-
Subscribe to Blog:
SEARCH THE BLOG
CATEGORIES
- Aerospace
- Asset Maintenance
- Automotive
- Blog
- Building Products
- Case Studies
- Chemical Processing
- Consulting
- Food & Beverage
- Forestry Products
- Hospitals & Healthcare
- Knowledge Transfer
- Lean Manufacturing
- Life Sciences
- Logistics
- Manufacturing
- Material Utilization
- Metals
- Mining
- News
- Office Politics
- Oil & Gas
- Plastics
- Private Equity
- Process Improvement
- Project Management
- Spend Management
- Supply Chain
- Uncategorized
- Utilities
- Whitepapers
BLOG ARCHIVES
- May 2025 (1)
- April 2025 (1)
- March 2025 (1)
- February 2025 (4)
- January 2025 (4)
- December 2024 (4)
- November 2024 (2)
- October 2024 (6)
- September 2024 (5)
- August 2024 (5)
- July 2024 (6)
- June 2024 (3)
- May 2024 (3)
- April 2024 (4)
- March 2024 (3)
- February 2024 (4)
- January 2024 (5)
- December 2023 (2)
- November 2023 (1)
- October 2023 (6)
- September 2023 (3)
- August 2023 (4)
- July 2023 (2)
- June 2023 (3)
- May 2023 (7)
- April 2023 (3)
- March 2023 (3)
- February 2023 (5)
- January 2023 (6)
- December 2022 (2)
- November 2022 (5)
- October 2022 (5)
- September 2022 (5)
- August 2022 (6)
- July 2022 (3)
- June 2022 (4)
- May 2022 (5)
- April 2022 (3)
- March 2022 (5)
- February 2022 (4)
- January 2022 (7)
- December 2021 (3)
- November 2021 (5)
- October 2021 (3)
- September 2021 (2)
- August 2021 (6)
- July 2021 (2)
- June 2021 (10)
- May 2021 (4)
- April 2021 (5)
- March 2021 (5)
- February 2021 (3)
- January 2021 (4)
- December 2020 (3)
- November 2020 (3)
- October 2020 (3)
- September 2020 (3)
- August 2020 (4)
- July 2020 (3)
- June 2020 (5)
- May 2020 (3)
- April 2020 (3)
- March 2020 (4)
- February 2020 (4)
- January 2020 (4)
- December 2019 (3)
- November 2019 (2)
- October 2019 (4)
- September 2019 (2)
- August 2019 (4)
- July 2019 (3)
- June 2019 (4)
- May 2019 (2)
- April 2019 (4)
- March 2019 (4)
- February 2019 (5)
- January 2019 (5)
- December 2018 (2)
- November 2018 (2)
- October 2018 (5)
- September 2018 (4)
- August 2018 (3)
- July 2018 (2)
- June 2018 (4)
- May 2018 (3)
- April 2018 (3)
- March 2018 (2)
- February 2018 (2)
- January 2018 (1)
- December 2017 (1)
- November 2017 (2)
- October 2017 (2)
- September 2017 (1)
- August 2017 (2)
- July 2017 (2)
- June 2017 (1)
- April 2017 (3)
- March 2017 (3)
- February 2017 (2)
- January 2017 (2)
- December 2016 (2)
- November 2016 (4)
- October 2016 (4)
- September 2016 (3)
- August 2016 (6)
- July 2016 (4)
- June 2016 (4)
- May 2016 (1)
- April 2016 (3)
- March 2016 (4)
- February 2016 (2)
- January 2016 (4)
- December 2015 (3)
- November 2015 (3)
- October 2015 (1)
- September 2015 (1)
- August 2015 (4)
- July 2015 (6)
- June 2015 (4)
- May 2015 (7)
- April 2015 (6)
- March 2015 (6)
- February 2015 (4)
- January 2015 (3)
CONNECT WITH US
Tag Archives: Industry 4.0
Thanks to cloud and edge computing, SaaS — software as a service — has become a highly transformative technology in both manufacturing and the supply chain. It makes software systems and various technologies accessible to a wide range of operations, big or small. That’s because the system itself is hosted remotely, so the central technologies don’t have to be on the premises or within a facility. SaaS tools are fully built cloud applications.
