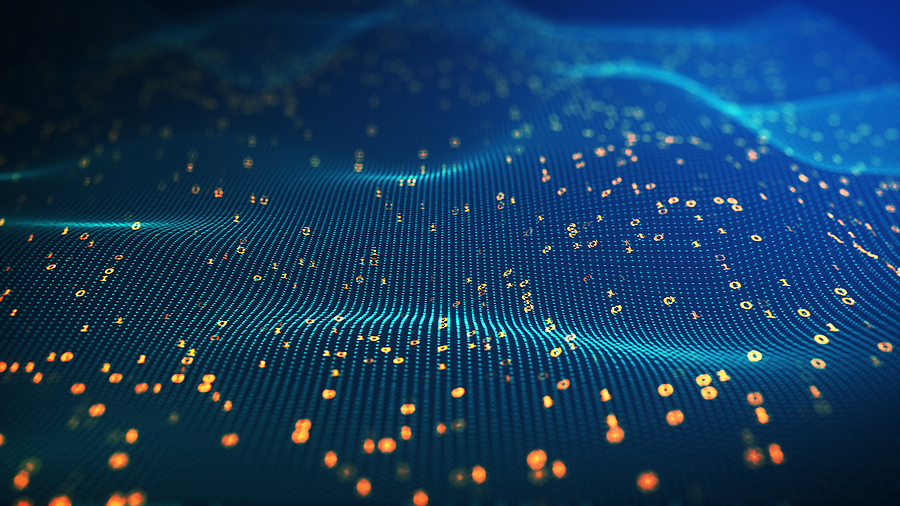
The Hidden Cost of Bad MRO Data: How Clean Data Cuts Millions in Transaction Waste
In industrial operations, Maintenance, Repair, and Operations (MRO) functions are essential but often overlooked as a source of inefficiency. While MRO spend typically accounts for less than 10% of a company’s total procurement, it can represent up to 80% of its transactional activity. The root of this imbalance?
Poor data.
Bad MRO data is more than a technical issue, it’s a strategic liability. Duplicate part numbers, inconsistent naming conventions, missing attributes, and obsolete records all combine to slow down procurement, increase errors, and inflate costs. The problem is so pervasive that some studies estimate up to 26% of all purchase orders require rework due to bad data.
How Poor Data Inflates Transaction Costs
Economists refer to the hidden friction in business processes as transaction costs-the overhead incurred not from the value of goods themselves, but from the effort required to find, negotiate, and manage those goods.
In MRO, transaction costs are driven by three main issues:
- Search & Information Costs: Technicians spend hours searching for parts due to inconsistent or missing descriptions. Inventory may be in stock but not findable due to duplicates or poor categorization.
- Bargaining & Decision Costs: Without a standardized view of item-level data, procurement can’t consolidate purchases, compare prices, or analyze spend across suppliers, weakening negotiation power.
- Policing & Enforcement Costs: Mismatches between purchase orders, invoices, and goods receipts arise from inaccurate data, creating labor-intensive reconciliation and delays in payment or fulfillment.
These costs don’t just reduce efficiency, they erode trust in systems and waste valuable labor hours across procurement, maintenance, and finance teams.
The Power of a Clean, Structured MRO Dataset
Fixing these problems starts with building a clean, enriched, and standardized MRO data foundation. That means:
- Removing duplicate entries and normalizing naming conventions
- Enriching descriptions with missing attributes like dimensions, materials, and manufacturer part numbers
- Assigning consistent classifications using global taxonomies such as UNSPSC or eCl@ss
When data is standardized and machine-readable, organizations can streamline part identification, automate procurement, and unlock powerful analytics. They can also reduce inventory costs, prevent emergency orders, and improve supplier performance tracking.
Automating the Solution with AI
The scale and complexity of MRO datasets make manual data cleansing and classification impractical. That’s where AICA’s Product Data Intelligence platform plays a pivotal role.
AICA automates the process of data classification, cleansing, and enrichment by applying domain-specific machine learning models trained on millions of MRO records. It can:
- Detect and merge duplicates
- Normalize inconsistent formats
- Assign accurate UNSPSC GPC, or eCl@ss codes
- Enrich missing product attributes
The result is a reliable, structured material master that integrates directly into ERP, EAM, and procurement systems, serving as a “single source of truth” for all MRO items.
How USC Consulting Group and AICA Work Together
We’ve partnered with AICA enabling us to deliver rapid, scalable improvements in material master quality for our clients, unlocking cost savings, productivity gains, and strategic sourcing capabilities.
Together, USC and AICA help organizations move beyond firefighting and toward a future of proactive, data-driven operations, where every transaction is faster, smarter, and more reliable.
Start your product data transformation today, get in touch with us to find out more.