-
Subscribe to Blog:
SEARCH THE BLOG
CATEGORIES
- Aerospace
- Asset Maintenance
- Automotive
- Blog
- Building Products
- Case Studies
- Chemical Processing
- Consulting
- Food & Beverage
- Forestry Products
- Hospitals & Healthcare
- Knowledge Transfer
- Lean Manufacturing
- Life Sciences
- Logistics
- Manufacturing
- Material Utilization
- Metals
- Mining
- News
- Office Politics
- Oil & Gas
- Plastics
- Private Equity
- Process Improvement
- Project Management
- Spend Management
- Supply Chain
- Uncategorized
- Utilities
- Whitepapers
BLOG ARCHIVES
- July 2025 (1)
- June 2025 (4)
- May 2025 (1)
- April 2025 (1)
- March 2025 (1)
- February 2025 (4)
- January 2025 (4)
- December 2024 (4)
- November 2024 (2)
- October 2024 (6)
- September 2024 (5)
- August 2024 (5)
- July 2024 (6)
- June 2024 (3)
- May 2024 (3)
- April 2024 (4)
- March 2024 (3)
- February 2024 (4)
- January 2024 (5)
- December 2023 (2)
- November 2023 (1)
- October 2023 (6)
- September 2023 (3)
- August 2023 (4)
- July 2023 (2)
- June 2023 (3)
- May 2023 (7)
- April 2023 (3)
- March 2023 (3)
- February 2023 (5)
- January 2023 (6)
- December 2022 (2)
- November 2022 (5)
- October 2022 (5)
- September 2022 (5)
- August 2022 (6)
- July 2022 (3)
- June 2022 (4)
- May 2022 (5)
- April 2022 (3)
- March 2022 (5)
- February 2022 (4)
- January 2022 (7)
- December 2021 (3)
- November 2021 (5)
- October 2021 (3)
- September 2021 (2)
- August 2021 (6)
- July 2021 (2)
- June 2021 (10)
- May 2021 (4)
- April 2021 (5)
- March 2021 (5)
- February 2021 (3)
- January 2021 (4)
- December 2020 (3)
- November 2020 (3)
- October 2020 (3)
- September 2020 (3)
- August 2020 (4)
- July 2020 (3)
- June 2020 (5)
- May 2020 (3)
- April 2020 (3)
- March 2020 (4)
- February 2020 (4)
- January 2020 (4)
- December 2019 (3)
- November 2019 (2)
- October 2019 (4)
- September 2019 (2)
- August 2019 (4)
- July 2019 (3)
- June 2019 (4)
- May 2019 (2)
- April 2019 (4)
- March 2019 (4)
- February 2019 (5)
- January 2019 (5)
- December 2018 (2)
- November 2018 (2)
- October 2018 (5)
- September 2018 (4)
- August 2018 (3)
- July 2018 (2)
- June 2018 (4)
- May 2018 (3)
- April 2018 (3)
- March 2018 (2)
- February 2018 (2)
- January 2018 (1)
- December 2017 (1)
- November 2017 (2)
- October 2017 (2)
- September 2017 (1)
- August 2017 (2)
- July 2017 (2)
- June 2017 (1)
- April 2017 (3)
- March 2017 (3)
- February 2017 (2)
- January 2017 (2)
- December 2016 (2)
- November 2016 (4)
- October 2016 (4)
- September 2016 (3)
- August 2016 (6)
- July 2016 (4)
- June 2016 (4)
- May 2016 (1)
- April 2016 (3)
- March 2016 (4)
- February 2016 (2)
- January 2016 (4)
- December 2015 (3)
- November 2015 (3)
- October 2015 (1)
- September 2015 (1)
- August 2015 (4)
- July 2015 (6)
- June 2015 (4)
- May 2015 (7)
- April 2015 (6)
- March 2015 (6)
- February 2015 (4)
- January 2015 (3)
CONNECT WITH US
Tag Archives: sustainability
Mining companies are embracing operational excellence to remain competitive, profitable, and sustainable in a challenging and rapidly evolving industry.
Operational Excellence is the cultural and process foundation that enables mining companies to unlock real value. Companies that operate without a strong Operational Excellence mindset often struggle with performance improvement, change adoption and sustainability.
Largely driven by efforts to improve safety, increase operational efficiency, reduce downtime, improve cost performance, meet sustainability goals, and manage operational risks, many companies already have or are deploying an Operational Excellence framework of practices, tools, and behaviors. It combines process discipline with people engagement and data-driven decision-making.
The benefits of Operational Excellence
Mining companies that embrace Operational Excellence are realizing a range of measurable, quantifiable benefits across safety, cost, productivity, and ESG metrics. These gains often begin within months and scale significantly with sustained execution and digital integration.
There are many real-world examples of how mining companies are applying Operational Excellence in their operations and linking with the use of today’s developing technologies:
- When addressing equipment reliability issues, BHP deployed predictive analytics across its mobile equipment fleet, and reduced unplanned maintenance by up to 25%, thus improving asset availability, and saving millions in downtime.
- Rio Tinto leveraged bottle-neck analysis, short interval controls and Lean Six Sigma practices to address process optimization issues and used digital twins at its processing plants to optimize throughput and reduce energy use, while boosting recovery rates by 2–5%.
- After analyzing fleet performance and dispatch efficiency issues with continuous improvement kaizens and visual management/KPI dashboards, Newmont leveraged an integrated Operational Excellence dispatch system using AI that improved truck utilization and increased daily production by 7–10% at certain sites.
