-
Subscribe to Blog:
SEARCH THE BLOG
CATEGORIES
- Aerospace
- Asset Maintenance
- Automotive
- Blog
- Building Products
- Case Studies
- Chemical Processing
- Consulting
- Food & Beverage
- Forestry Products
- Hospitals & Healthcare
- Knowledge Transfer
- Lean Manufacturing
- Life Sciences
- Logistics
- Manufacturing
- Material Utilization
- Metals
- Mining
- News
- Office Politics
- Oil & Gas
- Plastics
- Private Equity
- Process Improvement
- Project Management
- Spend Management
- Supply Chain
- Uncategorized
- Utilities
- Whitepapers
BLOG ARCHIVES
- June 2025 (4)
- May 2025 (1)
- April 2025 (1)
- March 2025 (1)
- February 2025 (4)
- January 2025 (4)
- December 2024 (4)
- November 2024 (2)
- October 2024 (6)
- September 2024 (5)
- August 2024 (5)
- July 2024 (6)
- June 2024 (3)
- May 2024 (3)
- April 2024 (4)
- March 2024 (3)
- February 2024 (4)
- January 2024 (5)
- December 2023 (2)
- November 2023 (1)
- October 2023 (6)
- September 2023 (3)
- August 2023 (4)
- July 2023 (2)
- June 2023 (3)
- May 2023 (7)
- April 2023 (3)
- March 2023 (3)
- February 2023 (5)
- January 2023 (6)
- December 2022 (2)
- November 2022 (5)
- October 2022 (5)
- September 2022 (5)
- August 2022 (6)
- July 2022 (3)
- June 2022 (4)
- May 2022 (5)
- April 2022 (3)
- March 2022 (5)
- February 2022 (4)
- January 2022 (7)
- December 2021 (3)
- November 2021 (5)
- October 2021 (3)
- September 2021 (2)
- August 2021 (6)
- July 2021 (2)
- June 2021 (10)
- May 2021 (4)
- April 2021 (5)
- March 2021 (5)
- February 2021 (3)
- January 2021 (4)
- December 2020 (3)
- November 2020 (3)
- October 2020 (3)
- September 2020 (3)
- August 2020 (4)
- July 2020 (3)
- June 2020 (5)
- May 2020 (3)
- April 2020 (3)
- March 2020 (4)
- February 2020 (4)
- January 2020 (4)
- December 2019 (3)
- November 2019 (2)
- October 2019 (4)
- September 2019 (2)
- August 2019 (4)
- July 2019 (3)
- June 2019 (4)
- May 2019 (2)
- April 2019 (4)
- March 2019 (4)
- February 2019 (5)
- January 2019 (5)
- December 2018 (2)
- November 2018 (2)
- October 2018 (5)
- September 2018 (4)
- August 2018 (3)
- July 2018 (2)
- June 2018 (4)
- May 2018 (3)
- April 2018 (3)
- March 2018 (2)
- February 2018 (2)
- January 2018 (1)
- December 2017 (1)
- November 2017 (2)
- October 2017 (2)
- September 2017 (1)
- August 2017 (2)
- July 2017 (2)
- June 2017 (1)
- April 2017 (3)
- March 2017 (3)
- February 2017 (2)
- January 2017 (2)
- December 2016 (2)
- November 2016 (4)
- October 2016 (4)
- September 2016 (3)
- August 2016 (6)
- July 2016 (4)
- June 2016 (4)
- May 2016 (1)
- April 2016 (3)
- March 2016 (4)
- February 2016 (2)
- January 2016 (4)
- December 2015 (3)
- November 2015 (3)
- October 2015 (1)
- September 2015 (1)
- August 2015 (4)
- July 2015 (6)
- June 2015 (4)
- May 2015 (7)
- April 2015 (6)
- March 2015 (6)
- February 2015 (4)
- January 2015 (3)
CONNECT WITH US
Tag Archives: Supply Chain Disruption
What’s ahead for the life sciences industry? One word: Growth.
Like the focused medical industry, this larger category of all things related to human health research and development experienced an unprecedented period of growth during the pandemic. While that explosion is likely to level off and normalize, life sciences can expect a bright future — albeit with some challenges on the road ahead. They include supply chain disruption, staffing shortages and the increased need to become more efficient in manufacturing to keep up with demand.
