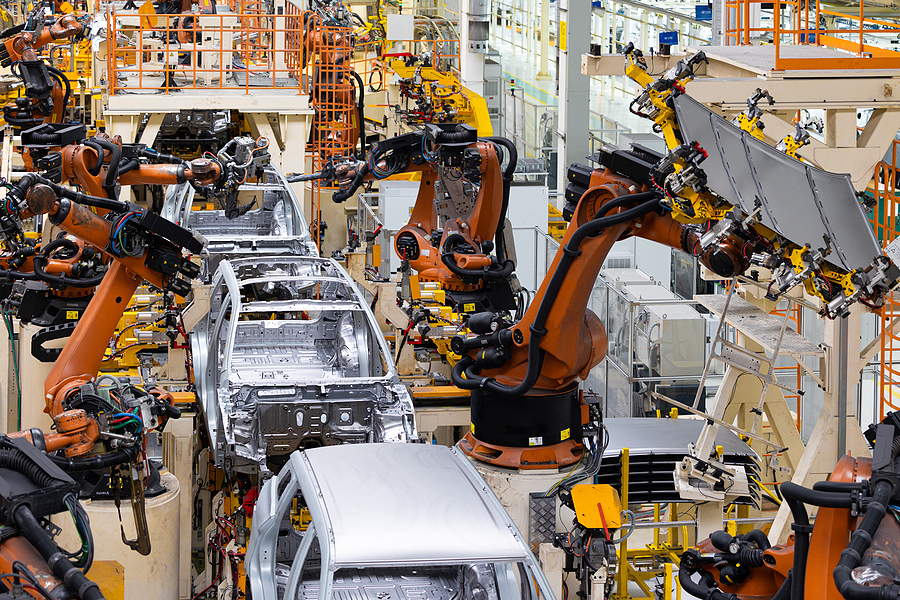
Robots, Cobots and Their Impact on Automotive Assembly
Industrial and collaborative robots have had a tremendous impact on the automotive industry, changing the standards for production, quality control and safety. In assembly, they have permanently shifted how workers and plant managers interact with machinery.
The State of Robots and Cobots in the Automotive Sector
Industrial and collaborative robots are foundational to the automotive sector. While they can seem similar at first glance, the two have fundamental differences. Their specialized designs and applications give them each a unique place in the industry.
Of course, industrial robots came first and have become the standard. They brought tremendous value to operations, leading to the automotive industry becoming one of the most mechanized industries. These heavy-duty machines outperform their human counterparts in tasks like material handling and part insertion.
Collaborative robots — often referred to as cobots — are meant to act as support rather than replacements. Their place on the factory floor is directly next to workers since they’re much safer than their industrial counterparts. They excel at precision-based tasks like bin picking, screw-driving and product dispensing.
Although traditional industrial robots have long been the industry standard, cobots have quickly grown in popularity. In the automotive sector alone, their combined global sales value was roughly 3.8 billion in 2022. Both technologies have significantly impacted worker safety, assembly efficiency and production yields.
The Rise of Robots and Cobots
In the automotive sector, the popularity of robotics is plain to see. Industrial robot installation increased by 31% between 2020 and 2021 alone, demonstrating how it has room to expand despite already being an industry staple. What makes this technology so highly sought-after?
Industrial robots have existed for ages and they are reliable. They are what’s known as mature technology, meaning their user base has eliminated most of their faults over the years. This consistency is crucial in the automotive sector, given the complex nature of the assembly line.
Cobots have quickly reached the popularity of industrial robots because they can adapt rapidly and outperform their counterpart regarding safety. Instead of being trapped in cages far away from humans, they work alongside employees on the factory floor. They open up many new opportunities for broadened automation and efficiency improvements.
Although most robot and cobot applications involve automation, worker safety and production capacity improvements have also proven significant. Humans no longer have to lift obscenely heavy objects or work in intense heat because their role requires it. Instead, the machines take over the dirty, complex and challenging tasks.
The Role of Robotics in Automotive Assembly
Robots and cobots have made a substantial impact on automotive assembly. Many factory floors now have humans and machinery working alongside each other instead of separately. Because of this development, plant managers have been able to automate duties they never previously could’ve.
Typically, monotonous manual work takes up most of the workweek. Across various industries, more than 40% of employees spend the majority of their workday on repetitive duties. Although the widespread adoption of industrial robotics has made the automotive sector somewhat of an outlier in this sense, there are still plenty of jobs left to partially or fully automate.
Even if demand changes, manufacturers can use cobots to continue automating whatever they need to. Since these machines are reprogrammable, their duties can adjust depending on a plant’s needs. For example, they could easily switch from bin picking to sealant dispensing to make up for an unexpected job vacancy or a sudden shift in consumer expectations.
Robots also protect the automotive industry from common pain points like labor shortages, human error and assembly line bottlenecks. This development is clearly visible with cobots, considering plant managers can support any manual duty with them and reprogram them at will.
These machines can safeguard production rates even in unforeseen circumstances. The COVID-19 pandemic impacted the sector significantly, causing unprecedented downtime. More than 50% of automotive companies experienced substantial disruption during this period. If facilities had a combination of robots and cobots, they likely could’ve avoided the effects of the sudden labor shortage.
The Impact of Robotics in Automotive Assembly
With robots and cobots, plant managers can fully or partially automate virtually any position in the assembly line. As a result, they can pursue highly-trained employees with more specialized skills. This development might eventually give rise to product quality improvements.
Robotics has also made labor condition improvements possible. In the past, workers had to do every hazardous or strenuous task by hand. Even with the introduction of industrial robots, they still risked injury and exhaustion. The development of cobots allowed them to work alongside each other.
Most importantly, robotics has vastly improved product yields. While Industrial robots are an industry staple, their large size, operational skill requirements and ability to injure workers hold them back. Cobots closed the gap, allowing plant managers to automate what was left.
Robotics Innovate Automotive Assembly
While cobots have quickly risen in popularity, traditional industrial robots are still vital parts of automotive assembly because they excel in heavy-duty tasks. A combination of both helps maximize efficiency, worker safety and product yields.
*This article is written by Jack Shaw. Jack is a seasoned automotive industry writer with over six years of experience. As the senior writer for Modded, he combines his passion for vehicles, manufacturing and technology with his expertise to deliver engaging content that resonates with enthusiasts worldwide.