-
Subscribe to Blog:
SEARCH THE BLOG
CATEGORIES
- Aerospace
- Asset Maintenance
- Automotive
- Blog
- Building Products
- Case Studies
- Chemical Processing
- Consulting
- Food & Beverage
- Forestry Products
- Hospitals & Healthcare
- Knowledge Transfer
- Lean Manufacturing
- Life Sciences
- Logistics
- Manufacturing
- Material Utilization
- Metals
- Mining
- News
- Office Politics
- Oil & Gas
- Plastics
- Private Equity
- Process Improvement
- Project Management
- Spend Management
- Supply Chain
- Uncategorized
- Utilities
- Whitepapers
BLOG ARCHIVES
- June 2025 (4)
- May 2025 (1)
- April 2025 (1)
- March 2025 (1)
- February 2025 (4)
- January 2025 (4)
- December 2024 (4)
- November 2024 (2)
- October 2024 (6)
- September 2024 (5)
- August 2024 (5)
- July 2024 (6)
- June 2024 (3)
- May 2024 (3)
- April 2024 (4)
- March 2024 (3)
- February 2024 (4)
- January 2024 (5)
- December 2023 (2)
- November 2023 (1)
- October 2023 (6)
- September 2023 (3)
- August 2023 (4)
- July 2023 (2)
- June 2023 (3)
- May 2023 (7)
- April 2023 (3)
- March 2023 (3)
- February 2023 (5)
- January 2023 (6)
- December 2022 (2)
- November 2022 (5)
- October 2022 (5)
- September 2022 (5)
- August 2022 (6)
- July 2022 (3)
- June 2022 (4)
- May 2022 (5)
- April 2022 (3)
- March 2022 (5)
- February 2022 (4)
- January 2022 (7)
- December 2021 (3)
- November 2021 (5)
- October 2021 (3)
- September 2021 (2)
- August 2021 (6)
- July 2021 (2)
- June 2021 (10)
- May 2021 (4)
- April 2021 (5)
- March 2021 (5)
- February 2021 (3)
- January 2021 (4)
- December 2020 (3)
- November 2020 (3)
- October 2020 (3)
- September 2020 (3)
- August 2020 (4)
- July 2020 (3)
- June 2020 (5)
- May 2020 (3)
- April 2020 (3)
- March 2020 (4)
- February 2020 (4)
- January 2020 (4)
- December 2019 (3)
- November 2019 (2)
- October 2019 (4)
- September 2019 (2)
- August 2019 (4)
- July 2019 (3)
- June 2019 (4)
- May 2019 (2)
- April 2019 (4)
- March 2019 (4)
- February 2019 (5)
- January 2019 (5)
- December 2018 (2)
- November 2018 (2)
- October 2018 (5)
- September 2018 (4)
- August 2018 (3)
- July 2018 (2)
- June 2018 (4)
- May 2018 (3)
- April 2018 (3)
- March 2018 (2)
- February 2018 (2)
- January 2018 (1)
- December 2017 (1)
- November 2017 (2)
- October 2017 (2)
- September 2017 (1)
- August 2017 (2)
- July 2017 (2)
- June 2017 (1)
- April 2017 (3)
- March 2017 (3)
- February 2017 (2)
- January 2017 (2)
- December 2016 (2)
- November 2016 (4)
- October 2016 (4)
- September 2016 (3)
- August 2016 (6)
- July 2016 (4)
- June 2016 (4)
- May 2016 (1)
- April 2016 (3)
- March 2016 (4)
- February 2016 (2)
- January 2016 (4)
- December 2015 (3)
- November 2015 (3)
- October 2015 (1)
- September 2015 (1)
- August 2015 (4)
- July 2015 (6)
- June 2015 (4)
- May 2015 (7)
- April 2015 (6)
- March 2015 (6)
- February 2015 (4)
- January 2015 (3)
CONNECT WITH US
Tag Archives: Asset Maintenance
Are you performing preventive maintenance on a regular basis? If you’re not, you may want to consider adding it to your schedule. Why? In a word, it’s about efficiency. In a few words (as its name suggests), it prevents problems before they start. Preventive maintenance is becoming the manufacturing industry standard. Roughly 80% of asset and facilities stakeholders are embracing the process as a way to cut costs, increase efficiency, and keep assets running like clockwork.
