-
Subscribe to Blog:
SEARCH THE BLOG
CATEGORIES
- Aerospace
- Asset Maintenance
- Automotive
- Blog
- Building Products
- Case Studies
- Chemical Processing
- Consulting
- Food & Beverage
- Forestry Products
- Hospitals & Healthcare
- Knowledge Transfer
- Lean Manufacturing
- Life Sciences
- Logistics
- Manufacturing
- Material Utilization
- Metals
- Mining
- News
- Office Politics
- Oil & Gas
- Plastics
- Private Equity
- Process Improvement
- Project Management
- Spend Management
- Supply Chain
- Uncategorized
- Utilities
- Whitepapers
BLOG ARCHIVES
- July 2025 (1)
- June 2025 (4)
- May 2025 (1)
- April 2025 (1)
- March 2025 (1)
- February 2025 (4)
- January 2025 (4)
- December 2024 (4)
- November 2024 (2)
- October 2024 (6)
- September 2024 (5)
- August 2024 (5)
- July 2024 (6)
- June 2024 (3)
- May 2024 (3)
- April 2024 (4)
- March 2024 (3)
- February 2024 (4)
- January 2024 (5)
- December 2023 (2)
- November 2023 (1)
- October 2023 (6)
- September 2023 (3)
- August 2023 (4)
- July 2023 (2)
- June 2023 (3)
- May 2023 (7)
- April 2023 (3)
- March 2023 (3)
- February 2023 (5)
- January 2023 (6)
- December 2022 (2)
- November 2022 (5)
- October 2022 (5)
- September 2022 (5)
- August 2022 (6)
- July 2022 (3)
- June 2022 (4)
- May 2022 (5)
- April 2022 (3)
- March 2022 (5)
- February 2022 (4)
- January 2022 (7)
- December 2021 (3)
- November 2021 (5)
- October 2021 (3)
- September 2021 (2)
- August 2021 (6)
- July 2021 (2)
- June 2021 (10)
- May 2021 (4)
- April 2021 (5)
- March 2021 (5)
- February 2021 (3)
- January 2021 (4)
- December 2020 (3)
- November 2020 (3)
- October 2020 (3)
- September 2020 (3)
- August 2020 (4)
- July 2020 (3)
- June 2020 (5)
- May 2020 (3)
- April 2020 (3)
- March 2020 (4)
- February 2020 (4)
- January 2020 (4)
- December 2019 (3)
- November 2019 (2)
- October 2019 (4)
- September 2019 (2)
- August 2019 (4)
- July 2019 (3)
- June 2019 (4)
- May 2019 (2)
- April 2019 (4)
- March 2019 (4)
- February 2019 (5)
- January 2019 (5)
- December 2018 (2)
- November 2018 (2)
- October 2018 (5)
- September 2018 (4)
- August 2018 (3)
- July 2018 (2)
- June 2018 (4)
- May 2018 (3)
- April 2018 (3)
- March 2018 (2)
- February 2018 (2)
- January 2018 (1)
- December 2017 (1)
- November 2017 (2)
- October 2017 (2)
- September 2017 (1)
- August 2017 (2)
- July 2017 (2)
- June 2017 (1)
- April 2017 (3)
- March 2017 (3)
- February 2017 (2)
- January 2017 (2)
- December 2016 (2)
- November 2016 (4)
- October 2016 (4)
- September 2016 (3)
- August 2016 (6)
- July 2016 (4)
- June 2016 (4)
- May 2016 (1)
- April 2016 (3)
- March 2016 (4)
- February 2016 (2)
- January 2016 (4)
- December 2015 (3)
- November 2015 (3)
- October 2015 (1)
- September 2015 (1)
- August 2015 (4)
- July 2015 (6)
- June 2015 (4)
- May 2015 (7)
- April 2015 (6)
- March 2015 (6)
- February 2015 (4)
- January 2015 (3)
CONNECT WITH US
Tag Archives: Preventative Maintenance
Poor asset management can result in significant financial losses beyond the cost of replacement, with reputational damage, compromised data, and operational disruption a few of many risks involved. Effective asset management, on the other hand, is essential for businesses across industries, with advantages that include increased productivity, elevated asset utilization, and minimal downtime, The Enterprise World highlights. For organizations that aim to enhance their asset management process, the perfect balance of key strategies is a must — especially when the goal is to better manage the return and disposal of physical assets.
Preventative maintenance as a front line defense
For companies that manage assets like physical tech equipment, a strategy that focuses on maintenance is essential in order to maintain assets that are in optimal working condition at all times. Further advantages include asset longevity, reduced maintenance costs over time, and greater operational efficiency. Due to the value that preventative maintenance can bring, businesses must consider the strategy as a valuable front line defense in an asset’s life cycle.
While manual, routine inspections are crucial to an effective asset maintenance strategy, technology now plays an indisputable role in predictive maintenance and asset management as a whole. Artificial intelligence (AI) is just one technology that is gaining traction in asset management. For example, AI algorithms can process large amounts of data in order to predict maintenance issues and generate optimal schedules for maintenance — all the while factoring in an asset’s previous maintenance data. This can prove to be particularly beneficial for organizations that possess a significant number of assets (such as many laptop computers). When combined with efforts like manual asset tracking, businesses can rest easy in knowing that everything is accounted for, in good condition, and up-to-date on routine maintenance.
