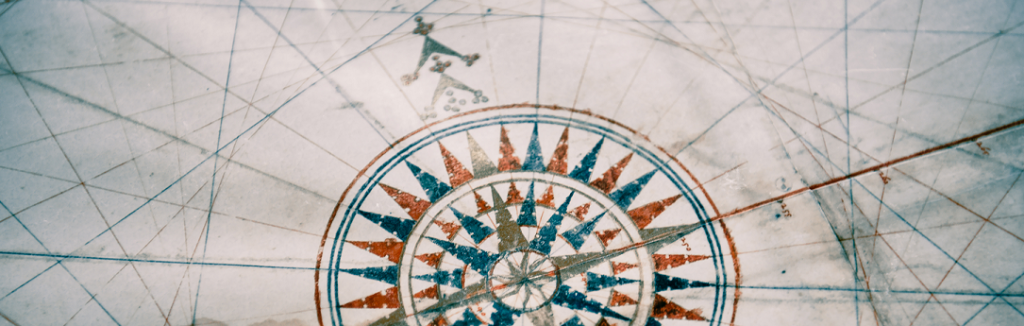
Use Process Maps to Raise Efficiency
Process maps can help you improve operations and add value to your organization.
In lean manufacturing, process maps are powerful tools that can help you understand what your current processes look like now, and what they should be. On continuous improvement projects they are essential. If you have embarked on the journey of making your facility more efficient, but are facing difficulty figuring out exactly where you need to make changes, you should consult with proven operations consultants who can use process maps to help identify your problem areas and eliminate them.
Process maps provide a realistic view of a production process
According to Six Sigma Material, that process maps involve the creation of detailed flow diagrams of processes, using color coded symbols. These maps provide a high-level view of what operations look like and how processes work with one another. The intention behind using process maps is to help you see your processes as they really are. This can be a very valuable learning experience for you, especially if you are ready to start making improvements.
“Consultants can help you identify automation opportunities, duplication, redundancy, delays, and idle time.”
Using process maps, operations consultants can help you identify automation opportunities, duplication, redundancy, poor decision-making, delays, and idle time. Addressing any one of these areas can raise efficiency at your plant, but addressing them all is a game changer. In lean manufacturing, this is known as waste elimination. Process maps are documents that should be updated and analyzed on a regular basis. The more detail they have, the easier it will be for you to have the best process and capture opportunities.
Enhance your value stream with process maps
According to Lean Manufacturing Tools, process maps can add value and reduce costs in an organization. They are one of the most important tools in a consultant’s kit. It is important to point out, however, that process maps are only helpful if you take action. It is essential to have a clearly defined goal to work toward. In this way, the analysis of your process map will be based on amending existing processes to get you to where you need to be.
A comprehensive process map captures your value stream – the processes that your product goes through, from raw material to customer delivery. In your value stream, a product goes through a series of steps that either add value or waste time. Done right, a process map will find those weak areas and allow you to improve them. All non-value adding steps and delays should be fixed and reflected in the next iteration of the process map. As previously mentioned, this involves taking action, which will necessitate educating and training plant staff – another area where manufacturing consultants shine.
Lean Manufacturing Tools also pointed out that depending on the purpose of the mapping, there are various tools that can be employed. Before mapping, you should know exactly what it is you are trying to achieve. Are you trying to fix an individual work cell or the whole supply chain. Value stream mapping, for example, will help you see your whole process, but it won’t provide enough detail to analyze a specific process.
Use process maps to improve your operations and add value to your organization.
A comprehensive view of a facility’s processes
Six Sigma Material explained that a successful process mapping exercise combines all types of diagrams and should show you your processes from a macro bird’s-eye view as well as on a granular level, but accomplishing this will require effort from your whole team. Additionally, improving your operations will involve educating everyone on what the processes are like and how they should be improved. Some improvements are self-evident, others need a little bit of extrapolation.
If you attempt to create process maps on your own and they don’t end up perfect, don’t worry. There are many software programs that can help you handle the complexity involved. These solutions can help you identify rework loops, communication issues, delays, and other issues. Additionally, you can create a brown paper process map, which combines many different mapping tools on a roll of paper that is often hung on a wall. You may be shocked to discover the number of steps involved in creating one of these, as well as the people and forms involved in a basic process. You may also find yourself wanting to dig deeper. However, if this seems difficult, you should probably consult with a manufacturing consulting firm with a proven track record in lean manufacturing techniques. Lean principles are all about improving your value stream by removing obstacles, delays, and other inefficiencies. In this area, getting outside help is a good idea so that you can successfully achieve your desired results.