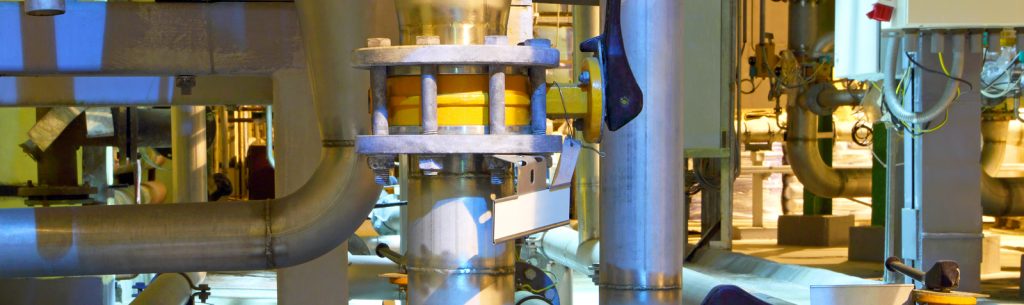
Process Industries and CI: Where the Trouble Starts
Continuous Improvement (CI) for process industries can feel like trying to fix plumbing with the water turned on. No matter how carefully you approach the problem, messes will occur.
At petrochemical and bulk chemical plants where operations run around the clock, any downtime subtracts from potential revenue. The only recourse is minimizing losses and augmenting operations in ways that enduringly promote expedient changes while upholding the safety and quality standards of today.
That’s where CI makes its case, particularly when applied to these areas:
- Scheduling maintenance.
- Enhancing equipment reliability.
- Optimizing labor.
- Standardizing the latest methods for changeover and turnaround.
- Analyzing inventory turns.
- Responding operationally to pricing variation.
With that said, process improvement researchers at technology firm Quandary Consulting Group have found that CI initiatives, while beneficial, often face several barriers that sink success. How have CI implementers in process industries struggled the most to reduce the impact of applying this important discipline to their operations?
They didn’t finish what they started
CI, referred to as kaizen in the circles of lean manufacturing and Six Sigma, does not mean existing in a state of perpetual adjustment, where something is always in progress. Rather, kaizen encourages an openness and willingness to change at all times, a focus on betterment over contentment with the status quo.
Facilities run into trouble when they begin a CI project and fail to fully follow though, instead choosing to look at what lies ahead than what’s in their laps currently. The first thing to go is the detailed real-time analysis, then motivation wanes, then the project lingers on unfinished or is wrapped up hastily. Prevention requires three resources: a senior-level leader to take ownership of the project at hand, a quantifiable terminus, and a method for articulating gains to project stakeholders to energize involvement.
They never considered those most affected by changes
CI pushes adopting companies toward operational perfection, but as a philosophy, it also challenges the behavior of those directly involved in improvement initiatives, both leaders and technicians.
Change management of any name requires advocacy spurred by honest collaboration. Not every improvement will appear as such to certain workers, and indeed they might not be. The benefits of change may not readily present themselves. It’s up to project leaders to communicate what operational excellence will be achieved through improvement. Those leaders must also learn to use that communication as a springboard for changes as opposed to facilitate involvement in the middle or end of a project.
They didn’t recognize when enough was enough
CI projects push limits, but eventually limits push back. Using music as a metaphor, columnist and consultant Alastair Dryburgh illustrated two different ways facilities with continuous improvement initiatives react to those hard limits.
“There’s a very clear standard of what makes a good pianist or violinist,” wrote Dryburgh, “and the difference between the really top people and the next level is very small […] In rock, rap or hip hop, on the other hand, it’s different. Everyone is working in the same sort of genre, roughly, but success comes from establishing a distinctive sound and personality.”
Companies tend to think about continuous improvement too literally, as making something progressively better and better. Eventually, however, they reach a limit where the investment into change far outweighs the slight return. Those organizations must consider the value of innovation as CI. What’s left to determine is whether the limit can go no higher or if doing something daring in another area will achieve even greater operational performance.
They didn’t leverage the right expertise
Advanced process control systems commonly used in process industries bolster best practices for operational data utilization, but they aren’t everything. Big data insights that encourage CI need capable hands to convert those values into actionable strategy. If leaders at processing plants are without such expertise, they should consider a partnership with operational consultants for large-scale projects or for advice on how to train current operators to support future endeavors. For more information, contact the operations management consultants at USC Consulting Group.