A streamlined return process
Effective equipment tracking is essential for any business with physical assets. Today, equipment management endeavors go well beyond a simple spreadsheet, and will typically involve the combined use of both physical tracking options (like barcodes or equipment tags). Software is another essential element, as asset management software provides a deeper look into the valuable details associated with physical assets. This technology will not only provide an overview of the assets that a business has, but details in regard to maintenance history and location (to highlight a couple of insights).
Businesses that have a well-defined asset tracking approach can easily overlook the complex nature of certain parts of the asset management process. For example, the return process can often involve several kinks along the way, such as employees that fail to send back company equipment, or inefficient shipping which can result in untimely delays. As such, effective equipment tracking does extend to a successful equipment return process. This is especially crucial for companies that routinely ‘loan out’ technology to their employees — a lost laptop is just one asset that can create a ripple effect for a business. In addition to lost productivity and the cost of replacement, the company may also have to shoulder the cost associated with a data breach, a factor that further underlines the importance of an effective return process. In addition to clear instructions, it’s essential that a business has a strategy in place to streamline the return. In addition to a trustworthy equipment management system and staying on top of paperwork (such as custom fees, etc.), aspects like consistent tracking updates throughout the shipping process can make a major difference.
Asset disposal can be a sustainable process
The integration of technology can elevate an asset management strategy by enabling businesses to continuously optimize maintenance schedules and elevate the return process. In turn, companies can minimize the downtime of assets, and benefit from equipment that will go the mile. When assets are truly no longer useful, however, businesses must abide by an effective disposal strategy. In many cases, there are sustainable approaches that can underline further advantages, such as environmental benefits or supporting the local community.
In some cases, a business may wish to donate old equipment (like computers, printers, etc.) to schools in order to support the local community. Businesses may wish to explore other options as well, such as the ability to refurbish and sell their equipment. Recycling old tech is another solution, and can be a sustainable option for equipment that is truly at the end of its life cycle. Before old tech leaves the hands of a business, however, it’s crucial to gain a full understanding of the laws, regulations, and the additional considerations that are involved. For example, businesses that wish to recycle their tech will need to comply with e-waste disposal laws. Other tasks are equally as necessary, such as a thorough asset inventory, the proper and secure destruction of any sensitive information (including GDPR compliance where applicable). Enlisting the help of a certified and professional Information Technology Asset Disposition (ITAD) provider can be a great option that can help guide a business through the process.
Poor management of physical assets brings to light a number of stark consequences for a business, from unnecessary financial losses to lessened efficiency overall. A balance between technology driven solutions and smart considerations, however, can make for an elevated management process even where asset return and disposal are concerned.
*This article is written by Lottie Westfield. Lottie spent more than a decade working in quality management in the automotive sector before taking a step back to start a family. She has since reconnected with her first love of writing and enjoys contributing to a range of publications, both print and online.
Downtime – the dreaded halt in production that can cripple a manufacturing operation. It’s more than just an inconvenience; it’s a hidden cost that can eat away at your profits. A recent study revealed that nearly 82% of businesses have experienced unexpected downtime in the past three years, with the average incident lasting four hours and costing a staggering $2 million. The impact goes beyond just financial losses – downtime can disrupt customer deliveries, delay critical projects, and erode trust with clients.
The Potential Culprits
One major factor is neglecting preventive maintenance. Regular servicing not only keeps equipment functioning smoothly but also allows technicians to identify potential problems before they snowball into major breakdowns.
Another hidden source is outdated equipment. Obsolete machinery can be a drag on your entire production line. Imagine a slow, malfunctioning piece of equipment holding up the entire process. This can put undue stress on other machines, leading to premature wear and tear, and ultimately, more downtime. Upgrading to newer, more efficient models can significantly improve production flow and reduce the risk of breakdowns. Outdated software can also be a culprit. Running outdated software can lead to compatibility issues with newer systems and leave your facility vulnerable to security breaches.
Beyond equipment and software, a lack of proper training for your workforce can also contribute to downtime. If operators don’t fully understand how a machine works, they might misuse it, leading to errors and breakdowns. Investing in comprehensive training empowers your employees with the knowledge and skills they need to operate machinery safely and efficiently, minimizing the risk of operator-induced downtime.
Finally, the importance of data tracking cannot be overstated. Keeping detailed logs of equipment issues and production hiccups allows you to identify recurring problems and implement preventative measures. Think of it as a historical record that helps you anticipate and address potential bottlenecks before they derail your production schedule.
Finding the Right Solution for You
The good news is that there are steps you can take to combat downtime and keep your production lines humming. Conducting risk audits to identify potential problems, installing sensors to monitor equipment health (like a torque transducer that detects excessive force on a rotating shaft), and implementing a comprehensive preventive maintenance program are all crucial steps in the battle against downtime.
Investing in employee training and partnering with reliable third-party service providers can further strengthen your defenses. By adopting a proactive approach to maintenance and addressing the root causes of downtime, you can significantly reduce disruptions and ensure your manufacturing operation runs smoothly and efficiently.
Want to learn more about the specific costs associated with different downtime causes? The following infographic breaks down the financial impact of various downtime triggers, helping you identify areas for improvement and optimize your production process for maximum uptime.