- An asset of Teck Resources used Operations Excellence processes and tools to better understand energy use through waste identification, energy audits and cross-functional teams to deploy AI-driven energy optimization, cut energy consumption by 9%, which contributed to both cost savings and ESG targets.
As with any performance change, organizations will vary focus as they mature. Early-stage Operations Excellence organizations focus on fixing the basics — stabilizing performance and embedding a management rhythm; while mature Operations Excellence organizations deliver strategic advantage — agile, data-driven, low-cost, and high-performing operations.
The bottom-line, Operational Excellence is the cultural and process foundation that enables mining companies to unlock real value. Companies that digitize without a strong Operational Excellence mindset often struggle with adoption and sustainability.
How to accelerate Operational Excellence maturity
USC Consulting Group is an operations management consulting firm that partners with organizations and coaches your people to significantly impact performance outcomes and accelerate Operational Excellence maturity.
USC brings a tailored, structured, and disciplined methodology, along with a range of tools and techniques we apply collaboratively with our client’s personnel. We work with our clients to find full operating potential and unlock the hidden value through Operational Excellence.
We identify waste, redundancies, and ineffective processes, and then rapidly recover the prioritized opportunities, and convert them to improvements in performance and operating profit. Further, our people embed with client teams to develop, enhance, prototype, validate and implement operational excellence strategies to drive, sustain and perpetuate improvements in mining operations, while changing how plans, schedules, and work is executed.
In short, USC implements measurable, sustainable changes that drive operational performance and financial improvements.
USC clients experience measurable operational and financial results that significantly improve both the efficiency and profitability of their operations such as:
- Enhanced Safety Performance (10–40% reduction in injury rates)
- Increased Production Throughput (5–15% increase in ore mined or tonnes processed per day, reductions in production losses, downtime, delays, and rework)
- Higher Recovery and Yield (2–5% increase in mineral recovery through process optimization)
- Improved Equipment Reliability & Availability (10–25% reduction in unplanned downtime; 5–15% increase in OEE)
- Lower Operating Costs (8–20% reduction in cost per tonne; reductions in overtime, fuel usage, maintenance, and material waste)
- Reduced Variability (Up to 50% reduction in cycle time variance in drilling, hauling, and milling)
.
USC Helps You Tackle Key Challenges
- Optimize production strategies and increase mine throughput and mill recovery
- Predict asset integrity and reliability needs and improve time on tools and equipment availability
- Improve integrated mine planning across all time horizons to strategically & tactically impact performance
- Mitigate risks through stronger stakeholder partnerships, while removing redundancies in the supply chain
- Overcome cultural and organizational communication issues, while ensuring quality expectations
Do you want to understand how prepared your company is to build a performance focused culture that drives sustainable results based on an Operational Excellence foundation?
Want to find out more about how USC can help you unlock the hidden value lurking in your mining operations? Contact us today.
Labor shortages, supply chain disruption, and technological change have been cause for concern for executives in the manufacturing industry the last few years. As 2024 draws to a close, business leaders are looking ahead to the coming year. What will manufacturing be facing in 2025?
Here are five trends and challenges we’re expecting for the manufacturing industry in 2025 and advice on how to handle each issue.
1. Digital transformation
It’s not that AI and technology are coming for people’s jobs. It’s about this technology being able to streamline how the job gets done, adding speed, quality, and efficiency to the process. The 2024 Manufacturing and Distribution Pulse Survey Report by Citrin Cooperman found 43% of leaders in manufacturing are currently implementing advanced tech programs and policies in their organizations.
It’s involving AI and Machine Learning to optimize processes and outcomes, the Internet of Things (IoT) which will use smart technology to have machines communicate their own glitches and needs for maintenance, and robotics and automation for tasks like assembly.
The end goal is to increase predictive maintenance, optimize processes, ramp up quality control and provide real-time data for better decision making.
What manufacturing should do:
At USC, we help clients use AI, Machine Learning, and Predictive Analytics to optimize their workflows, processes and demand forecasting. Companies should be using these techniques now, if they’re not already. It’s also crucial to upskill existing employees to be able to work with the new technologies. That’s a win-win for manufacturing companies and their workforce. Higher skilled employees are happier, more effective, and more loyal to the company.
2. Talent
Workforce development, skills gaps and employee retention will be the top issues in regard to talent in 2025. It has been estimated that 1.9 million manufacturing jobs could go unfilled over the next decade if talent challenges aren’t solved. The old guard, long term, experienced employees that executives rely on to get the job done are retiring without a strong pipeline of younger workers to take their place. In addition, the labor force itself is concerned with flexibility, hours, pay, child care and more.
But there’s also the issue of skills. A new study by Deloitte and the Manufacturing Institute found that the need for roles requiring higher-level skills, including technical, digital and soft skills are growing at a rapid rate.
What manufacturing should do:
Working with local trade schools, community colleges and even high schools to offer internships and apprenticeships is a great way to build the talent pipeline.
Also, offering current employees training in digital skills, as well as soft skills like leadership and management training, will provide the company with higher-skilled workforce. This will create a sense of loyalty and pride in the employee knowing the company is investing in them with an eye toward the future.
3. Sustainability
The focus on sustainability is everywhere. Manufacturers are feeling increased pressure to become greener, and as a result are implementing environmental, social and governance strategies.