Current life sciences trends
The life sciences industry is a big tent, encompassing the development and production of products and services geared toward biology, medicine and health care. We’re talking about pharmaceuticals, biotech, medical devices, clinical research, robotics, genomes and more. Everyone was witness to the great vaccine race of 2020, with big pharma rushing to develop the COVID vaccine. While that moment of urgency has, thankfully, passed, the industry is still feeling the effects of the pandemic, spurring continued growth in intellectual property.
Here are some of the life sciences trends we’re seeing in the industry for the coming year (and beyond).
Digitization
This trend isn’t unique to life sciences, but it’s definitely taking center stage in this industry. Using data analytics, artificial intelligence and machine learning to further personalize health care treatments, gain more meaningful insights, hone and enhance pharmaceuticals and devices, and improve outcomes will remain a focus in the near future and beyond.
M&A
Remember that vaccine race we were talking about? While the worldwide COVID vax panic has passed, the race for newer, better innovations in vaccines, drugs and other pharma intellectual property is still on. Like many other industries, life sciences is feeling the effects of disruption via startups. In life sciences, that means smaller companies that are going full tilt into scientific advancements. Experts believe this trend will drive a significant amount of mergers and acquisitions. Look for big pharma to target small, innovative companies. According to ContractPharma, companies with less than $250 million in revenue are powering innovation in biopharma. By 2026, ContractPharma predicts those companies will account for 60% of biopharma’s growth.
Manufacturing
All of this innovation and M&A activity is predicted to impact manufacturing as well, not only in the area of things like AI and robotics-fueled innovation and the exploding demand for personal medical devices (fueled by the telehealth tsunami) but in good, old fashioned upgrades to facilities, focuses on efficiencies, and the ability to do more with less. Because of all the innovation and increased demand, life sciences manufacturing needs to be lean and mean.
Supply chain disruption
How many of us would love to never hear that phrase again? Yet, it continues to plague almost every industry, from chicken farming to biopharma. In life sciences, it’s about costs, logistics, shortages of the drugs themselves (c’mon Hollywood, stop using Ozempic for weight loss!), and changes in trade policy.
Staffing
Staffing woes are hitting life sciences on all sides. The industry is experiencing challenges finding workers in manufacturing facilities, but it’s not just those frontline employees that are scarce these days. There’s a growing shortage of pharmacists, leading to the very recent announcement that CVS and Walmart are cutting their pharmacy hours in stores nationwide.
All that said, the industry looks bright in the areas of innovation and growth. There will be bumps along the way which include drug shortages, the staffing needed to get those drugs into the hands of patients, as well as the overriding need for manufacturing of drugs, personal health devices and other health equipment to be as efficient as possible. A management consulting firm can help them get there.
Augmenting the Life Sciences industry
At USC Consulting Group, we are operations management consultants who specialize in helping manufacturers, including those in healthcare and life sciences, transform their operations and processes into lean (or Lean) and mean operations, functioning at optimal efficiency levels.
Looking at the current life sciences trends, it’s clear that the M&A push along with supply chain and manufacturing challenges require some introspection of operations management industrywide. With M&As comes due diligence prior to any deal, then the blending of processes, procedures, and even equipment and facilities after the acquisition. Managing that is an enormous job. Combine that with staffing woes and continued supply chain disruption, and it’s easy to see the urgency for efficiency in operations.
Our goal is to improve business performance by increasing productivity and throughput, reducing costs, eliminating waste, improving quality and leveraging existing assets.
To get there, we will typically focus on Lean Six Sigma methodologies, including:
- Reduced Waste: Aggressively minimizing or eliminating anything that does not add value
- Just Right: Right venue, right conditions, right resources
- Self-Sustainment: Culture of improvement without continuous top-level instigation
- Protected: Anticipation of unpredictable and fluctuating demand
- Cost-Management: Provide your organization with the ability to better manage the cost component of delivering quality patient care
One key element in our approach that you may not find elsewhere: We get onto the floor and partner with your employees, the people who are doing the job day to day. We also involve your upper management and C-suite execs to achieve success with a top-down and bottom-up approach.
Whether the end product is high-tech medical devices or branded pharmaceuticals, life sciences companies have much to gain from kicking their manufacturing efficiencies into high gear. This marketplace demands it. The race for innovation is high, and companies need to develop and manufacture product quickly to avoid being left behind.