Does it seem like you’re always putting out fires? Not in the literal sense, of course. We’re talking about operations problems and snafus that seem to pop up at the most inconvenient times. Machines break down. Workers call in sick. Human errors can result in costly fixes. Unforeseen backups or bottlenecks slowing things down. Too much inventory. Not enough inventory. Some days, it can seem like you’re in a constant state of troubleshooting. The problem with that is, it’s hard to move forward into tomorrow when you’re consumed with putting out the fires of today.
Sound familiar? You’re not alone. At USC Consulting Group, we hear it a lot from the clients we partner with to increase efficiency and streamline operations at their facilities. Over the years, we’ve learned that the best course of action to break the cycle of constantly putting out fires is to get ahead of those problems before they become “fires.” Easier said than done, right? Actually, no. The way to do it is to implement an effective Management Operating System (MOS).
MOS 101
What is a Management Operating System, or MOS? Without using industry jargon, a MOS is simply a structured approach to operations. It’s intentional, forward-looking and at times anticipatory, in that it can help spot trouble before it spots you.
A good MOS is a set of tools, processes and frameworks that guide the operations of your business, namely the way employees work. It fosters continuous improvement to address issues as they occur. Or, ideally, before they occur.
Because many of the “fires” you’re stamping out every day can range from production shortfalls to problems related to worker safety, companies that use production lines or have other types of hazardous workplace environments commonly employ management operating systems.
Your MOS should be able to spot inefficiencies in an operating system before they become major problems. This ensures that adjustments can be made so operations are not adversely affected. An MOS should also use real-time feedback so an organization can safely direct operations, funding and other resources to maximize return on investment.
The best management operating systems center around four main components:
- Processes
- Systems
- Roles
- Structures
In other words, it maps out how the job gets done, in what way and by whom.
Let’s look at that in a little more detail.
When designing processes, businesses must be sure that they’re safe, secure and clear for employees to understand and tools are used to support operations — and never in ways that are not dictated by the overall structure. This means users should not use tools in inappropriate ways, especially those that could simply automate their inefficient methods. One process change we always recommend is preventative maintenance. Taking a little downtime today to service your machines can save major work stoppages tomorrow.
An effective MOS uses well-designed systems that help employees and the company as a whole achieve goals, which means they should run smoothly and enhance and even boost established efficiency.
Roles within an MOS should adhere to clearly defined job descriptions that require certain skill sets, and when combined with a business’ processes and systems can best utilize talents. The skills gap has only complicated the matter, but that’s fodder for another blog.
The best-run management operating systems always establish a business-wide structure upon which the different roles within the company interact. This is usually done last because it ensures that the processes do not dictate the entire established structure and cause further issues.
Read more about it in our blog, “How Can a Management Operating System Help Your Organization?”
Benefits of using a good MOS
Putting a carefully planned management operating system in place, one that is unique to your organization and its challenges and strengths, can result in a boatload of positive benefits. According to CEO Magazine, an MOS allows for an organization to “better control the flow of work and production, driving higher outcomes in customer service, quality and cost.”
At a minimum, these systems make use of tools that allow organizations to create plans for future work in certain operations, carry out that work, and then measure the work performance data to suggest future improvements that could be needed.
At maximum? Your company will perform with operational excellence, humming along at capacity, anticipating hiccups before they become problems, planning for growth or even downturns so you won’t be taken by surprise and generally making your life easier and your bottom line stronger.
Other ways an MOS can benefit you and your company:
- Cost savings
- Waste reduction
- Increased product quality
- Identification of workflow gaps
- Find ways to improve efficiency
- Get a handle on any compliance issues or regulations
- Elimination of impediments to your workflow
- Inventory wrangling (so you don’t have too much or too little despite supply chain bottlenecks)
A word about technology. Sure, you can automate your management operating system. Many companies do. But in our opinion, it can’t match good, old-fashioned brainpower, experience garnered through years on the line, common sense of longtime employees and forward-thinking ideas.
Ready to stop the firefighting mentality and talk about it? Give us a call or email us at info@usccg.com. We’ll listen first and then collaborate with you on a path toward operational excellence. It’s what we do.
Are you performing preventive maintenance on a regular basis? If you’re not, you may want to consider adding it to your schedule. Why? In a word, it’s about efficiency. In a few words (as its name suggests), it prevents problems before they start. Preventive maintenance is becoming the manufacturing industry standard. Roughly 80% of asset and facilities stakeholders are embracing the process as a way to cut costs, increase efficiency, and keep assets running like clockwork.
By performing regular preventive maintenance (or its cousin, data-based predictive maintenance) you are heading off problems, snafus and breakdowns at the pass. It’s about identifying and handling any potential issues that may be lurking down the road. The point is to find potential problems before they become real problems that could lead to delays and costly headaches.
The irony of preventive maintenance is that it can sometimes seem like it causes more problems than it solves. It requires regular downtime, which in itself is a problem. There’s also the tricky matter of timing. Finding the optimal time to perform the maintenance can be a delicate balance between shutting down for maintenance too soon and waiting too long.
But, the challenges are worth the rewards. Ensuring you have the proverbial well-oiled machine will make your operation more efficient and productive now and in the future.
