-
Subscribe to Blog:
SEARCH THE BLOG
CATEGORIES
- Aerospace
- Asset Maintenance
- Automotive
- Blog
- Building Products
- Case Studies
- Chemical Processing
- Consulting
- Food & Beverage
- Forestry Products
- Hospitals & Healthcare
- Knowledge Transfer
- Lean Manufacturing
- Life Sciences
- Logistics
- Manufacturing
- Material Utilization
- Metals
- Mining
- News
- Office Politics
- Oil & Gas
- Plastics
- Private Equity
- Process Improvement
- Project Management
- Spend Management
- Supply Chain
- Uncategorized
- Utilities
- Whitepapers
BLOG ARCHIVES
- July 2025 (1)
- June 2025 (4)
- May 2025 (1)
- April 2025 (1)
- March 2025 (1)
- February 2025 (4)
- January 2025 (4)
- December 2024 (4)
- November 2024 (2)
- October 2024 (6)
- September 2024 (5)
- August 2024 (5)
- July 2024 (6)
- June 2024 (3)
- May 2024 (3)
- April 2024 (4)
- March 2024 (3)
- February 2024 (4)
- January 2024 (5)
- December 2023 (2)
- November 2023 (1)
- October 2023 (6)
- September 2023 (3)
- August 2023 (4)
- July 2023 (2)
- June 2023 (3)
- May 2023 (7)
- April 2023 (3)
- March 2023 (3)
- February 2023 (5)
- January 2023 (6)
- December 2022 (2)
- November 2022 (5)
- October 2022 (5)
- September 2022 (5)
- August 2022 (6)
- July 2022 (3)
- June 2022 (4)
- May 2022 (5)
- April 2022 (3)
- March 2022 (5)
- February 2022 (4)
- January 2022 (7)
- December 2021 (3)
- November 2021 (5)
- October 2021 (3)
- September 2021 (2)
- August 2021 (6)
- July 2021 (2)
- June 2021 (10)
- May 2021 (4)
- April 2021 (5)
- March 2021 (5)
- February 2021 (3)
- January 2021 (4)
- December 2020 (3)
- November 2020 (3)
- October 2020 (3)
- September 2020 (3)
- August 2020 (4)
- July 2020 (3)
- June 2020 (5)
- May 2020 (3)
- April 2020 (3)
- March 2020 (4)
- February 2020 (4)
- January 2020 (4)
- December 2019 (3)
- November 2019 (2)
- October 2019 (4)
- September 2019 (2)
- August 2019 (4)
- July 2019 (3)
- June 2019 (4)
- May 2019 (2)
- April 2019 (4)
- March 2019 (4)
- February 2019 (5)
- January 2019 (5)
- December 2018 (2)
- November 2018 (2)
- October 2018 (5)
- September 2018 (4)
- August 2018 (3)
- July 2018 (2)
- June 2018 (4)
- May 2018 (3)
- April 2018 (3)
- March 2018 (2)
- February 2018 (2)
- January 2018 (1)
- December 2017 (1)
- November 2017 (2)
- October 2017 (2)
- September 2017 (1)
- August 2017 (2)
- July 2017 (2)
- June 2017 (1)
- April 2017 (3)
- March 2017 (3)
- February 2017 (2)
- January 2017 (2)
- December 2016 (2)
- November 2016 (4)
- October 2016 (4)
- September 2016 (3)
- August 2016 (6)
- July 2016 (4)
- June 2016 (4)
- May 2016 (1)
- April 2016 (3)
- March 2016 (4)
- February 2016 (2)
- January 2016 (4)
- December 2015 (3)
- November 2015 (3)
- October 2015 (1)
- September 2015 (1)
- August 2015 (4)
- July 2015 (6)
- June 2015 (4)
- May 2015 (7)
- April 2015 (6)
- March 2015 (6)
- February 2015 (4)
- January 2015 (3)
CONNECT WITH US
Tag Archives: Supply Shortages
The automotive industry outlook shows it travelling down the road toward another challenging year. The global supply chain is still reeling from COVID-era issues resulting in slow manufacturing times. Reduced consumer demand for traditional vehicles is impacting the industry, and the gasoline crisis amid the Russia-Ukraine tensions is keeping people off the roads. Despite these challenges, there is great reason for positivity. Brighter skies are on the horizon.
One especially bright spot: Electric vehicles. EVs have taken the market by storm, with many manufacturers worldwide making pledges for increased production and utilization of this emerging technology. Along with that comes increased need for things like batteries and charging stations to support widespread EV use. It’s exciting to see the increased need for the infrastructure and tools required to go electric!
In this article — with information from The Economist Intelligence Unit’s (EIU) comprehensive Automotive Industry Outlook 2023 — we will highlight key trends to be aware of in the industry for the coming year.
