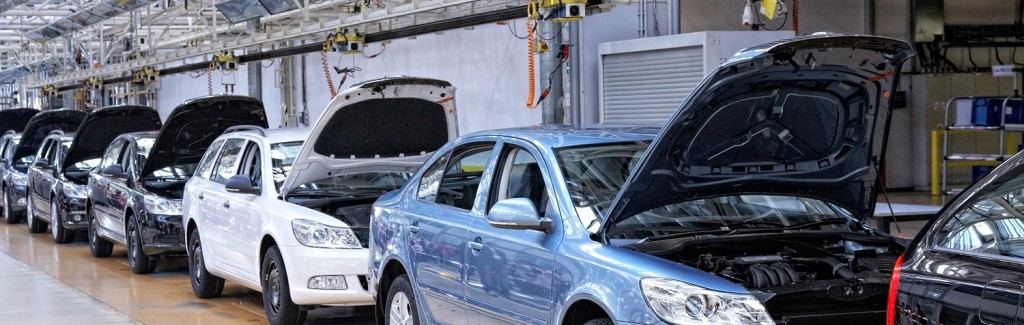
4 Ways to Reduce Plant Changeover Time
All manufacturers invariably understand the importance of keeping changeover time to a minimum, as increased downtime means a drop in productivity, and ultimately, revenue. To effectively lower changeover time, they must first be measured accurately. According to Lean Production, one standard calculation that manufacturers can apply across multiple assets is to measure changeover time from the creation of the last good product in the current run to the first good product in the next production run. This article explains one popular methodology for promoting faster changeovers – SMED – and provides 4 suggestions manufacturers should consider when aiming to limit downtime.
The basics of improving changeover times
Lean Production noted that improving changeover times is typically done through standardizing processes, maintaining up-to-date information on equipment settings, and keeping track of real-time metrics. Successful manufacturers will facilitate work in these areas through automation, but will not attempt to use automation alone to reduce times. Plant managers must update processes, establish plans, and adhere to efficient schedules before they can expect an investment in new technology to yield the desired results.
When standardizing processes, plant managers should focus on human improvements. This involves defining roles and establishing accountability. If necessary, manufacturers should coach their teams on the best ways to do their jobs. Regardless of position, operators and technicians must follow processes as they are laid out. Doing so will mean retrieving parts before the changeover time begins, regularly marking down equipment settings, and eliminating idle time. On the technical side, installing quick release mechanisms and modularizing equipment can also prove beneficial.
“Plant managers should focus on human improvements.”
Single Minute Exchange of Dies
It is important to point out that changeover time can vary drastically from one industry to another. Packagers may only spend a few minutes doing a changeover, whereas automobile manufacturers could spend days or weeks adjusting equipment for new models. However, regardless of industry, keeping downtime to a minimum is essential. A LEAN Journey mentioned that one technique for reducing changeover time is Single Minute Exchange of Dies, or SMED, which enables manufacturers to perform more frequent changeovers. This approach is based on managing production in a more flexible manner, allowing for smaller batch sizes, while still maintaining high output.
Lean Production explained how SMED can help manufacturers achieve a significant reduction in changeover time. The methodology is based on separating the changeover process into a series of sequenced events called ‘elements.’ The main goal is to manage as many elements as possible while the equipment is still running, thereby lessening downtime indirectly. SMED takes elements that are not involved in the current production run, moves them externally to the process, and streamlines their use by completing them faster. For example, if a smaller piece of equipment must be calibrated before it fits into a larger framework as part of changeover, the smaller piece ought to be managed independently of the process. SMED is particularly helpful in an iterative process.
Smart manufacturers understand that automation alone does not raise efficiency
Actionable items for faster changeovers
Whether using SMED or focusing on faster changeovers, the approach is the same. As previously mentioned, successfully reducing changeover time comes down to thinking, not tinkering. Accordingly, here are four suggestions to help you reduce your changeover times:
- Separate internal and external setup activities
If you have certain processes that can be performed without having to shut down equipment, do them while production is still active. This will limit the amount of downtime you accrue. - Laterally remove idle time from equipment and workers’ schedules
Some manufacturers believe that machines can be idle as long as workers are still doing their job, but the best way to raise efficiency is to maximize productivity across the board. Equipment does not need to be offline as long as you may think. - Maintain fully stocked staging areas with all necessary parts and tools
You can rely on a Kanban system of inventory management, or keep track of parts using other methods, but make sure workers have the necessary tools at the right times. Not doing so results in more time spent wandering around, and less time on value-added activities. - Maintain a schedule of changeover times and continue to beat your record
You can display changeover times near plant equipment so that staff is always kept aware of operational goals. The only way to know if changeover times are reduced is to continually measure them over time.
Reliable Plant mentioned that improving changeover times will likely lead to the establishment and documentation of new work processes. As such, operators will have to be trained in best practices on an ongoing basis. However, as an organization becomes more efficient after each improvement, eventually it will achieve a lean manufacturing environment. The road toward efficiency and reduced changeover time can be painful at times, but it will most certainly pay off in the long run.