Our extensive experience in life sciences has helped countless companies implement business intelligence solutions to increase productivity, reduce labor, lower overall operating costs and improve yields and product quality. Our particular expertise covers the clean room environment, packaging methods ranging from multivac to hand assembly, and pharmaceutical delivery methods such as liquid, suspension, gelcaps, tablets and softgels.
We’ll work at every level within your company to deliver improvements that net substantial savings. And we’ll leave you with the knowledge, tools and technology to sustain those improvements over time.
Contact USC Consulting Group today to infuse life back into your operations.
It’s a double-edged sword for the building products industry today.
The production and demand slump during the pandemic has turned into a boom. Residential and commercial building is on a high.
Yet, challenges still exist for the building products industry as it navigates these uncertain economic times.
While each company has its unique issues, our team of subject matter experts have compiled the most common challenges we’re seeing for the building products industry today, and share productive solutions we’re recommending to our clients to tackle them.
Download our free eBook “Constructing the Building Products Industry: An Outlook of Challenges and Solutions” as we advise on tactics to deal with the boom and optimize your operations.
In this eBook you will learn how to overcome the following:
- Rising costs
- Supply chain bottlenecks
- Understaffing & skills gap
- Post-COVID boom
These strategies will help you get started on combating industry challenges and carry you through these uncertain economic times. If you need more in-depth help or would like to discuss specific issues you are experiencing, give us a call today. We listen first and then advise on how we can make your operations more efficient.
Imagine a scenario in which there is unprecedented demand for the products you manufacture, but disruptions in the supply chain are making it difficult, if not impossible, to meet that demand and even if you do, logistics bottlenecks are preventing them from getting where they need to go. Many manufacturers have been running up against this problem since the pandemic began.
Now imagine that people’s very lives literally depend on those products being manufactured and delivered to their destinations.
If you’re in the medical device manufacturing industry, you’re likely thinking: “Welcome to my world.” Not only has it been as hard hit as any other manufacturer by supply chain disruptions and logistic backups, the implications of the resulting shortages of the devices they manufacture may cost people their lives.
The FDA is calling the shortages of medical devices at this critical time a “public health emergency.” It published a device shortage list including the categories of personal protective equipment for medical workers, testing supplies and equipment, and ventilation-related products. The list also outlines the specific products, the estimated duration of the shortage, and the reasons for the shortages, along with what the government is doing about it.
That list is illuminating — and even frustrating — for many reasons, but it’s not all bad news. Among the most common reasons for shortages, including increased demand and supply chain issues, which manufacturers have little control over, there is also one culprit that manufacturers can control: “Requirements for complying with good manufacturing practices.”
As medical device manufacturers know, the FDA has strict compliance requirements that affect every part of the process from designing to manufacturing to testing to shipping, even labeling. In those processes, there can be room for improvement. That’s something manufacturers can do — process improvements to get their products to market faster, while still complying with the FDA.
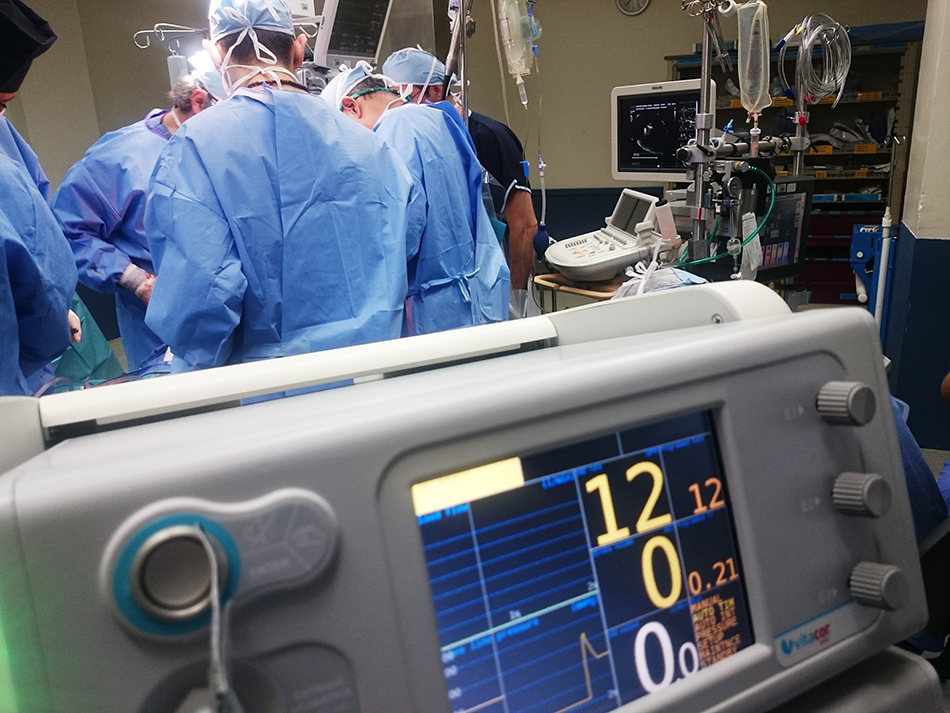
The FDA is calling the shortages of medical devices at this critical time a “public health emergency.”