By performing regular preventive maintenance (or its cousin, data-based predictive maintenance) you are heading off problems, snafus and breakdowns at the pass. It’s about identifying and handling any potential issues that may be lurking down the road. The point is to find potential problems before they become real problems that could lead to delays and costly headaches.
The irony of preventive maintenance is that it can sometimes seem like it causes more problems than it solves. It requires regular downtime, which in itself is a problem. There’s also the tricky matter of timing. Finding the optimal time to perform the maintenance can be a delicate balance between shutting down for maintenance too soon and waiting too long.
But, the challenges are worth the rewards. Ensuring you have the proverbial well-oiled machine will make your operation more efficient and productive now and in the future.
Let’s take a look at preventive maintenance benefits and challenges and how it can help boost your operations.
Preventive maintenance benefits
The idea behind doing regular maintenance on the lifeblood of your manufacturing operations — your machinery — is to keep it humming along at optimal efficiency and prevent any problems that might occur. Benefits to making it a regular part of your business process include:
You control the downtime schedule. It’s true that performing maintenance requires downtime. You’ll experience a work stoppage because of it. However, the good news is, when that downtime happens is up to you. You can schedule it for slow periods and avoid your high-volume times. Build maintenance into your schedule as a regular part of your routine.
Fewer surprises. A snafu happens, something breaks, and you have to stop production to figure out what it is and fix it. That can happen at any time, and trust us, it will happen when you least want it to. Performing preventive, not reactive, maintenance will lessen those unwelcomed surprises that erode your productivity and profitability. A general rule is that planned work will cost two-thirds less than unplanned work in time and other resources.
Increased efficiency. At USC Consulting Group, we’re all about efficiency, and one of the surest ways to find “hidden efficiencies” that you didn’t even know were possible is to perform regular preventive maintenance on your machines.
Increased longevity of your machinery and assets. This is key. Just like your car needs regular oil changes and tune-ups to keep it running at its best, so do your assets.
Preventive maintenance challenges
There are some challenges with doing regular preventive maintenance. However, in our view, these don’t outweigh the benefits.
Finding the optimal time to do it is tricky. A regular schedule is the key to finding the best time to shut down for maintenance. And the downtime is typically where we see the most pushback from executives and managers who aren’t thrilled with this process.
It will cause shutdowns. There’s no way around it. To perform maintenance on your equipment, the line must stop.
If it ain’t broke, don’t fix it. This is an old adage for a reason. You may be shutting down for your scheduled maintenance when no problems actually exist. The shutdown does come at a productivity cost, so… is it worth it? Some manufacturers solve this issue by performing predictive maintenance instead. It’s a more complex process that is data driven, and analyzes how your assets are performing in real time. All’s well? No shutdown. But if you find problems, that’s when you act. It reduces downtime, and you’re not replacing any parts while they’re still good to go. The downside of this approach is complexity and connectivity. If you don’t have state-of-the-art machinery, you won’t get the data analytics that this process requires. That’s why the majority of manufacturers today are using the preventive approach.
At USC Consulting, we’ve been helping manufacturing businesses increase their efficiency, production, throughput and profits for more than half a century. Get in touch today if you’d like to learn more about how preventive maintenance benefits can boost your bottom line.
Workplace injuries are frighteningly common. While incident rates have declined over time, there were 2.8 million nonfatal workplace accidents in both 2018 and 2019. Few things are as important as the safety of your employees, so facilities must prevent these incidents.
Every facility has unique conditions and concerns, but some steps can improve safety in any industrial workplace. Here are five of the leading ways you can keep your employees safe.
1. Prioritize Safety Training
The most crucial step in improving workplace safety is providing thorough training. Make sure you teach all employees proper safety procedures as well as why these policies matter. If they understand the risks that your protocols prevent, they’ll be more likely to follow them.
In addition to general safety training, you should instruct workers on the specific considerations for their position.
For example, anyone who has to operate a forklift should receive additional training on safe forklift operations. It’s not enough to only go over these procedures upon hiring, either. Hold regular refresher sessions to ensure no one forgets crucial safety procedures.
2. Take Advantage of Technology
Even with thorough training, employees won’t be able to avoid all hazards. New technologies can help you account for these blind spots. For instance, wearable tech can detect when a forklift or other employee is around the corner, even if a worker can’t see or hear them. The device can then alert them to stop, preventing a collision.