Let’s take a look at preventive maintenance benefits and challenges and how it can help boost your operations.
Preventive maintenance benefits
The idea behind doing regular maintenance on the lifeblood of your manufacturing operations — your machinery — is to keep it humming along at optimal efficiency and prevent any problems that might occur. Benefits to making it a regular part of your business process include:
You control the downtime schedule. It’s true that performing maintenance requires downtime. You’ll experience a work stoppage because of it. However, the good news is, when that downtime happens is up to you. You can schedule it for slow periods and avoid your high-volume times. Build maintenance into your schedule as a regular part of your routine.
Fewer surprises. A snafu happens, something breaks, and you have to stop production to figure out what it is and fix it. That can happen at any time, and trust us, it will happen when you least want it to. Performing preventive, not reactive, maintenance will lessen those unwelcomed surprises that erode your productivity and profitability. A general rule is that planned work will cost two-thirds less than unplanned work in time and other resources.
Increased efficiency. At USC Consulting Group, we’re all about efficiency, and one of the surest ways to find “hidden efficiencies” that you didn’t even know were possible is to perform regular preventive maintenance on your machines.
Increased longevity of your machinery and assets. This is key. Just like your car needs regular oil changes and tune-ups to keep it running at its best, so do your assets.
Preventive maintenance challenges
There are some challenges with doing regular preventive maintenance. However, in our view, these don’t outweigh the benefits.
Finding the optimal time to do it is tricky. A regular schedule is the key to finding the best time to shut down for maintenance. And the downtime is typically where we see the most pushback from executives and managers who aren’t thrilled with this process.
It will cause shutdowns. There’s no way around it. To perform maintenance on your equipment, the line must stop.
If it ain’t broke, don’t fix it. This is an old adage for a reason. You may be shutting down for your scheduled maintenance when no problems actually exist. The shutdown does come at a productivity cost, so… is it worth it? Some manufacturers solve this issue by performing predictive maintenance instead. It’s a more complex process that is data driven, and analyzes how your assets are performing in real time. All’s well? No shutdown. But if you find problems, that’s when you act. It reduces downtime, and you’re not replacing any parts while they’re still good to go. The downside of this approach is complexity and connectivity. If you don’t have state-of-the-art machinery, you won’t get the data analytics that this process requires. That’s why the majority of manufacturers today are using the preventive approach.
At USC Consulting, we’ve been helping manufacturing businesses increase their efficiency, production, throughput and profits for more than half a century. Get in touch today if you’d like to learn more about how preventive maintenance benefits can boost your bottom line.
As a typical rule of thumb in maintenance, planned work will consume roughly one third of the resources (labor cost, materials cost, and costs associated with equipment down-time) as unplanned work will consume. Therefore, the first objective of any maintenance program can be simplified as maximizing the percentage of time and resources spent on planned maintenance, and reducing the amount of unplanned maintenance or repair work resulting from unexpected breakdowns.
Understanding the Types of Work
Planned work can be broken down into two main categories: preventative maintenance and planned repairs. Preventative maintenance includes all the work done not in response to a failure, but to prevent future failures from occurring. This work is typically outlined by the manufacturer in terms of frequency and work that must be performed (oil change, lube, and filter). If the fleet size remains constant, so will the level of preventative maintenance. Planned repairs are work that must be done as a result of wear and tear in which the equipment has not yet failed and can still run reliably until the maintenance department is set up with the required materials, labor, and shop space to adequately address these repairs. For exemplary purposes in this article, we will consider maintenance needed for an underground mine as a model. Due to the travel time in underground mining and the requirement in most cases to have repairs done in the shop after a wash, these two types of planned work are best done together to minimize the mechanic’s trips to and from the equipment.
Given that the level of preventative maintenance will remain considerably flat, as both the materials required and time required can be predicted and cyclical, the only way to effectively increase planned work as a proportion of total work is to increase the level of planned repairs. The first task is to shift the balance of planned maintenance and unplanned maintenance. That is, to convert as much of the resources spent on unplanned work as possible into resources spent on planned work.
Converting Unplanned Work into Planned Maintenance
The first step is to create a backlog, a master list of all known repairs that must be made to each piece of equipment. It consists of repairs necessary to components that are in a partial state of failure, but have not yet failed. The size of a backlog and how well it is managed will provide some valuable insight as to the over-all health of your assets. A complete detailed backlog will also provide other benefits to management when taking a closer look at each type of equipment and analyzing which components require more attention than others. If repairs to equipment must be done before the equipment actually fails, the ability to identify or predict failures before they actually occur will be crucial. Coordination can then be made for the replacement of these components before failure occurs. This can be a very difficult and daunting task when considering a large fleet with complex equipment.
The first element to be considered when creating and managing a backlog is where the backlog work will be sourced from. Where will the maintenance planners get the information to create backlog list? Each time the equipment is inspected, an opportunity is provided to gather backlog. In an underground mining environment, some of these touch points include the preventative maintenance services, planned repairs, and operator circle checks.
An additional inspection can be strategically added to generate a greater and more detailed amount of backlog. Figure 1 below depicts the impact on parts procurement time of an inspection conducted by a mechanic in a predetermined time frame before the equipment is scheduled to come into the shop for a preventative maintenance service.
