-
Subscribe to Blog:
SEARCH THE BLOG
CATEGORIES
- Aerospace
- Asset Maintenance
- Automotive
- Blog
- Building Products
- Case Studies
- Chemical Processing
- Consulting
- Food & Beverage
- Forestry Products
- Hospitals & Healthcare
- Knowledge Transfer
- Lean Manufacturing
- Life Sciences
- Logistics
- Manufacturing
- Material Utilization
- Metals
- Mining
- News
- Office Politics
- Oil & Gas
- Plastics
- Private Equity
- Process Improvement
- Project Management
- Spend Management
- Supply Chain
- Uncategorized
- Utilities
- Whitepapers
BLOG ARCHIVES
- August 2025 (2)
- July 2025 (2)
- June 2025 (4)
- May 2025 (1)
- April 2025 (1)
- March 2025 (1)
- February 2025 (4)
- January 2025 (4)
- December 2024 (4)
- November 2024 (2)
- October 2024 (6)
- September 2024 (5)
- August 2024 (5)
- July 2024 (6)
- June 2024 (3)
- May 2024 (3)
- April 2024 (4)
- March 2024 (3)
- February 2024 (4)
- January 2024 (5)
- December 2023 (2)
- November 2023 (1)
- October 2023 (6)
- September 2023 (3)
- August 2023 (4)
- July 2023 (2)
- June 2023 (3)
- May 2023 (7)
- April 2023 (3)
- March 2023 (3)
- February 2023 (5)
- January 2023 (6)
- December 2022 (2)
- November 2022 (5)
- October 2022 (5)
- September 2022 (5)
- August 2022 (6)
- July 2022 (3)
- June 2022 (4)
- May 2022 (5)
- April 2022 (3)
- March 2022 (5)
- February 2022 (4)
- January 2022 (7)
- December 2021 (3)
- November 2021 (5)
- October 2021 (3)
- September 2021 (2)
- August 2021 (6)
- July 2021 (2)
- June 2021 (10)
- May 2021 (4)
- April 2021 (5)
- March 2021 (5)
- February 2021 (3)
- January 2021 (4)
- December 2020 (3)
- November 2020 (3)
- October 2020 (3)
- September 2020 (3)
- August 2020 (4)
- July 2020 (3)
- June 2020 (5)
- May 2020 (3)
- April 2020 (3)
- March 2020 (4)
- February 2020 (4)
- January 2020 (4)
- December 2019 (3)
- November 2019 (2)
- October 2019 (4)
- September 2019 (2)
- August 2019 (4)
- July 2019 (3)
- June 2019 (4)
- May 2019 (2)
- April 2019 (4)
- March 2019 (4)
- February 2019 (5)
- January 2019 (5)
- December 2018 (2)
- November 2018 (2)
- October 2018 (5)
- September 2018 (4)
- August 2018 (3)
- July 2018 (2)
- June 2018 (4)
- May 2018 (3)
- April 2018 (3)
- March 2018 (2)
- February 2018 (2)
- January 2018 (1)
- December 2017 (1)
- November 2017 (2)
- October 2017 (2)
- September 2017 (1)
- August 2017 (2)
- July 2017 (2)
- June 2017 (1)
- April 2017 (3)
- March 2017 (3)
- February 2017 (2)
- January 2017 (2)
- December 2016 (2)
- November 2016 (4)
- October 2016 (4)
- September 2016 (3)
- August 2016 (6)
- July 2016 (4)
- June 2016 (4)
- May 2016 (1)
- April 2016 (3)
- March 2016 (4)
- February 2016 (2)
- January 2016 (4)
- December 2015 (3)
- November 2015 (3)
- October 2015 (1)
- September 2015 (1)
- August 2015 (4)
- July 2015 (6)
- June 2015 (4)
- May 2015 (7)
- April 2015 (6)
- March 2015 (6)
- February 2015 (4)
- January 2015 (3)
CONNECT WITH US
Tag Archives: Software as a Service
Thanks to cloud and edge computing, SaaS — software as a service — has become a highly transformative technology in both manufacturing and the supply chain. It makes software systems and various technologies accessible to a wide range of operations, big or small. That’s because the system itself is hosted remotely, so the central technologies don’t have to be on the premises or within a facility. SaaS tools are fully built cloud applications.
Picture the type of software that governs a sophisticated manufacturing system. The servers that host that software, and where most of the data is contained, are located off-property away from the manufacturer’s facility. At any time, it can communicate with the connected equipment, and users can access the entire system remotely as well.
However, it’s maintained, serviced, and even secured by a remote provider. The only thing the manufacturer has to worry about is whether or not the connected equipment is running optimally. They don’t have to manage an on-site data center, update servers and software configurations, or even troubleshoot major problems — that’s all done by the SaaS provider.
SaaS is innovative, but how does that system affect the manufacturing industry as a whole? What are the benefits of SaaS when deployed within a smart factory or Industry 4.0 environment?
1. Reduced Costs
Manufacturing software comes in many forms. There are tools to aid in engineering and design, sales or marketing, measure production quality, organize finances, and much more. Each one of those applications requires a steady stream of data and a team to manage both the software and its backend.
Just imagine how much processing power is necessary to handle all of those systems, let alone the physical storage needed to contain the resulting data to keep it all running. The best solution even today is to build a data center, whether on-site or remote. They are very costly to manage and maintain.
SaaS solutions eliminate those costs and requirements because the bulk of the system is hosted elsewhere, on the provider’s servers. There’s no equipment to install and no software to update or manage. It’s all done off-site. That also reduces the need for a large IT or software development team on the manufacturing side.
The kickback is much lower operating costs for manufacturers, despite all the benefits realized from the applications.
