-
Subscribe to Blog:
SEARCH THE BLOG
CATEGORIES
- Aerospace
- Asset Maintenance
- Automotive
- Blog
- Building Products
- Case Studies
- Chemical Processing
- Consulting
- Food & Beverage
- Forestry Products
- Hospitals & Healthcare
- Knowledge Transfer
- Lean Manufacturing
- Life Sciences
- Logistics
- Manufacturing
- Material Utilization
- Metals
- Mining
- News
- Office Politics
- Oil & Gas
- Plastics
- Private Equity
- Process Improvement
- Project Management
- Spend Management
- Supply Chain
- Uncategorized
- Utilities
- Whitepapers
BLOG ARCHIVES
- August 2025 (2)
- July 2025 (2)
- June 2025 (4)
- May 2025 (1)
- April 2025 (1)
- March 2025 (1)
- February 2025 (4)
- January 2025 (4)
- December 2024 (4)
- November 2024 (2)
- October 2024 (6)
- September 2024 (5)
- August 2024 (5)
- July 2024 (6)
- June 2024 (3)
- May 2024 (3)
- April 2024 (4)
- March 2024 (3)
- February 2024 (4)
- January 2024 (5)
- December 2023 (2)
- November 2023 (1)
- October 2023 (6)
- September 2023 (3)
- August 2023 (4)
- July 2023 (2)
- June 2023 (3)
- May 2023 (7)
- April 2023 (3)
- March 2023 (3)
- February 2023 (5)
- January 2023 (6)
- December 2022 (2)
- November 2022 (5)
- October 2022 (5)
- September 2022 (5)
- August 2022 (6)
- July 2022 (3)
- June 2022 (4)
- May 2022 (5)
- April 2022 (3)
- March 2022 (5)
- February 2022 (4)
- January 2022 (7)
- December 2021 (3)
- November 2021 (5)
- October 2021 (3)
- September 2021 (2)
- August 2021 (6)
- July 2021 (2)
- June 2021 (10)
- May 2021 (4)
- April 2021 (5)
- March 2021 (5)
- February 2021 (3)
- January 2021 (4)
- December 2020 (3)
- November 2020 (3)
- October 2020 (3)
- September 2020 (3)
- August 2020 (4)
- July 2020 (3)
- June 2020 (5)
- May 2020 (3)
- April 2020 (3)
- March 2020 (4)
- February 2020 (4)
- January 2020 (4)
- December 2019 (3)
- November 2019 (2)
- October 2019 (4)
- September 2019 (2)
- August 2019 (4)
- July 2019 (3)
- June 2019 (4)
- May 2019 (2)
- April 2019 (4)
- March 2019 (4)
- February 2019 (5)
- January 2019 (5)
- December 2018 (2)
- November 2018 (2)
- October 2018 (5)
- September 2018 (4)
- August 2018 (3)
- July 2018 (2)
- June 2018 (4)
- May 2018 (3)
- April 2018 (3)
- March 2018 (2)
- February 2018 (2)
- January 2018 (1)
- December 2017 (1)
- November 2017 (2)
- October 2017 (2)
- September 2017 (1)
- August 2017 (2)
- July 2017 (2)
- June 2017 (1)
- April 2017 (3)
- March 2017 (3)
- February 2017 (2)
- January 2017 (2)
- December 2016 (2)
- November 2016 (4)
- October 2016 (4)
- September 2016 (3)
- August 2016 (6)
- July 2016 (4)
- June 2016 (4)
- May 2016 (1)
- April 2016 (3)
- March 2016 (4)
- February 2016 (2)
- January 2016 (4)
- December 2015 (3)
- November 2015 (3)
- October 2015 (1)
- September 2015 (1)
- August 2015 (4)
- July 2015 (6)
- June 2015 (4)
- May 2015 (7)
- April 2015 (6)
- March 2015 (6)
- February 2015 (4)
- January 2015 (3)
CONNECT WITH US
Tag Archives: Bottlenecks
Manufacturers today deal with greater demands from consumers than ever before. It is vital for manufacturers to deliver on time, every time. Fail to do so and they will lose customers, revenue, and credibility.
Therefore, streamlining operations is essential. This doesn’t mean manufacturers need to invest in expensive equipment or high-performance technology. Often, what needs to change is how people work and the strategies businesses can employ to support this.
