-
Subscribe to Blog:
SEARCH THE BLOG
CATEGORIES
- Aerospace
- Asset Maintenance
- Automotive
- Blog
- Building Products
- Case Studies
- Chemical Processing
- Consulting
- Food & Beverage
- Forestry Products
- Hospitals & Healthcare
- Knowledge Transfer
- Lean Manufacturing
- Life Sciences
- Logistics
- Manufacturing
- Material Utilization
- Metals
- Mining
- News
- Office Politics
- Oil & Gas
- Plastics
- Private Equity
- Process Improvement
- Project Management
- Spend Management
- Supply Chain
- Uncategorized
- Utilities
- Whitepapers
BLOG ARCHIVES
- August 2025 (2)
- July 2025 (2)
- June 2025 (4)
- May 2025 (1)
- April 2025 (1)
- March 2025 (1)
- February 2025 (4)
- January 2025 (4)
- December 2024 (4)
- November 2024 (2)
- October 2024 (6)
- September 2024 (5)
- August 2024 (5)
- July 2024 (6)
- June 2024 (3)
- May 2024 (3)
- April 2024 (4)
- March 2024 (3)
- February 2024 (4)
- January 2024 (5)
- December 2023 (2)
- November 2023 (1)
- October 2023 (6)
- September 2023 (3)
- August 2023 (4)
- July 2023 (2)
- June 2023 (3)
- May 2023 (7)
- April 2023 (3)
- March 2023 (3)
- February 2023 (5)
- January 2023 (6)
- December 2022 (2)
- November 2022 (5)
- October 2022 (5)
- September 2022 (5)
- August 2022 (6)
- July 2022 (3)
- June 2022 (4)
- May 2022 (5)
- April 2022 (3)
- March 2022 (5)
- February 2022 (4)
- January 2022 (7)
- December 2021 (3)
- November 2021 (5)
- October 2021 (3)
- September 2021 (2)
- August 2021 (6)
- July 2021 (2)
- June 2021 (10)
- May 2021 (4)
- April 2021 (5)
- March 2021 (5)
- February 2021 (3)
- January 2021 (4)
- December 2020 (3)
- November 2020 (3)
- October 2020 (3)
- September 2020 (3)
- August 2020 (4)
- July 2020 (3)
- June 2020 (5)
- May 2020 (3)
- April 2020 (3)
- March 2020 (4)
- February 2020 (4)
- January 2020 (4)
- December 2019 (3)
- November 2019 (2)
- October 2019 (4)
- September 2019 (2)
- August 2019 (4)
- July 2019 (3)
- June 2019 (4)
- May 2019 (2)
- April 2019 (4)
- March 2019 (4)
- February 2019 (5)
- January 2019 (5)
- December 2018 (2)
- November 2018 (2)
- October 2018 (5)
- September 2018 (4)
- August 2018 (3)
- July 2018 (2)
- June 2018 (4)
- May 2018 (3)
- April 2018 (3)
- March 2018 (2)
- February 2018 (2)
- January 2018 (1)
- December 2017 (1)
- November 2017 (2)
- October 2017 (2)
- September 2017 (1)
- August 2017 (2)
- July 2017 (2)
- June 2017 (1)
- April 2017 (3)
- March 2017 (3)
- February 2017 (2)
- January 2017 (2)
- December 2016 (2)
- November 2016 (4)
- October 2016 (4)
- September 2016 (3)
- August 2016 (6)
- July 2016 (4)
- June 2016 (4)
- May 2016 (1)
- April 2016 (3)
- March 2016 (4)
- February 2016 (2)
- January 2016 (4)
- December 2015 (3)
- November 2015 (3)
- October 2015 (1)
- September 2015 (1)
- August 2015 (4)
- July 2015 (6)
- June 2015 (4)
- May 2015 (7)
- April 2015 (6)
- March 2015 (6)
- February 2015 (4)
- January 2015 (3)
CONNECT WITH US
Tag Archives: Medical Devices
Imagine a scenario in which there is unprecedented demand for the products you manufacture, but disruptions in the supply chain are making it difficult, if not impossible, to meet that demand and even if you do, logistics bottlenecks are preventing them from getting where they need to go. Many manufacturers have been running up against this problem since the pandemic began.
Now imagine that people’s very lives literally depend on those products being manufactured and delivered to their destinations.
If you’re in the medical device manufacturing industry, you’re likely thinking: “Welcome to my world.” Not only has it been as hard hit as any other manufacturer by supply chain disruptions and logistic backups, the implications of the resulting shortages of the devices they manufacture may cost people their lives.
The FDA is calling the shortages of medical devices at this critical time a “public health emergency.” It published a device shortage list including the categories of personal protective equipment for medical workers, testing supplies and equipment, and ventilation-related products. The list also outlines the specific products, the estimated duration of the shortage, and the reasons for the shortages, along with what the government is doing about it.
That list is illuminating — and even frustrating — for many reasons, but it’s not all bad news. Among the most common reasons for shortages, including increased demand and supply chain issues, which manufacturers have little control over, there is also one culprit that manufacturers can control: “Requirements for complying with good manufacturing practices.”
As medical device manufacturers know, the FDA has strict compliance requirements that affect every part of the process from designing to manufacturing to testing to shipping, even labeling. In those processes, there can be room for improvement. That’s something manufacturers can do — process improvements to get their products to market faster, while still complying with the FDA.