What medical device manufacturers can do now
At USC Consulting Group, we’ve been helping manufacturers up their operational efficiency for more than 50 years. We analyze what you’re doing, how you’re doing it, and how we can create greater efficiency using your existing resources. A few tactics we’re implementing with our medical manufacturing clients to help mitigate these shortfalls and get their products to people who need them quicker include:
Investigate Lean / Six Sigma
Lean manufacturing is nothing new. The art of maximizing customer value while minimizing waste was pioneered by Henry Ford … or Toyota, depending on who you ask, decades ago. Six Sigma is a newer methodology designed to tackle defects in manufacturing. While Lean looks at making processes more efficient and reducing process lead times, Six Sigma focuses on cutting down on defects that can delay production. In fact, they’ve joined to become one methodology in some circles. Lean techniques help you get product off the line faster, heightening your throughput. Six Sigma strives to target the reason for any defects in the products. These two techniques can conflict — one sure way to cut down on defects is to slow down the process, which runs counter to Lean’s goals. Achieving the perfect balance between the two, and getting the job done faster with fewer defects, is indeed an art form, and worth exploring.
Use SIOP to make your planning and forecasting bulletproof
We recommend using SIOP (Sales, Inventory and Operations Planning) to elevate your planning process to achieve that perfect balance between your supply and demand. You’ve heard of S&OP, a popular business management process that involves sales forecast reports, planning for demand and supply, and other factors. The goal is to help companies get a better, more clear look at their operations and create better-informed strategy decisions, allowing them to deliver what clients need in the most profitable way.
It’s a useful process, but we’ve found a lot of our clients do not include inventory as a strategic tool in their S&OP process. Therefore, they leave the “I” out of SIOP. Adding inventory into the mix is just one additional step, but we find it can be the key to the whole process. When you’re focusing on inventory, it requires more careful planning and elevates the entire planning process up a notch. When your inventory is optimized, which is not an easy mark to hit in these days of supply chain disruption, things tend to fall into place. With SIOP, you can make your inventory work harder for you.
Download our free eBook, “Sales, Inventory and Operations Planning: It’s About Time,” to dive deeper into SIOP.
Involve your frontline employees
We call it the Employee Involvement Prototype (EIP). It’s about engaging with your employees at the machine level and getting good data from the floor. It includes anyone who has to do with the line, and entails taking a look at those operations and processes with input from the men and women who are actually doing the job on an hour-by-hour basis.
Focus on throughput, productivity and yield
Take a good look at what’s happening on the line. What is the “drumbeat”? Are all your functions in sync? Can you improve production by cutting redundant steps?
For more information on these two points, download our whitepaper, “Strategies for Meeting Increasing Customer Demand.” It goes into much more detail about how you can create that proverbial well-oiled machine.
When it comes to caring for people and providing the products they need, time is of the utmost importance. Medical device manufacturers understand they must overcome the worst supply chain disruptions to deliver to the people whose lives depend on them.
Need help? Give us a call. We can save your operations so you can save lives.
Supply chain disruptions have been a major challenge for manufacturers, and show no signs of abating. Here, David Newman, Supply Chain Practice Leader for USC Consulting Group, shares his insights into this pressing issue and offers tactics manufacturers can use to mitigate disruption risks.
QUESTION: “How have supply chains evolved over your career?”
