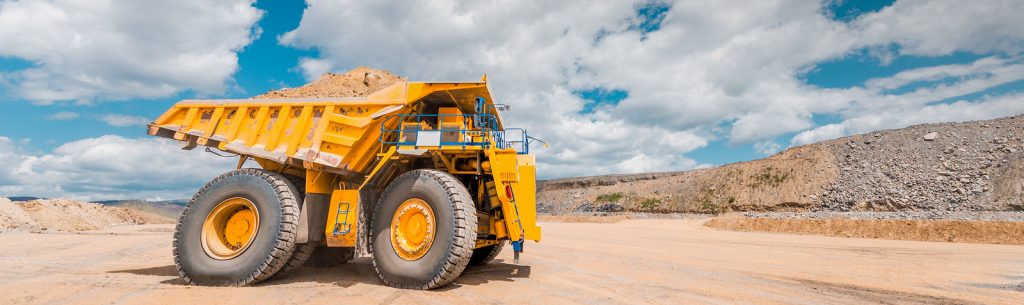
Resolving Utilization Challenges with Asset Management
Asset-intensive industries have cautiously maintained their commitment to present and future major capital investments in the wake of the 2008 economic collapse. Total capital expenditure, which includes the purchasing of both equipment and structures, has grown without pause since 2009, according to a recent report from the U.S. Census Bureau.
But ventures today are not the same as they were before 2008. They now come with new perspectives on how best to improve reliability across the business with tightening margins, ensure throughput or productivity by reducing downtime and preserve mission-critical assets effectively, intelligently, and affordably throughout their life cycles. To some degree, all industries with large-scale assets cared about these principles in the past, but now many – energy, oil and gas, process industries, telecom – must do so in the face of trends rapidly transforming their sectors.
Considering major capital investments? Here’s how enterprise asset management and maintenance can save you from dire financial straits.
Are you caught in an asset utilization trap?
Industries with heavy assets owe it to themselves to develop innovative and more robust asset management practices, lest they fall victim to an endless cycle of profligate capital spending.
Let’s use an example industrial businesses have no doubt experienced: how to respond to low asset utilization. A mining company crunches the data on month-over-month utilization for its fleet of articulating vehicles. Asset management metrics return a utilization rate of around 45 percent, same as it’s been for more than a year. Utilization has plateaued, so company stakeholders decide that increased capital investment on newer trucks will resolve their issue with stagnant asset-related revenue generation.
Chances are good that it won’t, definitely not if low utilization stems from maintenance and scheduling. An ill-prepared asset management program in charge of a larger fleet will only exacerbate the utilization problem, not fix it.
If this mining company, or any other asset-reliant business for that matter, truly believes in the doctrine of continuous improvement, they will turn their attention to the real culprit: underdeveloped asset management operating systems and reliability-centered maintenance. Here’s how to build out these areas and create an asset support network that drives higher utilization:
Get granular with preventive or predictive maintenance
All industries that rely on heavy equipment or high-tech plants must gradually, but assuredly, move toward a proactive versus reactive stance on enterprise asset management. Repairs and calibration must either happen on a time-based cycle (preventive maintenance or PM) or through advanced sensors and preemptive failure detection (predictive maintenance or PdM).
However, these are very broad recommendations asset management teams will probably already understand the value of. What specific details should PM and PdM adopters lock onto if they want to boost utilization?
Pinpoint ideal KPI metrics: Find the measurements that align best with your mission as an organization and can report capably on issues surrounding asset utilization, then automate the acquisition and visualization of those measurements so you understand them in real time.
Investigate data hygiene: Key performance indicators must be accurate to serve operators, technicians, and supervisors. Review where your data comes from, who handles it, and what may adversely affect its veracity.
Standardize cross-functional transparency: Businesses that democratize information allow their workers to contribute to and analyze all data related to asset health. Build visibility into the entire asset management operating system – reporting, inspecting, scheduling, repairing, confirming, and documenting – and leave no area of your business in the dark.
Devote more resources to root cause failure analysis
Are mechanical failures on critical assets really the result of something mechanical? You’ll never know without comprehensive root cause failure analysis (RCFA).
Although deficiencies or outright failures may present as technical glitches, best-in-class asset management processes must dig below the surface to reveal what’s actually causing asset functionality – and ultimately utilization across the board – to drop.
Returning to the hypothetical mining company from before – perhaps utilization rates were low because heavy trucks require a lot of maintenance. What kind of maintenance? Technicians report back that the most common work order is repair or replacement of shock absorbers. To the untrained eye, this appears rational given the rough terrain and capacity requirements of the job. But practitioners of thorough root cause failure analysis don’t stop there. They ask the following:
- Are these universal issues experienced by competitors?
- Are these failures caused by the roads we drive on?
- According to the manufacturer’s specifications, are we overloading these trucks?
- Is a lack of communication between operators and maintenance professionals to blame?
Immediate remediation of one, some, or all of these concerns will improve the reliability and availability of assets, raise utilization rates, and may even deter unnecessary capex and opex spending. In order to achieve this high level of awareness over the condition of capital investments, however, asset-intensive businesses must first invest their time and effort into fleshing out RCFA.
Want to learn more about how to improve asset utilization through asset management and proactive maintenance? Contact USC Consulting Group to speak to an operations management consultant today.