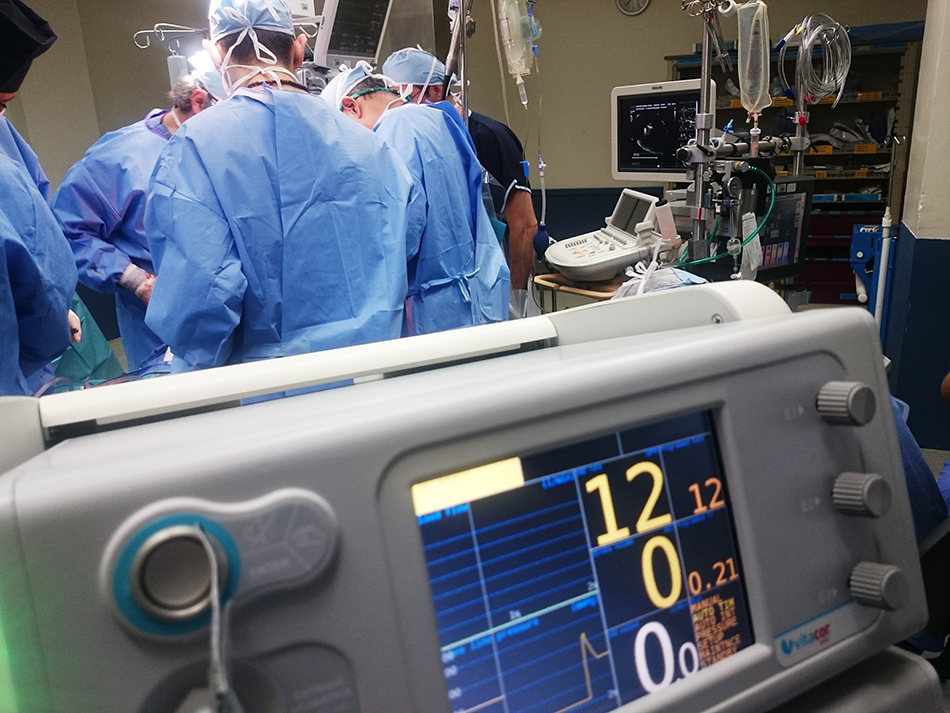
The FDA is calling the shortages of medical devices at this critical time a “public health emergency.”
What medical device manufacturers can do now
At USC Consulting Group, we’ve been helping manufacturers up their operational efficiency for more than 50 years. We analyze what you’re doing, how you’re doing it, and how we can create greater efficiency using your existing resources. A few tactics we’re implementing with our medical manufacturing clients to help mitigate these shortfalls and get their products to people who need them quicker include:
Investigate Lean / Six Sigma
Lean manufacturing is nothing new. The art of maximizing customer value while minimizing waste was pioneered by Henry Ford … or Toyota, depending on who you ask, decades ago. Six Sigma is a newer methodology designed to tackle defects in manufacturing. While Lean looks at making processes more efficient and reducing process lead times, Six Sigma focuses on cutting down on defects that can delay production. In fact, they’ve joined to become one methodology in some circles. Lean techniques help you get product off the line faster, heightening your throughput. Six Sigma strives to target the reason for any defects in the products. These two techniques can conflict — one sure way to cut down on defects is to slow down the process, which runs counter to Lean’s goals. Achieving the perfect balance between the two, and getting the job done faster with fewer defects, is indeed an art form, and worth exploring.
Use SIOP to make your planning and forecasting bulletproof
We recommend using SIOP (Sales, Inventory and Operations Planning) to elevate your planning process to achieve that perfect balance between your supply and demand. You’ve heard of S&OP, a popular business management process that involves sales forecast reports, planning for demand and supply, and other factors. The goal is to help companies get a better, more clear look at their operations and create better-informed strategy decisions, allowing them to deliver what clients need in the most profitable way.
It’s a useful process, but we’ve found a lot of our clients do not include inventory as a strategic tool in their S&OP process. Therefore, they leave the “I” out of SIOP. Adding inventory into the mix is just one additional step, but we find it can be the key to the whole process. When you’re focusing on inventory, it requires more careful planning and elevates the entire planning process up a notch. When your inventory is optimized, which is not an easy mark to hit in these days of supply chain disruption, things tend to fall into place. With SIOP, you can make your inventory work harder for you.
Download our free eBook, “Sales, Inventory and Operations Planning: It’s About Time,” to dive deeper into SIOP.
Involve your frontline employees
We call it the Employee Involvement Prototype (EIP). It’s about engaging with your employees at the machine level and getting good data from the floor. It includes anyone who has to do with the line, and entails taking a look at those operations and processes with input from the men and women who are actually doing the job on an hour-by-hour basis.
Focus on throughput, productivity and yield
Take a good look at what’s happening on the line. What is the “drumbeat”? Are all your functions in sync? Can you improve production by cutting redundant steps?
For more information on these two points, download our whitepaper, “Strategies for Meeting Increasing Customer Demand.” It goes into much more detail about how you can create that proverbial well-oiled machine.
When it comes to caring for people and providing the products they need, time is of the utmost importance. Medical device manufacturers understand they must overcome the worst supply chain disruptions to deliver to the people whose lives depend on them.
Need help? Give us a call. We can save your operations so you can save lives.