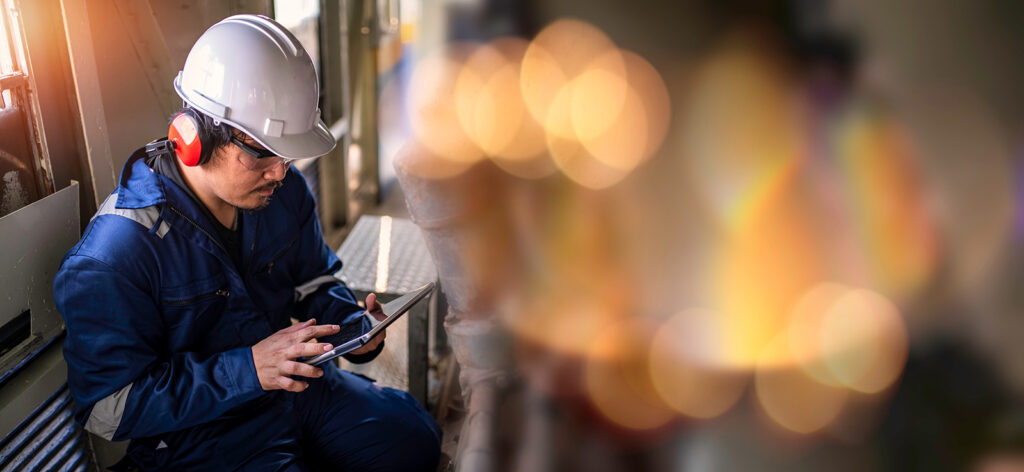
Asset Management in 2025: The Crystal Ball into Increased Reliability
Over the next five years, mining and metals companies are expected to spend between $25 billion to $30 billion annually to maintain their assets.
Largely driven by efforts to improve operational efficiency, reduce downtime, immediately reduce costs, meet sustainability goals, and manage operational risks in an increasingly volatile market, mining and metals executives are motivated to start their asset management transformation now. Delaying this transformation could result in lost competitive advantages, higher operational costs, and increased regulatory or market pressures.
Over the next five years, the mining and metals industry is projected to invest heavily in the maintenance of fixed and mobile assets. Various reports indicate that the industry is expected to allocate a significant portion of its CAPEX to maintaining and upgrading its assets. A substantial part of this investment will be directed toward maintaining critical assets required to meet global demand for minerals essential for the energy transition. In a recent survey conducted by Global Data, 48% of the companies surveyed indicated they plan to increase investments in technologies like AI and IoT sensors for equipment upkeep over the next two years.
Investment in predictive maintenance is becoming a top priority for many mining operations. Companies are leveraging their EAM’s with advancing technologies like Digital Twins, AI and IoT, along with other reliability and planning applications, and significantly transforming asset management and the asset lifecycle. These advancements in technology are expected to reduce maintenance costs by 20-30%.
Mining and metals companies integrating Enterprise Asset Management (EAM), Computerized Maintenance Management Systems (CMMS), AI, and IoT are experiencing several quantifiable benefits, including:
- Improved Asset Reliability and Uptime: Utilizing a combination of AI, IoT sensors and Digital Twins provides continuous real-time monitoring of equipment health allowing companies to predict potential failures before they occur while reducing the reliance on reactive and scheduled maintenance – reducing unplanned downtime and fewer equipment breakdowns, increasing equipment availability and extending asset lifecycles.
- Cost Reduction: A predictive maintenance capability helps avoid costly emergency repairs and reduces unnecessary scheduled maintenance, saving on labor and spare parts. It also ensures that the right parts are available when needed, minimizing overstock and understock issues, which helps reduce capital expenditure tied to inventory. It optimizes the energy usage of equipment by adjusting operational parameters in real-time, leading to lower energy consumption.
- Scalability and Flexibility: Leveraging these technologies together, allows companies to scale their asset management strategies as they grow, adapting to changes in operational needs without significant disruptions. Maintenance scheduling based on asset condition rather than time-based intervals, ensures that resources are used effectively, reducing downtime and improving workflow efficiency. They provide a holistic view of all assets, enabling better coordination between teams while improving “wrench-time” productivity and the execution of maintenance and operational tasks. It delivers a single platform to access real-time data across the entire asset portfolio, improving visibility and control over operations for optimizing performance and recommendations for future operations.
USC partners with your organization and coaches your people to significantly impact performance outcomes and accelerate Operational Excellence
USC brings a tailored, structured, and disciplined methodology, along with a range of tools and techniques we apply collaboratively with client’s personnel. Whatever your challenge, we are the people who work with our clients to find full potential and unlock the hidden value.
USC help to identify waste, redundancies, and ineffective processes, and then rapidly recover the prioritized opportunities, and convert them to improvements in performance and operating profit. Further, our people embed with client teams to develop, enhance, prototype, validate and implement asset management strategies to drive, sustain and perpetuate improvements in asset lifecycles and equipment reliability, while changing how plans, schedules, and work is executed. In short, USC implements measurable, sustainable changes that drive asset performance and financial improvements.
- Increased Wrench Time (up to 25% improvement) – Reducing non-productive time through improved work-order generation and prioritization, maintenance teams spend less time searching for work-orders, tracking down parts or waiting for approvals.
- Reduction in Travel & Downtime (up to 20% time savings) – Optimizing the routing and scheduling of maintenance tasks and reducing travel time between jobs to maximize “time on tools”.
- Faster Work-order Completion (up to 30% efficiency gains) – Reducing delays in task assignment, approval and completion tracking, technicians can move quickly from one job to the next by ensuring all the necessary tools and parts are available at the work site, eliminating delays caused by missing resources.
- Optimized Spare Parts Management (up to 15% time reduction) – Faster access to parts and accurate spare part forecasting reduce time on sourcing, stocking and searching while ensuring tools & parts are available for tasks.
- Better Data-Driven Decision Making (up to 20% longer asset life spans) – Collecting and analyzing needed information provides actionable insights that support planning and allow for more informed and pro-active decision making, often delaying the need for capital-intensive replacements.
USC clients experience measurable operational and financial results that significantly improve both the efficiency and profitability of their operations. Benefits delivered may include a 10-20% increase in overall equipment availability due to reduced unplanned downtime and optimized maintenance schedules and a 10-15% improvement in equipment utilization as predictive maintenance reduces the time equipment is out of service.
USC Helps You Tackle Key Challenges
- Optimize maintenance strategies and increase equipment availability operational output
- Predict asset integrity and reliability needs and improve time on tools
- Mitigate risks through stronger stakeholder partnerships, while removing redundancies in the supply chain
- Overcoming cultural and communication issues with contractors, while ensuring quality expectations
Do you want to understand how prepared your company is to drive needed asset management performance and reliability improvements and what the key focus areas that will contribute to lower operating costs? Contact us today.