-
Subscribe to Blog:
SEARCH THE BLOG
CATEGORIES
- Aerospace
- Asset Maintenance
- Automotive
- Blog
- Building Products
- Case Studies
- Chemical Processing
- Consulting
- Food & Beverage
- Forestry Products
- Hospitals & Healthcare
- Knowledge Transfer
- Lean Manufacturing
- Life Sciences
- Logistics
- Manufacturing
- Material Utilization
- Metals
- Mining
- News
- Office Politics
- Oil & Gas
- Plastics
- Private Equity
- Process Improvement
- Project Management
- Spend Management
- Supply Chain
- Uncategorized
- Utilities
- Whitepapers
BLOG ARCHIVES
- April 2025 (1)
- March 2025 (1)
- February 2025 (4)
- January 2025 (4)
- December 2024 (4)
- November 2024 (2)
- October 2024 (6)
- September 2024 (5)
- August 2024 (5)
- July 2024 (6)
- June 2024 (3)
- May 2024 (3)
- April 2024 (4)
- March 2024 (3)
- February 2024 (4)
- January 2024 (5)
- December 2023 (2)
- November 2023 (1)
- October 2023 (6)
- September 2023 (3)
- August 2023 (4)
- July 2023 (2)
- June 2023 (3)
- May 2023 (7)
- April 2023 (3)
- March 2023 (3)
- February 2023 (5)
- January 2023 (6)
- December 2022 (2)
- November 2022 (5)
- October 2022 (5)
- September 2022 (5)
- August 2022 (6)
- July 2022 (3)
- June 2022 (4)
- May 2022 (5)
- April 2022 (3)
- March 2022 (5)
- February 2022 (4)
- January 2022 (7)
- December 2021 (3)
- November 2021 (5)
- October 2021 (3)
- September 2021 (2)
- August 2021 (6)
- July 2021 (2)
- June 2021 (10)
- May 2021 (4)
- April 2021 (5)
- March 2021 (5)
- February 2021 (3)
- January 2021 (4)
- December 2020 (3)
- November 2020 (3)
- October 2020 (3)
- September 2020 (3)
- August 2020 (4)
- July 2020 (3)
- June 2020 (5)
- May 2020 (3)
- April 2020 (3)
- March 2020 (4)
- February 2020 (4)
- January 2020 (4)
- December 2019 (3)
- November 2019 (2)
- October 2019 (4)
- September 2019 (2)
- August 2019 (4)
- July 2019 (3)
- June 2019 (4)
- May 2019 (2)
- April 2019 (4)
- March 2019 (4)
- February 2019 (5)
- January 2019 (5)
- December 2018 (2)
- November 2018 (2)
- October 2018 (5)
- September 2018 (4)
- August 2018 (3)
- July 2018 (2)
- June 2018 (4)
- May 2018 (3)
- April 2018 (3)
- March 2018 (2)
- February 2018 (2)
- January 2018 (1)
- December 2017 (1)
- November 2017 (2)
- October 2017 (2)
- September 2017 (1)
- August 2017 (2)
- July 2017 (2)
- June 2017 (1)
- April 2017 (3)
- March 2017 (3)
- February 2017 (2)
- January 2017 (2)
- December 2016 (2)
- November 2016 (4)
- October 2016 (4)
- September 2016 (3)
- August 2016 (6)
- July 2016 (4)
- June 2016 (4)
- May 2016 (1)
- April 2016 (3)
- March 2016 (4)
- February 2016 (2)
- January 2016 (4)
- December 2015 (3)
- November 2015 (3)
- October 2015 (1)
- September 2015 (1)
- August 2015 (4)
- July 2015 (6)
- June 2015 (4)
- May 2015 (7)
- April 2015 (6)
- March 2015 (6)
- February 2015 (4)
- January 2015 (3)
CONNECT WITH US
Tag Archives: Safety Measures
Vaccine rollout is well underway in the U.S., painting a positive picture for the future. Still, it will take time for everyone to be fully vaccinated, and even then, COVID-19 safety protocols could linger for a while. In the meantime, workplaces can turn to automation to improve their anti-COVID-19 measures.
Temperature checks, social distancing, and mask mandates have become standard across many businesses. While necessary, enforcing these protocols can limit facilities’ productivity, as they rely on staff who could otherwise work on value-adding tasks. Since many companies had to reduce their active workforce by 39% on average, they need to improve productivity wherever possible.
Automating COVID-19 safety protocols also further removes employees from situations where they could contract the virus. Automation minimizes or eliminates close contact between workers during things like temperature checks.
Here’s how you can automate COVID-19 safety measures to stay safe and raise productivity.
1. Install Body Temperature Cameras
Temperature checks are one of the most common anti-COVID-19 measures, but they typically require close contact. Some businesses have found a way around this by installing thermal camera systems by employee entrances. These systems, which resemble metal detectors, scan worker temperatures as they walk, alerting relevant parties if they’re feverish.
Setting these systems up may be expensive at first, but you gain productivity in the process. The employee who would’ve performed temperature checks can instead work as usual, making your workplace more productive. Since these cameras can scan 30 people at once, they’re also more efficient than human-run checks.
Similar cameras throughout the workspace can detect if an employee develops a high temperature at work. You can then investigate further to determine if they need to go home or not.
2. Distribute Wearables for Social Distancing
Maintaining at least a 6-foot distance between workers is another crucial step in preventing COVID-19 outbreaks. Instituting a social distancing policy by itself isn’t enough to ensure people stay distant. It’s not economical to have managers monitor employees, either, so automation is the ideal solution.
