-
Subscribe to Blog:
SEARCH THE BLOG
CATEGORIES
- Aerospace
- Asset Maintenance
- Automotive
- Blog
- Building Products
- Case Studies
- Chemical Processing
- Consulting
- Food & Beverage
- Forestry Products
- Hospitals & Healthcare
- Knowledge Transfer
- Lean Manufacturing
- Life Sciences
- Logistics
- Manufacturing
- Material Utilization
- Metals
- Mining
- News
- Office Politics
- Oil & Gas
- Plastics
- Private Equity
- Process Improvement
- Project Management
- Spend Management
- Supply Chain
- Uncategorized
- Utilities
- Whitepapers
BLOG ARCHIVES
- July 2025 (1)
- June 2025 (4)
- May 2025 (1)
- April 2025 (1)
- March 2025 (1)
- February 2025 (4)
- January 2025 (4)
- December 2024 (4)
- November 2024 (2)
- October 2024 (6)
- September 2024 (5)
- August 2024 (5)
- July 2024 (6)
- June 2024 (3)
- May 2024 (3)
- April 2024 (4)
- March 2024 (3)
- February 2024 (4)
- January 2024 (5)
- December 2023 (2)
- November 2023 (1)
- October 2023 (6)
- September 2023 (3)
- August 2023 (4)
- July 2023 (2)
- June 2023 (3)
- May 2023 (7)
- April 2023 (3)
- March 2023 (3)
- February 2023 (5)
- January 2023 (6)
- December 2022 (2)
- November 2022 (5)
- October 2022 (5)
- September 2022 (5)
- August 2022 (6)
- July 2022 (3)
- June 2022 (4)
- May 2022 (5)
- April 2022 (3)
- March 2022 (5)
- February 2022 (4)
- January 2022 (7)
- December 2021 (3)
- November 2021 (5)
- October 2021 (3)
- September 2021 (2)
- August 2021 (6)
- July 2021 (2)
- June 2021 (10)
- May 2021 (4)
- April 2021 (5)
- March 2021 (5)
- February 2021 (3)
- January 2021 (4)
- December 2020 (3)
- November 2020 (3)
- October 2020 (3)
- September 2020 (3)
- August 2020 (4)
- July 2020 (3)
- June 2020 (5)
- May 2020 (3)
- April 2020 (3)
- March 2020 (4)
- February 2020 (4)
- January 2020 (4)
- December 2019 (3)
- November 2019 (2)
- October 2019 (4)
- September 2019 (2)
- August 2019 (4)
- July 2019 (3)
- June 2019 (4)
- May 2019 (2)
- April 2019 (4)
- March 2019 (4)
- February 2019 (5)
- January 2019 (5)
- December 2018 (2)
- November 2018 (2)
- October 2018 (5)
- September 2018 (4)
- August 2018 (3)
- July 2018 (2)
- June 2018 (4)
- May 2018 (3)
- April 2018 (3)
- March 2018 (2)
- February 2018 (2)
- January 2018 (1)
- December 2017 (1)
- November 2017 (2)
- October 2017 (2)
- September 2017 (1)
- August 2017 (2)
- July 2017 (2)
- June 2017 (1)
- April 2017 (3)
- March 2017 (3)
- February 2017 (2)
- January 2017 (2)
- December 2016 (2)
- November 2016 (4)
- October 2016 (4)
- September 2016 (3)
- August 2016 (6)
- July 2016 (4)
- June 2016 (4)
- May 2016 (1)
- April 2016 (3)
- March 2016 (4)
- February 2016 (2)
- January 2016 (4)
- December 2015 (3)
- November 2015 (3)
- October 2015 (1)
- September 2015 (1)
- August 2015 (4)
- July 2015 (6)
- June 2015 (4)
- May 2015 (7)
- April 2015 (6)
- March 2015 (6)
- February 2015 (4)
- January 2015 (3)
CONNECT WITH US
Tag Archives: Kanban
In most business settings, time is measured by hours and days — how long will it take to receive a proposal, mockup sheet or important presentation. But in the manufacturing world, time is measured in product cycles. From sourcing materials to testing to packaging, how long will it take to get one product from conception to full completion?
That is the essence of manufacturing cycle time.
Not to be confused with lead time, cycle time is how long it takes to complete a unit of product, from the beginning of the manufacturing process until the product is ready to ship. In this article we will detail how to calculate cycle times, and the ways you can improve it in your organization.
How to calculate cycle time
The manufacturing cycle time is different for every organization and every product run, and it’s important to constantly check on this variable to ensure productivity benchmarks are being met. The formula to determine cycle time is actually fairly simple:
Total amount of goods produced / Time of production = Cycle time
Once a baseline is determined, manufacturers can try a number of different things to decrease cycle time and increase profitability.