Gas Uncertainty
As long as the tensions between Russia and Ukraine persist, gas prices and availability will remain a question mark — but it’s a trend that started long before those tensions erupted. It began with the COVID pandemic.
Beginning in March of 2020, demand for gas plummeted when the majority of the U.S. was put on forced isolation. People just weren’t commuting. The highways were like ghost towns. Midway through the pandemic, folks started wondering when was the last time they filled up their gas tanks. They might not have been able to remember, but the industry certainly did. It caused many of the oil refineries in the United States to stall or close their doors for good.
While refinery numbers are slowly creeping back up, challenges still exist. According to the Refinery Capacity Report from the U.S. Energy Information Administration (EIA), this past June saw a refining shortage of roughly one million barrels of oil a day compared to pre-pandemic numbers. Add that to the ongoing tensions in Eastern Europe, and the market has many questions to answer in regards to supply and refinement capabilities.
Supply chain shortages
While the global supply chain is rebounding from the unprecedented COVID-era delays, there is still work to be done and shortages of supply.
One of the most prominent concerns for the automotive industry is the status and availability of semiconductors. EIU anticipates that additional capacity for this essential piece of equipment won’t come until 2024 — and the shortages of essential minerals such as steel, aluminum, nickel and lithium won’t just impact the semiconductor market, but the production of EV batteries as well.
To combat this, many countries are taking action to increase local production and mineral extraction. The United States, for example, recently passed the CHIPS and Science Act of 2022. According to the White House briefing, the act will drastically increase domestic semiconductor research and production, and “strengthen American manufacturing, supply chains, and national security, and invest in research and development, science and technology (…) including nanotechnology, clean energy, quantum computing, and artificial intelligence.”
It remains to be seen if this can supplement the semiconductor shortage for 2023, but it is certainly a step in the right direction for future availability.
Stalled sales
After a rise in both new and used vehicle prices in 2022, sales for traditional automobiles are set to decline in 2023. The reasons include a perfect storm of reduced commuting time for people who continue to work from home, continued high gas prices and the aforementioned supply chain issues and semiconductor shortages, which caused a massive increase in cost for both new and used vehicles. The result? People are putting off buying new vehicles as their cars sit in their garages. One of the biggest culprits is simply the rising prices of new cars. Consumers paid $3,462 more on average for a new vehicle in 2022 than the previous year.
Slowly but surely, as the supply chain issues are repairing and more supply enters the market, sales and prices are set to decrease in the upcoming year. The EIU predicts that new car sales will decrease by 2.4% in North America… but estimated global vehicle sales of $79 million will continue to fall short of the pre-pandemic $88 million in sales.
“The total EV investment among automotive suppliers and manufacturers is set to reach $526 billion between 2022 and 2026.“
The EV wave
The shining star of the automotive industry in 2023 and beyond is the continued production and implementation of electric vehicles and charging stations.
While electric vehicles only accounted for 8% of global sales in 2021, production and market share is set to explode to an estimated 33% of global sales by 2028, and as high as 54% in 2035, according to Reuters. Not only that, but the total EV investment among automotive suppliers and manufacturers is set to reach $526 billion between 2022 and 2026, nearly double the investment from the beginning of the decade.
The EIU confirms that optimism, predicting that the sales of electric vehicles will grow by roughly 25% in 2023, to almost 11 million units. The ongoing tax breaks and subsidies provided by countries around the world are seemingly propelling this growth, with more incentive now than ever to join the EV automotive revolution.
We can help to navigate uncertainty
While the automotive industry outlook is set for a challenging year in 2023, there is still light at the end of the tunnel for manufacturers to get back on track and capitalize on new trends.
At USC Consulting Group, we are always ready to help your organization stay on top of the automotive industry. Give us a call today to ensure successful operations in the upcoming year and the foreseeable future.
Imagine a scenario in which there is unprecedented demand for the products you manufacture, but disruptions in the supply chain are making it difficult, if not impossible, to meet that demand and even if you do, logistics bottlenecks are preventing them from getting where they need to go. Many manufacturers have been running up against this problem since the pandemic began.
Now imagine that people’s very lives literally depend on those products being manufactured and delivered to their destinations.
If you’re in the medical device manufacturing industry, you’re likely thinking: “Welcome to my world.” Not only has it been as hard hit as any other manufacturer by supply chain disruptions and logistic backups, the implications of the resulting shortages of the devices they manufacture may cost people their lives.
The FDA is calling the shortages of medical devices at this critical time a “public health emergency.” It published a device shortage list including the categories of personal protective equipment for medical workers, testing supplies and equipment, and ventilation-related products. The list also outlines the specific products, the estimated duration of the shortage, and the reasons for the shortages, along with what the government is doing about it.