There is governmental pressure because of tighter environmental standards, but there is also pressure coming from consumers who increasingly want and seek out goods that are manufactured with “clean” methods.
What manufacturing should do:
Continuing to investigate efficient technologies like solar and wind, and making investments in machinery and other assets that are more energy efficient, will be crucial in the coming year and beyond. It will help lower operating costs while satisfying the demand from consumers.
4. Supply chain
Supply chain disruption that plagued just about every business on the planet during the pandemic has eased to a great extent, but challenges are still out there. Lead times for materials is still high, and the cost of transportation and logistics is weighing on companies’ bottom lines.
Shipping delays and uncertainties are a big part of the problem, with headlines nearly every day of yet another cargo ship being attacked at sea.
Then there’s the issue of labor shortages all along the supply chain, both in foreign countries and the U.S., with labor strikes slowing down delivery and labor shortages of truck drivers adding to the snarl.
What manufacturing should do:
It’s extremely challenging for companies to combat labor shortages and shipping delays in their supply chains, but smart demand forecasting and considerations like reshoring supply sources can help. In addition, establishing a strong Sales, Inventory, and Operations Planning (SIOP) program will optimize your supply chain.
5. Tariffs
With a new administration may come new global trade policies, and it’s not just the U.S. that held elections in 2024. Many countries around the globe are restructuring leadership. Ongoing U.S.-China trade tensions will certainly intensify as a result of the tariffs the new administration is proposing, driving up the cost of materials for manufacturers.
What manufacturing should do:
Many manufacturers are ordering supplies and materials now, before the new administration takes over. Stocking up now, in case of major price hikes later.
This issue goes hand in hand with supply chain disruption and is one more reason to consider reshoring and nearshoring of supplies and materials.
The Outlook
Despite ongoing challenges, 2025 looks bright for manufacturers to grow their businesses. Adapting operations to be sustainable and incorporating advanced technology with an upskilled workforce to manage it, business leaders will enjoy major improvements to productivity, their supply chain, and customer satisfaction.
At USC Consulting Group, we’re here to help manufacturing companies become more productive and profitable with standardized operating procedures, enhanced management operating systems, SIOP improvements, and other strategies to find opportunities for greater efficiencies, increased throughput and bottom line results. Contact us today to have your operations humming in 2025.
The world is increasingly focused on sustainability, and the manufacturing sector is no exception. Consumers are demanding eco-friendly practices, and regulations are evolving to reflect this shift. This presents a compelling opportunity for manufacturers – by incorporating sustainability principles into the design of their machines, they can not only benefit the environment but also reap significant economic rewards.
The Benefits of Green Design
Sustainable manufacturing machine design offers a win-win scenario for businesses. By focusing on resource conservation and energy efficiency, manufacturers can significantly reduce their environmental footprint. This translates into a positive impact on the planet, aligning them with global sustainability goals. Additionally, sustainable design principles can lead to cost savings through minimized waste generation and lower energy consumption.
Beyond environmental and economic benefits, sustainable machine design can also enhance a company’s reputation. Customers today are increasingly conscious of eco-friendly practices, and a commitment to sustainability can be a major selling point. Furthermore, adhering to evolving environmental regulations becomes easier when sustainability is embedded into the design process from the very beginning.
Implementing Sustainable Design Principles
So, how can manufacturers translate these principles into action? A crucial step is integrating a life cycle assessment into the design process. This involves evaluating the environmental impact of the machine throughout its entire lifespan, from raw material extraction to disposal. This holistic approach allows engineers to make informed decisions about materials, manufacturing processes, and even end-of-life options.
Technology also plays a vital role in sustainable design. Advanced software tools like computer-aided design (CAD) can help engineers optimize both functionality and aesthetics, minimizing material usage and ensuring efficient operation. Additionally, simplifying design complexity can further reduce the environmental impact. Removing unnecessary components not only streamlines assembly but also minimizes energy loss during operation.
Material selection is another critical aspect of sustainable design. Opting for materials with lower embodied energy (the energy required to extract, process, and transport them) and those that can be easily recycled or reused can significantly reduce the environmental burden. For instance, utilizing high-efficiency, NEMA gearboxes, can not only improve overall system efficiency but also extend the lifespan of the equipment, reducing the need for premature replacements.
Safety plays a vital role not only for workers but also for the environment. Conducting thorough safety audits throughout the design process ensures the equipment operates safely and efficiently, minimizing the risk of accidents that could lead to environmental damage. Furthermore, integrating smart technologies like real-time energy monitoring and predictive maintenance systems empowers manufacturers to identify and address potential issues before they escalate into bigger problems.
Curious about the specific ways sustainable design can improve a machine’s environmental impact? The following infographic dives deeper into the benefits of sustainable manufacturing machine design, showcasing how each principle contributes to a greener future for the industry. By adopting these sustainable design principles, manufacturers can create machines that are not only efficient and productive but also environmentally responsible.
All roads are leading most industries to adopt increasingly more sustainable practices. The pressure for manufacturers to go green is growing in the face of climate change, supply chain challenges and especially consumer preferences.
A report from the Roundup, “Environmentally Conscious Consumer Statistics,” paints a pretty clear picture.
- Products marketed as sustainable grew 2.7x faster than those that were not.
- 78% of consumers feel that sustainability is important.
- The sale of carbon labeled products (such as those with 1% For the Planet or Climate Neutral Certification) doubled in one year, reaching $3.4 billion in 2021.