Similar devices can monitor signs of fatigue in workers. If it senses they’re nearing a state where it would be dangerous to work, it can warn them to take a break. Since overexertion and bodily reactions are the most common workplace injuries, these warnings can lead to substantial improvements.
3. Maintain All Machinery
Machinery is one of the most common sources of injury in an industrial workplace. When equipment malfunctions, it can pose a threat to even the most careful employees. To prevent these accidents, you should perform regular maintenance on all machinery.
Maintaining equipment on a schedule is safer and often more cost-effective than using it until it breaks. An even better method is predictive maintenance, which uses sensors to predict when a machine will need maintenance. This avoids unnecessary repairs, saves time and money, and prevents dangerous breakdowns.
4. Create an Emergency Response Plan
While addressing these everyday hazards, remember to prepare for emergencies, too. Roughly one quarter of businesses would be unable to reopen after a disaster. You can avoid becoming part of that statistic by creating and practicing an emergency response plan.
You don’t need a response plan to every type of disaster, but you should craft one for the most likely scenarios in your area. Identify which emergencies are most likely, then develop a response and recovery plan. Remember to train all employees in this plan and run drills periodically so everyone knows what to do should an emergency arise.
5. Foster a Culture of Responsibility and Safety
Finally, you should try to cultivate a company culture of safety. If safety is part of your workplace’s atmosphere, employees will make better choices and spot potential hazards as they arise. While a “culture of safety” is difficult to quantify, there are steps you can take to foster one.
Ensure all managers and team leaders lead by example by going above and beyond company safety policies. You should also establish and promote a straightforward, two-way communication system so workers can express their concerns.
You could also consider instituting a reward system for employees who exhibit safe behavior or recommend valuable safety changes.
Keep Your Workers Safe
Industrial facilities are often dangerous places to work, but they don’t have to be. If you follow these steps, you can create a safe work environment for all employees. You’ll protect your workers as well as improve efficiency and morale.
This article is written by Devin Partida. Devin is a tech writer with an interest in the IIot and manufacturing. She is also the Editor-in-Chief of ReHack.com.
As a typical rule of thumb in maintenance, planned work will consume roughly one third of the resources (labor cost, materials cost, and costs associated with equipment down-time) as unplanned work will consume. Therefore, the first objective of any maintenance program can be simplified as maximizing the percentage of time and resources spent on planned maintenance, and reducing the amount of unplanned maintenance or repair work resulting from unexpected breakdowns.
Understanding the Types of Work
Planned work can be broken down into two main categories: preventative maintenance and planned repairs. Preventative maintenance includes all the work done not in response to a failure, but to prevent future failures from occurring. This work is typically outlined by the manufacturer in terms of frequency and work that must be performed (oil change, lube, and filter). If the fleet size remains constant, so will the level of preventative maintenance. Planned repairs are work that must be done as a result of wear and tear in which the equipment has not yet failed and can still run reliably until the maintenance department is set up with the required materials, labor, and shop space to adequately address these repairs. For exemplary purposes in this article, we will consider maintenance needed for an underground mine as a model. Due to the travel time in underground mining and the requirement in most cases to have repairs done in the shop after a wash, these two types of planned work are best done together to minimize the mechanic’s trips to and from the equipment.
Given that the level of preventative maintenance will remain considerably flat, as both the materials required and time required can be predicted and cyclical, the only way to effectively increase planned work as a proportion of total work is to increase the level of planned repairs. The first task is to shift the balance of planned maintenance and unplanned maintenance. That is, to convert as much of the resources spent on unplanned work as possible into resources spent on planned work.
Converting Unplanned Work into Planned Maintenance
The first step is to create a backlog, a master list of all known repairs that must be made to each piece of equipment. It consists of repairs necessary to components that are in a partial state of failure, but have not yet failed. The size of a backlog and how well it is managed will provide some valuable insight as to the over-all health of your assets. A complete detailed backlog will also provide other benefits to management when taking a closer look at each type of equipment and analyzing which components require more attention than others. If repairs to equipment must be done before the equipment actually fails, the ability to identify or predict failures before they actually occur will be crucial. Coordination can then be made for the replacement of these components before failure occurs. This can be a very difficult and daunting task when considering a large fleet with complex equipment.