Let’s get started.
Why is it so Important to Streamline Manufacturing Operations?
Streamlining manufacturing processes ultimately maximizes a company’s profits and helps them stay competitive. Here are just some of the reasons why it’s so important:
- Increased Customer Satisfaction: streamlining manufacturing operations ensures that customer orders are received and fulfilled faster. Providing great customer service endears your company to your customers and keeps them loyal for the long-term.
- Cost-Effectiveness: every business wants to save money and streamlining operations is one of the best ways to achieve this. A streamlined manufacturing process requires less labor and significantly reduces time spent troubleshooting errors. This leaves more time (and money) for the things that are important – like better meeting customers’ needs.
- More Efficient Work Flow: when you have a streamlined manufacturing process, you have typically ironed out issues and eliminated bottlenecks that were causing delays. This improves the manufacturing process and results in a more efficient workflow. It enables manufacturers to produce goods faster, meet customers’ requests sooner, and achieve all of this without compromising on the quality of the product.
6 Ways Manufacturers Can Streamline Operations
Streamlining operations can feel like an overwhelming task at first. However, with the right strategies in place, it doesn’t take long to improve efficiency and boost productivity. Here are six tips to get you started:
1. Identify Issues in the Production Line
Every manufacturing operation has a bottleneck. This is a stage in the manufacturing process where things slow down or perhaps even stop. Bottlenecks are a nuisance and can lead to severe delays, time and labor inefficiencies, and increased costs. Identifying bottlenecks is essential for optimizing the production line and helping everything run more efficiently.
There are a few ways you can identify issues in your production line. For instance, you should look for signs of the following:
- Long wait times: if there are long wait times for customers or work is delayed because you’re waiting for materials or products to be delivered, this can cause bottlenecks and should be addressed as soon as possible.
- Backlogged work: you may also discover areas in your process where work is backlogged and piling up, causing a bottleneck that is harming your manufacturing efficiency. Taking care of backlogged work as a priority will help relieve these bottlenecks and get your process back up and running again.
- Machine Issues: sometimes machines fail and this could be due to lack of maintenance, outdated equipment, or poor staff training. Identifying machine issues and fixing these can have a huge impact on operation efficiency.
2. Support Faster Payment Processing
As a business owner, you know the importance of faster payment processing. Whether you’re paying your suppliers or your customers are buying your products, faster payment processing keeps everything running smoothly.
The simpler your payment process is, the better so spend time to find the best card reader for your business operation. Streamlining both the supplier and customer experience by offering online payments is a game-changer.
Online payments make it easier for customers to purchase from you, removing delays in the payment process and reducing cash flow issues. This helps streamline operations and keep everything running smoothly.
3. Adopt Lean Manufacturing Methodology
Lean manufacturing methodology focuses on reducing costs by limiting waste and improving manufacturing efficiency. Lean manufacturing is a great methodology to apply to your business if you’re looking to streamline operations.
For lean manufacturing methodology to be effective, all types of waste in the manufacturing process must be identified and then removed. There are four types of waste you should focus on eliminating as a priority. These include:
- Unnecessary transportation of materials such as equipment, tools, and employees can be avoided simply by optimizing factory layouts.
- Excess inventory. Whether it’s products, materials, or equipment, having excess inventory is a waste as it increases storage costs and slows down processes.
- Waiting time: time-wasting is common in manufacturing operations, either due to idle workers or idle machines. It typically occurs when workers can’t work because they’re waiting on materials or equipment. Machines can be idle when waiting on maintenance or replacement. Optimizing manufacturing processes eliminates this time wasting and boosts operational efficiency.
- Defective products are a waste that must be reduced as much as possible. For every defective product, you have an unhappy customer. This means returns are made and apologies are required, which increases costs and wastes time.
Reducing unnecessary waste goes a long way towards reducing lead times, boosting customer satisfaction, and improving operational efficiency. It is a process of continuous improvement and manufacturers will find that regular adjustments need to be made as customer demand fluctuates. However, adopting the lean manufacturing approach will go a long way towards streamlining your operations now and in the future.
4. Embrace Automation
Automation (utilizing production management software or robots to operate machinery) reduces the need for manual labor. It avoids human error and allows for consistency across all aspects of your manufacturing process.