- 62% of people say they “always or often” seek products to purchase because they are sustainable, which is up from just 27% in 2021.
Consumers are opting for products that are sustainable, but that’s not the only headline for manufacturers. Because, it’s not just products. It’s the companies, too. Some 29% of consumers said they are “often or always” influenced by a company’s commitment to adopting more sustainable practices.
Sustainability challenges: It’s not easy being green
Many in the manufacturing industry are undoubtedly feeling some kinship to Kermit the Frog these days. Despite the pressure to adopt more sustainable practices, as the Muppet so famously lamented: “It’s not easy being green.”
It’s all well and good to work toward shoring up the environment (and we need to) but it’s a challenging lift for manufacturers. Some obstacles include:
High upfront costs. New technologies, processes and materials come at a price. It’s especially tough for manufacturers in industries like food and beverage, which has razor-thin margins.
Long wait for return-on-investment. ROI from major expenses can take years to come to fruition.
Supply chain challenges. Even if your company has shifted to more sustainable practices, what about your suppliers?
Skilled labor shortage. It’s difficult enough to find warm bodies to work on the line. But new technologies come with new skills requirements.
Opportunities are emerging
At USC Consulting Group, we help companies look for the opportunities within challenging situations. We always find the silver linings. Here are a few:
Cost reduction. Yes, there are upfront costs. But sustainable practices can lead to reduced energy and water consumption, the possibility of lower regulatory compliance costs, and lower materials costs by using recycled materials.
New partners, suppliers and revenue streams. The sustainable marketplace is an ecosystem all its own. It’s possible to find new partners, customers and even suppliers.
Attract and retain top talent. Yes, there is a labor shortage. But the companies with strong sustainable practices are attracting the best people out there. Companies that care for the environment also find their employees are more engaged and involved.
Governmental tax breaks. The government is committed to rewarding companies for adopting more sustainable practices with tax breaks and other financial incentives.
Strategies for manufacturers
One of the best ways to adopt more sustainable practices is to first look in the mirror. It’s not necessarily about investing in new technologies and turning the world upside down. First, look at your processes and operating systems. You’ll likely find efficiencies you didn’t even know were there. Places to start:
Minimizing waste. Lean Six Sigma methodologies can find hidden wastes and lead to more efficient operations. Not only will it save you considerable money, but minimizing waste is a key principle in sustainability. That’s a win-win.
Operations improvements. How efficient are your operations? A solid management operations system, which is a structured approach to your operations, creates much greater efficiency. The best MOS focus on processes, systems, roles and structures to map out how the job gets done, and by whom. Learn more about it in our short video, Stop the Firefighting Mentality to Improve Your Bottom Line.
Sales, inventory and operations planning. You’ve heard of S&OP. We added the “I.” We find inventory to be a key piece of the operations puzzle. When doing sales forecasting and planning for demand and supply, adding inventory elevates the process a notch. It makes inventory a strategic tool. Learn more about it in our free eBook, “Sales, Inventory and Operations Planning: It’s About Time.”
Training. About that skilled labor shortage. A way to combat that is by training and upskilling your people. And solid training for not just employees on the line but managers, too, will get everyone on the same page, creating greater efficiency organization-wide.
By moving toward more sustainable practices, manufacturers can ultimately reduce costs, find greater efficiencies, attract both consumers and employees and help the planet in the process. But it’s not easy. At USC Consulting Group, we’re the experts on helping companies become more efficient, effective and profitable. With more than 55 years behind us, we’ve seen trends come and go. The key is turning challenges into opportunities. Get in touch to find out more.
When you hire a consulting firm, you expect recommendations, changes, process improvements and a healthy return on your investment. In short, you want your company to be more efficient and profitable when the consultants walk out the door than it was when they walked in. Right? That should be a given.
But, what happens when the project is finished, when the consultants are not there to guide the process going forward? The answer to that question is process improvement sustainability and is a key element USC Consulting Group specializes in.
The aftermath: Preparing clients for sustainability
At USC Consulting Group, operations consulting is what we do. Companies bring us in to look at their operations with a fresh set of eyes, leveraging best practices we’ve learned in our half century (and counting) in the business. We’re not party to office politics and other company red tape, and as such, we’re able to make recommendations for necessary changes, process improvements, and operating and management system overhauls to get the company functioning optimally.
Increasing throughput and yield, reducing excess costs, identifying and eliminating waste — these are some of our areas of expertise. But, at USC, there’s one thing we DON’T do. We do not set it and forget it.
That’s one aspect of our approach that sets us apart from our competitors out there. We play the long game. We don’t swoop in, offer solutions and swoop out, leaving clients on their own. We deliver results that our clients can maintain. We make sure the positive changes we’ve helped companies enact will stick, long after we’re not walking through the door every day. It’s the whole “give a man a fish vs. teach him how to fish” philosophy. It’s our goal to give clients the tools to keep it going. Here’s how we do it:
1. Employee involvement. This needs to start from Day One. It’s hard to overstate how critical employee involvement is while the project is happening, and after it’s complete. We use “daily huddles” with team members to engage on things like scheduling, production, maintenance, quality, project status and much more. We do best practice skills. We review KPIs. The whole idea is to give team members the tools to continue successful operations and maintain the results we’ve achieved together.