The first element to be considered when creating and managing a backlog is where the backlog work will be sourced from. Where will the maintenance planners get the information to create backlog list? Each time the equipment is inspected, an opportunity is provided to gather backlog. In an underground mining environment, some of these touch points include the preventative maintenance services, planned repairs, and operator circle checks.
An additional inspection can be strategically added to generate a greater and more detailed amount of backlog. Figure 1 below depicts the impact on parts procurement time of an inspection conducted by a mechanic in a predetermined time frame before the equipment is scheduled to come into the shop for a preventative maintenance service.
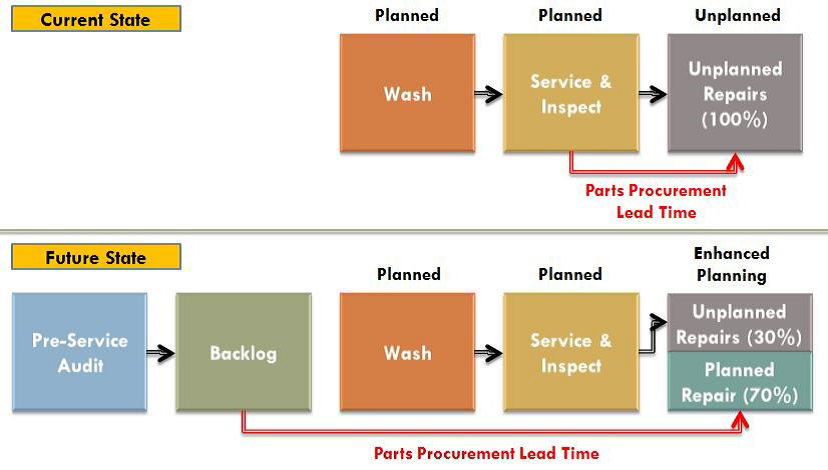
Figure 1—Current State vs. Future State with Backlog
Once the backlog list has been developed, the repairs can then be strategically scheduled alongside the preventative maintenance services while the equipment is already in the shop with shop space and labor assigned to it. Additionally, once these repairs have been scheduled, parts and materials can be ordered, packaged, and delivered to the shop where the repairs will be completed.
The supply benefits of planning repairs before failure are amplified in underground mining as the remote locations can be difficult for suppliers to deliver to. Even once on site, the materials must go through a complex supply delivery system to make their way underground. Planning these repairs ahead of time allows the equipment to run for the duration of this prolonged lead time. If the equipment is run until failure, it will remain down for the entire duration of this lead time until the needed parts can be delivered.
In generating and completing the backlog list against each piece of equipment, failures and breakdowns that would normally occur can now be discovered before failure and repaired on average much quicker than if the equipment would have broken down. The backlog system is working towards converting unplanned maintenance work into planned maintenance work, and therefore consuming one third of the resources on each repair converted as would normally be expended.
Planned maintenance leads to significant cost savings with improved productivity. For 50 plus years USC Consulting Group has helped organizations develop planned maintenance programs to increase their uptime. Contact us today to start converting your maintenance practices and keep your operations running as much as possible.
They happen every year in California and throughout much of the Pacific Northwest: wildfires. According to the Interagency Fire Center, 8.2 million acres burned in 2018 in the U.S. overall. In the Golden State so far in 2019, land scorched nears 8,000 acres.
But wildfire season is slightly different this time around, in addition to displacing thousands of residents and businesses, the effects have also led to widespread power outages. Some of these have been scheduled by the state’s largest utility provider, Pacific Gas & Electric Corp., in order to ensure the safety of firefighters and emergency personnel battling the blazes.
However, patience has ceased to become a virtue for many of the state’s residents impacted, and the length of the outages is peeling back the curtain on what many people view as one of the country’s most pressing problems as it relates to infrastructure: the aging electrical grid. Because the vast majority of small-business owners and major corporations require power to provide, manufacture, or deliver products and services, the grid’s failings are forcing companies to evaluate their current processes and develop workarounds so service interruptions are minimized.
As veteran business owners can attest, it’s not if they’ll be affected by outages, but when and for how long.
Are blackouts happening more frequently?