Picture the type of software that governs a sophisticated manufacturing system. The servers that host that software, and where most of the data is contained, are located off-property away from the manufacturer’s facility. At any time, it can communicate with the connected equipment, and users can access the entire system remotely as well.
However, it’s maintained, serviced, and even secured by a remote provider. The only thing the manufacturer has to worry about is whether or not the connected equipment is running optimally. They don’t have to manage an on-site data center, update servers and software configurations, or even troubleshoot major problems — that’s all done by the SaaS provider.
SaaS is innovative, but how does that system affect the manufacturing industry as a whole? What are the benefits of SaaS when deployed within a smart factory or Industry 4.0 environment?
1. Reduced Costs
Manufacturing software comes in many forms. There are tools to aid in engineering and design, sales or marketing, measure production quality, organize finances, and much more. Each one of those applications requires a steady stream of data and a team to manage both the software and its backend.
Just imagine how much processing power is necessary to handle all of those systems, let alone the physical storage needed to contain the resulting data to keep it all running. The best solution even today is to build a data center, whether on-site or remote. They are very costly to manage and maintain.
SaaS solutions eliminate those costs and requirements because the bulk of the system is hosted elsewhere, on the provider’s servers. There’s no equipment to install and no software to update or manage. It’s all done off-site. That also reduces the need for a large IT or software development team on the manufacturing side.
The kickback is much lower operating costs for manufacturers, despite all the benefits realized from the applications.
2. Better Security
When you need a process completed, but you don’t have the proper knowledge, the common practice is to call in a specialist. That is precisely what SaaS providers are, and it means they have access to highly specific resources and tools that no manufacturer realistically does. That translates to a better solution overall, especially when it comes to digital and data security.
Because their entire business is securing and maintaining their data centers, to provide software to clients, they have much more sophisticated and capable solutions in place. That filters down to the manufacturers subscribing to SaaS services, who realize better data security and smarter digital protections.
3. Unparalleled Flexibility
Manufacturers maintaining software and technology solutions in-house have to scale up when the operation grows, which can be devastating depending on how the market shifts and demand fluctuates. Spending hundreds of thousands to upgrade equipment only to experience a downturn in the market can ruin any business.
SaaS providers handle scaling and delivery. They can add new terminals and new users, and install or activate servers to accommodate their clients. This is not only done seamlessly, but it will also happen near-instantly. Customers can even try before they buy, trialing the services and solutions before deploying them within their facilities. If the software doesn’t work out or add value, it can be canceled at any time with a minimal impact on the greater operation.
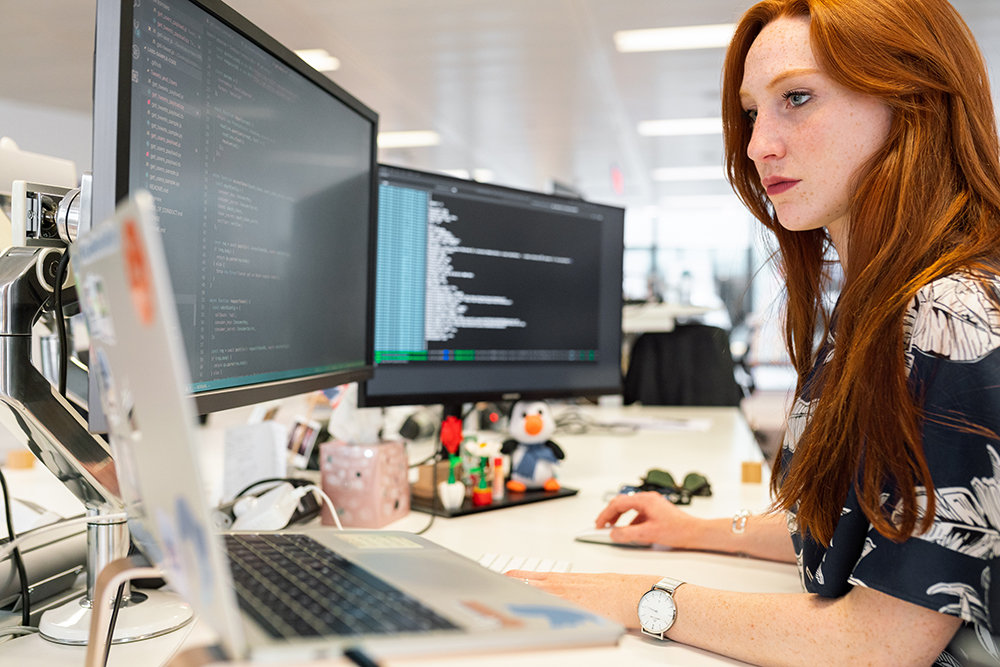
SaaS solutions can be accessed anywhere at any time allowing for more flexible operations.