Many warehouses and factories have turned to wearable technology to facilitate social distancing. These devices alert employees when they come within six feet of one another through noises and vibrations. These alerts are particularly helpful in areas with limited visibility where workers may not see each other.
You can’t expect to enforce social distancing by having managers roam the workspace. They can’t feasibly cover enough ground, and they could be working on more valuable tasks instead. Using wearables to maintain distance lets you keep employees safe without sacrificing productivity.
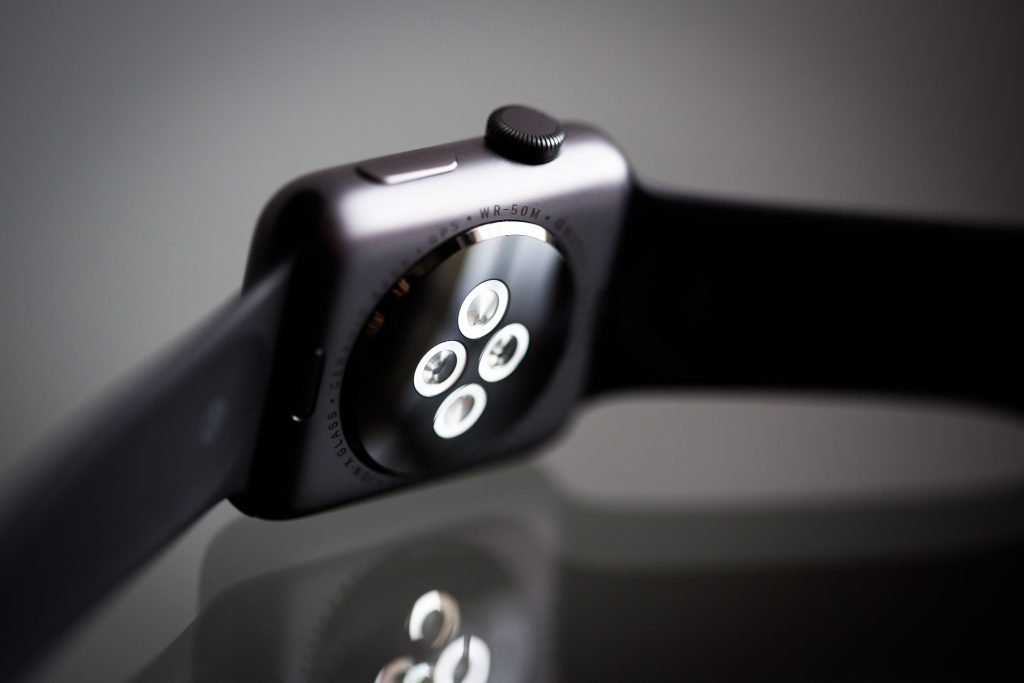
Photo by Torsten Dettlaff from Pexels
3. Use AI Cameras to Detect Masks
Masks are one of the simplest yet most effective ways to minimize the spread of COVID-19. Like with other regulations, though, mask mandates are only effective to the extent that employees comply with them. AI-enabled camera systems can detect if workers are wearing masks or not.
Machine vision systems can analyze video footage to see if anyone isn’t wearing a mask when they should be. You could deploy these with facial recognition to identify non-masked employees, but you may run into privacy concerns. An alternative would be a system that alerts managers when someone isn’t wearing a mask so they can look into it.
No matter what type of cameras you use, you should make sure your employees know about it. Privacy laws forbid employers from placing hidden cameras in private areas, and workers must know if and when you are recording them. Keep these factors in mind so you can protect employees from COVID-19 while preserving privacy rights.
4. Employ Sanitation Robots
Sanitation has found itself in the spotlight throughout the pandemic. Many businesses have adopted new cleanliness standards to eliminate cross-contamination and disease spreading through shared surfaces. Most companies pursue this by hiring cleaning crews or requiring workers to clean more frequently, which isn’t efficient.
A more cost-effective measure is to use sanitation robots. These automated cleaners are typically expensive but represent savings in the long run. Some take just 12 minutes to disinfect an area that would take a human worker more than an hour.
When you factor in how much it would take to pay a cleaning service over several months, the robots are more cost-efficient. Automation in this area also keeps people away from potentially contaminated surfaces, improving workplace health.
5. Implement Access Controls
Knowing where all employees are at any given time facilitates easier and more accurate contact tracing. Partitioning a workspace into separate zones can also help enable social distancing. To enforce these protocols more efficiently, you can use electronic access controls.
You can install locks that only open when workers scan their IDs. When employees have to scan into an area, you have a record of who was where if an outbreak occurs. You can then alert any other employees who might’ve contracted the virus so they can quarantine.
You could post workers by the doors to record who goes in and out, but that would be highly inefficient. Automatic access controls help ensure everyone working that day is adding value to the company.
Automation Improves Safety and Efficiency Amid COVID-19
Automating COVID-19 safety protocols lets you stay safe and maintain productivity. These solutions may come at a higher upfront cost, but their safety and efficiency benefits are impossible to ignore. They will also continue to help after the pandemic fades, ensuring productivity while preventing diseases like the flu.
COVID-19 has wreaked havoc on many businesses, but you can take measures to mitigate it. These five automation options will help keep your employees safe and efficient.
This article is written by Devin Partida. Devin is a tech writer with an interest in the IIot and manufacturing. She is also the Editor-in-Chief of ReHack.com.