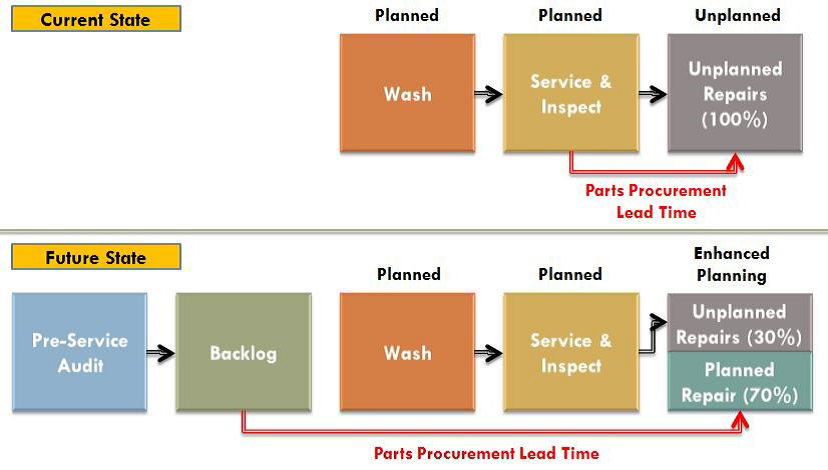
Figure 1—Current State vs. Future State with Backlog
Once the backlog list has been developed, the repairs can then be strategically scheduled alongside the preventative maintenance services while the equipment is already in the shop with shop space and labor assigned to it. Additionally, once these repairs have been scheduled, parts and materials can be ordered, packaged, and delivered to the shop where the repairs will be completed.
The supply benefits of planning repairs before failure are amplified in underground mining as the remote locations can be difficult for suppliers to deliver to. Even once on site, the materials must go through a complex supply delivery system to make their way underground. Planning these repairs ahead of time allows the equipment to run for the duration of this prolonged lead time. If the equipment is run until failure, it will remain down for the entire duration of this lead time until the needed parts can be delivered.
In generating and completing the backlog list against each piece of equipment, failures and breakdowns that would normally occur can now be discovered before failure and repaired on average much quicker than if the equipment would have broken down. The backlog system is working towards converting unplanned maintenance work into planned maintenance work, and therefore consuming one third of the resources on each repair converted as would normally be expended.
Planned maintenance leads to significant cost savings with improved productivity. For 50 plus years USC Consulting Group has helped organizations develop planned maintenance programs to increase their uptime. Contact us today to start converting your maintenance practices and keep your operations running as much as possible.
No manufacturing company can reach its full potential unless its people and assets are kept safe. Any accident, no matter how small, can seriously interrupt workflow and hurt a business’s ability to meet its production goals. This is why manufacturers must be diligent about creating a culture of safety within their organizations. Beyond establishing and promoting basic safety behaviors and procedures, investing in workplace automation could greatly improve the overall well-being of your industrial operation.
For example, robots can complete the same task thousands of times a day without becoming bored or inattentive, which can decrease delays caused by mistakes or distractions. Automation also means that human workers reduce their risk of suffering injuries due to repetitive strain.
Another advantage of automated technology is accident prevention. Autonomous forklifts and other self-driving machines can avoid collisions and other mistakes often made by human operators. This means work can continue with fewer interruptions and employees are able to stay on the job without injury.
Perhaps one of the most important benefits of workplace automation is the amount of data it provides. With detailed metrics that are compiled automatically, managers can get a clearer picture of their operations. Data can also help administrators identify areas of improvement that can be targeted to reduce the risk of accidents and increase productivity.
Building a safer and more successful workplace requires taking advantage of every tool at your disposal. To learn more about how automation can help you accomplish this goal, take a look at the accompanying infographic by The Numina Group.
By improving your processes and automating certain procedures, you can create a workplace that is not only safe, but extremely productive. If you’re looking for guidance in buttoning up your operations to be as efficient and secure as possible, contact us today.
Score operational excellence in your business by embracing the continuous improvement process.
Here’s the story…
The Ice Kings are struggling. They’ve lost 6 of their last 7 games. Last season, they went to the playoffs. What’s wrong?
Enter Coach USC, who takes a page from the USC Playbook – Embracing Continuous Improvement.
Coach USC takes a look at the team – who need to improve all of their skills – shooting, passing, stick-handling and skating. This means breaking it down to the fundamentals with practice and training.
Like the Ice Kings, businesses need to take a page from the USC Playbook to help them continuously improve starting with the fundamentals of proper employee training.
But all of the training in the world won’t make a difference unless the team is in top shape – that means exercising and maintaining a healthy lifestyle. Just as in business – it’s important for assets to “stay in shape” through predictive and preventative maintenance.
It doesn’t stop there – Coach USC performs data analysis by watching the game tape each week to see how they can keep playing better. Businesses can also continuously improve through organizational and operational reflection, capital awareness, and creating a culture of openness.
For over 50 years, USC Consulting Group has been a game changer – helping hundreds of clients to find gaps, refine processes and turn weaknesses into strengths.
Ready to find out more how USC can help your team embrace the continuous improvement process? Download the USC Playbook today.