4. Enhanced Interoperability
Typically, two pieces of distinct software cannot communicate with each other and the data they utilize isn’t guaranteed to be interchangeable. In manufacturing, this happens a lot with ERP and CMMS solutions. It complicates manufacturer-vendor relationships, especially when the default systems offer no interoperability.
Because SaaS solutions are hosted in the cloud, the systems accommodate interconnection between many different tools and platforms. CMMS, ERP, CRM, and project management tools can all communicate and share data, and the SaaS platform ensures it’s compatible and readable between those solutions.
5. Truly Agile Operations
If you look at what SaaS solutions provide manufacturers from a top-down perspective, it affords many operational efficiencies and creates new opportunities, without increasing the responsibilities the manufacturer is forced to take on. They have everything to gain and almost nothing to lose. Faster and more agile operations are implemented as a result, thanks to a system that’s always on, always ready to scale, and constantly being adapted to the needs of the manufacturer.
6. A Mobile Workforce
Because of the way SaaS solutions are maintained and delivered, they open up a whole new level of accessibility and mobility for manufacturing teams. Everyone from the decision-makers and supervisors to equipment operators gain access to on-demand and mobile-friendly solutions that can be accessed anywhere, at any time.
Additional features include mobile and real-time notifications, instant communication even between departments, remote access to mission-critical applications, and much more. Besides, security is managed on the backend, server-side, so users can move from terminal to terminal, or device to device, without compromising the system.
The caveat is that they need to follow proper security protocols, which means no password sharing or reuse, and precise authentication or verification systems.
An Ever-Evolving Industry Requires Adaptable Solutions
SaaS solutions are changing the manufacturing and production industries, but it’s not the only technology making a dent in normal operations. The entire field is undergoing a revolution, moving ever closer to Industry 4.0. The concept will see a marriage of advanced manufacturing techniques and smart, contextually-driven platforms to achieve seamless intercommunication, efficiency, and operability.
Software as a service plays a role in that movement, as manufacturers look to offset some of the requirements of the digital transformation. SaaS allows manufacturers to keep up with ever-evolving industries and markets. It reduces operational costs, speeds up output and processes, enhances security, improves software compatibility, and helps facilitate truly agile operations. What more could you ask for?
This article is written by Devin Partida. Devin is a tech writer with an interest in the IIoT and manufacturing. She is also the Editor-in-Chief of ReHack.com.
Most of the challenges supply chain players face in today’s market are related to the pandemic and economic shutdowns. Even so, they’re no different than what companies have dealt with in the past, or what will come after.
Understanding what those challenges mean for the greater market calls for a brief look at current events and existing obstacles.
1. Improving Resilience
The only thing constant in the market and supply chain operations is, interestingly enough, a wave of change. Whether it involves the shifting demands of consumers, raw material and supply shortages, or a global pandemic, something is always changing or evolving.
