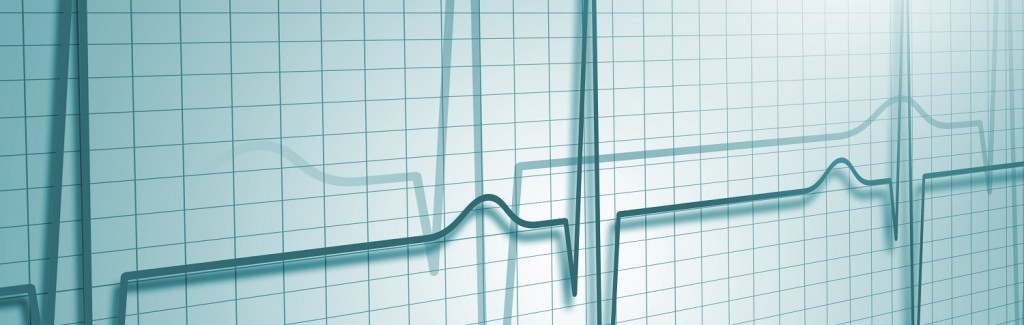
Improving Efficiency in Medical Device Manufacturing
In the coming decades, the field of medical device manufacturing will be put to the test. According to new U.S. Census Bureau estimates, more than 75 million baby boomers are reaching retirement age in the near future. Now more than ever, healthcare in general will need to find a functional way to accommodate so many late-in-life patients. And seeing as the number of millennials exceeds 83 million, a long-term solution is vital to the industry’s success. A system must be put in place that both adequately provides services to baby boomers today and is sustainable enough to at least lay the foundation for healthcare’s future. After all, the U.S. population is only getting bigger.
Medical device manufacturing will play a large, active role in how U.S. healthcare reinvents itself in the modern age, especially with the rise of the Internet of Things, a growing inter-operable network of wirelessly connected devices. A Goldman Sachs report on medical technology found devices like implantables and other forms of monitoring equipment have the power to lower healthcare costs for both providers and patients. Since cost stands among the single greatest concern for both parties, innovations in medical device manufacturing can be considered one of the most crucial drivers piloting this healthcare revolution.
That said, if medical device manufacturers cannot develop new equipment with quickness and efficiency, the medical industry as a whole loses a level of responsiveness it will desperately require during this transitory period. This industry can increase its efficiency by optimizing its research and development stages to help build an advanced infrastructure of digital awareness that will make low-cost, high-tech healthcare a reality?
“Manufacturers allocate more money to R&D, but generate fewer products
Never compromise on quality – reinforce it with process mapping
A study published in Nature Reviews Drug Discovery stated during the last six decades, the number of new treatments created for every $1 billion spent on research and development has declined by around 50 percent every nine years. In short, drug and medical device manufacturers allocate more money to R&D, but generate fewer products. Though this factor may indicate a need for efficiency improvements during a given product’s clinical trial stages, for the time being, manufacturers have no other choice but to find areas in R&D to cut for the sake of cost efficiency.
However, regulation from the Food and Drug Administration has only become more stringent in the last few decades with little sign of loosening. Reducing costs, therefore, should not jeopardize quality of the products under review.
Unconnected though it may seem, envisioning better layouts of a medical device manufacturer’s work cells on the production floor can increase efficiency by improving throughput and reducing resource costs, but potentially also improving a device’s quality. According to CIRTEC Medical Systems, O- and U-shaped production lines as well as intelligently placed tools and materials at every workstation increase efficiency by both reducing wasteful movement and action. Instead of hiring more employees or scaling up costly assets, manufacturers could instead strengthen R&D and standard operations through process mapping to gain a substantial efficiency margin.
Efficiency gains in one area often bolsters success in another. Streamlining R&D means manufacturers are able to move into the production stages faster. Reducing waste in manufacturing creates a greater pool of resources to encourage innovation in R&D
Medical device manufacturers can integrate new technology into their operations
In-house tech takes center stage in R&D, innovation timeline
As we just touched on, rudimentary organizational upgrades can impact operational efficiency in extraordinary ways. Outside of the production floor, however, there are plenty of other opportunities to incorporate more consolidated, actionable lines of inter-departmental communication to that very end. But before the medical device manufacturing industry can accomplish those goals, companies within may need to overcome certain stigmas regarding the on-boarding of new internally facing technology.
A poll conducted by PricewaterhouseCoopers found executives in medical device manufacturing expect increases in innovation, but around 86% have yet to focus their directives on enhancing the processes directly related to fast-tracking new products from R&D through their releases to market. Moreover, of the executives surveyed, only 12% use advancements like mobile technology, data analytics, and cloud technology to “create new business models that center on clinical and consumer dynamics.”
While these technological additions to the world of medical device manufacturing cannot purport any innate efficiency improvements, their absence in an industry dedicated to the advancement of healthcare through state-of-the-art computerized machinery doesn’t make much sense. As the nature of patient care turns a corner, so too should the organizations leading the charge, which means laying the groundwork for more intelligent, responsive health services through the integration and development of dynamic digital assets that allow employees to communicate data comprehensively.
To learn more about the importance of medical device design, check out Toptal’s article Prioritizing Health Pros’ Pain Points in Connected Medical Device Design