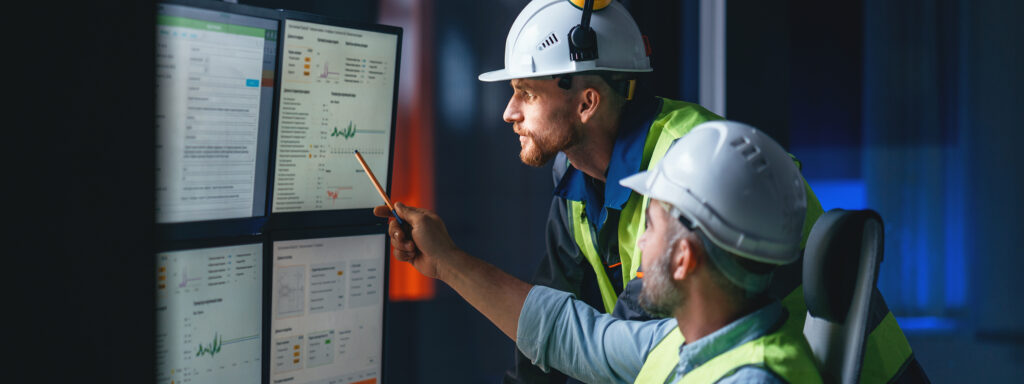
Managing the Unexpected: What it Takes to be a High Reliability Organization
Have you heard of a High Reliability Organization? The concept has been out there for several decades but it’s taking center stage again now. Let’s delve into what a High Reliability Organization is, why this concept is coming to the forefront again, and whether you should explore implementing the principles in your own organization.
Simply put, a High Reliability Organization (HRO) is a company that has a solid operating system of execution in place that emphasizes safety and strives to minimize risk across the business.
We’re talking about complex or hazardous industries like nuclear power, the Navy and other branches of the military, air traffic controllers and the mining industry.
The idea behind HRO is a basic one. Expect the unexpected. An HRO creates a number of operational systems and ways of working that promote consistency and keep the focus on achieving company goals while avoiding major errors. These systems not only make the HRO more nimble, responsive and functional than a non-HRO competitor, but they also deliver more efficiency and most importantly, safety.
Why being an HRO is vital today
The concept of HROs has long been a method of ensuring safety in hazardous industries, but it’s becoming more relevant today in mining and other industries because of a perfect storm of circumstances. The marketplace is changing dynamically. Shifting sands don’t exactly make for solid foundations. A few things happening now:
Natural disasters. We seem to be in a period of increased earthquakes, “storms of the century,” droughts, volcanic eruptions and more. It makes facilities vulnerable to disruption.
Cyber attacks. Another vulnerability. As the industry gets more dependent on technology, the vulnerability to hacking of control systems ratchets up.
Boomer retirements. The impact of this can’t be overstated. Baby Boomers make up nearly a third of the entire U.S. workforce. The U.S. Census Bureau projects that 4.4 million people will turn 65 (retirement age) every year from now through 2027. During the period from 2022 to 2030, 75 million Americans are expected to retire. Called the Silver Tsunami or the Great Retirement, it is the largest surge of retirement age Americans in history.
Loss of institutional knowledge. Those retiring Boomers represent your most experienced, knowledgeable workers. These are the people who have gotten the job done, and done safely, for decades. All of that know-how will walk out the door with them.
Lack of skilled workers. It’s a real problem for many industries, including mining. Talent acquisition and training is on the top of the list of concerns for mining CEOs, because when those Boomers retire, the mining industry needs skilled, experienced people to keep the operation moving.
Doing more with less. In this economy, it is incumbent on companies to do more with less, cut costs, trim staff and extend the lifecycle of equipment while also investing in AI.
All of these things are coalescing into a situation in which the mining industry is experiencing a great potential for increased risk. It’s easy to see why. Experienced people retiring en masse, less experienced people taking up the mantle but not having that deep institutional knowledge you just can’t get in a training course, and the need for constant cost cutting – it all adds up to risk.
And when you’re talking about operations in a mine, risk doesn’t just mean business disruption. It means people’s lives.
