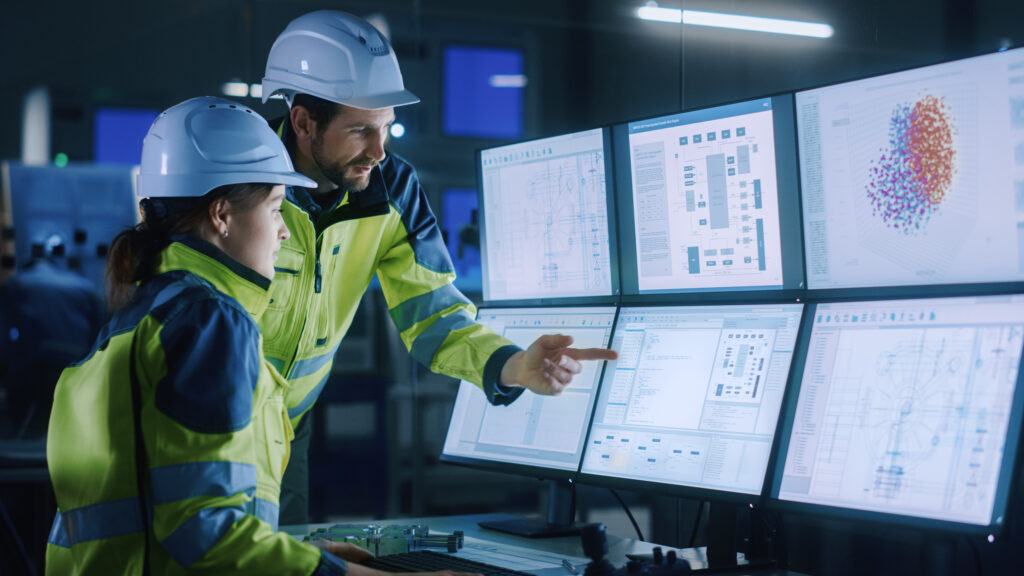
Leveraging the Power of AI and IoT in your Management Operating System
By integrating their Management Operating Systems (MOS) with AI and IoT, mining and metals companies can significantly enhance their operational capabilities, leading to better asset management, increased productivity, and ultimately, improved financial performance.
Utilizing IoT devices, such as sensors and connected equipment, to continuously collect data on various aspects of their operations, including equipment performance, environmental conditions, and production metrics, this real-time data is fed into the MOS, providing a comprehensive and up-to-date view of operations. The collected data is then analyzed by AI algorithms within the MOS to generate insights, identify patterns, and predict outcomes, allowing for proactive management of assets and operations, such as predicting equipment failures or optimizing production schedules.
A key aspect of any MOS is to assist management in decision making. Integrating AI with MOS enables real-time decision support, where AI provides recommendations or automates decision-making processes based on the analysis of IoT data. This helps managers make more informed decisions quickly, improving responsiveness to changing conditions. Additionally, AI allows the MOS to simulate different operational scenarios and predict their outcomes. This capability helps managers evaluate the potential impact of different decisions before implementing them, reducing risks and optimizing outcomes.
By focusing on operational efficiency, AI models integrated into the MOS can optimize processes in real-time by adjusting operational parameters based on current conditions and historical data, leading to improvements in ore and metal recovery, energy efficiency, and overall productivity. AI can also be used to analyze data on resource usage and availability, helping the MOS to optimize the allocation of resources such as labor, equipment, and materials, leading to cost savings and improved operational efficiency.
When approaching enterprise asset management and predictive maintenance models, integrating AI and IoT with the MOS, companies can enhance their predictive maintenance capabilities. AI algorithms analyze sensor data from IoT devices to predict when maintenance is needed, helping to prevent unexpected equipment failures and reduce downtime. This assists the MOS to automatically schedule maintenance activities based on AI predictions, ensuring that maintenance is performed only when necessary and that it is coordinated with other operational activities.
The use IoT and AI integration helps the MOS to optimize inventory levels by predicting demand for spare parts and materials based on operational data, thus reducing inventory costs and ensuring that critical components are available when needed. By having AI analyze data across the supply chain, assisting the MOS to optimize logistics, reduce lead times, and minimize costs associated with the procurement and transportation of materials.
Integrating Management Operating Systems with AI and IoT in the mining and metals industry offers substantial benefits, but it also comes with several challenges and potential pitfalls.
USC partners with your organization and coaches your people to significantly impact performance outcomes and accelerate Operational Excellence
For more than 55 years, USC has been working with clients to address the challenges and avoid the pitfalls when developing, enhancing and deploying their management operating systems.
As technology enablers, like AI and IoT, are deployed, we help clients to address the challenges through careful planning and a strong focus on change management, including employee involvement. By proactively identifying and mitigating the pitfalls, mining and metal companies can successfully integrate AI and IoT with their MOS, unlocking the full potential of these technologies for improved asset management and operational efficiency.
Integrating AI and IoT into MOS often requires close coordination across different departments, such as IT, operations, and maintenance. Misalignment or lack of communication between these departments can lead to project delays and failures. The complexity of integrating AI and IoT, projects can often experience timeline and budget overruns. Effective project management is critical to keep the implementation on track and within budget.
Mining and metal operations often have data scattered across different systems and departments. Integrating this data into a unified MOS that can effectively leverage AI and IoT is challenging, particularly if the data is stored in incompatible formats or is not standardized. AI systems require high-quality, accurate data to function effectively. Inconsistent, incomplete, or inaccurate data can lead to poor AI performance, resulting in unreliable predictions or insights. Ensuring that data from IoT devices is processed in real-time is crucial for effective AI-driven decision-making. However, high latency in data transmission or processing can lead to delays, reducing the effectiveness of AI in making timely decisions.
Many companies often face a skills gap when it comes to AI, IoT, and data analytics. There may be a shortage of in-house expertise required to manage and maintain these advanced technologies effectively, so having a partner can assist in compressing the time it normally takes cleanse data and align MOS processes. Employees accustomed to traditional methods may resist adopting new technologies, especially if they perceive AI and IoT as threatening their jobs or making their roles redundant. Effective change management and training programs are essential to address this issue.
Companies that have integrated their Management Operating Systems with AI and IoT are experiencing several quantifiable benefits across various aspects of their operations. These benefits are often measurable in terms of improved safety (30-50% reduction in safety incidents), cost savings (10-40% reduction in maintenance costs), and an increased productivity (5-15% increase in productivity and 10-20% improvement in operating efficiency), just to name a few. By leveraging these technologies effectively, mining and metal companies can achieve substantial improvements across their entire value chain.
USC helps you tackle key challenges
- Ensure the right resources are at the right place to minimize lost time – enabling safe and disciplined execution
- Optimize mine planning and scheduling across all planning horizons – delivering detailed and accurate plans
- Identify potential roadblocks proactively during mine planning and solve complexity during the planning process
- Control quality of work at the point of execution by identifying off specification and enabling in-shift correction
- Enhance your ability to cluster & centralize scarce human expertise, allowing all sites to benefit from their expertise
Do you want to understand how a MOS can integrate your mine and operational planning, while helping you to safely increase performance site wide? Contact us today.