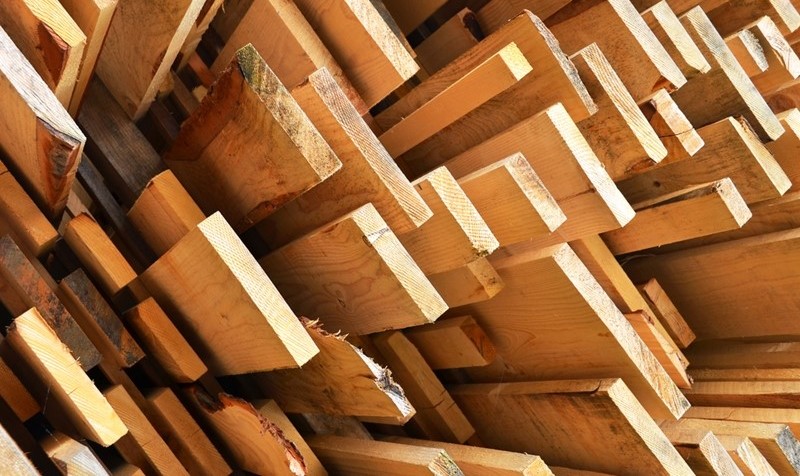
Optimizing Asset Utilization in Lumber Mills
Forestry has been one of the most profitable industries in recent years, even with modifications made to integrate environmentally sustainable practices into the mix. The Southeastern Lumber Manufacturers Association stated U.S. forestry products, from wood to paper, generate as much as $200 billion every year. Moreover, replanting strategies have made U.S. forests today 25 percent denser than in the 20th century.
As lucrative as some business opportunities within this industry can be, the potential for inefficiency detracting from any potential prosperity is also quite high. Work in the U.S. lumber manufacturing in particular is extremely competitive. According to an estimate by the U.S. Lumber Coalition, $0.60 to $0.70 out of every dollar spent on timber remunerate manufacturers for the cost of production, not toward profit. As such, competition in lumber manufacturing can sometime work against all parties involved. However, finding ways to reduce materials costs or inefficiencies in internal processes may provide lumber companies a cushion with which to benefit from marginal decreases in final product pricing.
One such area ripe for optimization is asset utilization. How manufacturers use their tools and equipment ultimately decides the outcome of their enterprise. By scrutinizing the ways operators complete a given task and whether their actions align with the industry’s best practices, lumber yard managers can potentially eliminate waste, save resources, cut lead times, and increase the quality of the lumber they produce.
Optimizing asset utilization in mill machinery means cutting lumber smarter, to retain more of it.
Comprehensive automation throughout the entire lumber mill
From a general standpoint, automating as much of millwork as possible feasibly increases the likelihood of greater asset utilization. Research from North Carolina State University found that while reducing manual processes at the onset – like gang rip – could boost yield and curtail operational errors resulting in wasted wood, many procedures on-site still rely too heavily on employees who could be better utilized elsewhere.
For instance, if rough mills could integrate technology capable of assessing least-cost grade-mix – which directly correlates to the accuracy of a yield prediction – then communicate that data effectively to industrial sawing equipment without operator intervention, lumber manufacturers could erase a time- and labor-intensive step from the milling process. When lumber yard employees are expected to eyeball raw materials to determine their grade, this affords too much room for mistakes to occur. Faulty judgments produce waste and increase labor costs to make up for lost time. Automating as many aspects of lumber mill operations as possible increases asset utilization, and leaves nothing to chance.
Rethinking how debarking assets affect resources
It stands to reason that the more fiber retained after raw material has been debarked, the greater the possibility of creating ideal lumber products. Manufacturers of forestry goods that own conventional drum or closed cylinder debarking equipment, however, might find a number of efficiency upgrades by switching to cradle debarkers, according to the U.S. Department of Energy.
To start, open-top debarking systems provide operators with the freedom to debark different types and grades of wood to account for bark thickness. Closed systems shear back bark without taking these variations into consideration. In the end, this cuts back on how much tree fiber is lost during the debarking process, retaining more resources for the mill to turn into lumber.
“Cradle debarkers use 33% less energy than closed models.”
Additionally, as the DOE states, cradle debarkers use 33 percent less energy than closed models. They are also compact enough to integrate into lumber mill operations instead of setting up a separate debark facility elsewhere, effectively phasing out costly transportation costs between the two sites. In making one simple equipment change, saw mills could permanently optimize the milling process without reshaping much else.
Limiting lumber variation through modern data-driven initiatives
Determining the dimensions by which fiber is cut into lumber ultimately impacts both yield and how manufacturers operate saws and other equipment. That said, companies in the industry must remember to account for differential shrinkage during lumber drying, which could lead to resource hemorrhaging and could cost anywhere between $50,00 to as much as $250,000 annually depending on the mill in question, according to a study conducted by members of the Forest Products Society.
By abandoning traditional formulas for ascertaining optimal board thickness in favor of real-time statistical process control. Up-to-the-second data increases a lumber mill’s recovery rate for the fiber they cut into lumber, as it limits the time between resource assessment and the sawing process. In doing so, mills can increase asset utilization by paring down waste created when inaccurate drying predictions result in defective lumber products.
As the saying goes, “It is a poor craftsman who blames his tools.” The weight of this argument still rings true, but intelligently optimizing asset utilization supports mill equipment operators so they get the most out of the tools they use daily and, in turn, process lumber efficiently without generating unnecessary waste.