2. Action items. Throughout our process, we will regularly identify action items, steps that need to take place going forward. We’ll get agreement on these and hold people accountable for success. It helps set them up for continued success after the project is finished.
3. Managing change management. We say it often — we can effect all the change in the world. But if we don’t manage that change correctly, none of it will stick. We’ve become experts in effective change management over the years. A few pearls of wisdom we’ve picked up along the way: Operational changes require behavioral changes. Employees, especially longtime employees, don’t necessarily love that. People need reassurance their jobs aren’t disappearing. Also, it’s extremely useful to recruit “advocates” on the front lines who can champion the changes we’re implementing. And it’s vital to be clear on the “why” of any changes put forth. Read more about it in “8 Change Management Best Practices to Ensure Sustainability” on our blog.
4. General training. We develop education and training for “in the field” work for team members, supervisors, leads and managers to support the Management Operating System changes being made by the team as well as supporting behavioral change management — also a critical part of the process. People need to do their jobs differently. Sometimes radically differently. And it can be a stumbling block for employees who may be resistant to change. The training gives them the skills to keep progress going.
5. Lean Six Sigma training. It’s a pretty safe bet you don’t have a Lean Six Sigma Master Black Belt on your staff currently. No problem. We do. One of the most effective ways to create lasting process improvements out there, Lean Six Sigma is the combination of two manufacturing methodologies, Lean, which is focused on eliminating waste and reducing process lead times and Six Sigma, which focuses on cutting down on defects and improving quality. But it takes a lot of study to get it right. That’s why we choose team members to train in this highly effective tool so our efforts using it to increase efficiency and decrease defects are sustainable. Read all about Lean Six Sigma in our eBook, “Lean Six Sigma: Do You Really Know These Methodologies?”
6. Toolkit. This is a playbook of what we’ve done on the project, successes we have achieved, steps forward, sustainable practices and more. It’s a detailed, workable plan that outlines how to go forward and build on that success.
All of these tactics work in tandem to ensure process improvement sustainability, so companies remain firing on all cylinders now and into the future. But, that’s not all. We may not be on site every day after a project is completed, but we’re always just a phone call away. We play the long game with our clients and perform audits to ensure sustained results. Setting and forgetting isn’t part of our playbook. Never has been. Never will be.
The material handling industry is the backbone of globalized supply chains. However, it encounters a range of challenges, both internal and external. One notable external challenge is the impact of labor shortages on transportation and logistics, which are vital components of material handling operations.
To overcome these challenges, companies are making significant investments in technology. According to the 2023 MHI Annual Industry Report, 74% of supply chain leaders are increasing technology spending.
While capitalizing on advanced supply chain technologies can offer some respite, leaders may need to take more profound measures to effectively address the emerging issues.
In light of the survey responses featured in the MHI report, this article aims to explore the three primary challenges faced by the material handling industry.
#1: Worker safety
According to the US Bureau of Labor Statistics, there were 5,190 fatal work injuries in 2021, with 798 attributed to exposure to harmful materials or the environment — the highest figure since the series began in 2011!
Material handling operations often involve risky conditions for workers. From handling hazardous chemicals in facilities to lifting heavy loads in warehouses, workers in this supply chain sector regularly risk their health and lives.
Common causes of worker injuries in material handling include:
- improperly stored materials falling
- damaged storage units
- heavy manual lifting, pushing, or carrying
- exceeding loading limits on lifting equipment
- collision with materials or equipment.
Ensuring workers’ safety and security is vital and requires a multi-pronged approach. Safety negligence or violation can quickly become a compliance issue, resulting in monetary and reputational damage.
Material handling and supply chain companies address workplace safety challenges by providing personal protective equipment (PPE), delivering safety training, conducting equipment training, and performing safety audits.
Conscious companies that rely on manual labor also address the ergonomics of material handling in their safety training. Identifying ergonomic risk factors in manual or machine-supported lifting, carrying, and pushing jobs is critical for preventing fatigue and injury.
To prioritize the health and safety of their employees, conscious companies cultivate a “safety-first” culture. A prime example of a logistics company that excels in worker safety is DHL, based in Germany.
Safety is a core value for DHL, and they have implemented a holistic approach to address safety concerns through continuous training, strict compliance with regulations, and active employee engagement.
#2: Material and equipment damages
Poorly maintained equipment, untrained workers, and natural disasters can lead to expensive damages. Among these challenges, equipment damage stands out as one of the primary concerns for material handling companies, often resulting in downtime. In fact, unplanned downtime costs manufacturers a staggering $50 billion annually.
To ensure reliability and resilience, timely maintenance is crucial for all aspects of material handling operations, ranging from trucks and forklifts to pallets and sliding racks.
Similarly, it is equally important to prevent damage to the materials being handled by the equipment or workers. Well-organized warehouse loading and unloading processes, supported by well-trained workers and advanced technology, can effectively minimize material handling damages.
Many supply chain companies are leaning towards predictive maintenance solutions for equipment to ensure they are well-maintained for operations. Predictive maintenance leverages technologies like artificial intelligence (AI) and machine learning (ML) to predict potential problems with equipment and fleet.
In addition, these companies are minimizing accidents that result in costly damages through increased visibility. Warehouse inventory management and organization technology, for example, helps maintain optimal inventory levels, prevents overstocking, and ensures efficient use of storage space.
Gradesens, a Swiss company specializing in predictive maintenance, is helping logistics companies with very-narrow aisle warehouses proactively maintain automated systems for loading and unloading. With accurate and timely maintenance, the warehouses prevent downtime because of equipment failure.
