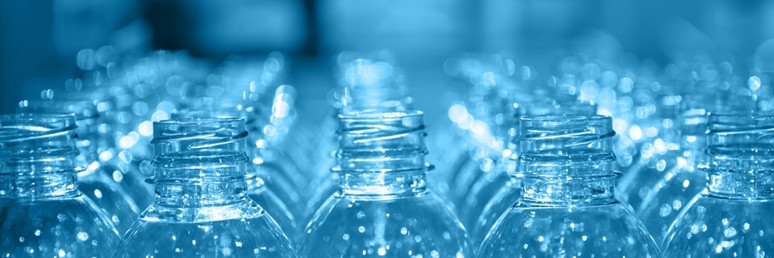
Upgrade Operations to Reduce Plastic Manufacturing Costs
Plastic has left an indelible mark on the manufacturing industry. This ubiquitous material helps companies produce high-quality products at an inexpensive cost for both the consumers and themselves. Moreover, the chemical makeup of plastics and other polymers opens up new frontiers in manufacturing as the industry finds new and exciting ways to deploy these materials to suit its needs and those of future generations. Reducing plastic manufacturing costs can have a huge impact on society and the industry.
The Plastics Industry Trade Association places plastics manufacture as the third largest sector in the field, one capable of generating more than $380 billion in annual shipments and employing more than 885,000 employees spread across every single U.S. state. However, even titans of industry can find methods of improving operational efficiency to simplify their supply chain relationships, streamline internal processes, and manage their resources more intelligently to secure the bottom line. As big as plastics is, it fits the mold for such improvement opportunities. Where can manufacturers focus their attention if they want to see their performance prosper and plastic manufacturing costs reduced?
Energy efficiency through reverse logistics
Like many process industries relying predominantly on raw materials, plastics manufacturing expends a great deal of energy in production. Most plastics are derived from either hydrocarbon gas liquids or natural gas. According to the U.S. Energy Information Administration, electricity makes up a significant portion of this industry’s energy consumption, used primarily in heating, cooling, and processes like compression and injection molding, as well as thermoforming. That said, ancillary processes also take their fair share – a study published in Manufacturing Engineering found the energy costs related to additive manufacturing techniques can be anywhere between 53 to 104 times more expensive than traditional injection molding.
However, energy conservation may not necessarily be in the cards for plastics manufacturers, as usage directly correlates to the desired chemical reaction necessary for production. Instead of devoting company resources toward finding solutions for reducing energy costs on-site, plastics manufacturers should give reverse logistics prospects equal consideration. While establishing or enhancing such a program may add a level of complexity to business functionality, the rewards outweigh those concerns by a wide margin. A recent study by the U.S. Department of Energy uncovered that the industry has the potential to dramatically decrease its energy and plastic manufacturing costs by instituting robust recycling measures, especially for companies working with polyethylene. A “modest” campaign could yield as much a 17 percent energy cost reduction, but an “aggressive” one could cut energy spend by nearly a third.
Implementing dynamic reverse logistics recycling programs for reclaimed or returned goods isn’t merely a fly-by-night trend for trimming costs, but a whole new way of envisioning manufacturing. Plastics manufacturers should consider instituting or expanding these areas to push their enterprises toward peak operational efficiency, powered by an innovative approach to waste management.
Where can plastics manufacturers focus their attention if they want to see their performance prosper and operational costs reduced?
Automated, end-to-end enterprise resource planning to cover administrative duties
Apart from optimizing on the manufacturing floor, plastics also requires well-oiled administrative processes behind the scenes to ensure plant operations run smoothly and cost-effectively. Automating a number of services on the back end can eliminate deficiencies caused by clerical errors related to data entry, as well as other pertinent processes specific to plastics like tracking fluctuating resource markets to scaling and managing plastics recipes. Moreover, programming these machinations to run automatically organizes low-level tasks in a way that complements the business intelligence gleaned from them by employees, managers, and supervisors.
“Comprehensive enterprise resource planning can provide the answers plastics manufacturers are looking for.”
Comprehensive enterprise resource planning can provide the answers plastics manufacturers are looking for. For instance, a 2015 DuPont survey regarding the top concerns facing the plastics industry placed “unstable oil prices” in the third seat, a single percentage point behind “environment and sustainability” and “competitive global environment.” By adequately forecasting demand and operational costs with real-time data tracking from volatile oil markets and others, plastics manufacturers can apportion resource spend intelligently, reducing waste by way of over- and underproduction, over- and understocking inventories, meeting budgetary requirements on daily resource investments, and more.
Plastics manufacturers without ERP or with only single-tier systems should seriously consider upgrading to a two-tier deployment as they scale. As a Constellation Research survey found, nearly half of all businesses with Tier-1 ERP already in place were considering making the switch to two-tier. Respondents thinking about onboarding two-tier ERP were motivated predominantly by its low cost in comparison to their overburdened, single-tier operations and as insurance securing their competitiveness in an ever-changing global market.
Well-executed ERP management doesn’t handle small, meaningless tasks, but decidedly important ones that plastics manufacturers might not have the human capital to oversee with the intensity the 21st-century business mandates. This resource puts automation to work for the plant, providing everyone from plant managers to executives with the information necessary to consolidate operations into a simplified, data-driven workflow and make industry-leading decisions about the direction of their organization.