Despite this, many trends have skewed towards lean processes and a boost in agility. The problem is that in eliminating excess, many of the redundancies that would boost resilience have become less of a focus.
Until now, the tradeoff has been lucrative. By cutting many of those redundancies, operators have been able to conserve funds, reduce operating costs, and speed up mission-critical processes. If there’s less inventory on hand, there are fewer goods to sort, worry about, or waste. Unfortunately, the pandemic stomped hard on the entire economy, and not having those extra resources compounded all of the other problems.
The entire supply chain has learned an invaluable lesson about proper balancing, as opposed to leaning heavily on a single paradigm or strategy. Going forward, everyone will be focused on building strong supplier relationships, with multiple access points and opportunities. The goal is to bring some of those redundancies back, without destroying agile processes.
2. Building Out Flexibility
To keep up with market changes, supply chain operations need to be flexible. They need strong alternatives, with clear processes and sourcing adaptations.
How does this differ from resilience? Resilience involves creating a more secure operation, while flexibility is about developing alternatives and fostering relationships to support them.
If one supplier is experiencing delays, then an immediate shift to another, with a reliable supply, may be necessary. Taking that a step further, if that shortage is impacting an entire lineup of suppliers, then it’s time to find alternative resources — like a comparable raw material. A move like that cannot always happen quickly or in-the-moment.
Having those avenues in place before an event is the proper solution. The same could be done with regular operations, like a spike in product demands.
3. Unprecedented Visibility
Long before COVID-19, consumers were growing more aware of the environmental impact of their actions, and of the companies they’re doing business with. This has led to many operators moving not just to more sustainable practices, but also making more transparent moves in the market, and sharing them. The pandemic has certainly amplified that need, to ensure safe and healthy practices.
But end-to-end supply chain visibility is challenging, to say the least. That’s where modern technologies come into play, thanks to Industry 4.0. IIoT devices, supply-related blockchain applications, machine learning, and big data all have a role to play, and they’re already being used in the industry to great effect. They also provide a host of benefits, which affect even some of the other challenges like resiliency, flexibility, security, and so on.
More visible practices will become commonplace as supply chain operators work together to create a sustainable, open, and secure network.
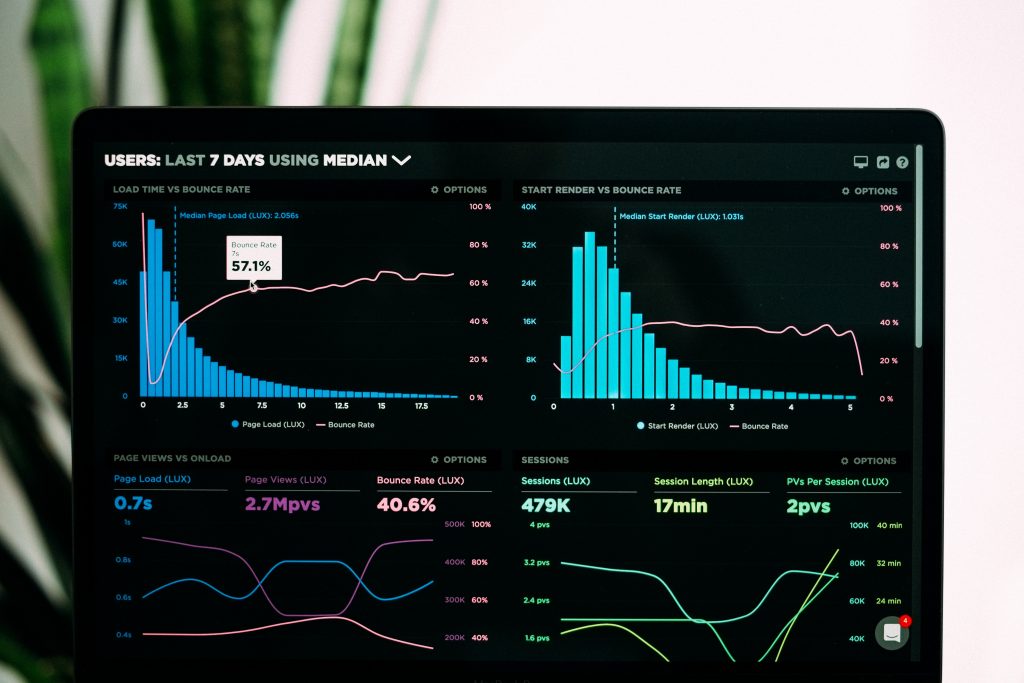
Photo by Luke Chesser on Unsplash
4. Data-Driven Operations
The supply chain has always been powered by data, but digitization takes it to a whole new level. Successful management improves planning in operations, materials-sourcing, production, and distribution.
