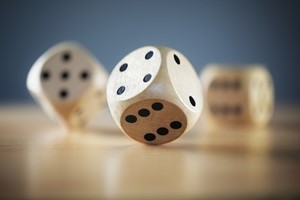
Balancing Risk Management in Lean Operations
Process industries, perhaps more so than any other, need a strong risk management approach since they experience and interact with risk on a daily basis. Due to the continual nature of a process-focused enterprise, these companies ostensibly subject themselves to the highest level of risk because they’re continually operating without stop.
As such, the most production-minded companies who pride themselves on efficient, timely output require a stellar and comprehensive risk management strategy. But risk is multifaceted, and in many ways, proper risk management deployment can positively impact and maximize lean processes.
“Everyone working at a processing plant assesses and manages risk.”
How does risk management apply to lean processes?
Lean processes boil down to the elimination of waste. While some experts may argue honing operations has more to it than, the mission of an average company seeking to increase value potential is to “trim the fat” and reduce areas of excess. According to Lean Manufacturing Tools, some of these areas include overproduction, overprocessing and extraneous movement.
However, promoting a true lean mindset shouldn’t hinge myopically on the problem, but the factor or process that yields the problem. This is where risk management comes in. In one way or another, everyone working at a processing plant assesses and manages risk. For example, when an employee applies his occupational knowledge by safely operating heavy machinery, he’s leveraging the risk of injury with his expertise. That said, risk management doesn’t exclusively pertain to preventing injuries in the workplace. That same employee prevents value loss by processing material properly.
Managers and supervisors seeking to flesh out their risk management simultaneously enhance their lean capabilities. BASF explained risk matrices as a very simple math problem: Risk equals probability times severity. This means equal weight is given to small issues that occur frequently and huge ones that only happen once in awhile. Lean process oversight follows similar guidelines: Waste production can be glaring or ingrained in the system, but either way, it’s unwanted at a business seeking efficiency.
Proper risk management avoids processes that could take down the whole operation.
Why risk management and lean operations complement each other without redundancy
In fact, many common areas typically attributed to managing risk are practically blood-related to lean opeations. For instance, since the advent of the digital age, data curation has wedged itself into every industry. Regardless as to what companies do, these days, they all do it with data. In process industries, apart from customer data, information gleaned from machinery and integral technologies can provide managers with valuable insight toward both eliminating inefficiencies and removing risk from the equation.
For example, if a piece of smart equipment reports to a company’s operational risk management system that it’s running too hot, this procedure blends liability control with lean best practices. Not only do these alerts reduce the chances of worker injury, but they also give supervisors an advanced opportunity to address the issue on their own terms, rather than having to deal with a crippled production line completely out of the blue. A Mälardalen University study found downtime can consume almost a quarter of a manufacturer’s total cost ratio. Thankfully, intelligent data deployment and management can resolve those risks and many more.
The biggest mistake a person looking to optimize their production can make is cutting corners. Lean processes aren’t made by throwing the baby out with the bathwater, but by utilizing the resources available with the most innovative and effective methods. operational risk management keeps workers safe, but it’s just as important as a deterrent for expensive downtime, compromise products and surprise repairs.