2. Better Security
When you need a process completed, but you don’t have the proper knowledge, the common practice is to call in a specialist. That is precisely what SaaS providers are, and it means they have access to highly specific resources and tools that no manufacturer realistically does. That translates to a better solution overall, especially when it comes to digital and data security.
Because their entire business is securing and maintaining their data centers, to provide software to clients, they have much more sophisticated and capable solutions in place. That filters down to the manufacturers subscribing to SaaS services, who realize better data security and smarter digital protections.
3. Unparalleled Flexibility
Manufacturers maintaining software and technology solutions in-house have to scale up when the operation grows, which can be devastating depending on how the market shifts and demand fluctuates. Spending hundreds of thousands to upgrade equipment only to experience a downturn in the market can ruin any business.
SaaS providers handle scaling and delivery. They can add new terminals and new users, and install or activate servers to accommodate their clients. This is not only done seamlessly, but it will also happen near-instantly. Customers can even try before they buy, trialing the services and solutions before deploying them within their facilities. If the software doesn’t work out or add value, it can be canceled at any time with a minimal impact on the greater operation.
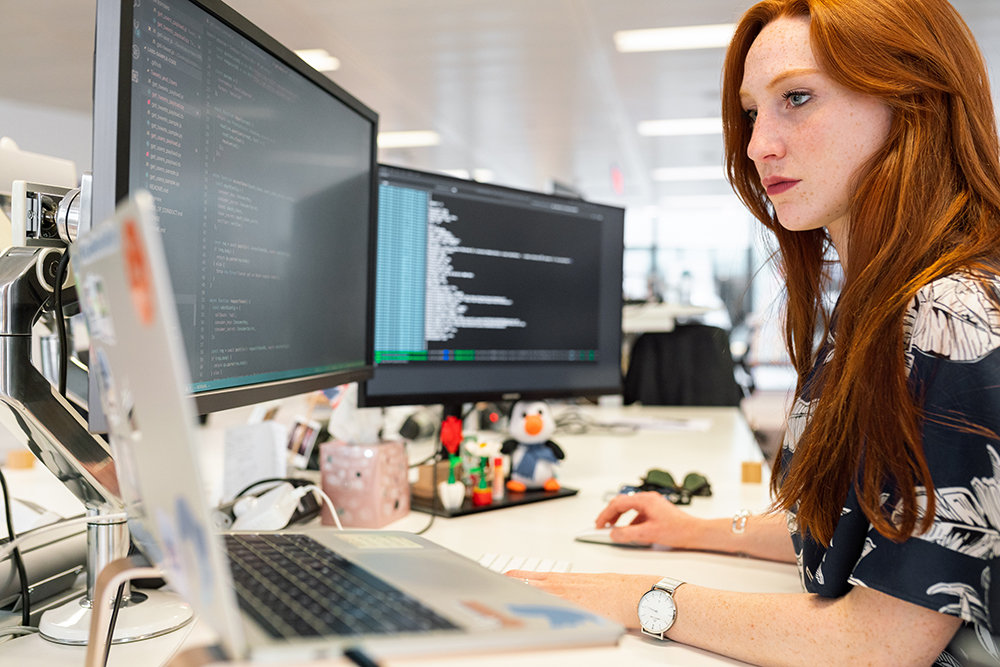
SaaS solutions can be accessed anywhere at any time allowing for more flexible operations.
4. Enhanced Interoperability
Typically, two pieces of distinct software cannot communicate with each other and the data they utilize isn’t guaranteed to be interchangeable. In manufacturing, this happens a lot with ERP and CMMS solutions. It complicates manufacturer-vendor relationships, especially when the default systems offer no interoperability.
Because SaaS solutions are hosted in the cloud, the systems accommodate interconnection between many different tools and platforms. CMMS, ERP, CRM, and project management tools can all communicate and share data, and the SaaS platform ensures it’s compatible and readable between those solutions.
5. Truly Agile Operations
If you look at what SaaS solutions provide manufacturers from a top-down perspective, it affords many operational efficiencies and creates new opportunities, without increasing the responsibilities the manufacturer is forced to take on. They have everything to gain and almost nothing to lose. Faster and more agile operations are implemented as a result, thanks to a system that’s always on, always ready to scale, and constantly being adapted to the needs of the manufacturer.
6. A Mobile Workforce
Because of the way SaaS solutions are maintained and delivered, they open up a whole new level of accessibility and mobility for manufacturing teams. Everyone from the decision-makers and supervisors to equipment operators gain access to on-demand and mobile-friendly solutions that can be accessed anywhere, at any time.
Additional features include mobile and real-time notifications, instant communication even between departments, remote access to mission-critical applications, and much more. Besides, security is managed on the backend, server-side, so users can move from terminal to terminal, or device to device, without compromising the system.
The caveat is that they need to follow proper security protocols, which means no password sharing or reuse, and precise authentication or verification systems.
An Ever-Evolving Industry Requires Adaptable Solutions
SaaS solutions are changing the manufacturing and production industries, but it’s not the only technology making a dent in normal operations. The entire field is undergoing a revolution, moving ever closer to Industry 4.0. The concept will see a marriage of advanced manufacturing techniques and smart, contextually-driven platforms to achieve seamless intercommunication, efficiency, and operability.
Software as a service plays a role in that movement, as manufacturers look to offset some of the requirements of the digital transformation. SaaS allows manufacturers to keep up with ever-evolving industries and markets. It reduces operational costs, speeds up output and processes, enhances security, improves software compatibility, and helps facilitate truly agile operations. What more could you ask for?
This article is written by Devin Partida. Devin is a tech writer with an interest in the IIoT and manufacturing. She is also the Editor-in-Chief of ReHack.com.