Many areas within manufacturing can benefit from automation, most notably: payment and accounting processes, order processing, marketing efforts, and inventory management (to name a few!)
According to Industrial Machinery Digest, “One obvious byproduct of automation is increased productivity […] The market should see more businesses turning to industrial automation on various scales. When this happens, the market will be able to see not only more innovative products produced on a larger and quicker scale, but the quality increasing with production speed.”
Adopting automation as part of your manufacturing process will help streamline your operations like nothing else. It will allow your organization to keep up with customer demands and grow as your business grows.
5. Reduce Downtime (where possible)
As mentioned earlier in this article, many things can cause your processes to bottleneck. One of these is downtime.
Downtime is a significant cause of inefficiency in the manufacturing process. Therefore, finding ways to reduce it can improve efficiency. A few common causes of downtime are:
- Machine maintenance requirements
- Equipment failure
- Employee absenteeism
- Bottlenecks in the process
- Human error
To improve on these it is important to monitor your production processes closely. This will let you identify and address any issues quickly and efficiently.
6. Train Employees Well
For employees to do a good job and support a streamlined manufacturing process, they need to know what they’re doing and proper training supports this. Proper employee training is a surefire way to improve efficiency, boost company morale, and support business success.
Establishing an effective team through professional training lets employees add real value to your business by preparing them for higher responsibilities, increasing their productivity, strengthening any weaknesses, improving workplace safety, and boosting production overall.
If you want to streamline your manufacturing operations, it is essential that you properly train your employees. This will go a long way towards supporting your business success.
In Summary
We hope the tips shared in this article have highlighted the importance of optimizing your manufacturing processes and how to achieve this! We know that streamlining your operations can feel a little daunting at first (we’ve all been there!) But with the right strategies we know you can transform your manufacturing process and take your business to new heights.
*This article is written by Sophie Bishop. Sophie is an experienced construction writer with a passion for sharing insights and her experience within the health and safety sector. Sophie aims to spread awareness through her writing around issues to do with healthcare, wellbeing and sustainability within the industry and is looking to connect with an engaged audience. Contact Sophie via her website: https://sophiebishop.uk/.
Are you always putting out fires? Not in the literal sense, of course. We’re talking about operational problems that pop up at the most inconvenient times. Once you take care of one issue, two more seem to appear in its place. Issues such as:
- Machines break down
- Workers calling in sick
- Human errors
- Backups and bottlenecks
- Inventory uncertainty
If you’re busy troubleshooting today, it’s hard to focus on improving tomorrow. Opportunities for growth can be missed.
Get ahead of problems before they catch fire by watching this video:
At USC Consulting Group, we’ve been helping clients for over 50 years to implement strong Management Operating Systems that assist them with breaking that firefighter mentality.
The best management operating systems center around four main components:
- Processes
- Systems
- Roles
- Structures
A well-designed MOS will have your company operating like a well-oiled machine, making your bottom line stronger and your operations more efficient.
So put down the fire extinguisher and enhance your management operating system today by contacting USC Consulting Group.
Phone: +1-800-888-8872
Email: info@usccg.com
Learn more about the benefits of an effective MOS in our article How Can A Management Operating System Help Your Organization?
Does it seem like you’re always putting out fires? Not in the literal sense, of course. We’re talking about operations problems and snafus that seem to pop up at the most inconvenient times. Machines break down. Workers call in sick. Human errors can result in costly fixes. Unforeseen backups or bottlenecks slowing things down. Too much inventory. Not enough inventory. Some days, it can seem like you’re in a constant state of troubleshooting. The problem with that is, it’s hard to move forward into tomorrow when you’re consumed with putting out the fires of today.
Sound familiar? You’re not alone. At USC Consulting Group, we hear it a lot from the clients we partner with to increase efficiency and streamline operations at their facilities. Over the years, we’ve learned that the best course of action to break the cycle of constantly putting out fires is to get ahead of those problems before they become “fires.” Easier said than done, right? Actually, no. The way to do it is to implement an effective Management Operating System (MOS).
MOS 101
What is a Management Operating System, or MOS? Without using industry jargon, a MOS is simply a structured approach to operations. It’s intentional, forward-looking and at times anticipatory, in that it can help spot trouble before it spots you.
A good MOS is a set of tools, processes and frameworks that guide the operations of your business, namely the way employees work. It fosters continuous improvement to address issues as they occur. Or, ideally, before they occur.