Machine learning and advanced analytics will highlight new trends, opportunities, and decisions directly related to the market. A predictive model might help account for a demand shift or shortages, before signs of change rear their head. Similar data might empower leaner processes that don’t sacrifice mission-critical redundancies.
That’s what Industry 4.0 is all about: smarter and contextually driven processes that utilize real-time market details to bob and weave with incredibly precise actions. It’s safe to say that no industry has ever seen anything like this before, which is why these technologies have taken root so deeply and rapidly in the modern world.
Many operators have already adopted and deployed data-driven practices in regular operations, so it’s more about discovering new ways to leverage the related solutions. Digital twins have become almost pervasive in the industry, but with the help of artificial intelligence, they can become so much more valuable.
5. International Relations and Trade Agreements
Without touching upon specific events, political or otherwise, the past few years of tumultuous global relations and trade agreements have posed some unique challenges.
In November 2020, 15 countries came together to ratify one of the largest free trade agreements in history — the Regional Comprehensive Economic Partnership (RCEP). While the United States and India withdrew, the agreement still has a significant impact on foreign trade and the supply chain. It should help strengthen the economies in North and Southeast Asia.
Supply chain operators must remain mindful of these changes, along with any on the horizon, and how they might impact the market, relations, and partnerships. Parsing some of these events is a challenge by itself. There is no straightforward answer, unfortunately, but it does highlight the need to maintain a team of experts for understanding and dealing with them.
6. Trade Disruptions
Despite being a mission-critical component of the modern supply chain, the trans-Pacific trade lane has been disrupted in various ways. From ocean rate spikes due to trade tariffs to physical disruptions, much like the Suez canal mishap, there’s an ever-growing need to plan for these events and make up for when they do happen.
It’s impossible to predict some of these events, which is why resilience and flexibility are so important. Supply chain operators will need to form strong partnerships to resolve issues quickly and create new opportunities.
Looking to the Future
The entire supply chain faces formidable challenges, and there are no guaranteed solutions. But that doesn’t mean there’s no way forward. Modern technologies like IIoT and advanced analytics, alongside data-driven operations, can certainly alleviate some of the growing pressure. So can the improved resilience and flexibility of all parties.
Preparing for the future will keep everyone on their toes. But the good news is that there is a light at the end of the tunnel. As the pandemic hopefully winds down, many challenges will become more manageable, as well.
This article is written by Devin Partida. Devin is a tech writer with an interest in the IIoT and manufacturing. She is also the Editor-in-Chief of ReHack.com.
Lean manufacturing and Industry 4.0 are in some ways a case in contrasts. The former is a production methodology designed to reduce operational costs through a combination of process efficiencies, a lighter footprint and smart time management. In short, it’s a system of minimizing waste and maximizing productivity through the barest of essentials. According to a recent research report spearheaded by IndustryWeek, lean manufacturing systems is a major priority among manufacturers in the U.S. today, behind only quality management systems.
Industry 4.0 is next-generation technology, which relies heavily on state-of-the-art equipment, tools, data, and analytics to make automation possible. Here, it’s out with the old and in with the new, made possible by investing in industrial practices and smart technology that expedite production and reduce human error. Often, it’s assumed that Industry 4.0 can replace the human element altogether.
