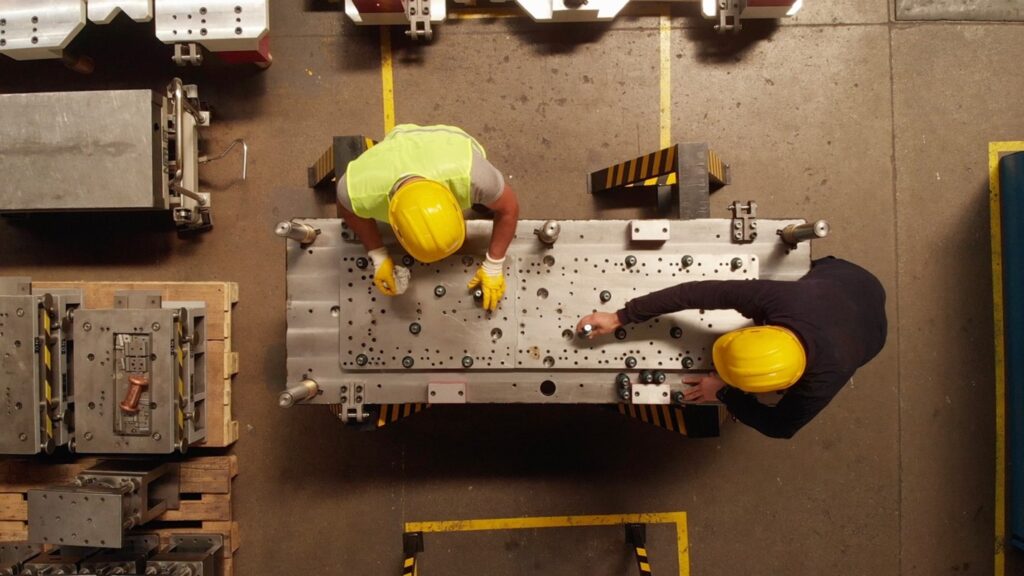
The Hidden Cost of Downtime in Manufacturing: Keeping Your Production Lines Humming
Downtime – the dreaded halt in production that can cripple a manufacturing operation. It’s more than just an inconvenience; it’s a hidden cost that can eat away at your profits. A recent study revealed that nearly 82% of businesses have experienced unexpected downtime in the past three years, with the average incident lasting four hours and costing a staggering $2 million. The impact goes beyond just financial losses – downtime can disrupt customer deliveries, delay critical projects, and erode trust with clients.
The Potential Culprits
One major factor is neglecting preventive maintenance. Regular servicing not only keeps equipment functioning smoothly but also allows technicians to identify potential problems before they snowball into major breakdowns.
Another hidden source is outdated equipment. Obsolete machinery can be a drag on your entire production line. Imagine a slow, malfunctioning piece of equipment holding up the entire process. This can put undue stress on other machines, leading to premature wear and tear, and ultimately, more downtime. Upgrading to newer, more efficient models can significantly improve production flow and reduce the risk of breakdowns. Outdated software can also be a culprit. Running outdated software can lead to compatibility issues with newer systems and leave your facility vulnerable to security breaches.
Beyond equipment and software, a lack of proper training for your workforce can also contribute to downtime. If operators don’t fully understand how a machine works, they might misuse it, leading to errors and breakdowns. Investing in comprehensive training empowers your employees with the knowledge and skills they need to operate machinery safely and efficiently, minimizing the risk of operator-induced downtime.
Finally, the importance of data tracking cannot be overstated. Keeping detailed logs of equipment issues and production hiccups allows you to identify recurring problems and implement preventative measures. Think of it as a historical record that helps you anticipate and address potential bottlenecks before they derail your production schedule.
Finding the Right Solution for You
The good news is that there are steps you can take to combat downtime and keep your production lines humming. Conducting risk audits to identify potential problems, installing sensors to monitor equipment health (like a torque transducer that detects excessive force on a rotating shaft), and implementing a comprehensive preventive maintenance program are all crucial steps in the battle against downtime.
Investing in employee training and partnering with reliable third-party service providers can further strengthen your defenses. By adopting a proactive approach to maintenance and addressing the root causes of downtime, you can significantly reduce disruptions and ensure your manufacturing operation runs smoothly and efficiently.
Want to learn more about the specific costs associated with different downtime causes? The following infographic breaks down the financial impact of various downtime triggers, helping you identify areas for improvement and optimize your production process for maximum uptime.