The preventive maintenance methodology has become industry standard. An estimated 80% of asset and facilities stakeholders now leverage preventive workflows, while approximately half take advantage of predictive maintenance tools meant to further enhance such forward-thinking processes, per research from Advanced Technology Services and Plant Engineering. Why are so many businesses embracing this approach? The return on investment can be immense. Some see maintenance savings of between 12% and 18% percent, on top of the revenue-generating performance improvements that naturally unfold as a consequence of machine uptime increases, according to Transcendent. Companies on the outside looking in on the emergence and solidification of the PM model typically view these developments with considerable envy and race to keep up with the competition. However, firms attempting to play catch-up at hyperspeed often encounter roadblocks — most notably, the perceived cost of implementation.
Redesigning existing maintenance workflows is neither easy nor expense-free. These essential backend processes support production activities that directly affect the bottom line, and changing them, even incrementally, might seem risky, especially for organizations with thinner margins. However, the long-term costs that come with hanging on to reactive maintenance methodologies could very well outweigh the expenses incurred as a product of PM implementation and the shop floor disruption that could accompany such a move. Organizations looking to embark on this transition would be wise to unpack the entire cost equation and determine the potential ROI.
Understanding PM implementation costs
The Preventive Maintenance (PM) concept is easy to understand — focus on equipment upkeep and optimization, and address small mechanical deficiencies before they devolve into bigger problems bound to cause downtime. The idea is far more complicated in practice, however. To actually achieve PM implementation, maintenance stakeholders must navigate a multistage process that begins with program design. This initial phase normally involves establishing an overarching PM objective. Some organizations move forward with PM implementation with the sole purpose of saving money, while others want to ensure optimal shop floor performance. Choosing an end goal establishes the foundation for effective program development. Here, maintenance experts — ideally those intimately familiar with OEM requirements, Plant Engineering reported — design granular equipment management processes, including rotating and reciprocating mechanical component lubrication.
Once maintenance personnel have developed an effective PM plan, they can move forward with deployment. This normally entails scheduling mission-critical PM tasks through computerized maintenance management software and training the staff members who will execute these actions. To ensure long-term PM sustainability, stakeholders will create and release program management and communication workflows that facilitate adherence and continuous improvement. This process requires considerable effort and can come with an equally substantial price tag. According to Plant Engineering, the expense breakdown might include items like this:
- Mechanic reassignment: Businesses often find themselves reassigning top-notch mechanics to oversee PM program design. This move could disrupt maintenance operations and potentially have a material impact on production, should serious equipment issues arise.
- Ancillary component installation: PM implementation sometimes requires the purchase of smaller mechanical components or accessories — infrared scanning guns for equipment heat checks and automated lubrication for scheduled machine conditioning, for instance — that are key to PM success.
- CMMS implementation: For firms without CMMS technology, installing one of these platforms is almost essential. Pricing for CMMS software varies. Pared-down versions might cost as little as $40 per user per month, while more robust platforms featuring customized features could require larger investments, TechRadar reported.
- Vendor onboarding: PM tasks such as equipment lubrication management can become overwhelming for internal maintenance teams, which is why some organizations end up outsourcing these processes to external vendors. This improves efficiency and saves time but costs money.
These are a handful of the most common expenses organizations navigating PM implementation encounter. However, the costs sometimes do not stop here — under-the-radar expenses can materialize post launch, per researchers from Oniqua Enterprise Analytics. These extra amounts actually come from over-maintenance. This occurs when maintenance teams become overly focused on equipment optimization and establish work intervals that are far too short, meaning staff members execute upkeep activities so often that both time and resources go to waste. A surprisingly large number of firms make this mistake, according to analysts for Oniqua, who found that 80% of PM tasks unfold over a period of 30 days or fewer and that 30% to 40% of these duties are applied to equipment that has little to no impact on uptime.
Assessing PM implementation ROI
While the aforementioned costs can certainly make PM implementation seem overwhelming, the operational returns that come with embracing this approach typically make these initial expenses easier to swallow. For example, researchers for ReliaSoft estimated that organizations with reactive maintenance operations in place pay around $8 per replacement part, while those with PM strategies spend just $2 per new equipment component. Additionally, PM programs often catalyze shop floor improvements that could only be achieved through purchasing new machinery. An operation that implements such an initiative might pay $100,000 per year to maintain PM workflows that increase capacity by 25% — a gain that would require an upfront equipment investment of $500,000 and $200,000 in annual staffing and asset management work, Reliable Plant reported. Together, PM-related cost reductions and productivity boosts can generate big returns, according to Jones Lange LaSalle, which found that some adopters stood to 545% ROI.
This sort of improvement is simply too significant to pass up for most modern businesses, particularly small and medium manufacturers, many of whom are just getting by within today’s fluid marketplace. That said, pursuing PM implementation can be an immensely daunting task for all organizations, regardless of sector or size. Here at USC Consulting Group, we have been helping companies across a variety of industries navigate PM implementation for decades, leveraging proven techniques and tools that simplify change management and lay the foundation for sustainable organizational growth via continuous operational improvement.
Contact us today to learn more about our work and how we can help your business embrace the Preventive Maintenance methodology.
