avoiding hindering operations. That is why being proactive is so important. Reactionary maintenance slows down or delays production, and reduces windows of opportunity to fix and optimize assets. Alternatively, if an organization is proactive about its maintenance work, things run a lot more smoothly. Using labor effectively means that everyone gets to do their scheduled work.
Ultimately, the best opportunities for asset maintenance work are the result of planning, scheduling, and coordination. Instead of waiting for downtime windows to appear, supervisors have the responsibility of scheduling jobs carefully so that when downtime appears, it is expected and used the right way.