#3: Controlling emissions
Carbon emissions are a huge problem for major industries, and material handling is no exception. With environmental organizations ringing alarm bells on rising global temperatures, material handling and supply chain leaders are paying close attention to sustainability.
Material handling operations, including warehousing, contribute to greenhouse gas (GHG) emissions through electricity usage, particularly natural gas. Additionally, using fossil fuel-powered vehicles and equipment contributes significantly to carbon emissions. Many material handling companies make up Scope 3 emissions for other organizations.
Fortunately, the material handling industry is adopting energy-efficient practices, thanks to environmental advocacy and pressure from governments with ambitious sustainability goals.
The MHI report revealed that organizations in material handling are investing in electrification, natural resource management, sustainable water consumption, and the transition to renewable energy.
Similarly, the European Logistics Supply Chain Sustainability Report found that 80% of surveyed companies consider sustainability a key focus area.
Material handling companies are reducing carbon footprint by investing in electric lift trucks. Electric forklifts have zero emissions compared to their counterparts powered by internal combustion engines.
Renewable energy has also been a focus for the industry, with major companies setting goals to go 100% carbon-neutral or net zero emissions. For instance, Amazon, the largest corporate buyer of renewable energy, uses clean energy in many fulfillment centers. The company plans to reach its 100% renewable energy goal by 2025.
The takeaway
Material handling is linked with virtually every industry, which makes its challenges essentially every industry’s challenges.
Some of the issues aren’t unique to material handling. For instance, sustainability is a global issue. The good news is that many companies are taking promising measures to combat these challenges: and technology is at the heart of these solutions.
It’s imperative for organizations in material handling to provide training and maintain equipment for better worker safety. Similarly, investing in clean energy solutions can go a long way in reducing emissions, which is good for the environment and business.
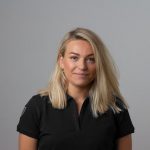
Matilda Odell
*This article is written by Matilda Odell. Matilda works as the Content Creation Specialist at the brand TAWI, a brand by Piab Group, which enables smart lifting optimized for people and businesses. Piab helps its customers to grow by transforming their businesses with increased automation. If you have any questions about lifting equipment such as vacuum lifters or other lifting devices, Matilda is the person to talk to.
If your business is experiencing challenges with processes and operations, it isn’t as efficient as it should be, or if you are striving to increase throughput while cutting costs, it may be time to bring in an operations management consultant.
However, before you sign on the dotted line, you should know the advantages and drawbacks to hiring operations management consultants to help. Let’s take a behind-the-scenes look at operations consulting, how it can benefit your business and some pitfalls we can help you avoid.
Pros and cons of operations management consultants
Operations consulting is what USC Consulting Group has specialized in for more than half a century, and with that, we have been exposed to various situations around the world. But it’s not always easy bringing in people from the outside to tackle the challenges you’re having internally. Here are some pros and cons to consider.
Pro: Process improvement expertise. Your company is in the business of whatever it is you do. Consultants are in the business of process improvements. It’s all we do. We are experts in techniques like Lean Six Sigma (LSS) — there aren’t many companies out there with many in-house black belts in this discipline. LSS is focused on eliminating waste and improving throughput, and it takes years to become an expert in it. External consultants like USC goes beyond LSS to focus on both your people and processes.
Con: Lack of accountability. Some external consultants “fix it and forget it.” They swoop in, offer recommendations for change, hand you a file stuffed full of info about what they found and then swoop out, on to the next project. This is a serious drawback. (Note: USC does NOT work this way)
Pro: Industry expertise. At USC Consulting Group, we have 55 years of experience under our belts. We’ve seen it all. And while every situation and challenge is unique, we are coming at those challenges with decades of experience as our solid foundation for success.
Con: Learning curve. Consultants lack knowledge of in-house procedures and it takes a couple of weeks to get up to speed with a company’s specific processes. USC performs Feasibility Studies to build the business case for the project and at the same time get acquainted with the client’s facilities and operations. We start by listening, hastening that learning curve.
Pro: Training and improvement for staff. If you’re working with the right outside consultant, that is. At USC, we aren’t just about fixing challenges for companies. We coach and teach our clients on how to sustain those changes, instead of just fixing and forgetting. In other words, we provide the training and know-how for you to take it from there. The result is the upskilling of your employees as part of the bargain. That’s an added bonus not all consultants provide.
Con: Lack of sustainability. This is another potential downside of hiring the wrong consultant. Sure, it’s great to highlight challenges and offer recommendations for change, but those changes don’t stick if the consultant leaves it to you to implement them. That’s why we work with your team to implement the process improvement changes and train your people along the way so they can sustain the success long after we’ve left.
Pro: Unbiased third-party advisors. Consultants are not part of a company’s internal politics. We are above the fray. This comes in handy when recommending process changes, because who takes direction from whom can be tricky in companies. We’ve seen it time and time again: recommendations for change go down easier when they come from outside the organization, rather than from within it.
Con: Don’t know the unwritten or unspoken rules. Yes, we may be the aforementioned unbiased third-party advisors, and that’s a big advantage. But it also can be a stumbling block because we don’t know the unwritten rules in your organization. These are cultural norms, do’s and don’ts, that aren’t in any company handbook. Depending on the company, this may be good or bad.