More than 43,000 commercial aircraft navigate American airspace daily, shuttling an estimated 2.6 million passengers among airports here and abroad, according to the Federal Aviation Administration. An army of approximately 10.6 million aviation professionals facilitate these efforts, propelling the countless behind-the-scenes and front-of-house functions that make modern air travel possible. Maintenance specialists are among these essential personnel and perform mission-critical duties that support passenger safety and operational efficiency. Carriers understand well just how important these technicians are and devote tens of billions of dollars annually to funding maintenance programs, per analysts for the International Air Transport Association, who estimated that total MRO spending for the industry was $76 billion in 2017, the latest year for which IATA research was available. Despite this level of investment and hard work on the part of on-the-ground maintenance teams, many airline companies struggle with aircraft availability and reliability.
Southwest Airlines’ recent rash of maintenance foibles is among the most prominent examples. The airline, which is the second-largest American carrier based on market share, according to the Bureau of Transportation Statistics, has been forced to cancel hundreds of flights throughout the month of February 2019 as a consequence of unplanned maintenance issues, per Reuters. Southwest has watched its stock prices decrease by almost 6 percent over this tumultuous span, which it seems will continue for the foreseeable future.
Recently, the carrier conducted an internal review and discovered that as many as 100 disgruntled mechanics may have deliberately caused some of the maintenance disruptions that catalyzed hundreds of cancellations and delays, The Dallas Morning News reported. While this brand of alleged internal vandalism is certainly unique, Southwest Airlines’ aircraft availability issues are not. Available seat miles for all U.S. carriers dropped from 1.74 billion in 2017 to 1.66 billion in 2018, the BTS found. This was the first year-on-year ASM decrease the agency recorded since 2009.
It is clear that carrier maintenance divisions must make improvements, but how? The IATA pinpointed some sector-specific operational problems that are hamstringing maintenance teams in the industry. By addressing these issues, carriers can bolster aircraft availability, re-engage travelers and regain ground in the marketplace.
OEM explosions and trade tensions
U.S. airlines consume an estimated 40 percent of all aircraft equipment produced worldwide, according to the Business Research Company. While domestic carriers are expected to continue their spending dominance, the aircraft manufacturing space itself is undergoing significant change, the IATA found. For one, more original equipment manufacturers are entering the aftermarket component arena in a bid to usurp the MRO manufacturers that have long populated the subsector.
The OEMs entering this niche market offer top-of-the-line replacement components and sometimes bundle such items with system-wide repair services, Aviation Pros reported. These offerings boast obvious benefits but are designed to draw airline procurement teams away from MRO producers or manufacturers that provide FAA-certified items with parts manufacturer approval.
Unfortunately, the emergence of aftermarket OEM products is not the only development catalyzing jarring change within the aircraft equipment space. Widespread economic protectionism is hamstringing international supply chain operations and making it difficult for aviation manufacturers to obtain reasonably priced raw materials, CBS News reported. These organizations have no choice but to raise their prices to cover the extra overhead costs that come with possibly rerouting shipments or bearing the brunt of 10 percent to 15 percent tariff increases. In the end, these additional expenses trickle down to carriers, of course.
Together, these less-than-positive trends directly affect airline maintenance teams. How? With their colleagues in the procurement department scrambling to adjust to these new realities, maintenance leaders and technicians risk MRO stock shortages that delay aircraft upkeep and ultimately lead to slowdowns or cancelations.
That said, there are viable solutions to the procurement problems discussed above – most notably, strategic sourcing. By redesigning their procurement networks and cultivating collaborations with multiple vendors spread across geographic locations, airlines can get the parts they need, when they need them and for the right price, no matter the market conditions.
Growing technician shortages
Both domestic and international carriers are staring down an immense and ever-expanding aviation maintenance technician shortage, per researchers for the Aviation Technician Education Council, who predict airlines will be struggling to fill approximately 15,000 open maintenance positions by 2027. There are two reasons for this. For one, an estimated 30 percent of current maintenance specialists are near retirement age, the ATEC found. Secondly, many of the young talent who might step into these empty positions are pursuing other careers or going to college to move into management roles in the aviation space rather than take on technical work, CNBC reported. This is, of course, a major problem for carrier maintenance crews, most of which are already struggling to keep fleets in good shape with the assistance of seasoned technicians.
While airlines may not have the resources to launch their own training academies, they can help cultivate talent pipelines by working with educational institutions to offer apprenticeships and other hands-on opportunities that engage young people interested in entering the aviation arena and potentially the maintenance specialty. Carriers can also address talent shortages operationally by developing and rolling out workflow optimization programs that allow them to do more with less. These kinds of stopgaps can not only mitigate the impact of the developing technician deficit but also lens carriers the operational framework they need to move forward without depending on future workforce development.
U.S. airlines that hope to address the above maintenance challenges and keep their customers should take immediate action, lest they see cancellations and delays knock them out of the marketplace.
Is your airline searching for a strategic partner that can help bolster maintenance operations in the face of great change and turmoil? USC Consulting Group can assist. We have been working with organizations within the aviation industry for more than five decades, collaborating with them to transform their operations and adapt to marketplace shifts of all kinds.
Connect with us today to learn more about our experience and how we can help your carrier adjust to the ongoing maintenance challenges.