Because many of the “fires” you’re stamping out every day can range from production shortfalls to problems related to worker safety, companies that use production lines or have other types of hazardous workplace environments commonly employ management operating systems.
Your MOS should be able to spot inefficiencies in an operating system before they become major problems. This ensures that adjustments can be made so operations are not adversely affected. An MOS should also use real-time feedback so an organization can safely direct operations, funding and other resources to maximize return on investment.
The best management operating systems center around four main components:
- Processes
- Systems
- Roles
- Structures
In other words, it maps out how the job gets done, in what way and by whom.
Let’s look at that in a little more detail.
When designing processes, businesses must be sure that they’re safe, secure and clear for employees to understand and tools are used to support operations — and never in ways that are not dictated by the overall structure. This means users should not use tools in inappropriate ways, especially those that could simply automate their inefficient methods. One process change we always recommend is preventative maintenance. Taking a little downtime today to service your machines can save major work stoppages tomorrow.
An effective MOS uses well-designed systems that help employees and the company as a whole achieve goals, which means they should run smoothly and enhance and even boost established efficiency.
Roles within an MOS should adhere to clearly defined job descriptions that require certain skill sets, and when combined with a business’ processes and systems can best utilize talents. The skills gap has only complicated the matter, but that’s fodder for another blog.
The best-run management operating systems always establish a business-wide structure upon which the different roles within the company interact. This is usually done last because it ensures that the processes do not dictate the entire established structure and cause further issues.
Read more about it in our blog, “How Can a Management Operating System Help Your Organization?”
Benefits of using a good MOS
Putting a carefully planned management operating system in place, one that is unique to your organization and its challenges and strengths, can result in a boatload of positive benefits. According to CEO Magazine, an MOS allows for an organization to “better control the flow of work and production, driving higher outcomes in customer service, quality and cost.”
At a minimum, these systems make use of tools that allow organizations to create plans for future work in certain operations, carry out that work, and then measure the work performance data to suggest future improvements that could be needed.
At maximum? Your company will perform with operational excellence, humming along at capacity, anticipating hiccups before they become problems, planning for growth or even downturns so you won’t be taken by surprise and generally making your life easier and your bottom line stronger.
Other ways an MOS can benefit you and your company:
- Cost savings
- Waste reduction
- Increased product quality
- Identification of workflow gaps
- Find ways to improve efficiency
- Get a handle on any compliance issues or regulations
- Elimination of impediments to your workflow
- Inventory wrangling (so you don’t have too much or too little despite supply chain bottlenecks)
A word about technology. Sure, you can automate your management operating system. Many companies do. But in our opinion, it can’t match good, old-fashioned brainpower, experience garnered through years on the line, common sense of longtime employees and forward-thinking ideas.
Ready to stop the firefighting mentality and talk about it? Give us a call or email us at info@usccg.com. We’ll listen first and then collaborate with you on a path toward operational excellence. It’s what we do.
This is the story of William the Conqueror.
No, not the 11th century figure, but William the Vice President of Operations at Acme Widget Company who becomes the Savior of Operational Improvements. William is under siege with problems that are eating into operational efficiency, causing delays and slowing down his throughput. There’s trouble on the line. Machinery breakdowns are causing delays. William’s supervisors aren’t communicating issues during shift changes. And William is struggling to hire and retain skilled employees to get the job done.
The result of this operational onslaught? Acme Widget Company is not meeting its demand at a critical time. William is getting frustrated with the delays, breakdowns and inefficiencies. So is his boss.
That’s when William called USC Consulting Group — an operations management consulting firm that has been helping companies identify trouble spots, reduce operating costs, and increase efficiency and throughput for more than 50 years.
Working with William, USC Consulting Group investigated the Five M’s:
- Machine (Does it need maintenance?)
- Methods (Can you make processes more efficient?)
- Materials (Supply chain bottlenecks?)
- Measurements (Are we measuring the right things?)
- Man or Woman (Are your people skilled and trained?)
Focusing on the five Ms and with USC’s help, William and his team got things running smoothly, with improved efficiency and increased throughput. William’s boss was so pleased with the results that he promoted William to COO*.
William had, indeed, conquered his operational issues.