If it seems like outages are occurring with greater regularity, it’s not your imagination. In 2017, the most recent year in which complete data is available, outages totaled 3,526 nationally, according to estimates from Eaton. These affected close to 37 million people — many of them business owners — and lasted close to an hour and a half per outage. They also occurred in all 50 states.
“For the ninth consecutive year, California experienced the highest number of power failures.”
For the ninth consecutive year, California experienced the highest number of power failures. And between 2008 and 2017, the total was close to 4,300, more than doubling the amount in Texas, which saw the second highest number at 1,603, Eaton reported. Furthermore, how much time passed before the lights came back on in the Golden State was considerably longer than the national average at 133 minutes.
Of course, outages are hardly isolated to the nation’s most-populated state. Several other states experience a greater number of them and for lengthier time periods than in years’ gone by. These included Alaska (138 minutes), the state with the lowest population density, Arizona (138 minutes), Wyoming (153 minutes), Vermont (172 minutes), and Montana (212 minutes).
Why are they occurring on a more regular basis?
Because so many variables play into the power supply and its reliability (e.g. weather-related events, source of electricity, car accidents that damage utility poles, etc.), it’s difficult to isolate their frequency to one issue. In general, however, the uptick is largely due to a lack of investment in fixing the grid as it presently exists and the growth in the country’s population. In other words, more properties are tapping into an already tapped out energy infrastructure.
As chronicled by the American Society of Civil Engineers, the U.S. at present has approximately 640,000 miles worth of high-voltage transmission lines. Most of these distribution lines were installed in the 1950s and 1960s. At that time, they weren’t expected to last more than 50 years. With it now being 2019, do the math. What’s more, in the contiguous U.S., power grids are operating at full capacity.
In short, wear and tear, accompanied by utility lines being stretched thin, has taken a toll.
“The government lacks an adequate federal energy policy.”
Additionally, investments in shoring up the grid have been insufficient. Some lines are owned by the federal government, which the ASCE notes lacks an adequate federal energy policy, while others are managed by investor-owned utilities. Specifically, they’re responsible for only 6% of electrical providers, yet serve close to 70% of customers.
Add in the surge in wildfire activity as well as other weather-related catastrophes — 17 of the last 25 Atlantic hurricane seasons have been above average in terms of activity, according to the National Oceanic Atmospheric Administration — something’s got to give. That something is the electricity.
These are among the reasons why major utility providers such as PG&E don’t expect blackouts to diminish anytime soon. At an October meeting held by the California Public Utilities Commission, PG&E CEO Bill Johnson noted it could be 10 years or more before they’re “really ratcheted down significantly,” NPR reported.
Although many households in California are still in the dark a month removed from the shutoff events, at least 2 million Californians were without power when the outages peaked in October.
What is the solution?
While there are many potential answers to the power problem, something everyone agrees on is there’s no quick fix. Some communities and municipalities, such as those in Wyoming, have decided to bury electrical lines so they’re underground, thus avoiding impact-related events that cause outages. This may help explain why Wyoming has averaged the fewest power outages between 2008 and 2017 (only 94). However, the problem with these is cost: three times more than traditional overhead, as noted by the Casper Star Tribune.
ASCE has a few suggestions, noting that any meaningful action must start at the top:
- Federal government must comprehensively assess where grid requires reinforcements and strategically invest in alternative energy sources such as biomass, hydroelectric, geothermal, and solar.
- Utilize remote sensing and inspection technologies to improve maintenance and real-time detection.
- Rebuild distribution lines so they’re more resistant to seasonal forces (wind, heavy snow, ice, etc.).
- Make it easier for utility providers to obtain permits they need to begin construction.
- Enact a national “storm hardening” plan that is guided by the recommendations of electrical engineers.
Restoring the nation’s power grid — as well as your own — will cost money, but doing nothing about it may cost more if outages continue to proliferate as expected. From 2003 to 2012, outages resulted in losses that averaged between $18 billion and $33 billion for the U.S. economy when adjusted for inflation, according to ASCE’s calculations. Even one lengthy outage can be devastating on productivity, never mind several.
At USC Consulting Group, we can power your processes so you can keep your business up and running so the lights don’t go out. We do this by analyzing how your company functions at present, set up asset maintenance best practices, and offer step-by-step solutions for where to fill gaps. The productivity improvements and supply chain optimization we recommend can help you work proactively so you’re always expecting the unexpected. Please contact us today.