So if lean manufacturing aims to reduce operational expenses, while Industry 4.0 typically requires added spending, are the two mutually exclusive? Not necessarily. It is possible for them to coexist when Industry 4.0 tech is leveraged strategically as a supplement to, not a replacement for, your staff.
Originally appearing in the Lean Enterprise Institute’s blog Lean Post, a classic case in point is a company called Denso, which since its inception, has tried to prioritize its people first and foremost. But the company is now also taking advantage of technology to augment their workers’ ongoing performance.
Must be purposeful about IoT utilization
Headquartered in Japan, Denso specializes in automotive components and is perhaps best known for being Toyota’s largest parts supplier. Many companies these days are using the Internet of Things (IoT) technology to improve processes and enhance output. But as Denso North American Production Innovation Center Vice President Raja Shembekar discovered, IoT is all too frequently not put to its full or proper use. In other words, without proper planning, it has no real problem-solving application, at least among the competitors he observed.
Not being strategic and intentional about IoT implementation — and how it can support workers on the shop floor — raises the risk of not obtaining the intended result: improving output, quality, or ideally both.
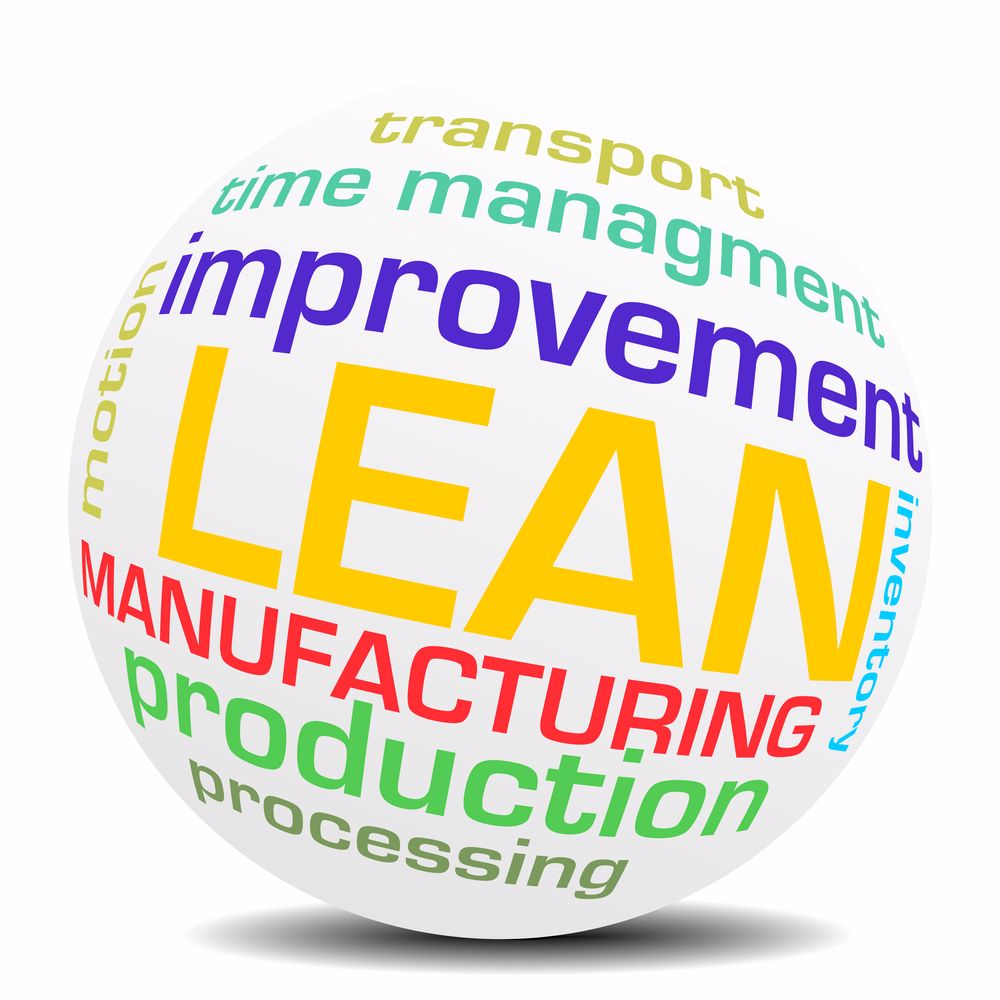
You can stay lean and leverage Industry 4.0 technology all at once.