Moral of the Story: William is not a real person, however, the struggles he and his team were experiencing are a reality for many executives today. Are you experiencing issues like William’s? Would you like to discover operational improvements in your business to increase your throughput and efficiency? Give USC Consulting Group a call at 1-800-888-8872 and we will put our expertise to work for you.
*You may not get promoted to COO, but you will increase your operation’s efficiency.
In part 1 of this blog series about logistics, we talked about the state of the industry today. Summed up in one word: Chaos.
We who work with logistics have seen supply chain disruptions before. But nothing like this. Foreign manufacturing partners can’t get the materials they need to do the job. If product is manufactured and loaded onto a cargo ship, there’s every chance that ship will be floating offshore, not allowed to enter a port because of pandemic travel restrictions and complex testing requirements. CNN recently reported that some workers on cargo ships have been onboard for a full year because they can’t get off due to COVID restrictions. If the cargo gets to the port, the containers are stacked up like so many Legos because the trucking industry is experiencing an unprecedented labor shortage — there’s nobody to drive the trucks that haul the cargo to its destination.
The perfect logistics storm. And in its wake, angry consumers, burned-out employees across the logistics spectrum, and frustrated business owners and managers who just want to get their product to market.
What’s being done about it
The White House launched the Supply Chain Disruptions Task Force in June, which focused on bottlenecks that are bedeviling everyone in the logistics industry. As part of that, President Biden named a “Port Envoy” specifically charged with driving coordination between private companies who run the transportation industry and the logistics supply chain.
One recommendation from the task force: Keep California ports open 24/7.
That’s all well and good. But many in the logistics industry say it solves only part of the problem. Brian Bourke, chief growth officer at logistics firm Seko, summed it up nicely in an interview with Bloomberg. He said the 24/7 port schedule mandate is pointless without trucks to pick up the cargo at the port and warehouses being open to receive it. He said touchpoints at all levels of the process need to be in sync to solve the problem. “Everything is connected … that’s why they call it a supply chain.” Good point.
What logistics companies can do
In part 1 of this blog series, we highlighted some actions logistics companies can take right now. It’s about streamlining and perfecting operations, making processes on your end bulletproof, and making sure you’re functioning at the highest capacity. It won’t solve the pandemic problem and it won’t get all of those containers out of ports if truckers aren’t on the job, but you will be doing what you can.
Some of our recommendations included:
Rethink foreign supply chains. Having Asia as a supply partner has long been seen as a way to cut costs. But those cheaper costs come at a price when the supply chain breaks down. Finding more domestic partners is a must.
Make operations more efficient. Look at your own house with a 360-degree perspective to make sure you’re as efficient as possible.
Use SIOP to perfect supply levels. For more information on SIOP and how it can increase your operations efficiency, download our free eBook, Sales, Inventory and Operations Planning: It’s About Time.
Ramp up your hiring. Rethink your pay, benefits, PTO and other perks for the hands you need to get product from point A to B.
For a more detailed look into these recommendations, read “Moving logistics forward from the great bottleneck of 2021: Part 1.”
26th Annual Third-Party Logistics Study
In September, NTT Data released their 2022 26th Annual Third-Party Logistics Study, which highlighted how the industry is managing through the worst crisis in decades. The report has several areas of insight into how logistics companies can move forward, and what logistics peers are thinking.
Here are some highlights from the report:
The intelligent supply chain: The role of technology
The report states “new technology holds the potential to uncover opportunities, increase efficiency and reduce risk within the supply chain, and technology continues to play a critical role in the supply chain. This year’s study respondents reported that promising technologies include 5G, real-time data transmission, Internet of Things and data analytics.”
- 52% of shippers and 63% of 3PLs said 5G technology is either moderately or critically important.
- 63% said they are investing in Internet of Things technology to improve workforce productivity, while 57% said it will improve real-time decision-making and create a competitive differentiator in the market.
- Shippers are focused on increased investment in intelligent data analytics (26%), robotics (20%) and autonomous forklifts (20%).
Cold chain: Planning and moving sensitive loads
According to the report, “the cold chain, which handles everything from ultra-cold vaccine distribution, to fresh food, is critical, and each link must stay connected flawlessly to ensure the quality and safety of temperature-sensitive products. To help meet demands, shipper respondents with cold chains reported a mix of in-house, partially outsourced and fully outsourced services.”
- 89% of shippers reported have a solid cold chain strategy.