That list is illuminating — and even frustrating — for many reasons, but it’s not all bad news. Among the most common reasons for shortages, including increased demand and supply chain issues, which manufacturers have little control over, there is also one culprit that manufacturers can control: “Requirements for complying with good manufacturing practices.”
As medical device manufacturers know, the FDA has strict compliance requirements that affect every part of the process from designing to manufacturing to testing to shipping, even labeling. In those processes, there can be room for improvement. That’s something manufacturers can do — process improvements to get their products to market faster, while still complying with the FDA.
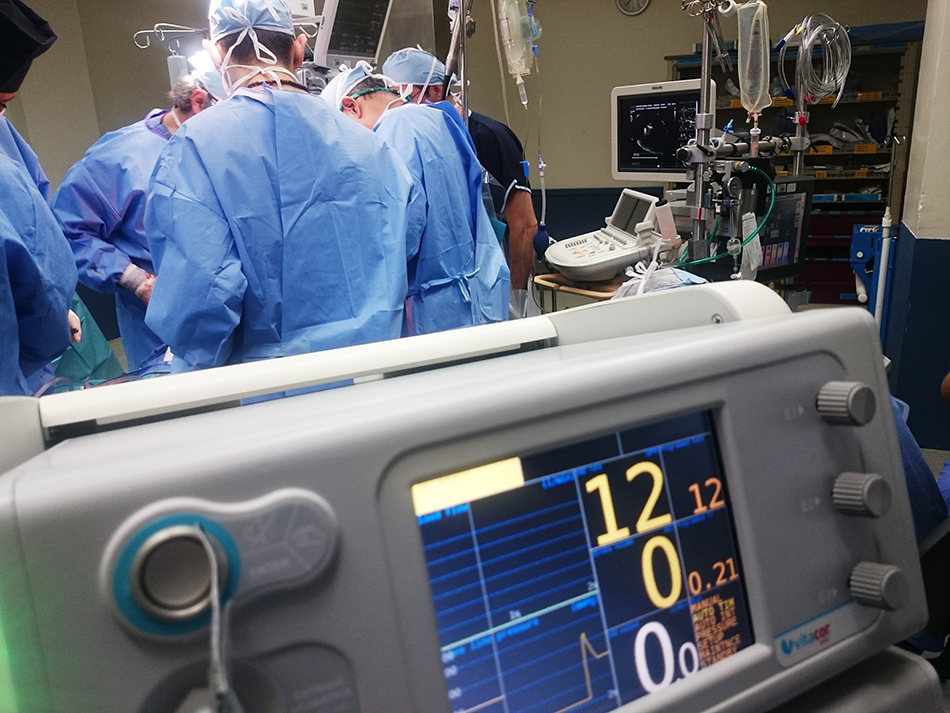
The FDA is calling the shortages of medical devices at this critical time a “public health emergency.”
What medical device manufacturers can do now
At USC Consulting Group, we’ve been helping manufacturers up their operational efficiency for more than 50 years. We analyze what you’re doing, how you’re doing it, and how we can create greater efficiency using your existing resources. A few tactics we’re implementing with our medical manufacturing clients to help mitigate these shortfalls and get their products to people who need them quicker include:
Investigate Lean / Six Sigma
Lean manufacturing is nothing new. The art of maximizing customer value while minimizing waste was pioneered by Henry Ford … or Toyota, depending on who you ask, decades ago. Six Sigma is a newer methodology designed to tackle defects in manufacturing. While Lean looks at making processes more efficient and reducing process lead times, Six Sigma focuses on cutting down on defects that can delay production. In fact, they’ve joined to become one methodology in some circles. Lean techniques help you get product off the line faster, heightening your throughput. Six Sigma strives to target the reason for any defects in the products. These two techniques can conflict — one sure way to cut down on defects is to slow down the process, which runs counter to Lean’s goals. Achieving the perfect balance between the two, and getting the job done faster with fewer defects, is indeed an art form, and worth exploring.
Use SIOP to make your planning and forecasting bulletproof
We recommend using SIOP (Sales, Inventory and Operations Planning) to elevate your planning process to achieve that perfect balance between your supply and demand. You’ve heard of S&OP, a popular business management process that involves sales forecast reports, planning for demand and supply, and other factors. The goal is to help companies get a better, more clear look at their operations and create better-informed strategy decisions, allowing them to deliver what clients need in the most profitable way.
It’s a useful process, but we’ve found a lot of our clients do not include inventory as a strategic tool in their S&OP process. Therefore, they leave the “I” out of SIOP. Adding inventory into the mix is just one additional step, but we find it can be the key to the whole process. When you’re focusing on inventory, it requires more careful planning and elevates the entire planning process up a notch. When your inventory is optimized, which is not an easy mark to hit in these days of supply chain disruption, things tend to fall into place. With SIOP, you can make your inventory work harder for you.
