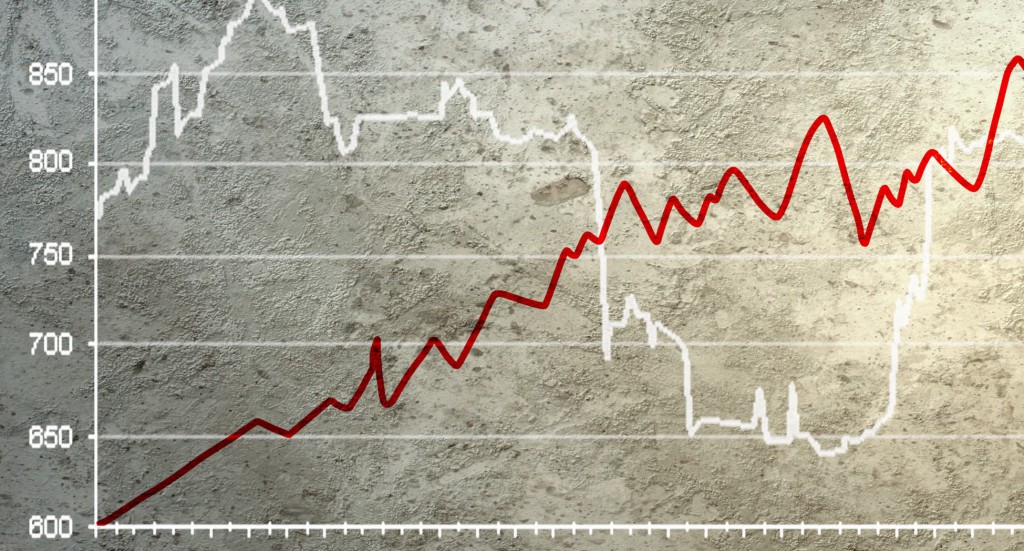
Why Continuous Improvement is a Good Idea
An essential element in promoting efficient operations at a manufacturing plant is continuous improvement, requiring an ongoing effort to improve products and processes. Effective operations consultants can help you implement a culture of continuous improvement, using process maps and key performance indicators, to help you achieve your desired results. Using lean methodologies, like continuous improvement, you can learn to evaluate existing operating procedures and continually improve upon them to keep your facility running at maximal capability.
“Problems are not best solved on a case-by-case basis.”
How technology fits into the continuous improvement plan
To get the most out of technology solutions and equipment, you should make sure your processes and systems operate in unison. To accomplish this, you often have to make changes to company culture. Before you invest in technology, think about what need you are trying to address. If you put technology in place, you should be prepared to interpret and act on the data that stems from that system. Many organizations believe that technology alone will improve their production processes, ignoring the fact in a manufacturing setting, technology must be linked to actionable items. Technology is an enabler, not an end-all be-all solution. Without processes to receive the technology, it can stagnate.
When facing operational challenges, remember that problems are not best solved on a case-by-case basis. Instead, look for root causes and try to define the weak points. You cannot solve a problem if you don’t know exactly where or what it is. For example, if you were to invest in new automated equipment in the hopes of increasing production, you would be ignoring many of the important considerations that should go into the equation. Do you have employee downtime? Do you manage staging areas efficiently? Do your changeover schedules support the increased production quota?
Tribal knowledge can be troublesome
Sometimes, tribal knowledge can work against you during a continuous improvement initiative. The Process Excellence Network pointed out there is no shortage of good ideas for what could be improved at any organization. If you decide to introduce new measures aimed at improving production, you may face resistance from some of the senior level operators and technicians. They have been in their job for many years and believe they know the best way to get things done. This is why operations consultants are effective during in continuous improvement projects, because they can coach your staff and help them consider the broader issues. If you want to introduce new measures that raise efficiency, you have to work on informing, educating, and training your staff. Get them to understand and believe that there is a better way of doing things.
Continuous improvement involves process mapping and coaching.
You may have workers at your organization that are not used to continuous improvement, which requires a lot of process mapping and communication. However, they are also highly skilled in their specific work areas. You can make tribal knowledge work for you by documenting their expertise while you work with them to amend certain processes. These senior workers can then help you train new hires on the improved approach. Tribal knowledge is only troublesome if you allow it to be.
What you can do to counteract the skills gap
Today in U.S. manufacturing, the skills gap is an issue that is frequently discussed. With the baby boomer generation aging out, there is a lot experience and knowledge will go with them. The manufacturing community has, at times, expressed dismay about capturing that knowledge, but experts have been quick to point out that continuous improvement will help. There isn’t one specific solution for fixing the skills gap issue, but a combination of strategies can be used together to address current and future issues.
The way a manufacturing plant should run is based on routines. Continuous improvement is all about taking those routines, making them better, and documenting the changes. Ongoing training on how routine activities ought to be conducted is essential. Manufacturing consultants are experts in studying and helping companies develop effective routines. If you are worried about the impending brain drain at your organization, consider employing the continuous improvement methodology at your plant so you keep your valuable knowledge and expand upon it. If you can get your teams to do repeatable work, the skills gap should not worry you. Instead, focus on promoting consistency, in each process, and in each plant.
Ultimately, when working on continuous improvements, skilled operations consultants can teach you how to make sure expectations are being met. Remember, the success of your teams translates as success for you. Focus on developing your people, improving your processes, and fitting new technology into clearly established functions. Do these things over and over and you could see continuous improvement.