- Most shippers, 91%, and 3PLs, 100%, said they expect demand for cold chain capacity to increase over the next three years.
- Both shippers (70%) and 3PLs (52%) said COVID-19 has accelerated their growth plans, increasing their need for more cold chain capacity.
- 70% of shippers said they expect to grow inhouse cold chain capabilities and talent over the next three years.
- 50% said they plan to outsource more of their cold chain capabilities. About 90% of 3PLs said they plan to expand their cold chain capabilities and service offering.
The effects of COVID-19
The study states, “COVID-19 drew national and global attention to the supply chain and highlighted the need for contingency planning and risk mitigation strategies. Researchers took a deeper look at the effect the pandemic had on shippers and their logistics providers as well as how their experiences have shaped their future plans.”
- 96% of 3PLs and 100% of shippers said they are enhancing their readiness and continuity planning. The top five areas 3PLs are currently working to improve based on current approved projects and budgets are data analysis and visibility (50%), labor management and scheduling (48%), domestic transportation and logistics (38%), and warehouse distribution and operations (38%).
- Shippers reported currently working to improve demand forecasting (42%), capacity forecasting (40%), international transportation and logistics (38%), supply chain network design or redesign (36%), and data analysis and visibility (33%).
Rebalancing supply chains
According to the study: “For years supply chains focused on reducing inventory levels and cutting costs, but the past year has drawn attention to the risk of becoming too lean. A move to just-in-time inventory has impacted the resilience and agility of supply chains to respond to significant disturbances, and this year’s Annual Third-Party Logistics Study looked at shippers’ plans to rebalance supply chains.”
- 68% of shippers believe that supply chains have become too global and must be rebalanced toward more regional and local/domestic ecosystems within larger global enterprises.
- 83% of shippers said they plan to adjust sources of supply as a direct result of efforts to rebalance toward regional and local/domestic sources.
- For shippers, several factors are contributing toward global rebalancing, including increased need for supply chain resilience (71%), increased awareness of supply chain vulnerabilities (63%) and more restrictive trade policies (41%).
For a deeper dive into these areas, download the entire report here.
At USC Consulting Group, we’ve been helping companies find efficiencies in the midst of challenging times for more than 50 years. Contact us today to learn more.
When is the last time you can remember logistics dominating the headlines? Rarely has this industry gotten this much press. That’s because the public is feeling what we who work with logistics have known for awhile — bottlenecks and supply chain disruptions have led to an unprecedented level of delay transporting goods from point A to point B.
Foreign suppliers have been stymied because of travel restrictions as a result of complex and confusing vaccination and testing processes. But even when the cargo arrives, ports on both coasts of the U.S. are filled to the brim with container ships, backed up like a logjam because there are no trucks available to transport those containers to where they need to go.
As anyone involved with the industry knows, logistics is the unsung hero of the American economy. The public rarely thinks about how the product they’re putting into their grocery cart made its way to the store, but they sure notice when it’s not on the shelf.
The problem has gotten so bad that it has captured the attention of the media and even the White House.
All eyes are on logistics right now
This past month, logistics and supply chain disruptions have been the lead story on the evening news night after night, with reporters stationed at ports shooting footage of the enormous backlog of containers. News articles are advising consumers on how to plan for empty shelves in their local grocery store or worse yet, the toy stores around the holidays. Remember the toilet paper shortage of 2020? It’s on the horizon again. Parents are urged to shop now for holiday gifts for their kids.
The problem has become so dire that the White House launched the Supply Chain Disruptions Task Force in June, which focused on bottlenecks that are bedeviling everyone in the logistics industry. As part of that, President Biden named a “Port Envoy” specifically charged with driving coordination between private companies who run the transportation industry and the logistics supply chain.
At the UN General Assembly earlier this fall, heads of state worldwide got a letter from the International Chamber of Shipping (ICS) warning of a global transport system collapse if governments don’t restore freedom of movement to transport workers.
The government doesn’t have to tell the logistics industry about the problems it has been facing since 2020. And typical bureaucratic red tape might suggest they’re not going to snap their fingers and fix what’s wrong immediately. So what can logistics companies do to make sure the goods they deliver will keep rolling?
At USC Consulting Group, we’ve been helping companies navigate all types of crisis situations for more than fifty years. In this two-part blog, we’ll highlight some of the strategies we’re recommending to our clients.
