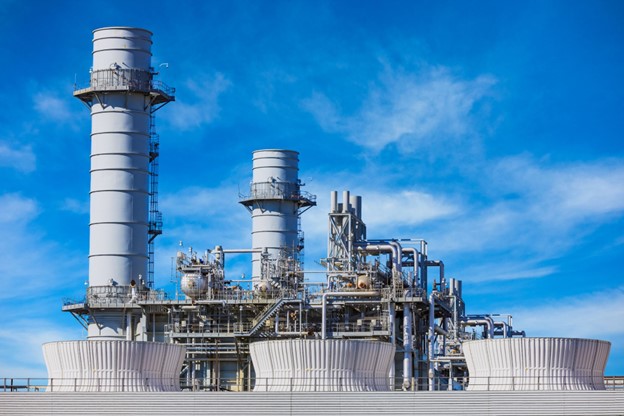
Why Equipment Reliability Matters in Oil and Gas Operations
Equipment reliability is a fundamental pillar in oil and gas production. From upstream drilling to downstream refining, operations depend on machinery that works consistently under high pressure, fluctuating temperatures, and corrosive environments. When a critical component fails, the disruption ripples far beyond the immediate site. It impacts production schedules, safety protocols, and profit margins. Maintaining uptime is not just a matter of convenience but a key driver of operational success.
Unplanned Downtime Carries Real Costs
A single mechanical failure can bring operations to a halt, costing thousands or even millions of dollars in lost production and emergency repairs. In highly integrated supply chains, even a brief pause can delay multiple projects down the line. Beyond direct financial losses, there is reputational damage and the risk of regulatory scrutiny. In an industry where timelines are tight and contracts are performance-based, reliability directly influences competitiveness.
Safety and Environmental Impact
Oil and gas sites often operate in remote or high-risk environments. When equipment breaks down unexpectedly, workers may be exposed to hazardous conditions during emergency maintenance. Malfunctioning valves, corroded pipelines, or faulty sensors can lead to environmental spills or gas leaks. Reliable systems reduce the likelihood of these dangerous incidents. Implementing proactive maintenance programs improves safety outcomes and aligns operations with stricter environmental standards.
Corrosion Control and Long-Term Performance
One of the silent threats to equipment reliability is corrosion, particularly in offshore and coastal operations. Metals degrade faster in harsh environments unless protected. That is where systems such as a cathodic protection system play a key role. By preventing corrosion from compromising vital infrastructure, these technologies extend equipment lifespan and help companies avoid costly replacements. Investing in preventative measures keeps long-term performance stable and predictable.
Strategic Maintenance as a Competitive Tool
Modern oil and gas companies are turning to data-driven maintenance strategies to extend asset life and minimize surprises. Predictive analytics and condition monitoring help teams detect wear and tear before failure occurs. Equipment logs, pressure readings, and temperature data create a clearer picture of what is performing well and what is at risk. Fewer unexpected failures mean fewer shutdowns and a steadier flow of product from well to refinery.
Reliable equipment forms the backbone of high-performing oil and gas operations. From cost control to worker safety to environmental responsibility, reliability is not an afterthought. It is a business necessity. Maintaining a strong maintenance culture and investing in technologies that protect critical assets can yield long-term advantages across the entire supply chain.
The below infographic provides more information on the challenges, the importance, and the methods and tools to improve O&G equipment reliability:
If you need help enhancing your maintenance reliability, contact USC Consulting Group today.