Download our free eBook, “Sales, Inventory and Operations Planning: It’s About Time,” to dive deeper into SIOP.
Involve your frontline employees
We call it the Employee Involvement Prototype (EIP). It’s about engaging with your employees at the machine level and getting good data from the floor. It includes anyone who has to do with the line, and entails taking a look at those operations and processes with input from the men and women who are actually doing the job on an hour-by-hour basis.
Focus on throughput, productivity and yield
Take a good look at what’s happening on the line. What is the “drumbeat”? Are all your functions in sync? Can you improve production by cutting redundant steps?
For more information on these two points, download our whitepaper, “Strategies for Meeting Increasing Customer Demand.” It goes into much more detail about how you can create that proverbial well-oiled machine.
When it comes to caring for people and providing the products they need, time is of the utmost importance. Medical device manufacturers understand they must overcome the worst supply chain disruptions to deliver to the people whose lives depend on them.
Need help? Give us a call. We can save your operations so you can save lives.
Manufacturers have had an uneasy past two years. Disruptions early in the pandemic nearly brought production to a halt in some areas, and now, supply chain shortages plague the industry.
Building materials have seen some of the most dramatic shortages, with 94% of surveyed builders struggling to find framing lumber. Electronics manufacturers and those relying on them have struggled, too. The automotive industry stands to lose $61 billion this year due to semiconductor shortages.
Other materials and parts in short supply include palm oil, plastics, corn, steel, and chlorine.
The Causes Behind Manufacturing Supply Shortages
There are many factors behind these shortages, most of them sprouting from the pandemic. Economic downturns and worksite restrictions have stopped or slowed many processes like farming, mining, and parts production globally. Even as these obstacles fade, these producers of materials and parts find themselves with considerable backlogs, leading to ongoing shortages.
A surge in demand has compounded these supply issues. General manufacturing demand was already increasing, with U.K. consumers alone spending more than $1.6 billion online weekly in 2019. E-commerce skyrocketed further amid the pandemic, and on the commercial side, many manufacturers rushed to meet previous production levels, outpacing their still-struggling suppliers.
International travel restrictions have also made shipping slower and more expensive, exacerbating the crisis.
Strategies for Mitigating Supply Issues
While there is no silver bullet for these supply shortages in manufacturing, several steps can mitigate their impact. Manufacturers can also take this opportunity to prepare against future disruptions, avoiding similar situations. Here are three leading strategies for navigating these supply issues.
1. Improving Visibility
One of the most crucial changes to make is to increase visibility across the supply chain. Internet of things (IoT) technology and data analytics programs can give manufacturers more insight into stock levels and developing situations. They can then predict shortages and take steps early to account for them.
Real-time visibility can also help track shipments to give customers a better idea of when they can expect their end products. Over time, this data can inform more accurate predictions and reveal needed workflow changes. Manufacturers can then become more resilient against supply chain issues.
2. Diversifying Sources
In manufacturing, many facilities tend to source from a single supplier. While this minimizes costs, it also intensifies shortages when disruptions arise. Manufacturers can lessen the impact of slowdowns and other unexpected issues by diversifying their sources.
Much like how Amazon uses artificial intelligence (AI) to keep merchandise close to consumers, manufacturers can analyze data to find ideal nearby sources. Domestic or near-short suppliers will produce fewer disruptions in a crisis as there’s less distance and fewer regulations involved. Using multiple suppliers will further reduce shortages by removing dependencies.
3. Turning to Alternatives
Some manufacturers have found relative success in using alternative materials to account for shortages. For example, some construction material companies have switched to unconventional insulation materials in the face of petroleum shortages. Manufacturers may be able to adjust processes to use novel or less-common materials to maintain production.
If facilities take this route, being transparent with customers is crucial. End products may have different qualities or incur higher prices with new materials, so manufacturers must be upfront about these changes. They may cause initial disruptions but can mitigate persistent issues with conventional parts.
Manufacturing Must Adapt Amid Widespread Shortages
Given the prevalence and severity of these shortages, they won’t likely go away soon. It will take time for production to fulfill backlogs and meet demand. On the positive side, this increased demand indicates healthy industry growth, but manufacturers must prevent similar crises in the future.
Since these shortages are multifaceted issues, no one solution will fix them. Adopting a multi-step approach, including implementing new technologies for visibility and adjusting sourcing methods, is essential. The industry faces significant obstacles right now, but these will inspire positive change for the future.
*This article is written by Devin Partida. Devin is a tech writer with an interest in IIoT and manufacturing. She is also the Editor-in-Chief of ReHack.com.