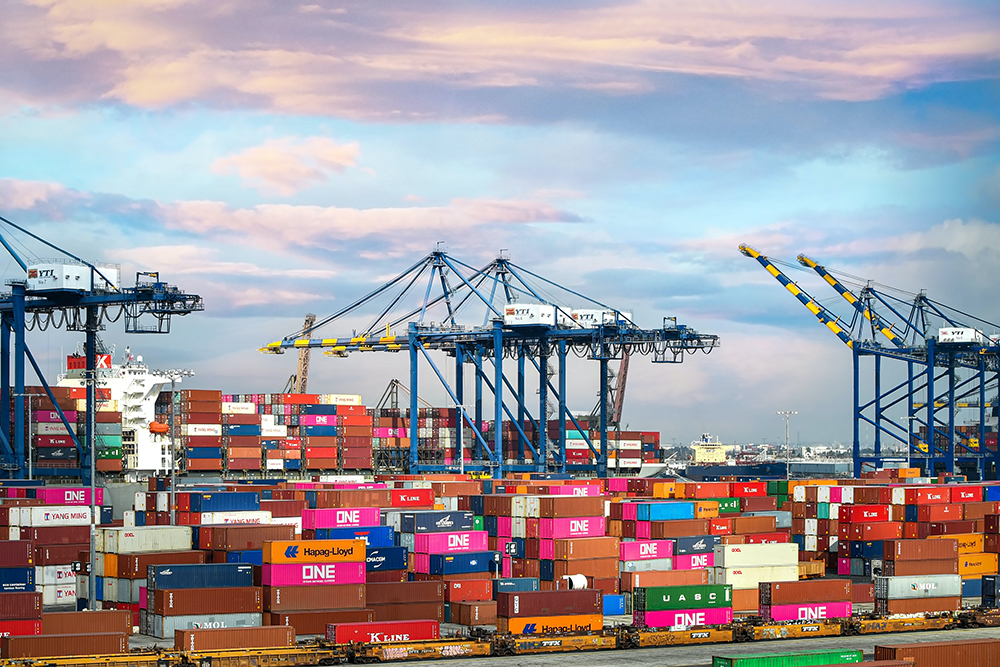
Shipping containers pile up at the Port of Los Angeles
Rethink foreign supply chains
Having Asia as a supply partner has long been seen as a way to cut costs. But that business model had been fraying at the edges even before the pandemic unraveled it. According to the 2022 26th Annual Third-Party Logistics Study, 83% of shippers saw supply chain disruption this year, and 68% of logistics pros believe supply chains have become too global. Looking for domestic suppliers is vital. And it’s not necessarily about the pandemic. Yes, the issue of pandemic-based restrictions and hold-ups exists now, but when this pandemic is in our collective rear-view mirror, it’s still vital to have more domestic suppliers. That’s because trade policies, diplomatic relations, tax laws, and governmental regulations can change, putting your supply chain in jeopardy.
Make operations more efficient by taking a 360-degree look
We specialize in making operations more streamlined by looking for hidden opportunities for efficiency that exist in your current processes and procedures. Will this solve the problem of your containers sitting at a port instead of being on the road? No. But making sure your internal operations are running at optimal efficiency will help balance your bottom line in the event more slowdowns occur.
Use SIOP to perfect supply levels
You’re probably familiar with sales and operations planning (S&OP), a process that involves sales forecast reports, planning for demand and supply, and other factors. It’s useful, but we think it’s incomplete. Inventory is left out of the mix. If you’ve been using S&OP, we encourage you to use sales, inventory, and operations planning, that factors in your all-important inventory. For more information on SIOP and how it can increase your operations efficiency, download our free eBook, Sales, Inventory, and Operations Planning: It’s About Time.
Ramp up your hiring
The trucking industry in particular is stretched extremely thin when it comes to drivers. All industries are experiencing a hiring crunch right now, and logistics needs to step up its hiring game to entice more people to sign on to the great jobs in transportation. That means competitive pay, solid benefits, and generous PTO.
In Part 2 of this topic, we look deeper into the Third-Party Logistics Study and go into more recommendations for moving logistics forward.
