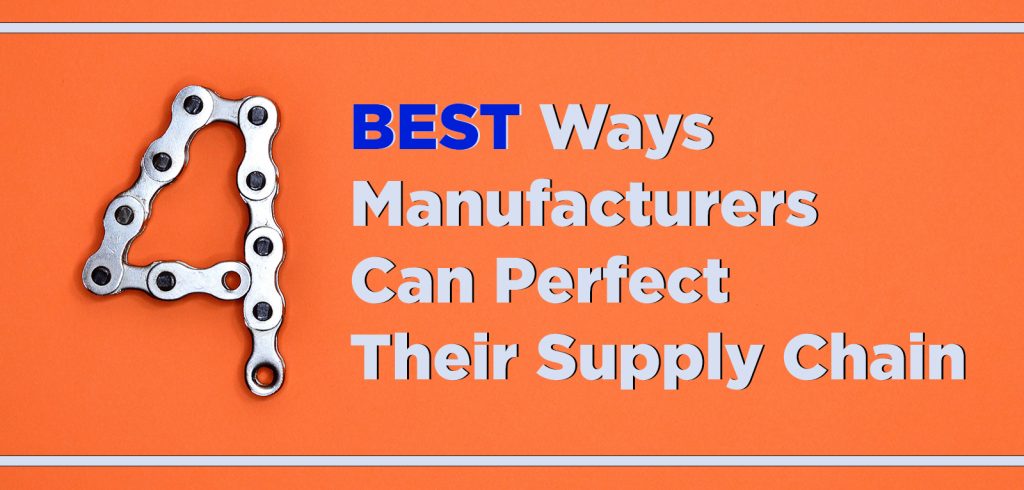
4 Best Ways Manufacturers Can Perfect Their Supply Chain
After a highly tumultuous beginning to the new decade, the economy is taking an unanticipated turn for the better. Economic experts forecasted joblessness as high as 15% nationwide well into 2021. Remarkably, the unemployment rate is back to single-digits as small, mid-sized and large businesses seem to have gotten their groove back. Leading the way — and defying the odds — are manufacturers. Yet with COVID-19 and product shortages still a reality, some manufacturers are wondering what they can do to improve their supply chain resiliency to prepare for present and future disruption.
“After the coronavirus (COVID-19) brought manufacturing activity to historic lows, the sector continued its recovery in August, the first full month of operations after supply chains restarted and adjustments were made for employees to return to work,” said Timothy Fiore, chair of the Institute for Supply Management (ISM) in a press release. “Survey Committee members reported that their companies and suppliers operated in reconfigured factories, with limited labor application due to safety restrictions.”
In a separate poll conducted by the ISM, purchasing managers at some of the largest manufacturing companies expressed ongoing unease about future shocks to their supply chain while they scramble to remedy current shortages. If your company is in a similarly tenuous situation, below are a few recommendations to help you shore up your supply chain risks.
1. Enhance communication with both customers and suppliers
Institute for Supply Chain Management CEO Thomas Derry said organizations that have been able to mount a comeback did so by touching base with partners more frequently to avoid any confusion or misunderstandings. This is true for your customers as well as your suppliers. Customers who have low switching costs will find alternatives to your product if competitors are able to more promptly satisfy demand. Customer service level expectations have been lowered for many hard to get items during the pandemic, but if your product isn’t prompt, communication should be. Courteous responsiveness goes a long way to ease customer impatience. Additionally, sales forecasts will require more frequent attention if customer loyalty, and backlogs, falter.
A strong Sales, Inventory, and Operations Planning (SIOP) process and culture will provide the information you will need to communicate quickly changing demand and depleting inventory levels to your supply base. Don’t just rely on what your MRP screen is telling you about supply timing. This is an opportunity for your purchasing team to make frequent, personal communication with key suppliers, to identify supply risks as early as possible and call in favors if needed. If product is delayed in log-jammed logistics channels, work with freight forwarders, customs brokers, and expedited freight carriers who specialize in simplifying and accelerating delivery.
2. Focus on strategic sourcing
Strategic sourcing focuses on the development of long-term supply relationships for operationally critical products and services. Start by assessing the reliability of your current suppliers. Understand your relative importance to them as a customer, as well as the risks they are experiencing with their suppliers. Assess alternative vendors and your readiness to pivot quickly to a new supplier. If there are multiple vendors for a key material, inquire regarding their capability to handle increased supply requirements. If a material is sole sourced, or otherwise considered very high risk for supply disruption, consider negotiating purchase options with credible alternative suppliers. Options might cost a fraction of lost down-time and provide your company a place in line ahead of competitors who might also be scrambling for material if a key supplier goes down.
If a component involves manufacturer owned tooling, identify alternative suppliers who can operate with your tooling and assess the lead times needed to restore supply. In the long-term, study pros and cons of investing in additional tooling and dividing production between suppliers. While sole sourcing minimizes investment and supplier related costs, it increases vulnerability to disruption.
Derry noted that firms are essentially learning from their mistakes by being more proactive in this regard and if not adding more suppliers, seeking alternative ones who haven’t come through for them in the past.
3. Stop, look, and listen
This is a common phrase heard in kindergarten and grade school classes as teachers seek their students’ attention, but it applies to manufacturing settings as well. No supply chain is perfect. Take time to walk the floor to see what could use some fine-tuning. Simply by using your senses — looking and listening — can quite literally be eye-opening.
Monitoring the shop floor can help you determine where and when maintenance is necessary. For example, perhaps you have equipment that’s making an odd noise, which is typically the first sign of a performance issue. Maintaining a services schedule can help you avoid sudden breakdowns where you have to stop everything to fix whatever happens to be the problem.
4. Increase your inventory
“Firms are also mitigating risk by carrying more inventory as a buffer against disruption,” Derry explained based on results of the poll done by ISM released in July.
Lean manufacturing and Just-in-Time (JIT) inventory principles have enabled manufacturers to significantly reduce operating expenses and increase profitability. However, JIT inventory inherently comes with increased risk of supply outages. During times of uncertainty, perform cost-benefits analysis by assessing the holding cost of increased inventory levels vs the likelihood and cost of production disruptions. How much you increase your inventory will depend on the response time to acquire new supply as well as your ability to delay customer orders without losing sales. How long you need to hold higher levels of inventory will depend on the expected duration of the heightened supply risk. During times of increased uncertainty, inventory is a first-stop insurance policy for production continuity that may yield a competitive advantage allowing your company to continue production while competitors falter.
At USC Consulting Group, we can help you build a better supply chain by applying lessons learned and instituting impactful change that lasts. If you are ready to move your supply chain from a position of vulnerability to resilience, contact us today.
This article was co-authored by USC Consulting Group’s Manager of Supply Chain Practice, David Newman.