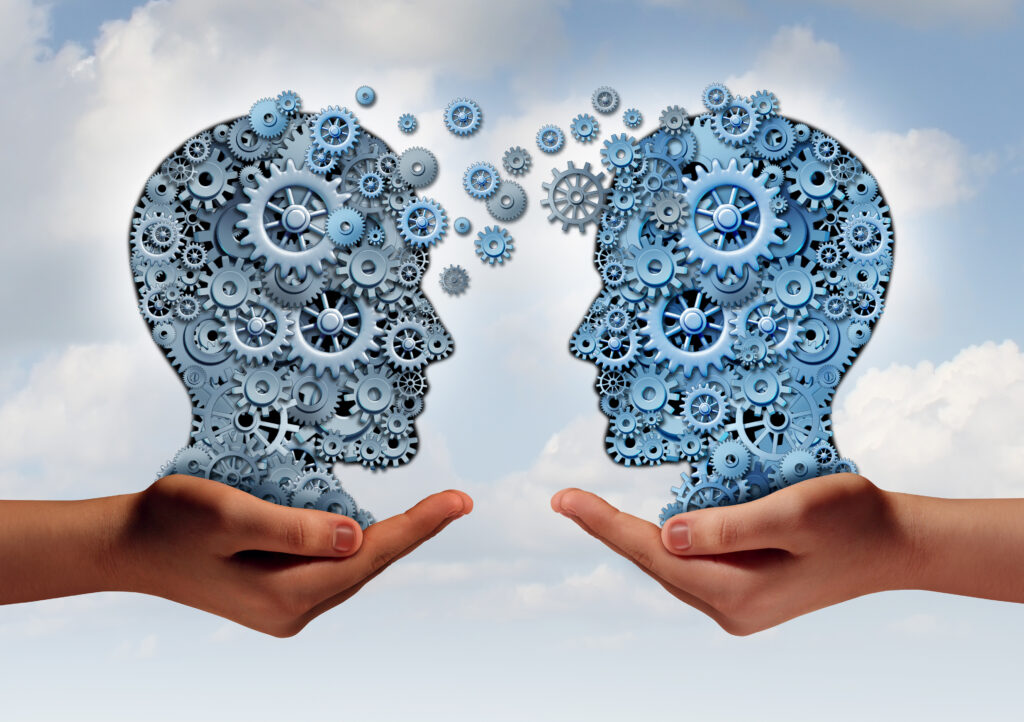
5 Ways to Address the Manufacturing Industry Skills Gap
In today’s manufacturing industry, the “skills gap” is one of most pressing and talked about issues. Last year, many major media outlets covered the issue extensively, demonstrating its importance. Manufacturing requires a high level of technical proficiency and encompasses a wide range of competencies. At a time when the industry is witnessing the retirement of the largest percentage of its workforce, the lack of skill and technical knowledge of new workers is troubling.
The “skills gap” is a major problem in manufacturing today
The oldest baby boomers turned 65 in 2011, and each successive year, approximately 10,000 more seasoned workers will retire, according to the Pew Research Center. Fortunately, manufacturers can enact a few strategies to offset the impending brain drain that is taking place. IndustryWeek reported on a Pennsylvania chemical producer that faced the problem of having 150 skilled labor jobs open and unfilled. Ranging from welders to mechanical engineering technicians, the company struggled to hire qualified staff. The unfilled positions represented 38 percent of the 400 skilled-worker positions open at any point in time. The CEO of the company explained why it was so difficult to fill positions.
“In some cases [a position] takes as long as a year to fill because of a mismatch of skills — either in the skills area we need or in the geographic area where we need that skill,” said the CEO , according to the news source.
Lean methodologies will alleviate the skills gap problem
According to Reliable Plant, the lean manufacturing philosophy does great things for improving training practices and can help preserve expertise in a facility. When lean methodologies are used in training programs, the benefit is that a facility is able to make progress in multiple areas at once and keep best practices at the forefront. Instead of training employees and working toward continuous improvement in a silo-ed fashion, training should be ongoing and encompass continuous improvement principles to promote greater delivery and material development.
Accordingly, here are 5 ways companies can work on developing highly skilled employees and closing the skills gap:
- Implement Continuous Improvement
One of the best ways manufacturing companies can establish lean operations is to always improve upon existing processes. As an organization commits to developing best practices on an ongoing basis, that effort should involve constant training of employees. Plant improvements must always be reflected in process documents and then incorporated into employee work routines. Companies should motivate staff to collect data, analyze information, and raise job performance to the next level based on the findings. The most important thing to remember is to always improve. If a manufacturing company is able to do this, they will find less of a skills gap among their ranks because project managers will continually educate their teams on the latest amendment to their routines.
“The best thing an organization can do is facilitate the sharing of information.”
- Encourage staff communication
Companies that encourage their staff members to communicate about work issues, across departments and geographies, will be able to retain a greater amount of valuable tribal knowledge, should seasoned workers suddenly leave. The best thing an organization can do to avoid a skills gap is to facilitate the sharing of information, so when experts leave, their information will have already been passed down to the next generation. Also, for training purposes, giving workers a voice results in more active training sessions and higher levels of engagement. That enthusiasm will carry through to the plant floor, where the workers can turn knowledge into results. The more actively a company involves employees in training, the more effective the results are. - Focus on customer satisfaction
Interestingly, an effective strategy for raising technical expertise at a facility is making its training program very customer-centric. The lean manufacturing philosophy stresses the importance of creating value for the customer. Organizations can train their employees to think about the end result, regardless of their position. Someone on the assembly line with an understanding of what the customer ultimately wants to see is in a better position to make the right decisions. Likewise, managers can help their teams see what their individual skills gap is, and what they need to develop to excel in their job and create good products. It is important to remember that training employees to think of the customer is a way of putting his or her money to good use. Plant managers are also more likely to pass on their expertise when they understand how that act will benefit the customer in the long run.
Ongoing training programs are essential in the manufacturing industry.
- Address the reality on the ground
Often, plant managers will give directives to facility staff without getting involved in the day-to-day details those directives might entail. This is not an effective way to manage a plant and it is essential that managers take the time to get to know workers, listen to their feedback, and incorporate their opinions into company plans. When implementing a training program, management will benefit from this approach because they will have a chance to watch staff members perform their job tasks, which facilitates the development of better training materials. This approach is also helpful down the road, as managers will need to check to see if employees are putting their training to good use – preventing a skills gap. - Develop and maintain proper documentation
The importance of updating standard operating procedures in a facility cannot be emphasized enough. Lean managers not only use process documents to guide their operations and decision-making, but they also use visual aids for brainstorming and conceptualizing projects. One of the best ways to understand a concept is to use diagrams and process maps. Manufacturers should use work flow maps, diagram their production processes, and always refer to SOPs. When a facility operates in this way, training is greatly enhanced as the company culture is already based on doing things by the book and the skills gap is more easily avoided. The effort required to change the way something is done is much less if it can be addressed simply by amending process documents. If a facility does not use documentation with vigilance, introducing a new process can involve hours of explanation and unnecessary work.
Ultimately, learning and development in the manufacturing industry is crucial. Given the aforementioned skills gap, as well as the proven benefit of making training a regular part of everyday operations, lean methodologies should be a part of every organization’s approach for managing their operations.