Go to Part 2 of Moving Logistics Forward series →
Do you know what’s preventing your operations from being more efficient? Find the clues that will tell you where to look. The key to doing more with your existing assets is uncovering hidden opportunities for efficiency and increased productivity. Things you might not even see that are right under your nose.
That’s where USC Consulting Group’s expertise comes in. After 50+ years, we’ve become skilled detectives. Uncovering those hidden opportunities is our specialty. We often find them by looking at issues that are accepted in the workplace as “That’s the way we’ve always done it.”
We uncover hidden efficiencies by asking questions:
- Where is the bottleneck?
- Is it technical?
- Is it tactical?
If it’s about technology, or your assets, maybe it’s time to bring in the engineers to improve on your machines’ functions.
If it’s tactical, we look at your processes to find areas of improvement.
For more on how the subject matter experts at USC Consulting Group detect inefficiencies in our clients’ operations, watch as Detective Payne points the way:
If you’d like to find more efficiency in your operations, get in touch. We’ll put our expert detective work to use for you.
Nobody knows the job better than your frontline employees. So, when you’re instituting new efficiencies to improve the processes and procedures that they use on the job every day, one vital key to success is getting their buy-in from the get-go.
At USC Consulting Group, helping companies find process improvements is what we do. We work with companies in industries like manufacturing, mining and metals, oil and gas, food and beverage, transportation and logistics, and others to become more efficient, effective and in the end, profitable. We strive to empower your performance and help you reach your highest potential by uncovering greater operating excellence across the entire supply chain. It’s about identifying and eliminating wasteful practices and procedures.
One big difference between us and the other guys is how we go about doing that.
We sell our methodology and our process, not just a solution
Nine times out of ten, when companies come to us, they already have a pretty good idea of what their challenges are. So we don’t go into a client engagement telling them what we think they should do. We have over 50 years in this industry behind us, but all of that experience doesn’t mean we provide cookie-cutter solutions. Most of our clients are looking to us to break bottlenecks in their operation, find out if they can do more with what they have, or even do more with less. But every one of our clients is unique. Every one of those bottlenecks has a different cause. The only way to find the best road that will lead to more process efficiencies is not to rest on our laurels and do what worked for the last client, but to roll up our sleeves, get into your operation and see what’s going on.
A big part of that is listening to your frontline people.
Your frontline employees are the key to the success of the project
We don’t simply sit in your boardroom and pontificate with your C-suite about how to do things better. At USCCG, we believe it’s about effecting change at the point of execution. That means we involve your frontlines. Ferreting out new processes and solutions that can increase efficiencies starts with the people actually doing the job. It’s the only way it’s going to work. Here’s why:
A single source of truth. By talking to your frontline employees, we get the lowdown on what’s happening in your operation day to day. We hear what’s going right, and at times, what’s going wrong. They often can see what the problems are, but not know how to fix them. We can get the single source of truth from your frontlines and implement plans to fix the issues and improve productivity. It’s crucial to finding where efficiencies can happen.
From resistance to change… We get it; change is difficult to accept. More than that, it can be threatening. Frankly, it’s completely counterproductive to swoop in and tell people that the way they’ve been doing their jobs for years is inefficient at best and wrong at worst. You’ll lose their cooperation. They’ll be resistant to any new ideas, because those new ideas mean the way they’ve been working has been wrong. If you don’t get their cooperation, it can be difficult to implement any sort of process changes. And if you have their opposition, it can be downright impossible.
…to drivers of change. That’s why involving your employees in the process from the start is so important. It ensures they’ll feel listened to and respected. It won’t be something that’s happening to them. Positioning this process as a way to harvest their wealth of frontline information in order to make the company more effective and efficient is the key to making it work. We involve employees from the get-go, and time and time again, we’ve seen them become the drivers of change.
Making the changes stick. Initial buy-in is only the beginning of the importance of your employees to this process. It goes further than that. It’s about making sure those changes stick. Your employees need to feel invested in the process changes in order for them to stick to them, on the job, every day. That’s why we don’t come in and hand them a new playbook. They’ll help write it. And that’s crucial to the success of implementing change.
At USC Consulting Group, we understand how important employees are in the process of change. We will respect them, listen to their institutional knowledge that only years on the job day after day can provide, and create a collaborative approach to finding the hidden opportunities for greater efficiency in your operation.
For more information about how we work during this time of COVID, download our free eBook Times have Changed – USCCG Can Help You Adapt.