“Not being strategic and intentional about IoT implementation — and how it can support workers on the shop floor — raises the risk of not obtaining the intended result.”
Concerned that Denso could fall into this tech trap, Raja built a small team composed of quality assurance managers and IoT aficionados to identify where production shortcomings existed and how, if at all, IoT capabilities could potentially fill in the gaps. They found just the thing by placing tiny sensors on cooling fans, which are used to maintain the temperature of brazing ovens for producing aluminum heat exchangers. The placement of said sensors on the fans enabled maintenance workers to swap out fans before they broke, forestalling production issues and avoiding lengthier timelines for parts to be ready for sale.
In short, IoT was able to provide workers with the insight and intelligence they needed to take action as it pertains to installation, supporting their roles. Raja noted that the maintenance team was skeptical about the sensors accurately forecasting when the fans would fall apart, but they played along.
“They took the fan out [and] the blades on the fan had disintegrated,” Raja recounted. “They were totally shocked that they had no idea this was happening and we could provide that prediction.”
As noted by Manufacturing.net, there is a risk in jumping aboard the Industry 4.0 bandwagon, simply because it’s the “in” thing to do. Organizations must first assess what their problems are and whether Industry 4.0 investments can actually solve those issues. This requires a complete assessment of current business processes as they exist and what desired outcomes are if they’re not being realized. Additionally, if Industry 4.0 can optimize the supply chain, as an example, manufacturers must make certain that their supply chain infrastructure can support the adjustments or installations that game-changing technology may entail.
Another way for lean manufacturing and Industry 4.0 to be cohesive is by getting to the bottom of the following question: Does the adoption of machine learning, IoT or some other form of computer-integrated technology supplant or support your team?
Workers expect job losses from AI, just not theirs
The answer will differ for everyone, but what is known is today’s workforce has a love-hate relationship with artificial intelligence. In a 2018 survey conducted by Gallup, approximately 75% of respondents said they anticipate more jobs will be lost than created as a result of AI’s increased adoption. However, only about 1 in 5 — 23% — were worried that their own job was in jeopardy.
While the increased implementation of AI has led to job losses, whether it does or not depends on management philosophy, according to the Lean Enterprise Institute’s blog. A mechanistic approach to business decisions relies heavily on technology, sometimes to the exclusion or replacement of actual workers. From an organic-systems perspective, however — which Raja ascribes — tech takes a backseat to employees who are on the front lines of warehouses, factory floors, and assembly lines.
“Technology provides data that allows the associate and the team leaders at the gemba [factory floor] to provide a far higher level of decision making,” Raja told the Lean Post.
Raja went on to state that at Denso, the addition of Industry 4.0 tech has helped workers make smarter, more well-informed decisions about how to continuously improve and enhance production through PDCA, meaning “Plan-Do-Check-Act.” The goal at Denso is always to leverage tech so it provides work crews with actionable information about the current systems in place so they can react accordingly, not to take those decisions away from them. As Manufacturing.net recommended, it may be worthwhile to perform trial runs of innovative technology to see if it supports or supplants your workforce and where adjustments can be made. In essence, better to “try before you buy.”
For optimal gains when marrying Lean philosophies and Industry 4.0 principles, utilizing an operations management firm may be best. USC Consulting Group has the expertise and experience to help you achieve results by leveraging your existing technology and ensuring that it aligns with your manufacturing philosophy. Please contact us today to learn more about our offerings and how we may be able to help.