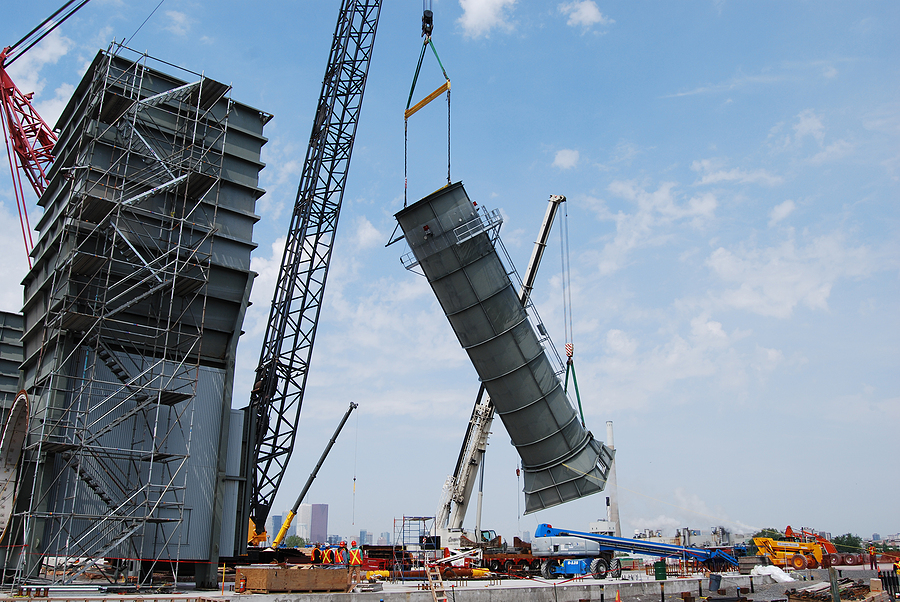
Understanding Working Load Limits: The Key to Preventing Rigging Accidents
In industries that rely on lifting and hoisting heavy loads, understanding load limits is crucial to preventing rigging accidents. Proper knowledge of working load limits (WLL), safety factors, and best practices can safeguard workers, equipment, and overall operations. By ensuring compliance with industry regulations and providing thorough training, businesses can minimize risks and maintain productivity.
The Importance of Working Load Limits
A WLL is the maximum weight a piece of rigging equipment can safely handle under normal operating conditions. This value is calculated by dividing the equipment’s minimum breaking strength by a designated safety factor. Exceeding the WLL can severely compromise the equipment’s structural integrity, increasing the risk of failure.
Ignoring WLL guidelines can result in dropped loads, damaged property, and serious injuries. Industrial rigging companies must prioritize understanding and adhering to these limits to maintain workplace safety.
Understanding Safety Factors
A safety factor is a margin of added strength built into rigging equipment to account for unexpected forces or conditions. For example, if a chain sling has a minimum breaking strength of 10,000 pounds and a safety factor of 5, its WLL would be 2,000 pounds. This additional margin helps ensure the equipment performs reliably, even if minor defects or dynamic forces occur during lifting.
Using rigging equipment without considering safety factors significantly increases the likelihood of failure. Companies must select gear with appropriate safety margins based on their operational environment and load requirements.
Consequences of Exceeding Load Limits
When rigging equipment is overloaded, catastrophic consequences can follow. Overloading leads to accelerated wear, metal fatigue, and component deformation. These conditions weaken the equipment, making it more susceptible to sudden breaks or malfunctions. Such incidents can cause severe injuries, fatalities, and extensive damage to valuable materials or machinery.
Beyond immediate safety concerns, exceeding load limits can also result in regulatory fines, equipment downtime, and increased liability. Maintaining strict adherence to load limits is essential for mitigating these risks.
Best Practices for Rigging Safety
To enhance rigging safety, businesses should adopt the following best practices:
- Proper Equipment Selection: Choose rigging equipment rated for the expected load size and environmental conditions. Ensure all gear meets industry standards and regulations.
- Routine Inspection: Regularly inspect all rigging equipment for signs of wear, damage, or fatigue. Pay close attention to hooks, chains, wire ropes, and attachment points. Damaged gear should be removed from service immediately.
- Load Calculations: Always calculate the weight of the load and ensure it falls within the WLL of the rigging equipment in use. Factor in additional forces such as wind, shock loads, and angles that can affect stability.
- Proper Training: Provide comprehensive training to employees involved in lifting operations. Workers should understand WLLs, safety factors, and equipment inspection procedures.
- Compliance with Regulations: Follow industry standards set by organizations such as OSHA (Occupational Safety and Health Administration) and ASME (American Society of Mechanical Engineers). Compliance ensures safer practices and reduces the risk of accidents.
Maintaining Safety and Efficiency
Understanding load limits is fundamental to preventing rigging accidents and ensuring workplace safety. By investing in quality equipment, conducting regular inspections, and providing proper training, businesses can reduce risks and improve operational efficiency. Companies that prioritize safety not only protect their employees but also minimize costly downtime and equipment damage.
For industries relying on industrial rigging, a commitment to load limit awareness and safe practices is essential. By following these guidelines, businesses can create safer environments, maintain compliance, and ensure successful lifting operations every time.
*This article is written by Kelly Zurawski. Kelly is a Part Owner of Equip Trucking & Warehousing, LLC, which transports heavy equipment, industrial machinery, metalworking machinery, and much more. Kelly’s brother and husband are also Part Owners. The family’s passion for heavy equipment moving began with Zurawski’s grandfather and father, who also worked in the industry.