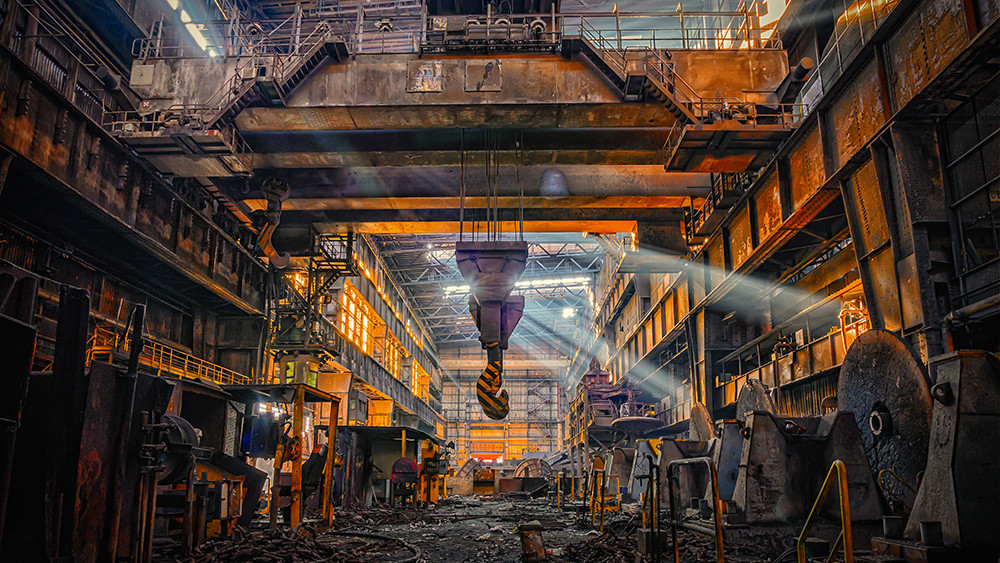
Is the Just-in-Time (JIT) Manufacturing Model Dead?
Did the unprecedented supply chain disruptions caused by the pandemic kill the just-in-time (JIT) manufacturing model? We’d like to come out with a resounding “No!” to answer that question, but it definitely was a topic for discussion among many different types of manufacturers over the past 18 months. Here’s a bit of backstory on that, and why we feel Just-In-Time manufacturing will be more important than ever going forward.
Just-In-Time, or Lean manufacturing, took a hit during COVID, there’s no debate about that. As more and more critical inventory didn’t arrive when manufacturers across many types of industries needed it, it created alarming shortages and delays. Consumers started “panic buying,” driving demand into the stratosphere when manufacturers didn’t have the supply to meet it — remember trying to get toilet paper in the early days of the shutdown? It caused many manufacturers to go back to a “safety stock” method, which is calculated by looking at your average daily use of any given thing and multiplying that by your average lead time to get it. Since the lead times went through the roof with border shutdowns and other delays, manufacturers stocked up, making sure they had more than they needed to get the job done at any point in time.
But that flew in the face of Lean manufacturing principles, which, not for nothing, have been around since the 1930s. The Lean Enterprise Institute defines it this way: “Changing the focus of management from optimizing separate technologies, assets, and vertical departments to optimizing the flow of products and services through entire value streams.”
Just-In-Time Origins
A very short history, in case you’re not familiar with how it all began: Lean manufacturing has been credited to Toyota founder Sakichi Toyoda, his son Kiichiro and their chief engineer, Taiichi Ohno. The whole point of the concept was to look at common areas of waste in manufacturing operations and eliminate them to create greater efficiency on the line. And really, in this post-pandemic age, don’t we all want to subscribe to less waste and more efficiency?
The 7 wastes (or is it really 8?)
Let’s look at the classic “seven wastes” identified by Toyota’s Lean manufacturing model, and think about adding one more.
Overproduction. This is making more product than your customers are demanding. It leaves you with unused product.
Waiting. This could be waiting on the shop floor between steps on the line, or waiting on supply or even equipment.
Transporting. Waste in the transportation stage could either mean excessive movement of inventory, causing the possibility of damage, or even excessive movement within the manufacturing process itself. Think about how close equipment is to each other, and the efficiency of movement of product down the line.
Processing. This is one area where we tend to find opportunities for greater efficiency for many of our clients. It involves extra, unnecessary steps in the manufacturing process on the line.
Inventory. Inventory problems come in the form of having too much stock on hand. The “safety stock” method contributes to it, but it can also be the culmination of overproduction.
Excess motion. Similar to transportation, the motion piece of this puzzle focuses on unnecessary or excessive movement. It’s about how the job gets done. Extra walking, lifting, reaching. Think of it as the ergonomics of the workplace. How close are tools when you need to tweak something on the machinery?
Defects. Defects in product happen to the best of us. But, there are ways to focus on cutting down defects, including detecting potential snafus before they become bigger problems.
Within the past few years, an addition to these classic “seven wastes” has been cropping up in conversations and in blogs about manufacturing.
People. This is about taking a close look at the untapped potential of your people. If your boots on the ground are just doing the job by rote, you’re not taking advantage of ideas and knowledge they may have gained for more efficient ways to get the job done. This is one of the reasons we involve frontline workers in our efforts.
Examining all of these areas of “wastes” in your operation will help you become more efficient and ultimately more profitable. In times of demand uncertainty, that’s more important than ever.
At USC Consulting Group, we’re dedicated to help our customers find more efficiencies in their process no matter what the economy is doing. If you’d like to learn more, please contact us today.
If you’d like to read more in depth about why Lean practices make sense, read our blog, “5 Reasons Why You Need to Stick with Lean Manufacturing Principles.”