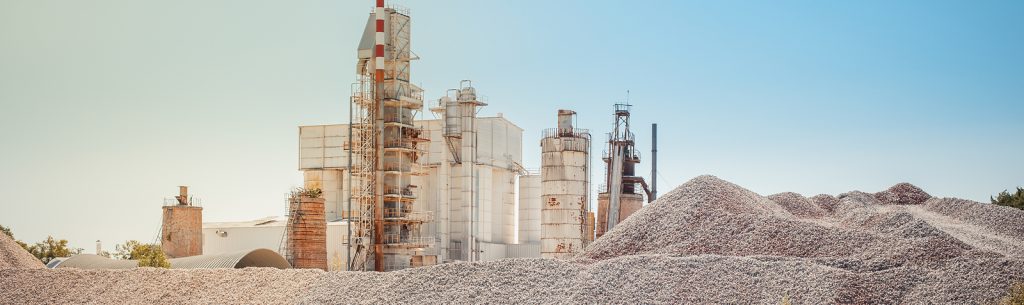
Understanding the Hard Truths of Cement Production
In 2015, the U.S. cement industry alone produced more than 80 million tons of Portland cement and nearly 2.5 million tons of masonry cement from its 101 facilities according to research from the United States Geological Survey.
Quite an amount, but not surprising given the ubiquity and versatility of the material – cement and concrete support our roads, bridges, and waterways, as well as act as the DNA to urbanization stateside and abroad. In a sense, cement is the “god particle” of progress. As the U.S. looks to repair its crumbling infrastructure and cities continue to attract large swathes of the population, cement will always have a void to fill.
Or will it? Recent challenges to the industry have made the future of even this most universal resource uncertain. What are they and what are their implications?
Environmental concerns throughout production cycle
At the root of nearly all the industry’s troubles lies ecological woes over production. The cement industry faces grave environmental issues that increase its costs and divert attention to competitors in the construction and building materials sectors like wood and steel.
“Cement production releases carbon emissions equal to 75% its weight.”
First, cement production requires incredible energy to heat its kilns. Annually, this figure works out to approximately 0.25 percent of the total energy consumed in the U.S. across all sectors, residential included, according to the U.S. Energy Information Administration. Furthermore, the EIA report on the cement industry points out its “reliance on coal and petroleum coke,” a combustive material high in carbon necessary for mass production.
Problems with greenhouse gases far surpass those of energy efficiency. Research by Maclean’s revealed cement production releases carbon emissions equal to about 75 percent its weight. For scale, the 80 million tons of Portland cement manufactured in the U.S. over 2015 effectively created 60 million tons of carbon dioxide in the process.
Ecological consciences aside, high emissions rates from production aren’t cheap in the age of the carbon tax. Inevitably, keeping the course will only jeopardize finances and taint low units costs once the expenditures trickle down to the consumer. To the U.S. cement industry’s credit, strides have been taken to mitigate emissions. According to Green Biz, cement businesses averaged an annual 0.5 percent reduction in carbon in recent years. Unfortunately, these gains aren’t commensurate with production growth as urbanization soars nationally and internationally.
Oil stagnancy could lead to production losses
Cementing is a crucial step in the oil and natural gas extraction process. Among various other uses, drillers line wellbores with cement to protect the integrity of their equipment and fill wells to stem the flow of resources. In fact, the oil and gas sector consumed roughly 4 percent of all domestic cement in 2015, according to the USGS.
Of course, oil and natural gas prices aren’t what they used to be. Economic downturn in the recent past could easily dissuade companies from investing in exploration and the production of new wells. Drilling development in upstream oil operations has traditionally been a capital-intensive endeavor. Investment spending usually follows value growth – for example, between 2003 and 2014 total oil company investments rose by more than $100 billion as per-barrel prices increased by over $50, according to the EIA.
Simply put, if the money isn’t there, businesses cannot rest on their financial laurels for very long. Something must give, and new wells at a time when production has stagnated doesn’t make fiscal sense. With some of its biggest buyers out of the picture, the cement industry may too suffer from overproduction. It will need to expand its portfolio or push to new markets to stay the course.
USC Consulting Group understands the struggles facing cement companies today and is ready to help the industry turn things around one business at a time. Learn about how one cement producer reduced maintenance costs with the help of experts from USCCG.