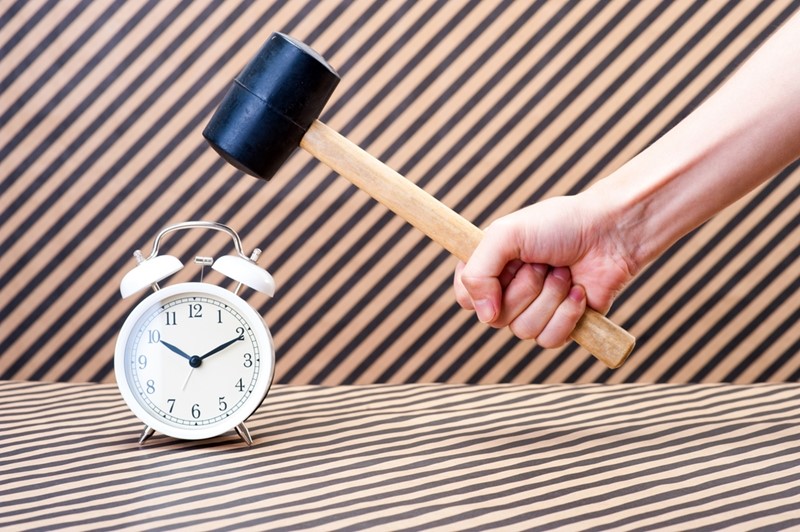
Knocking a few seconds from key areas of your cycle time can have a dramatic impact on productivity.
How to improve cycle time
There are a number of ways that a manufacturer can decrease cycle time, such as:
Streamline production process as a whole
By identifying and eliminating any bottlenecks or inefficiencies during the production process, manufacturers can reduce cycle time by improving the system as a whole.
Take a detailed look at your operations — are there issues associated with the production layout of your floor? Are there certain tasks that could be automated or otherwise simplified? Is there an opportunity for you to implement lean manufacturing principles? Evaluating your operations is a great way to identify inefficiencies in your organization.
The key is to reduce the time required in order to increase overall capacity, all while ensuring that nothing gets missed, as shortcuts can lead to quality control issues and dissatisfied customers.
Improve equipment and systems
Is your equipment up to date? Or are you using outdated machinery and legacy technologies?
The more outdated the equipment a manufacturer works with, the greater opportunity for preventable delays in operation. Take an assessment of physical equipment and the software your businesses utilizes on a daily basis. If you find that your systems are more than five or ten years old, it may be time to set aside profits to update your manufacturing facility.
Invest in employee training
Well-trained employees are more likely to work efficiently, produce high-quality results and create ways to optimize operations.
Develop a culture of employee development and make sure they feel comfortable giving suggestions. Doing so can increase morale — leading to higher retention rates, a growing concern of manufacturers — and improve the quality of operations as a whole. The more high-quality employees a manufacturer has, the more efficient the business will run.
Utilize analytics
Manufacturers should take an even deeper look at operations, utilizing analytics to alert them to any inefficiencies in the process.
On the surface, production could seem to be running smoothly, but perhaps there is an area of production, for example, that is taking 20% longer than expected. Create and gather data points wherever possible, because you never know what inefficiencies may be lurking under a normal-looking production cycle.
At USC Consulting Group, we can help your manufacturing business decrease manufacturing cycle time and increase efficiency and productivity. Contact us to find out more.
Innovation is driven by technological advancements, but far too often, manufacturers across all industries are overly concerned with how to bring the cutting edge to their products as opposed to their processes. The Big Data movement, canonized the world over as the saving grace for the burgeoning deluge of computerized information, allows businesses to do astronomically more in regards to customer relations and demand forecasting than once thought possible – that is, these companies can create a friction-less environment in which they can consume data at nigh-negligible costs, and apply their findings with minimal oversight and spend, resulting in momentous value-add potential.
But without the proper IT architecture in place, this can only be a pipe dream for businesses unwilling to bump up internal technological resources directly connected to production, be it the process or the product. Applications designed to monitor and control lean manufacturing initiatives can enhance the industries that bring them aboard, so long as these applications in question put the horse back before the cart, so to speak. What process improvements can be made to data-intensive operations using objective-minded management?
In manufacturing, measurement is everywhere, including data and process improvement.
Performance measurement
Believe it or not, metrics utilization isn’t just for the world of business – these days, the average individual uses a number of different “signals” to interact with the world around them, like how smartphone apps let hurried commuters know exactly what time public transportation pulls out of the station. In a sense, even low-tech devices like a car’s fuel gauges serve roughly the same purpose: conglomerating disparate information under a single, user-friendly visualization. In recent years, gas tank telemetry has evolved beyond simply stating fractions, but estimating how many miles a driver has left before refueling becomes a necessity. This is a much more actionable unit of measurement for this particular metric, as it assumes drivers won’t want to fill up unnecessarily as a means of saving money and time if it can be avoided without hindering functionality.
