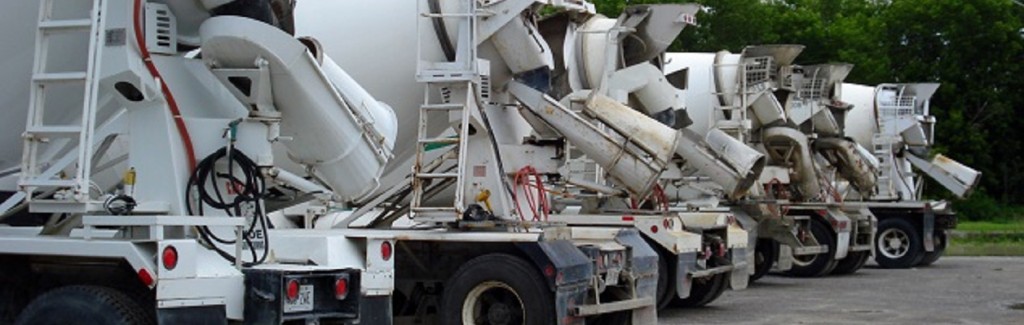
Tighten the Bolts on Your Asset Maintenance Program
Regularly scheduled repairs on capital-intensive assets are the cornerstone of any preventive, predictive, or proactive maintenance strategy in the industrial sector. By preempting outright equipment failures and counteracting small, nearly unnoticeable deficiencies in performance, businesses save cycle time, maintain product/service quality, optimize labor costs, prevent waste, keep operators safe, and preserve the lifespan of their most valuable machinery.
All these benefits aside, planned asset maintenance programs require plant managers and decision-makers to coordinate with technicians as to customizing a maintenance agenda that comports with the business at hand, whose operations may differ vastly from others. However, a few considerations are universal and enhance maintenance scheduling no matter where or how one works.
Consider capacity always
In the industrial sector, nothing should be more valuable to a business than production or service. To that end, companies dependent on advanced machinery rely on scheduled asset maintenance programs, first and foremost, to sustain uptime. Planned maintenance or tune-ups minimize the impact offline equipment has on the business’s bottom line.
Depending on the number of assets under a given planned maintenance program, it is possible to lose this edge because of –believe it or not – poor planning in regard to capacity. Let’s say you own a fleet of 100 delivery trucks and, on an average day, you need 90 up and running to accommodate your customers. Any maintenance schedule, therefore, could only address one-tenth of the fleet on any given day, otherwise, the work would compromise availability.
Capacity, unfortunately, is never that cut and dry. Maintenance management teams should always consider backlog, upcoming product/service changes, or seasonal demand metrics which may affect operations and respond intelligently.
Planned maintenance can deliver incredible value, so long as you’re doing it the right way.
Factor in labor costs
Reactive maintenance, or responding to failures after they occur, can cost a business significantly through emergency labor. A study by Maintenance Phoenix found businesses can spend nearly 20% of the total replacement cost for a given machine to remedy a single reactive maintenance event. Comparatively, proactive maintenance events generally cost just 1.4% of the same variable.
Expenses that low don’t happen automatically, so maintenance management teams should keep a few things in mind. First, it is almost always better to spread larger maintenance orders over a few shifts rather than tackling everything all at once. This leaves room in technicians schedule for other things that may crop up.
“Don’t let overtime negate the margin of savings reclaimed by switching to a planned program.”
Second, overtime expenses should be a major factor in planning, regardless of whether businesses employ in-house repair professionals or outsource. Typically, initiating a preventive, predictive, and proactive asset maintenance program involves hiring a few additional technicians. Scheduled maintenance during overtime hours may, therefore, negate the margin of savings reclaimed by switching to a planned program in the first place.
Prioritize work orders
Another benefit to scheduled maintenance is the ability to rank work orders in a low-risk environment. Reactive maintenance forces organizations to respond to situations as they arise, leaving little to no time to respond to anything else. Since planned maintenance catches failures before they happen – usually through embedded sensors and telemetry monitoring internal changes in temperature or vibration – the organizations that adopt such programs may be allowed windows of opportunity to handle repairs before experiencing the repercussions of leaving them unattended.
With that in mind, an asset-heavy company should not only create an actionable list of all their equipment and components, but rank those assets according to importance based on their respective business objectives. These lists should update after every major tech investment to ensure prioritization accurately reflects current operations. Advanced computerized maintenance management software (CMMS) could be a welcome addition to maintenance management system and help businesses develop both a master asset list and real-time asset hierarchies.
Making the change to scheduled asset maintenance delivers many competitive advantages, so use these tips to develop a more robust and effective program.