HRO core principles
It’s about more than just focusing more on safety. The core principles of HROs, specifically in the mining industry, include:
Preoccupation with failure. It’s vital to anticipate the potential for failure and put measures in place to stop a problem before it starts. Emergency response training, regular equipment inspections and maintenance, failsafe protocols. The goal here is to be ready to spring into action, to have that training kick in, when a potentially disastrous situation arises.
Sensitivity to operations. Everyone’s eyes need to be open, all the time. Much like the “see something, say something” campaign at airports, it means developing a culture of awareness among workers on the front lines and in the front office. Identifying processes and ways of working that can be optimized; or potential issues or risks that could lead to disruption in the future.
Resilience. The ability to roll with the punches. Redundancies need to be built in. Clear protocols for disruptions or sudden change responses need to be automatic.
Shared understandings. Everyone in the organization needs a shared understanding of HRO principles, the role they themselves play, and are operating with the same road map.
Respect hard-earned expertise. Those Boomers who are retiring? They know how to get the job done. They’re carrying your organization’s institutional knowledge – the part of the job that can’t be taught in a training class. This knowledge needs to be respected, especially when decisions get made.
Why being an HRO matters
Why should mines focus on high reliability? Here are a few of the benefits.
Safety. Since the first canary went down a coal mine, this industry has been implementing safety protocols. It can be dangerous for people working in a mine, period. Anticipating risks and putting safety protocols in place will save lives and reduce accidents and injuries.
Efficiency. The focus on asset management minimizes unscheduled downtime and process disruptions, while getting everyone on the same page streamlines operations. It all works together to increase efficiency.
Equipment lifespan. One of the challenges today is doing more with less, and that means keeping aging equipment on the job. The regular maintenance and inspection of equipment adds to its lifespan.
Hiring and retention. That lack of skilled workers? It’s causing stiff competition for the skilled workers who are out there. Being a High Reliability Organization shows new recruits that you’re committed to safety, value their contributions and knowledge. In short, it’s a powerful recruiting tool.
How USC can help: Anticipate the Unexpected
One of the most vital components of transforming into an HRO is the integration of a solid Management Operating System that breaks down siloes between areas of the organization like engineering, maintenance, procurement and operations.
The end goal: Constantly anticipating the unexpected and executing in a consistent manner.
When USC begins the process, we start with an assessment of current operations. Then we do a deep dive. Some, but by no means all, of the areas we focus on:
Identify operational disconnects. Is everyone on the same page to execute the plan? Are priorities between departments aligned? Has production prepared access to equipment to be maintained? Are shift managers setting work expectations in the same way? How are variances to the plan addressed?
Close the gaps. This is about breaking down silos and getting everyone looking in the same direction, working in the same way, and managing departmental operations with a common vision.
Build in buy in. Like many projects that require change at all levels of the organization, this requires buy in from the corner office to the depths of the mine. In many instances, this requires a culture change, with people being used to doing the job one way now asked to shift their operations.
Make it transparent. Change can’t be foisted on people in a vacuum. The new initiative on transforming into an HRO should be a full team effort, with full transparency from the top.
Implement measures and metrics. It’s also important to implement accurate measurements and targets. Still, one assessment rises above all others: addressing overall organizational health. Organizational health is the softer side of the business that is frequently dismissed because it is often viewed as both difficult to revamp and even more difficult to measure.
HRO Checklist
Do you need to focus on High Reliability Organization? Here’s a quick checklist to help you decide.
- Do you have an organization-wide sense of susceptibility to the unexpected?
- Does everyone feel accountable for organizational reliability?
- Are your leaders paying as much attention to managing unexpected events as they are to achieving formal organization goals?
- Do people at all levels of your organization value quality?
- Have you identified how your activities could potentially harm your organization, employees, other stakeholders and the environment at large?
- Do you pay attention to when and why your employees or other stakeholders might feel angry or disenfranchised?
- Do you have widespread agreement among the organization’s members on what shouldn’t go wrong?
Transforming into a High Reliability Organization doesn’t happen overnight, and many challenges exist in the process. It requires a cultural shift, training for both workers and management, investing in protocols, and commitment from the top.
But, in today’s volatile world, it’s a solid framework the mining industry can use to ramp up safety, increase efficiency, minimize risks and anticipate the unexpected. For help setting up your HRO, contact USC Consulting Group today.