Pro: Cost. Bringing in an outside consultant is actually less expensive than doing the project in-house. If you use an internal process improvement team made up of current employees from different departments, you’re not only paying the cost of the project itself, but the cost of lost productivity when team members are away from their usual duties. If you have a dedicated internal process improvement team, we’re talking about costs involved with salaries, benefits, perks and the whole nine yards. On top of all of that, you are risking the costs associated with failure because you don’t have experienced pros on the project. At USC, there are no net annualized costs due to the results and benefits achieved within the first year that continue for many years after.
Con: Cost. Yes, there are both pros and cons to cost. With consultants, you’ll have a large upfront investment. There’s just no getting around that. But, in the immortal words of the author Kurt Vonnegut, you get what you pay for. Hiring a consulting firm, you’re paying for process improvement expertise. At USC, we have 55+ years of it under our belts. One important thing to note: The breakeven point, when you’re reducing operating costs and improving productivity and throughput, this offsets the cost of the project and is usually realized within six months or sooner.
Pro: Fresh eyes to overcome challenges. You know what they say about forests and trees. Sometimes, internal people are simply too close to the problem to see their way out of it. We can look at the big picture and shine a light on processes and gaps that may be weighing you down.
Pro: Horsepower. USC Consulting Group empowers employees with the tools and techniques that drive optimal performance, adding “horsepower” to your teams. We can augment your team’s efforts and achieve results quicker.
So what does this all mean? Yes, there are drawbacks to be aware of when bringing in operations management consultants. However, when done right, the benefits they bring to your team and process improvement projects completely outshine those concerns.
USC Consulting Group stands ready to help you. Operations consulting is what we do. We know we can come in and get the job done, helping our clients achieve greater efficiency and throughput, improved processes and ultimately a healthier bottom line. We’ll be happy to talk with you about how we can augment your operations.
Already have an internal improvement team? Read more about both options in our article: “Operations Management Consultants vs. Internal Improvement Teams: What’s the Difference?”
The eco-conscious movement is influencing a sustainable transition for manufacturers in the industrial sector. Higher demands for green products forces companies to lower their carbon emissions and surface-level waste production. Manufacturing facilities can limit their environmental effects by adopting six sustainability-enhancing practices.
1. Installing Solar
A direct way of reducing greenhouse gas emissions is by installing renewable energy systems. Nearly 81% of America’s energy supply comes from fossil fuels. During combustion, they release air pollutants, degrading the atmosphere’s natural composition.
Manufacturers can install solar panels on roofs, accessing emission-free electricity. Reducing localized air pollution supports the regional ecosystem and improves air quality. Transitioning away from fossil-fuel-derived electricity towards solar power also decreases a manufacturing facility’s utility costs.
Solar is currently the most cost-effective energy source on the market. When manufacturers cater to eco-conscious consumers’ needs using renewable energy, they increase their profits while decreasing their production costs.
2. Recycling Excess Materials
Manufacturing facilities can also decrease their environmental impacts by recycling excess materials. Many companies dispose of unused products because it is cost-effective. Though recycling comes with a small monthly fee, it significantly improves a company’s sustainability.
Recycling metals like aluminum can minimize the energy used to make new versions by 90% on average. It decreases emissions and landfill usage, preserving the environment’s natural state. Companies can also repurpose their excess materials, further reducing their ecological effects.
3. Increasing Water Efficiency
Manufacturing facilities may additionally improve their eco-friendliness by reducing freshwater exploitation. Companies can install a rainwater harvesting system to decrease their reliance on conventional water supplies. The system collects storm discharge in barrels, filters it, and pumps it into hoses, faucets, showerheads, and more.
4. Install Smart Devices
Companies can also decrease resource exploitation by installing smart devices. America uses nearly 155 billion kilowatt-hours of energy for commercial cooling alone. Manufacturing facilities can limit their electricity use by utilizing smart thermostats.
The device connects to a heating, ventilation, and air conditioning (HVAC) system, maintaining energy-efficient indoor temperatures. It gathers real-time weather predictions through a Wi-Fi connection, adjusting the thermostat to decrease emissions. Additionally, the device uses motion detection sensors, shutting the system off when a building is vacant.
5. Receive an Energy Audit
Receiving an energy audit can increase a manufacturer’s awareness of sustainability limitations. Companies now conduct audits specific to the standards of Leadership in Energy and Environmental Design (LEED). They assess the efficiency of devices, systems, and more, evaluating the entire facility’s emissions and eco-friendliness.
6. Use Automated Technology
More industries are using robots to increase the energy efficiency of manufacturing processes. Automated devices are more accurate than humans, decreasing error-derived material waste. Engineers also design the technology to limit electricity use, shrinking a facility’s carbon footprint.
Sustainable Manufacturing
Companies must also enhance the sustainability of their manufacturing processes to become greener. The products they use significantly affect their eco-friendliness. Some manufacturers outsource their materials from underdeveloped countries, accessing the most cost-effective versions.
These inexpensive goods are sometimes less sustainable because of their transportation footprint. International shipping practices account for 740 million metric tons of greenhouse gas emissions annually. Outsourcing materials can expand a manufacturer’s carbon footprint and decrease its ethical accountability.
Many cost-effective, outsourced materials come from countries with limited regulations and inadequate workers’ rights. When a company purchases products from these regions, they support unethical practices. Manufacturers can increase their sustainability by sourcing eco-conscious materials from their area, limiting emissions and regulating development.