DAVID NEWMAN: A lot has changed since I started in supply chain. 30 years ago the primary focus was on supply base optimization which sowed the seeds for single source supply bases. 20 years ago online retailers began to re-define fulfillment, distribution, and delivery optimization. Over the last 10 years, big data, the internet of things and machine to machine transactions have driven out inefficiencies out of the most competitive supply chains.
QUESTION: “What are the key supply chain concerns facing manufacturing companies today?”
DAVID NEWMAN: Among the three pillars of supply chain, COST, QUALITY, and DELIVERY – Delivery is taking center stage – and specifically, delays caused by disruption. On a trip to China, our driver pointed out of the window and said, “In this Province, China produces 40% of the world’s ceramic tile.” Now, when a highly centralized, efficient supply chain with overseas lead times meets a global pandemic and governments mandate that cities and provinces stay home for a month, there are going to be supply chain disruptions.
QUESTION: “What can Supply Chain Managers do to mitigate supply disruption risks?”
DAVID NEWMAN: Supply chain disruptions cause uncertainty. Generally speaking, there are five types of solutions supply chain managers employ to decrease uncertainty and to improve reliability in their supply chain: There are 1. TIME solutions, 2. PRICING solutions, 3. PRODUCTION solutions, 4. INVENTORY solutions, and 5. INFORMATION solutions.
The most common and easiest to employ are the TIME solutions. Things like expediting freight (which is a supply side response), or delaying order fulfillment (which is a demand side response). But, if your customers have other options and they have low customer loyalty, delaying delivery dates can significantly reduce your revenues. Alternatively, premium freight if you have a low margin product, can wipe out profits.
PRICES for hard to get commodities skyrocket during times of uncertain supply contributing to cost inflation. If these costs can’t be passed on to customers, margins suffer. Time and price-based solutions tend to be the easiest and quickest solutions, which is why they are most often employed in emergency situations.
PRODUCTION solutions include flexible manufacturing and quick changeover practices, having alternative suppliers and substitute materials, reducing quality rejects in order to have more saleable product, and improving the source, make and deliver cycle times. These solutions are effective during times of certain supply, but when dealing with disruptions, they’re often too little, too late.
QUESTION: “Why don’t companies just increase stockpiles?”
DAVID NEWMAN: Increasing INVENTORIES is a common response to disruptions, however there are often constraints in the warehouse and storage space. Excessive inventories drain cash and they tie up working capital. Times of uncertainty require regular reorder point and order quantity reviews in light of changing lead time demands. We find too often that manufacturers will rely on their suppliers for reorder points and order quantities. A better practice is to use statistical analysis to evaluate how changing lead times are affecting the reorder points and order quantities in your ERP system. The best practice utilizes machine-to-machine learning algorithms that update automatically according to consumption data and lead time data.
QUESTION: “What new types of information do responsive supply chain employ?”
DAVID NEWMAN: Uncertainty is nothing more than the absence of correct and timely INFORMATION. Executing on technology and process solutions to improve supply chain information is sometimes viewed as expensive, however it is rarely more expensive than increasing investments in facilities and equipment, or habitually discounting obsolete inventory, or perpetually incurring premium freight.
Some commonly used practices and tools to improve supply chain information include embedding a strong SIOP process – Sales, Inventory, and Operations Planning. Conducting Value Stream Maps to understand the tiered network of the supply chain, implementing strong Supplier Scorecards, and having a robust Risk Register process where there are early warning systems, contract optionality, and redundancies in the supply base, especially around critical parts and materials.
QUESTION: “Can’t I just rely on my Strategic Suppliers to keep me stocked?”
DAVID NEWMAN: Although supply chains have been improved significantly in the past 30 years with technology, supply chain disruptions are still managed by people. Developing key relationships with your strategic suppliers will ensure that there’s someone on the other end of the phone when you call regarding delivery dates. However, if daily phone calls is your go-to strategy, it’s not enough to ensure continuity in supply in our increasingly complex and disruptive supply chains.
How could your company benefit if presently disjointed internal functions and your supply chain partners shared connected, real-time information?
What if your team had data driven, scenario analysis tools to make rapid responses that provide optimum outcomes?
What if the supply chain drivers that most affect your business performance were translated into metrics for operations and supply chain accountability?
If your company needs help reducing supply disruptions, turn to the supply chain experts at USC Consulting Group. We have been empowering our clients’ performance for over 50 years.