Heavy production assets are ubiquitous across numerous industries, from residential construction to mining. Keeping this mission-critical equipment up and running is among the top priorities for modern industrial organizations. It is why the average firm devotes almost 10 percent of its facilities budget to maintenance activities, according to researchers from Plant Engineering.
Virtually all of these entities leverage either predictive or preventive maintenance methodologies, both of which materialized in recent years due to widespread enterprise digitization. But how exactly are businesses deploying these strategies to ensure heavy production assets maintain peak performance? Here is an industry-agnostic look into the state of predictive and preventive maintenance best practices for heavy asset optimization:
Unpacking the preventive approach
An estimated 80 percent of maintenance teams employ preventive maintenance techniques, per survey data from Advanced Technology Services and Plan Engineering. The proactive approach centers on one operational goal: reducing production downtime. There are several associated best practices that guide preventive maintenance implementation and management.
Relinquishing the reactive approach to asset maintenance is the most impactful of these exercises. Unfortunately, it is also the hardest to adopt, Modern Materials Handling reported. Maintenance specialists that have traditionally listened for the cacophony of mechanical collapse and responded in turn must change their mindsets and instead focus on implementing piecemeal adjustments to mitigate the wear and tear that causes asset failure.
Making this cultural switch is no easy task – neither is reassessing all production and maintenance policies and procedures, and drafting new ones to comport with key performance indicators and company goals. However, four-fifths of maintenance teams have managed to execute these and the other preventive best practices on the way to transformation, including groups responsible for overseeing heavy assets.
Industrial organizations that excel at heavy machinery maintenance and effectively address small mechanical errors before they devolve into downtime-causing kinks focus on developing and sustaining routine asset optimization schedules, according to Reliable Plant. Through consistent check-ups and slight tweaks, maintenance teams responsible for bulky equipment can ensure these key production tools are always in good condition and ready to perform. Usage monitoring is also key, as heavy assets that are misused, either intentionally or unintentionally, typically break down the fastest.
How does usage monitoring unfold within an actual production workflow? A construction company preparing to excavate a new worksite might assess the climate and the soil to determine which backhoe digging attachment is not only best suited for the task at hand, but also the least likely to cause mechanical stress. These and other techniques make preventive maintenance possible, even with heavy assets in play.
Unpacking the predictive approach
When investments in heavy machinery began climbing dramatically more than a half decade ago, equipment manufacturers advised industrial companies to adopt asset tracking solutions to ensure that the multimillion-dollar tools they were deploying were actually required, The Wall Street Journal reported. At the same time, an innovative approach to maintenance, which also happened to be based on data analytics, was emerging.
This methodology, called predictive maintenance, would allow organizations to harness the power of advanced information technology to monitor mission-critical machinery in real-time, calculate the potential for future downtime and make improvements to avoid shutdown. In the years since this strategy materialized, many businesses have embraced it. In fact, 47 percent of industrial firms attest to deploying predictive maintenance processes and tools, per Advanced Technology Services and Plan Engineering.
Perhaps the most well-publicized and successful predictive maintenance programs have unfolded within organizations leveraging larger production assets. For example, construction equipment giant Caterpillar was among the first asset producers to manufacture products meant for use in predictive maintenance workflows, Forbes Magazine reported. The company began building bulldozers, dump trucks, excavators and other common equipment with pre-installed wireless sensors designed to transmit usable performance insights to maintenance leaders. Caterpillar customers have seen significant efficiency gains and cost reductions as a consequence of this forward-thinking equipment and the accompanying software.
Harley-Davidson is another early adopter that propelled predictive maintenance to new heights. Starting back in 2010, the automotive giant began outfitting the decades-old equipment in its York, Pennsylvania plant with wireless sensors configured to monitor mechanical operations and measure physical variables such as component vibration to assess asset performance, The Journal reported. These tools and the predictive maintenance program they facilitated led to drastic shop floor improvement, as Harley-Davidson watched production throughput times and costs decrease.
While impressive, these outcomes merely represent the initial stages of the predictive maintenance approach, according to PricewaterhouseCoopers. The rise of deployable enterprise artificial intelligence technology is expected to have an immense impact on this strategy, lending industrial firms the ability to monitor more data points across larger pools of equipment, including heavy assets.
That said, there is ample ground to cover before AI-propelled predictive maintenance workflows become industry standard. Most organizations inhabit the second position on the predictive maturity scale, per PwC, and therefore still depend on instrument inspections and other manual means. However, a significant number have entered stage three and now leverage real-time condition monitoring tools. Far fewer are in stage four, where expansive data-driven workflows capable of handling massive amounts of asset information are the norm.
In any case, predictive maintenance holds immense potential for teams assigned to heavy assets and, as the survey data from Advanced Technology Services and Plan Engineering indicates, a good number of the teams overseeing large machinery today have at least embraced some processes and tools associated with the strategy.
Implementing preventive and predictive maintenance strategies centered on heavy equipment can seem like an overwhelming task, especially for smaller industrial firms or those with particularly intense production demands. For businesses in these positions, external assistance could be all but necessary. USC Consulting Group has been helping organizations optimize their maintenance operations for decades, leveraging proven techniques and tools that accelerate change and lay the foundation for sustainable growth.
Connect with us today to learn more about our work and how we can help your company reduce heavy asset-related downtime.