Asset-intensive industries have cautiously maintained their commitment to present and future major capital investments in the wake of the 2008 economic collapse. Total capital expenditure, which includes the purchasing of both equipment and structures, has grown without pause since 2009, according to a recent report from the U.S. Census Bureau.
But ventures today are not the same as they were before 2008. They now come with new perspectives on how best to improve reliability across the business with tightening margins, ensure throughput or productivity by reducing downtime and preserve mission-critical assets effectively, intelligently, and affordably throughout their life cycles. To some degree, all industries with large-scale assets cared about these principles in the past, but now many – energy, oil and gas, process industries, telecom – must do so in the face of trends rapidly transforming their sectors.
Considering major capital investments? Here’s how enterprise asset management and maintenance can save you from dire financial straits.
Are you caught in an asset utilization trap?
Industries with heavy assets owe it to themselves to develop innovative and more robust asset management practices, lest they fall victim to an endless cycle of profligate capital spending.
Let’s use an example industrial businesses have no doubt experienced: how to respond to low asset utilization. A mining company crunches the data on month-over-month utilization for its fleet of articulating vehicles. Asset management metrics return a utilization rate of around 45 percent, same as it’s been for more than a year. Utilization has plateaued, so company stakeholders decide that increased capital investment on newer trucks will resolve their issue with stagnant asset-related revenue generation.
Chances are good that it won’t, definitely not if low utilization stems from maintenance and scheduling. An ill-prepared asset management program in charge of a larger fleet will only exacerbate the utilization problem, not fix it.
If this mining company, or any other asset-reliant business for that matter, truly believes in the doctrine of continuous improvement, they will turn their attention to the real culprit: underdeveloped asset management operating systems and reliability-centered maintenance. Here’s how to build out these areas and create an asset support network that drives higher utilization:
Get granular with preventive or predictive maintenance
All industries that rely on heavy equipment or high-tech plants must gradually, but assuredly, move toward a proactive versus reactive stance on enterprise asset management. Repairs and calibration must either happen on a time-based cycle (preventive maintenance or PM) or through advanced sensors and preemptive failure detection (predictive maintenance or PdM).
However, these are very broad recommendations asset management teams will probably already understand the value of. What specific details should PM and PdM adopters lock onto if they want to boost utilization?
Pinpoint ideal KPI metrics: Find the measurements that align best with your mission as an organization and can report capably on issues surrounding asset utilization, then automate the acquisition and visualization of those measurements so you understand them in real time.
Investigate data hygiene: Key performance indicators must be accurate to serve operators, technicians, and supervisors. Review where your data comes from, who handles it, and what may adversely affect its veracity.
Standardize cross-functional transparency: Businesses that democratize information allow their workers to contribute to and analyze all data related to asset health. Build visibility into the entire asset management operating system – reporting, inspecting, scheduling, repairing, confirming, and documenting – and leave no area of your business in the dark.
Devote more resources to root cause failure analysis
Are mechanical failures on critical assets really the result of something mechanical? You’ll never know without comprehensive root cause failure analysis (RCFA).
Although deficiencies or outright failures may present as technical glitches, best-in-class asset management processes must dig below the surface to reveal what’s actually causing asset functionality – and ultimately utilization across the board – to drop.
Returning to the hypothetical mining company from before – perhaps utilization rates were low because heavy trucks require a lot of maintenance. What kind of maintenance? Technicians report back that the most common work order is repair or replacement of shock absorbers. To the untrained eye, this appears rational given the rough terrain and capacity requirements of the job. But practitioners of thorough root cause failure analysis don’t stop there. They ask the following:
- Are these universal issues experienced by competitors?
- Are these failures caused by the roads we drive on?
- According to the manufacturer’s specifications, are we overloading these trucks?
- Is a lack of communication between operators and maintenance professionals to blame?
Immediate remediation of one, some, or all of these concerns will improve the reliability and availability of assets, raise utilization rates, and may even deter unnecessary capex and opex spending. In order to achieve this high level of awareness over the condition of capital investments, however, asset-intensive businesses must first invest their time and effort into fleshing out RCFA.
Want to learn more about how to improve asset utilization through asset management and proactive maintenance? Contact USC Consulting Group to speak to an operations management consultant today.