In a manufacturing plant, similar rules apply, but as industries grow more and more complex, production metrics continue to include more dimensions and incorporate larger volumes of data. However, the end results must be just as easy to understand and act on, perhaps even more so. Additionally, all manufacturers charting key performance indicators (KPIs) do so as these metrics relate to their own operations. Lean or Six Sigma only works so far as companies can identify their own shortcomings and apply these systems like antiseptic to a wound. According to a study by the faculty of manufacturing engineering at the Technical University of Malaysia, more often than not, KPIs “reflect the company’s mission, vision, objectives, and goal which are key imperatives to the company’s success,” especially when it comes to employee management. Any worthwhile application managing KPIs and alerting decision-makers as to vital data must therefore be as reliable as it is flexible to specific needs.
“Data from the end of a given process should inform operations at the very beginning.”
Process Improvements
Collecting and reporting on terabytes of data is one thing, but what can the right data management platform do to streamline tangible on-site workflow? Operational process improvements and efficiency can be gained through data management applications driven by lean manufacturing principles like kanban, or a system of inventory control where production information acts as a catalyst. The popular “pull, don’t push” paradigm used throughout manufacturing finds a home here as well. Data from the end of a given process should inform operations at the very beginning to promote efficient resource spend and temper production based on throughput potential. If a popular nightclub reaches capacity but the bouncer continues to allow guests entry, it creates an unsustainable and unsafe situation for everyone involved. However, if that same bouncer grants access based on how many guests leave, the venue can serve the most patrons without causing a commotion.
That said, as the Massachusetts Institute of Technology outlines, small discrepancies in different kanban-focused data management tools could actually stifle objective-based process improvements and detract from lean manufacturing practices. Certain lean manufacturing data management assets compartmentalize different actions in a given process and assign products within production as “carriers of information.” Returning to the nightclub analogy, if the bouncer has to occasionally go into the club and manually count occupants, this can create inefficiency and can convince people waiting in line for admission to seek out another place to spend their Friday night. But if that bouncer uses a counting device at the door, he or she can immediately respond to a happy party leaving as the impetus for allowing more people in. Similarly, manufacturers shouldn’t be “counting heads” so much as they should ensure their process improvements made to process management applications assign throughput data its proper role as a production instigator. In doing so, manufacturers avoid bottle-necked workflow and any resulting downtime, upgrading their efficiency through more intelligent datalogical deployments.
Kanban is one of several tools used by manufacturers to increase efficiency and limit downtime in a production process. Facilities use Kanban to make sure that production lines are supplied with the right materials at the right time. In Japanese, Kanban means visual card, and although at first it used physical cards, now Kanban is powered with technology. Visual cards are used to signal that processes are in need of materials or parts. The tool was originally invented in conjunction with “pull” systems of production that employ the “just-in-time” concept. Using the Kanban system, a manufacturer can reduce downtime through proper planning and execution.
“Kanban prevents inventory overflow and ensures precise delivery of quality materials to the line.”
Lean manufacturers use Kanban
In a just-in-time environment, processes are based on pull production expectations. Facilities only working on what is expected become leaner since they do not house excessive levels of raw or finished materials. Demand-pull allows companies to only produce what is needed, determined by time and quantity considerations. “Push” methods of production, on the other hand, are based on expected sales and manage inventory differently.
Process Excellence Network explained that Kanban prevents inventory overflow and ensures precise delivery of quality materials to the line. Smart manufacturers use sophisticated production scheduling software to plan production, order stock, and manage exchanges with suppliers and customers. Today, Kanban employs modern resources like e-mails, sensors, and electronic monitoring equipment.
Three main benefits of Kanban are:
- Visual control of production lines and assurance that only what is ordered is made.
- Products are free of defects and defective parts are found before they cause problems.
- Continuous improvement is achieved through the constant reduction of stock in production.
Kanban can help prevent inventory overflow
Kanban helps eliminate overproduction and waste
The Environmental Protection referred to Kanban as the “nervous system” of lean production and explained that Kanban is integral to just-in-time production because it is the channel through which ordering takes place. Specifically, Kanban is found in the form of a card, labeled container, computer order, or other tools that signal when more parts are needed for the next phase of production – thus eliminating overproduction.
Overproduction is a key form of manufacturing waste, noted the EPA. Kanban systems help eliminate overproduction and limit waste by reducing the number of products that must be scrapped or discarded. Kanban also reduces the amount of raw materials used in production and improves management of energy, emissions, and waste, resulting in more efficient production
Suggestions for an Effective Kanban System
Process Excellence Network advised that manufacturers set up Kanban properly in the workplace, for maximum benefit. Firstly, customers should only withdraw items in a downstream process, and suppliers should only produce items in an upstream process, in exact amounts as specified by the Kanban. Secondly, items should not be made or moved without a Kanban and a tag must be included with every item. Thirdly, defective parts and incorrect amounts should never be sent to the next process. Lastly, a facility should always work to reduce the number of Kanbans to lower inventories and identify potential problems with parts and materials.
Ultimately, Kanban is an effective method for reducing downtime because it ensures the correct supply of quality materials to the production line at all times. Sometimes, manufacturers who believe tribal knowledge can outperform lean methodologies, fail to raise efficiency because they do not properly implement Kanban, or implement it but do not enforce strict adherence. However, the most effective production facility knows that becoming lean means understanding that planning and execution go hand in hand.