They may also use low-emission tools and machines, further shrinking their footprints. Manufacturers can additionally collect excess materials and reuse them for future projects. Decreasing greenhouse gas emissions and material waste may significantly increase a company’s sustainability.
Implementing Change Today
Manufacturers can enhance their facility’s sustainability by installing green systems and training employees to minimize waste and emissions. Adopting eco-conscious practices may be challenging for some workers, and there are methods of increasing their willingness to take part. Employers can use sustainable change to show they care and value their employees.
Lowering emissions and eschewing environmentally degrading materials can protect workers from polluted air consumption. Using automated systems also decreases their risk of injury on the job. When employees discover the importance of enhancing sustainability, a manufacturing facility can achieve efficient changes.
*This article is written by Devin Partida. Devin is a tech writer with an interest in IIoT and manufacturing. She is also the Editor-in-Chief of ReHack.com.
At USC Consulting Group, we are an experienced operations management firm that is proud to say we’ve been in business for more than 50 years. Not many companies like ours can say that. Here’s a look into how we work, and how we’ve stayed on top for more than five decades… and counting.
We don’t sit in the CEO’s office preaching about how you can improve your business. We work with your employees at all levels to learn the issues disrupting your operations and together we implement improvements.
Upgrade to state-of-the-art machinery? That’s a huge expense you probably don’t need. We help you get more out of your existing assets.
New safety protocols like temperature checks and physical distancing are taking everyone’s productivity down a notch. Supply chain disruptions aren’t helping, either. That’s why it’s crucial to be as efficient as possible.
We uncover hidden opportunities for greater efficiency in your processes and transfer that knowledge to your team to ensure sustainability.
Running like that proverbial well-oiled machine will be the key to you not simply surviving, but thriving. USC Consulting can help you get there.
Watch below to see what working with USC Consulting Group looks like:
If you are in need of an experienced operations management firm to improve your business, look no further than USC Consulting Group. We will help you reduce operating costs and improve productivity across your entire supply chain. Contact us today.
Nobody knows the job better than your frontline employees. So, when you’re instituting new efficiencies to improve the processes and procedures that they use on the job every day, one vital key to success is getting their buy-in from the get-go.
At USC Consulting Group, helping companies find process improvements is what we do. We work with companies in industries like manufacturing, mining and metals, oil and gas, food and beverage, transportation and logistics, and others to become more efficient, effective and in the end, profitable. We strive to empower your performance and help you reach your highest potential by uncovering greater operating excellence across the entire supply chain. It’s about identifying and eliminating wasteful practices and procedures.
One big difference between us and the other guys is how we go about doing that.
We sell our methodology and our process, not just a solution
Nine times out of ten, when companies come to us, they already have a pretty good idea of what their challenges are. So we don’t go into a client engagement telling them what we think they should do. We have over 50 years in this industry behind us, but all of that experience doesn’t mean we provide cookie-cutter solutions. Most of our clients are looking to us to break bottlenecks in their operation, find out if they can do more with what they have, or even do more with less. But every one of our clients is unique. Every one of those bottlenecks has a different cause. The only way to find the best road that will lead to more process efficiencies is not to rest on our laurels and do what worked for the last client, but to roll up our sleeves, get into your operation and see what’s going on.
A big part of that is listening to your frontline people.
Your frontline employees are the key to the success of the project
We don’t simply sit in your boardroom and pontificate with your C-suite about how to do things better. At USCCG, we believe it’s about effecting change at the point of execution. That means we involve your frontlines. Ferreting out new processes and solutions that can increase efficiencies starts with the people actually doing the job. It’s the only way it’s going to work. Here’s why:
A single source of truth. By talking to your frontline employees, we get the lowdown on what’s happening in your operation day to day. We hear what’s going right, and at times, what’s going wrong. They often can see what the problems are, but not know how to fix them. We can get the single source of truth from your frontlines and implement plans to fix the issues and improve productivity. It’s crucial to finding where efficiencies can happen.
From resistance to change… We get it; change is difficult to accept. More than that, it can be threatening. Frankly, it’s completely counterproductive to swoop in and tell people that the way they’ve been doing their jobs for years is inefficient at best and wrong at worst. You’ll lose their cooperation. They’ll be resistant to any new ideas, because those new ideas mean the way they’ve been working has been wrong. If you don’t get their cooperation, it can be difficult to implement any sort of process changes. And if you have their opposition, it can be downright impossible.
…to drivers of change. That’s why involving your employees in the process from the start is so important. It ensures they’ll feel listened to and respected. It won’t be something that’s happening to them. Positioning this process as a way to harvest their wealth of frontline information in order to make the company more effective and efficient is the key to making it work. We involve employees from the get-go, and time and time again, we’ve seen them become the drivers of change.
Making the changes stick. Initial buy-in is only the beginning of the importance of your employees to this process. It goes further than that. It’s about making sure those changes stick. Your employees need to feel invested in the process changes in order for them to stick to them, on the job, every day. That’s why we don’t come in and hand them a new playbook. They’ll help write it. And that’s crucial to the success of implementing change.
At USC Consulting Group, we understand how important employees are in the process of change. We will respect them, listen to their institutional knowledge that only years on the job day after day can provide, and create a collaborative approach to finding the hidden opportunities for greater efficiency in your operation.
For more information about how we work during this time of COVID, download our free eBook Times have Changed – USCCG Can Help You Adapt.